Roof panels that keep out the elements are essential for durable building construction. As a key component in roofing systems worldwide, quality roof panels contribute tremendously to structure integrity. Thankfully, advanced metal roll forming technology exists today to produce roof panels with incredible precision and efficiency.
One of the leading innovators in roof panel roll forming equipment is Bemo from Germany. Their versatile Bemo roof panel forming machines craft flawless roof panels in steel, aluminum, copper, zinc and other metals. This guide will explore Bemo’s popular range of roof panel roll formers alongside key considerations for contractors shopping for such machines.
How Bemo Roof Panel Forming Machine Work
Bemo’s roof panel production lines utilize the continuous roll forming process to shape flat metal coil into strong interlocking roof panels. This is achieved passing the coil through a series of consecutive forming stations made up of rollers and dies that gradually bend and twist the strip into the desired panel profile.
The automated multi-stage forming minimizes material stress while the interlocking seams provide exceptional structural stiffness. Whether producing standard corrugated roof sheets or complex sub-structured panels, Bemo’s roof panel roll formers handle over 50 profile shapes with ease.
Some benefits of roll formed roof panels from a Bemo machine include:
- High precision and consistency in dimensions
- Greater panel strength via cold forming
- Material and labor cost savings
- Range of custom profiles accommodated
- Fast production up to 15 meters per minute
But what truly sets Bemo apart is the sheer robustness and reliability of their roof panel roll forming lines even under 24/7 operation. Thanks to superior German engineering focused on precision and durability, Bemo machines churn out endless roofing material year after year for decades.
Now let’s investigate what makes their well-engineered roof panel production equipment tick…
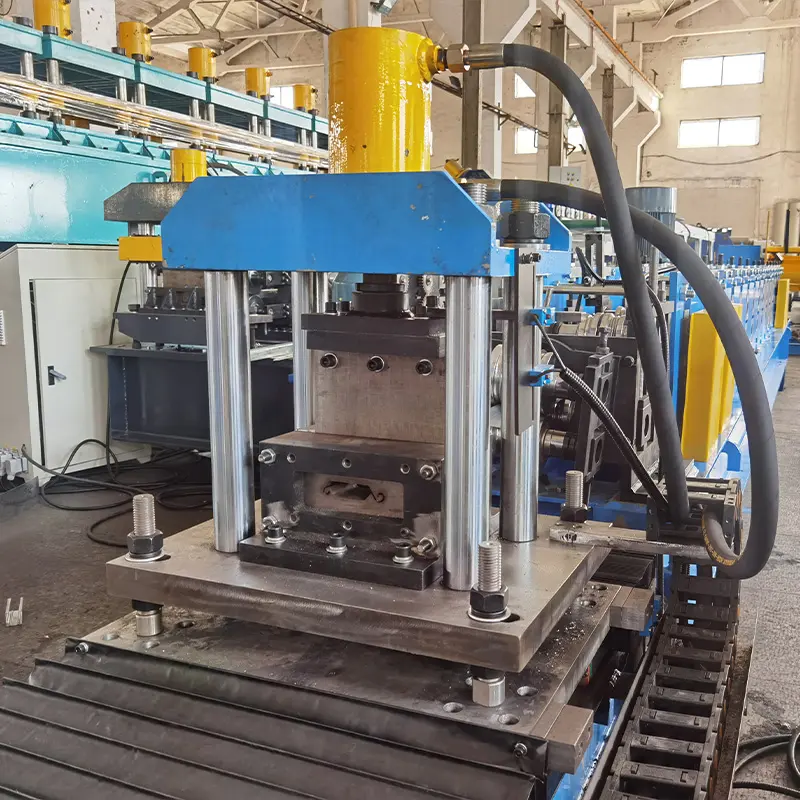
Key Components of Bemo Roof Panel Roll Forming Machines
Bemo’s heavy-duty roof panel roll forming machines are equipped with specialized components engineered to handle the toughest roofing applications.
The key elements include:
Coil Payoff Reel
This holds and feeds the large steel coil into the roll former. Bemo coil payoff reels with powered unwinding support coil diameters up to 2,500 mm and weights up to 8 metric tons depending on model. For smaller coil payoff reels check out the Bemo BNA series.
