C channel roll forming machines are essential equipment for businesses involved in the manufacturing of C channel profiles. These machines use a roll forming process to gradually bend a strip of metal into the desired shape. Understanding the working mechanism of C channel roll forming machines is crucial to producing high-quality profiles consistently. In this post, we’ll provide an overview of the roll forming process and the specific process used for C channel profiles, as well as discussing the key components of a C channel roll forming machine and the material considerations that are important to keep in mind.
Overview of Roll Forming with C Channel Roll Forming Machines
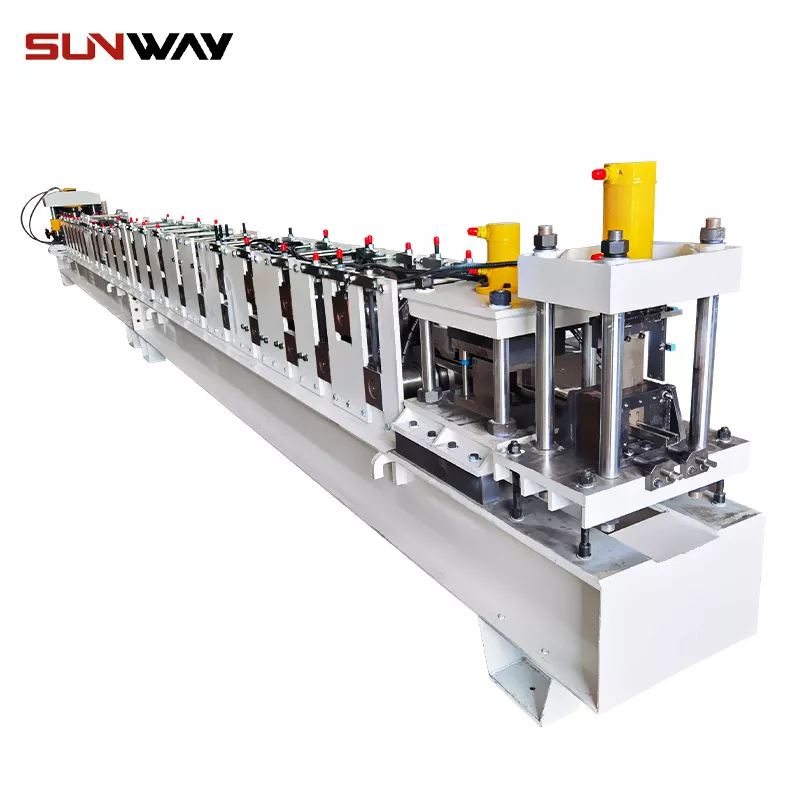
Roll forming is a metalworking process used to produce a wide range of profiles, including C channels. The process involves passing a strip of metal through a series of rollers that gradually bend and shape the metal into the desired profile.
The metal strip is typically fed into the machine from a decoiler and then passed through a series of rollers that are designed to progressively bend the metal strip into the desired shape. These rollers are arranged in pairs and work together to form the profile as the metal strip passes through the machine.
To ensure consistent and accurate forming, the rollers are precision-machined to very tight tolerances. Roll forming machines can have several sets of rollers to produce complex profiles with multiple bends and shapes.
Roll forming is a highly efficient and cost-effective process, as it allows for high-volume production with minimal waste. Additionally, it is a versatile process that can be used with a wide range of materials, including steel, aluminum, and copper.
The roll forming process is crucial to the manufacturing of C channel profiles, and understanding how it works is essential to producing high-quality profiles consistently.
