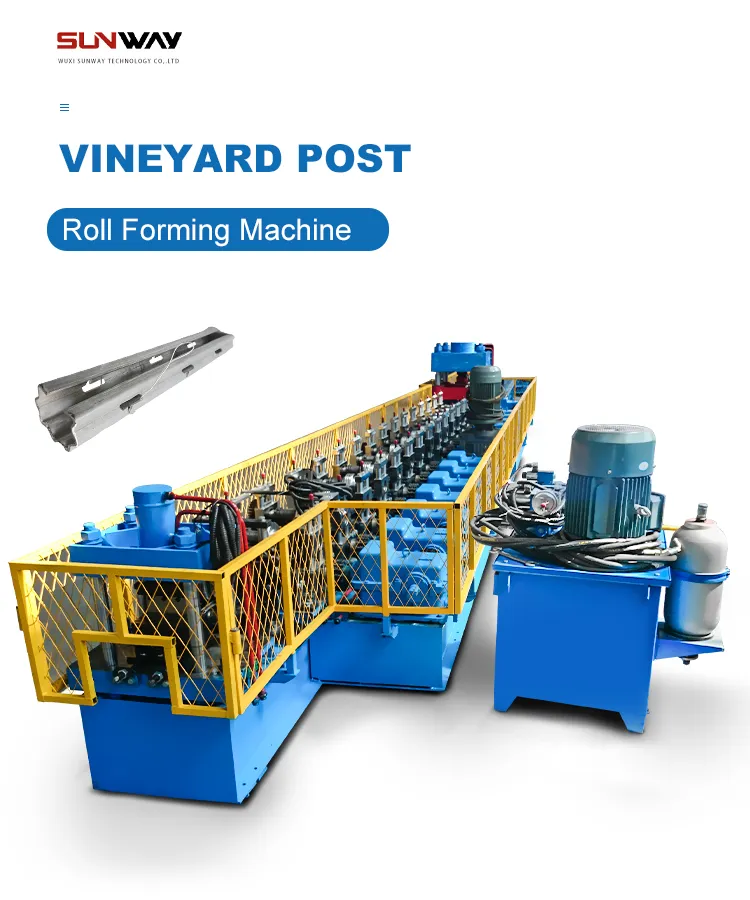
Rollform Makinesi have played a crucial role in the manufacturing industry for centuries, allowing for the production of metal components in large quantities and at a low cost. Over the years, they have undergone significant changes and improvements, resulting in more efficient, precise, and versatile machines. The evolution of them has been driven by advancements in technology, materials science, and engineering, enabling manufacturers to produce complex shapes and profiles with a high degree of accuracy and consistency. In this post, we will take a closer look at the history of them, their current state, and the potential future developments that could shape the next generation of these essential manufacturing tools. Join us on a journey through the past, present, and future of Rollform Makinesi.
the Historical Overview of Rollform Makinesi
-
Electrical Cabinet Frame Roll Forming Machine
-
Din Rail Roll Forming Machine
-
Cable Ladder Roll Forming Machine
-
PV Mounting Bracket C Shape Profile Roll Forming Machine
-
Cable Tray Roll Forming Machine
-
PV Mounting Bracket Roll Forming Machine (HAT / Omega Profile)
-
PV Mounting Bracket Z Shape Profile Roll Forming Machine
-
Solar mounting strut channel roll forming machine
-
Strut Channel Roll Forming Machine
The origins of Rollform Makinesi can be traced back to the early 19th century, when manual rolling mills were used to shape metal sheets. The first known machine that used a series of rollers to form metal sheets into desired shapes was developed in the late 1800s. This machine, called a roll former or rulo şekillendirme makinesi, was powered by a steam engine and consisted of several sets of rollers that gradually shaped the metal as it passed through the machine.
Over time, Rollform Makinesi evolved to become more automated and efficient. In the early 20th century, electric motors replaced steam engines as the primary source of power for them, allowing for more precise control over the speed and pressure of the rollers. In the 1950s and 1960s, computerized controls were added to them, further increasing their accuracy and efficiency.
In the latter half of the 20th century, advancements in materials science and engineering led to the development of new alloys and composites that could be processed using Rollform Makinesi. This opened up new opportunities for them to be used in the production of complex shapes and profiles for various industries.
Today, Rollform Makinesi continue to evolve and improve, with new innovations such as servo-electric drives, laser-guided measuring systems, and 3D printing technology being incorporated into their design. These advancements have made them even more versatile, precise, and efficient, enabling manufacturers to produce high-quality products at a lower cost and with less waste.
Present-Day Rollform Makinesi
There are several types of Rollform Makinesi currently in use in the manufacturing industry, each with its own unique features, benefits, and limitations.
- Single Station Rollform Makinesi: These machines have a single set of rollers that are used to bend and shape the metal into the desired profile. They are commonly used for producing simple shapes, such as C-channels and Z-purlins, and are relatively inexpensive and easy to operate.
- Double Station Rollform Makinesi: These machines have two sets of rollers that are used to bend the metal from both sides, resulting in a more precise and uniform shape. They are commonly used for producing more complex shapes, such as tubing and rails, and can be automated for increased efficiency.
- Multi-Station Rollform Makinesi: These machines have multiple sets of rollers that are used to bend and shape the metal in several stages, resulting in highly complex shapes and profiles. They are commonly used for producing automotive components, aerospace parts, and other precision products.