Straightening Rolls
These remove longitudinal stresses and straighten any coil curvature to ensure flatness before sheet enters forming stages.
Guiding Rolls
These guide the strip alignment as it progresses through the forming process.
Forming Stations
Bemo machines utilize upper and lower sets of roll forming stands with hardened rollers and dies to gradually shape the metal. This “nested” inline arrangement allows very compact footprint. Yet models like the 4-meter Bemo 2600 have up to 16 upper/lower forming stations to create complex roof panel profiles!
Bemo Roof Panel Roll Former Model | Number of Forming Stations |
Bemo 600 | 10 |
Bemo 1000 | 12 |
Bemo 1600 | 14 |
Bemo 2400 | 16 |
Bemo 2600 | 18 |
More forming stations allow creating longer panel sections and more intricate profiles as evident from the table.
Hydraulic System
A rugged hydraulic power unit drives the roof panel forming action through precision-machined gearboxes in each machine section. Bemo configs range from 37 kW to 75 kW motor capacity.
Control Panel
The user-friendly control panel with integrated PLC for precision allows adjusting roll former speed and other parameters for efficient changeovers between roof panel types. Touchscreen models also available.
Runout Roller Tables
Powered conveyor-type roller tables at exit end to smoothly run formed roof panels out of the machine. This carefully protects the finishing quality.
Safety Equipment
Standards panels guarding, emergency stops, light curtains to halt operation when beams are interrupted, and two-hand safety controls ensure operater protection.
Step-by-Step Metal Forming Process on a Bemo Roof Panel Machine
While capabilities vary across models, here is a general overview of how Bemo roll formers fabricate quality roof panels from flat strip steel:
- It all starts by loading a large steel coil weighing up to 8 tons onto a powered unwinding payoff reel.
- The pre-finished metal sheet gets fed into the entry area full of sturdy straightening rolls that remove longitudinal stresses and kinks from the pliable steel.
- Next the flattened strip enters a series of roller-die forming stations that progressively cold form the moving metal into the desired roof panel profile.
- Sophisticated gearing precisely controls the roller axes angles to avoid scratches and achieve formed panels within 0.2 mm dimensional accuracy!
- Special upper/lower roll designs also enable performing multiple bends/folds simultaneously at each station while maintaining sheet alignment.
- acs Upon exiting the last forming stand, the finished roof panel profile complete with interlocks runs out steadily onto powered roller tables.
- Finally the roll formed panels gets cut to required lengths by a saw to complete the efficient production cycle.
The result – strong and beautiful roof panels flowing continuously off the Bemo roll former!
While deceptively simple in concept, a staggering amount of custom engineering goes into these heavy-duty machines to form quality roof panels again and again without fail.
Roof Panel Profiles Formed on Bemo Roll Forming Machines
With 50+ profiles pre-programmed and custom variants possible, Bemo’s high-end modular roll formers can shape varied roof panels include trapezoid, corrugated steel sheets along with sub-structured insulated panels.
Some exact types of roofing sheets produced on Bemo machines are:
- Trapezoidal Steel Roof Panels – Very popular symmetric fluted profile used globally for roof cladding, sidewall construction, mezzanine floors, etc. The angled sides and low weight make trapezoidal sheeting ideal for both hot and cold regions. Bemo machines like the BNA series reliably churn these out everyday.
- Corrugated Roof Sheets – Classic wavy pattern where the sinusoidal form and additional stiffness from roll forming boost structural integrity. Still used today especially in agricultural buildings and DIY projects. The Bemo 1600 model handles small to mid-range corrugated sheets.
- Standing Seam Metal Roof Panels – Very weatherproof interlocked panels forming raised vertical seams after installation. This style popular on contemporary homes hides fasteners while allowing expansion/contraction. Some standing seam variants have curved profiles produced on high-end Bemo machines.
- Composite Insulated Roof Panels – Special sub-structured panels made by simultaneously roll forming two metal skins with solid/foamed plastic insulation sandwiched inside. Although requiring heavier-duty equipment, insulated panels provide excellent thermal/acoustic insulation. Bemo’s Insulated Panel Lines fully automate fused composite panel production.