C Channel Roll Forming Process
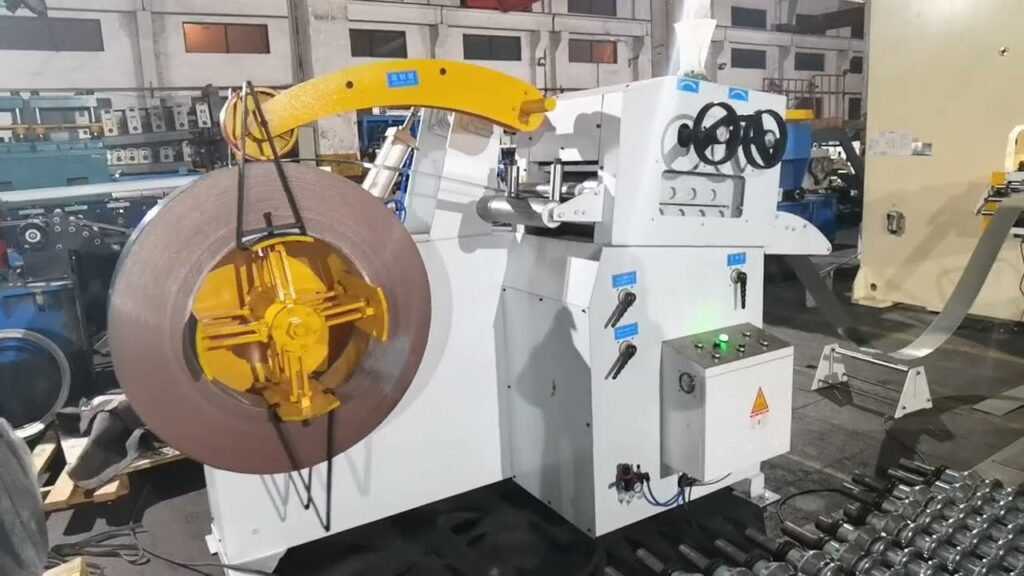
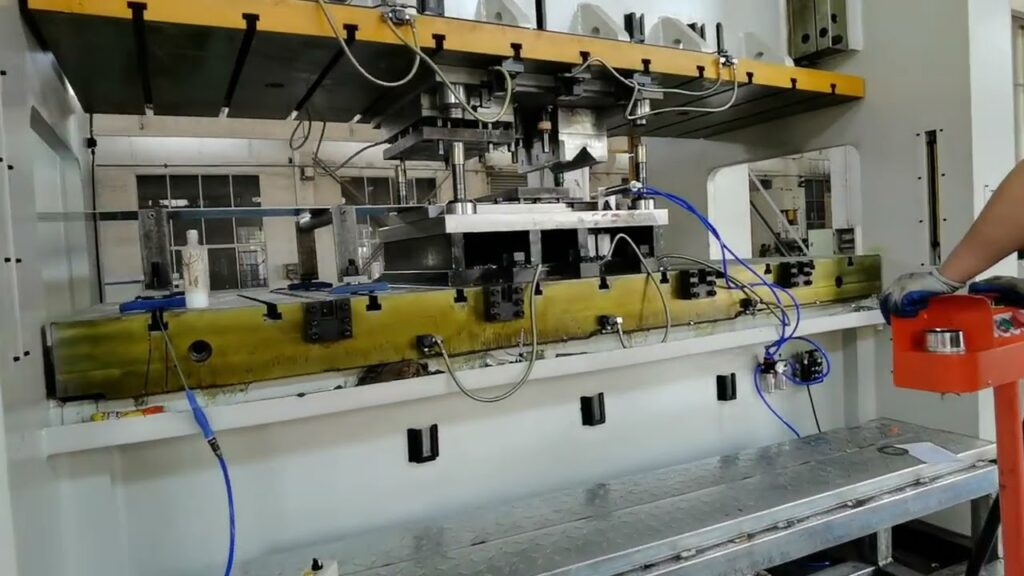
The roll forming process used for C channel profiles is similar to the general roll forming process but with some specific considerations. C channel profiles are characterized by their distinctive shape, which is formed by gradually bending a metal strip into the shape of a “C.”
To create a C channel profile, a roll forming machine uses a series of rollers that are specifically designed to gradually bend the metal strip into the desired C channel shape. The rollers are positioned in pairs, and each pair of rollers bends the metal strip a little more until the final C channel shape is achieved.