- Turret Punch Presses: These machines combine roll forming and punching capabilities to produce highly precise and complex shapes. They are commonly used for producing electrical cabinets, HVAC components, and other products that require multiple processes.
Benefits of Rollform Makinesi include their ability to produce high-quality, uniform components at a low cost, their versatility in handling a wide range of materials and thicknesses, and their ability to produce complex shapes and profiles. They are also highly customizable, with options for different roller configurations, feed systems, and cutting mechanisms.
However, Rollform Makinesi do have some limitations. They are not suitable for producing small, intricate shapes, and may require a significant amount of setup time for new products. They also require skilled operators to ensure proper setup and operation, and may require regular maintenance to prevent wear and tear.
In summary, Rollform Makinesi play a critical role in the manufacturing industry by enabling the efficient and cost-effective production of a wide range of metal components. Their versatility, precision, and efficiency make them a valuable asset for many industries, and advancements in technology continue to push the boundaries of what is possible with these machines.
the future of Rollform Makinesi
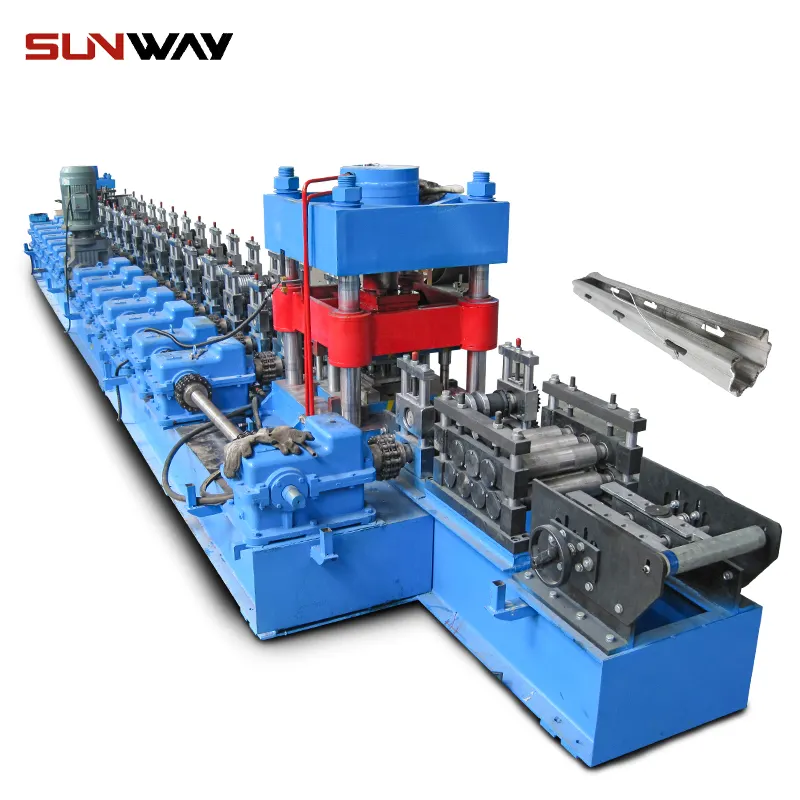
The future of Rollform Makinesi looks promising, as advancements in materials, software, and hardware are expected to continue to drive innovation in this field. Here are some potential developments that could lead to even more efficient and effective Rollform Makinesi:
- Smart Materials: Advances in materials science are likely to lead to the development of new smart materials that can be processed using Rollform Makinesi. These materials will have unique properties, such as shape memory or self-healing capabilities, which could make them ideal for use in the automotive, aerospace, and medical industries.
- 5G Connectivity: The rollout of 5G technology is expected to have a significant impact on Rollform Makinesi by enabling real-time monitoring, remote control, and predictive maintenance. 5G connectivity will also enable them to be integrated with other technologies such as robotics, AI, and IoT.
- Additive Manufacturing: The integration of additive manufacturing with Rollform Makinesi technology could open up new possibilities for producing customized and complex shapes. This could be particularly useful in the aerospace and medical industries, where there is a need for unique and complex components.
- AI-Powered Control Systems: Rollform Makinesi could benefit from AI-powered control systems that can optimize the production process, reduce waste, and improve quality. These systems would be able to learn from past performance and adapt to changing production conditions in real-time.
- Modular Design: Modular design could be used to create Rollform Makinesi that can be easily reconfigured for different products and materials. This would make it easier for manufacturers to adapt to changing market demands and reduce the need for costly equipment upgrades.
Overall, the future of Rollform Makinesi is likely to be characterized by increased automation, integration with other technologies, and the use of smart materials. These developments will make them even more efficient, precise, and versatile, enabling manufacturers to produce high-quality products at a lower cost and with less waste.
In conclusion, the evolution of Rollform Makinesi has been driven by advancements in technology, materials science, and engineering. From the early manual rolling mills to the highly automated, AI-powered machines of today, Rollform Makinesi have been instrumental in the production of metal components in various industries. The future of Rollform Makinesi looks promising, with the potential for new smart materials, 5G connectivity, additive manufacturing, AI-powered control systems, and modular design. These innovations will make Rollform Makinesi even more efficient, precise, and versatile, enabling manufacturers to produce high-quality products at a lower cost and with less waste. As the manufacturing industry continues to evolve, Rollform Makinesi will undoubtedly play a critical role in driving innovation and progress.