As evident, Bemo’s versatility allows catering to roofing contractors, farmers, developers and everyone in between!
-
Rolling Shutter Slat Roll Forming Machine
-
Electrical Cabinet Frame Roll Forming Machine
-
Din Rail Roll Forming Machine
-
Cable Ladder Roll Forming Machine
-
PV Mounting Bracket C Shape Profile Roll Forming Machine
-
Cable Tray Roll Forming Machine
-
Steel Coil Cut To Length Line Machine
-
Steel Coil Cut To Length Line Machine
-
Steel Coil Cut To Length Line Machine
Industrial Applications of Bemo Roof Panel Forming Equipment
Bemo’s heavy-duty European-built roof panel roll forming machines serve varied metal construction applications from large commercial structures to small DIY projects.
Here are the common industrial uses for roof panels produced on a Bemo machine:
- Metal Roofing Systems on Factories, Warehouses, Manufacturing Plants
- Roof Cladding for Aircraft Hangars, Metro Sheds
- Roofing Solutions for Commercial Buildings – Hotels, Shopping Complexes, Offices
- Agricultural Sector Applications such as Barns, Stables, Greenhouses
- Production of Trapezoidal Sheet Metal used in Mezzanine Floors and Partition Walls
- Roof Panel requirement for Housing Developments & Tornado Proof Homes
- Re-roofing Projects on Building Repairs/Renovations/Upgrades
- Cottage Industry/ Small Business/ Make Your Own Product Entrepreneurs exploring Localized Roof Panel Production
- DIY Home Owners tackling Garage, Carport, Patio Roofing needs
From expansive commercial roofs to residential patio projects, Bemo empower sheet metal workers worldwide to profitably deliver quality roof panels for all building sectors with their complete production solutions.
Bemo Roof Panel Roll Former Model Specifications
With renown for their heavy-duty European-built machines, Bemo offers varied roll former models engineered to meet different roof panel production scale requirements.
Here is a capabilities overview across their standard roof panel roll forming machine range:
Model | Bemo 600 | Bemo 1000 | Bemo 1600 |
---|---|---|---|
Production Speed | 10 m/min | 10 m/min | 15 m/min |
Max Coil Width | 600 mm | 1000 mm | 1550 mm |
Min Coil Thickness | 0.5 mm | 0.5 mm | 0.5 mm |
Max Coil Thickness | 1.5 mm | 2 mm | 3 mm |
Number of Forming Stations | 10 | 12 | 14 |
Typical Applications | Small Roof Panels | Mid-range Trapezoidals & Corrugated Sheets | Large Trapezoidals & Standing Seam Profiles |
The highlighted specs showcase light to mid-duty models handling mainstream roof cladding applications. But Bemo offers heavy tonnage equipment too
Model | Bemo 2400 | Bemo 2600 |
---|---|---|
Production Speed | 15 m/min | 18 m/min |
Max Coil Width | 1550 mm | 2100 mm |
Min Coil Thickness | 1.2 mm | 1.5 mm |
Max Coil Thickness | 6 mm | 8 mm |
Number of Forming Stations | 16 | 18 |
Typical Applications | Heavy Duty Roof Panels | Max Width/Thickness Panels |
These beastly machines with upgraded parameters can form broad sheets over 2 meters wide and handle thick coils too!
The complete range equips metal construction contractors with the ideal forming solution for small repair jobs or large commercial roofing projects alike.
In fact, Bemo offers customized roll forming lines purpose-built for every roofing need including:
- Insulated Roof Panels – Bemo insulated panel production lines flawlessly roll cold form a top metal skin, inject foam insulation via specialized metering equipment, then form the bottom skin while fusing everything together in one continuous process! Entirely automated lines available alongside manual versions requiring less investment.
- On-Site Mobile Trailer-Mounted Machines – For small contractors not ready to set up a dedicated roof panel manufacturing shop, Bemo offers trailer-mounted systems. Their compact efficient roll formers can quickly produce various panels right on the construction site!