The number of rollers required to create a C channel profile can vary depending on the complexity of the profile. Additionally, some C channel roll forming machines may use additional components, such as side rolls or idlers, to help guide and shape the metal strip as it passes through the machine.
The roll forming process for C channel profiles requires precision and accuracy to ensure that the final product meets the necessary specifications. To achieve this, the rollers are carefully designed and machined to tight tolerances, and the machine must be calibrated correctly to ensure consistent performance.
By understanding the specific roll forming process used for C channel profiles, businesses can ensure that their C channel roll forming machines are set up correctly and producing high-quality profiles consistently.
Machine Components of C channel roll forming machines
-
Vineyard Post Roll Forming Machine
-
Auto Size Changeable Sigma Purlin Roll Forming Machine
-
PV Mounting Bracket C Shape Profile Roll Forming Machine
-
C Z Purlin Channel Cold Roll Forming Machine Full Auto Galvanized Steel Profile
-
PV Mounting Bracket Roll Forming Machine (HAT / Omega Profile)
-
PV Mounting Bracket Z Shape Profile Roll Forming Machine
A C channel roll forming machine is made up of several key components that work together to form the C channel profile. These components include the decoiler, feeding system, rollers, and cut-off system.
- Decoiler: The decoiler is responsible for holding and unwinding the metal coil, which is fed into the machine. It ensures that the strip is fed smoothly and consistently into the machine.
- Feeding System: The feeding system is responsible for guiding and feeding the metal strip into the machine’s rollers. It typically includes a straightening unit and a series of rollers that guide the strip into the first set of forming rollers.
- Rollers: The rollers are the heart of the roll forming process. They are arranged in pairs and work together to gradually bend the metal strip into the desired C channel shape. The number and arrangement of rollers can vary depending on the complexity of the C channel profile.
- Cut-Off System: The cut-off system is responsible for cutting the C channel profile to the desired length. It typically includes a flying saw or a hydraulic cut-off press.
All of these components work together to form the C channel profile. The decoiler unwinds the metal coil, and the feeding system guides the metal strip into the machine’s rollers. The rollers then gradually bend the metal strip into the desired C channel shape. Finally, the cut-off system cuts the C channel profile to the desired length, completing the process.
It’s important to note that each component must be carefully designed and calibrated to work together to achieve consistent and accurate results. Any issues with one component can affect the entire process, resulting in subpar C channel profiles.
Material Considerations for C channel roll forming machines
Choosing the right material for C channel roll forming is critical to producing high-quality profiles consistently. The material you choose should be strong, durable, and able to withstand the forming process without losing its structural integrity.
The most commonly used materials for C channel roll forming include steel, aluminum, and copper. Each material has its own unique properties, which will affect its performance during the roll forming process. For example, steel is strong and durable, making it a popular choice for C channel profiles that require high strength and rigidity. Aluminum, on the other hand, is lightweight and corrosion-resistant, making it a good choice for applications where weight is a concern.
When selecting a material for C channel roll forming, you should also consider the thickness of the material. Thicker materials can be more difficult to form and may require more force from the machine’s rollers. Additionally, thicker materials may require a larger machine to accommodate the profile.
The strength of the material is also an important consideration. If the material is too weak, it may not be able to withstand the forming process without deformation or damage. Conversely, if the material is too strong, it may be difficult to form and may require a more powerful machine.
In summary, selecting the right material for C channel roll forming is crucial to producing high-quality profiles consistently. Consider the material’s strength, thickness, and other unique properties to ensure that it is suitable for the roll forming process and your specific application.
Understanding the working mechanism of C channel roll forming machines is crucial to producing high-quality C channel profiles consistently. Roll forming involves passing a metal strip through a series of rollers to gradually form the desired shape. The specific process used for C channel profiles requires precision and accuracy, and involves several key components, including the decoiler, feeding system, rollers, and cut-off system. Choosing the right material for roll forming is also important, considering factors such as thickness and strength. By understanding the working mechanism and material considerations of C channel roll forming machines, businesses can produce high-quality profiles consistently.