- Retrofitting Existing Lines – With machines built to last for decades, Bemo also provides cost-effective revamps via part replacement to upgrade old roll formers, increase output through higher speeds, or alter dimensions.
Clearly when your business depends on a constant supply of quality roof panels, Bemo empowers fabricators with the full infrastructure to profitably Excel in residential or commercial sheet metal working projects year after year!
Purchasing Considerations for a Bemo Roof Panel Roll Former
For metal fabricators setting up new panel production or expanding operations, investing in a Bemo roof panel roll forming system is a strategic long-term asset.
Like buying any large production equipment, let’s explore key factors contractors ought to consider when purchasing a machine:
Desired Sheet Width & Material Gauge
Primary specifications include max coil width/thickness models can process. Although upgradeable later, ensure to pick a base chassis having 30% extra capacity than present needs to allow business growth.
Required Roof Panel Profile
Review standard vs customizable profiles across Bemo roll formers to create the exact roof panel shapes your application demands.
Target Production Volume
Machine output m/min equates to total daily/monthly panel generation rate. Size appropriately as upgrading capacity later can get expensive.
Power Consumption
Related to output rate, installed motor capacity from 30 kW to 75 kW impacts energy bills.
Available Space
Bemo machines range from 11 ft to 50 ft length fully outfitted. Plan layout wisely for current floor space and future expansion.
Control System Sophistication
Available automation level varies from manual to full PLC plus touchscreen models. This impacts production monitoring/changeover ease.
Noise Level
Operating noise varies inversely with machine ruggedness/longevity. Plan noise reduction measures as required.
Special Configurations
Going beyond defaults, customized options exist for added line automation, integrated measuring systems, special safety add-ons, etc.
Total Cost of Ownership
Machine cost is only one portion. Factor in consumables, utilities, manpower expenses, maintenance over lifetime too. Upfront quality equals long-term savings.
Availability of Service Support & Spare Parts
Vet after-sales support competence and regional access. Machines may last 30 years, so reliable service coverage is a must!
As evident, quite a lot goes into procuring a large capital equipment like a Bemo roof panel roll former. While seeming overwhelming initially, their expert sales engineers simplify the process through transparent consultation tailored to each contractor’s unique requirements.
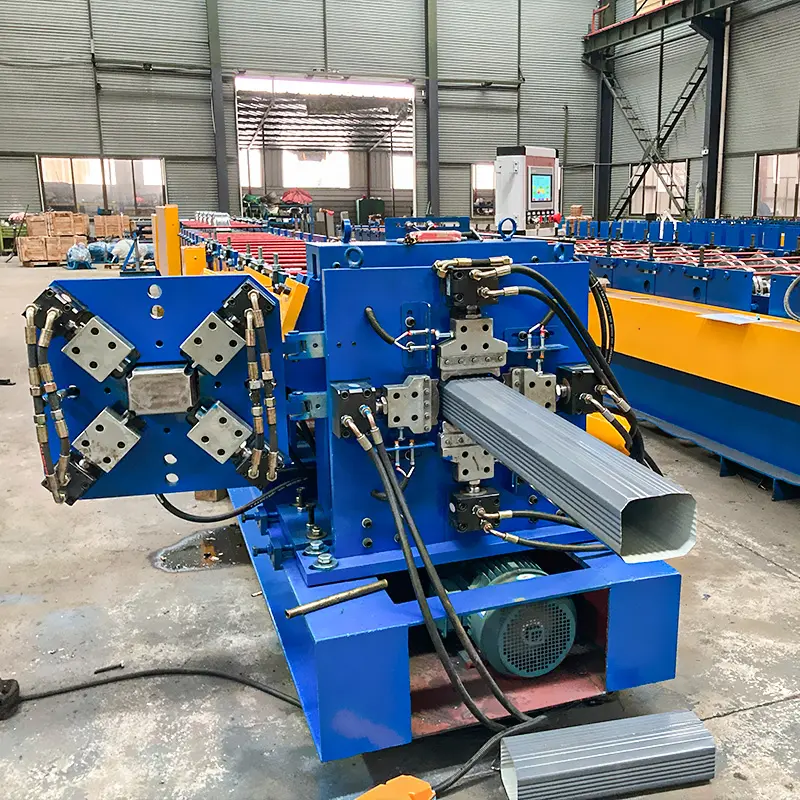
Roof Panel Quality Standards
Fabricating roof panels on a Bemo machine is just the beginning. Ensuring the final sheets consistently meet international quality norms separates the pros from the amateurs.
Here are the key standards commercial roof panel manufactures adhere to ensure their metal cladding provides lasting weatherproof performance:
Profile Dimensions
Roof panel width, height, straightness, flute size, etc. must match specs allowing proper installation and water runoff without leakage through seams/joints. Bemo machines provide calibrated tooling and integrated measuring systems to achieve profile accuracy within 0.2mm tolerance.
Coating Thickness & Adhesion
Primer and color coatings applied to roof panel surfaces must meet thickness standards for corrosion protection and UV resistance while passing tape adhesion tests. Consult coil suppliers to guarantee compatible chemistry.
Salt Spray Resistance
In coastal regions salt fog evaluation ensures metal coatings withstand a saline environment over 1000+ hours without blistering or excessive corrosion beyond acceptability thresholds.
Impact Resistance Testing
This lab test confirms the coated steel panels resist surface/substrate damage along with paint cracking when impacted by standard weighted spherical impact head dropped from set height.
Bend Testing
Roof panels experience expansion/contraction stresses. Bend tests help determine the flexibility and adhesion limits of the coated metal sheets without paint flaking or cracking.
And more exotic tests also sometimes conducted are…
Cyclical Corrosion Testing
This accelerated test exposes roof panels to continuous moisture/dryness cycles of salt spray, humidity, and heating to validate coating durability under harsh climatic fluctuation.
Fire Rating
Although metal itself is non-combustible, fire safety codes require testing roof panel assembly burntime contribution, melting point, and potential to spread flames.
Wind Uplift Testing
In storm-prone areas, standardized wind tunnel tests measure roof components rated capacity to withstand wind velocities and suction pressures before uplift failure.
Thermal Cycling
Similar to corrosion testing, repeated cooling and heating confirms paint finish performance across temperature extremes panels undergo annually.
Acoustic measurement indicates a roof construction’s effectiveness in blocking exterior noise – useful for warehouses near airports for example.
Solar Reflectance Index Rating
How well roofing reflects sunlight is quantified as solar reflectance helps lower cooling costs. White-painted metal panels from a Bemo can achieve among the highest SRI ratings.
Clearly fabricating quality roof panels involves science alongside art!
Thankfully with German engineering pedigree spanning over 78 years of innovation, Bemo machines incorporate expertise and controls to consistently output top-grade metal sheets for the most demanding builders.
Now let’s address some common questions raised regarding these versatile roll forming lines…
FAQ
Can your machine make a double lock standing seam metal roof?
Yes, many Bemo models can shape complex double interlocks for extra water resistance strength needed on standing seam applications. Custom profiling dies available too.
What thickness metals can the machine take?
Bemo’s cover an extensive range depending on model – from 0.5 mm sheets up to 8 mm thick coils! So virtually any metal from light aluminum to heavy steel plates.
Can I get a built-in automatic stacker for my roll former line?
Indeed, Bemo offers automatic stacking units seamlessly integrated with your roll former to neatly arrange finished panels exiting the system. Minimizes handling.
What is the maximum width your roof panel machines can handle?
Over 2 meters! Bemo’s advanced models like the 2600 have 2100 mm capacity to produce wide architectural roof panel applications.
Can Bemo equipment produce insulated sandwich panels too?
Yes, their composite panel lines flawlessly combine two separate metal sheets roll formed around injected insulation foam – all automatically using precision metering pumps.
Do you provide operator training at installation?
Yes, comprehensive training at your factory by Bemo’s technicians ensures understanding best practices for efficient working.
What is the average ROI period for purchasing a roof panel machine?
Depends on production scale, metal costs in your region, etc. but most find ROI under 2 years with such a vital profit centerpiece!