If you work in the manufacturing industry, you may have heard the term “corrugated sheet roll forming” in conversations about production processes. Corrugated sheets are widely used in roofing, siding, and industrial manufacturing applications due to their strength, durability, and versatility. But how exactly are these sheets manufactured? In this post, we’ll provide an overview of the mechanics of width corrugated sheet roll forming machines, explaining how they work, their advantages, applications, and maintenance. By the end of this post, you’ll have a better understanding of width corrugated sheet roll forming and how it can benefit your business.
what is Corrugated Sheet Roll Forming?
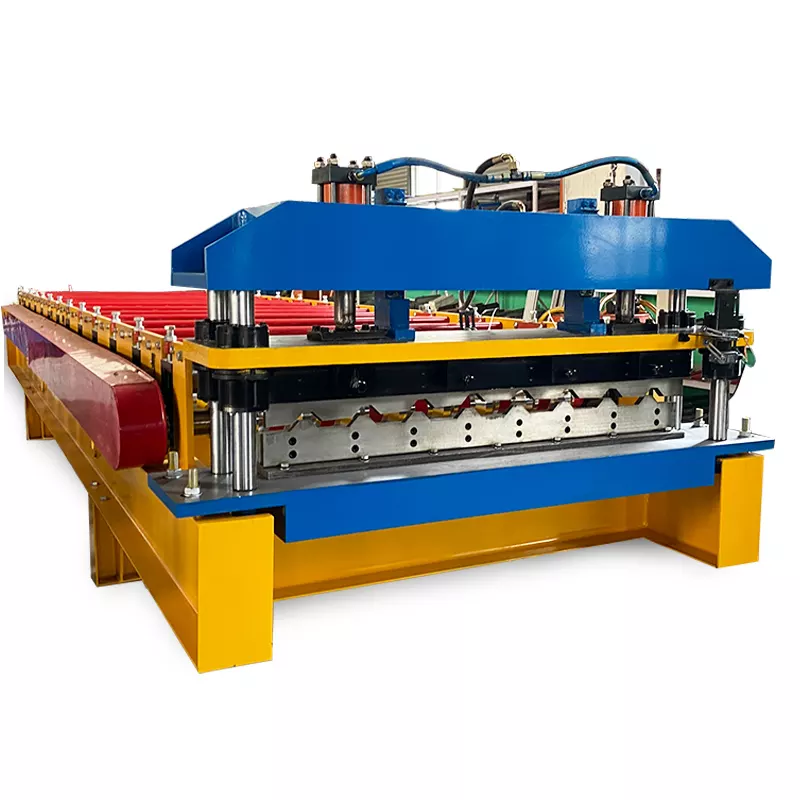
Corrugated sheet roll forming is a manufacturing process used to create corrugated sheets, which are widely used in roofing, siding, and industrial manufacturing applications. Corrugated sheets are sheets of metal that have been shaped with ridges and valleys, which increase their strength and durability.
Roll forming is the process of continuously bending and shaping a metal strip or sheet into a desired shape using a series of rollers. In corrugated sheet roll forming, the metal sheet is fed through a series of rollers that gradually shape it into the corrugated pattern.
The rollers can be adjusted to create different shapes and sizes of corrugated sheets, and the machine can be customized to meet specific production needs. Corrugated sheet roll forming offers several advantages over other manufacturing methods, including cost-effectiveness, precision, and efficiency.
By understanding the basics of corrugated sheet roll forming, businesses can better understand how this manufacturing process works and make informed decisions when it comes to investing in corrugated sheet roll forming machines for their production needs.
Components of Width Corrugated Sheet Roll Forming Machine
-
Electrical Cabinet Frame Roll Forming Machine
-
Din Rail Roll Forming Machine
-
Cable Ladder Roll Forming Machine
-
PV Mounting Bracket C Shape Profile Roll Forming Machine
-
Cable Tray Roll Forming Machine
-
PV Mounting Bracket Roll Forming Machine (HAT / Omega Profile)
-
PV Mounting Bracket Z Shape Profile Roll Forming Machine
-
Solar mounting strut channel roll forming machine
-
Strut Channel Roll Forming Machine
Width corrugated sheet roll forming machines consist of several components that work together to create corrugated sheets of metal. Here are the different components of a typical width corrugated sheet roll forming machine:
- Decoiler: The decoiler is a component that holds the metal coil and feeds it into the roll forming machine. The decoiler can be manual or automatic and can handle different widths and thicknesses of metal.
- Leveling Unit: The leveling unit is a component that flattens and straightens the metal strip before it enters the roll forming machine. This ensures that the metal is evenly fed into the machine, improving the accuracy and consistency of the final product.
- Punching Unit: The punching unit is a component that punches holes or shapes into the metal strip as it enters the roll former. This allows for the creation of corrugated sheets with customized hole patterns, which is important for attaching them to other building components.
- Roll Former: The roll former is the heart of the width corrugated sheet roll forming machine. It consists of a series of rollers that gradually shape the metal strip into the desired corrugated pattern. The rollers can be adjusted to create different shapes and sizes of corrugated sheets, and the machine can be customized to meet specific production needs.
- Cutting System: The cutting system is a component that cuts the finished corrugated sheet to the desired length. This can be done using a variety of methods, such as hydraulic shearing or sawing.
- Control Panel: The control panel is a component that allows operators to control and monitor the width corrugated sheet roll forming machine. It includes a range of features such as digital readouts, control knobs, and emergency stop buttons that allow operators to adjust the machine’s settings and respond quickly to any issues that arise.
By understanding the different components of a width corrugated sheet roll forming machine, businesses can better understand how these machines work and make informed decisions when it comes to purchasing, maintaining, and operating them.
Working Principle of Width Corrugated Sheet Roll Forming Machine
The working principle of width corrugated sheet roll forming machines is relatively simple, but it involves a series of precise steps to create corrugated sheets with a consistent shape and size. Here are the basic steps involved in the working principle of width corrugated sheet roll forming machines:
- Decoiling: The metal strip is uncoiled from a coil and fed into the roll forming machine.
- Leveling: The leveling unit straightens the metal strip, ensuring that it is even and flat as it enters the roll forming machine.
- Punching: The punching unit creates holes or shapes in the metal strip to meet specific design requirements.
- Roll Forming: The metal strip is gradually shaped into the desired corrugated pattern by a series of rollers. The rollers can be adjusted to create different shapes and sizes of corrugated sheets.
- Cutting: Once the metal strip has been shaped into corrugated sheets, the cutting system cuts the sheets to the desired length.
- Stacking: The finished corrugated sheets are stacked and ready for use.
The working principle of width corrugated sheet roll forming machines is highly precise and requires skilled operators to ensure the quality of the final product. By understanding the working principle of width corrugated sheet roll forming machines, businesses can better understand how these machines work and make informed decisions when it comes to investing in them for their production needs.
Advantages of Width Corrugated Sheet Roll Forming Machine
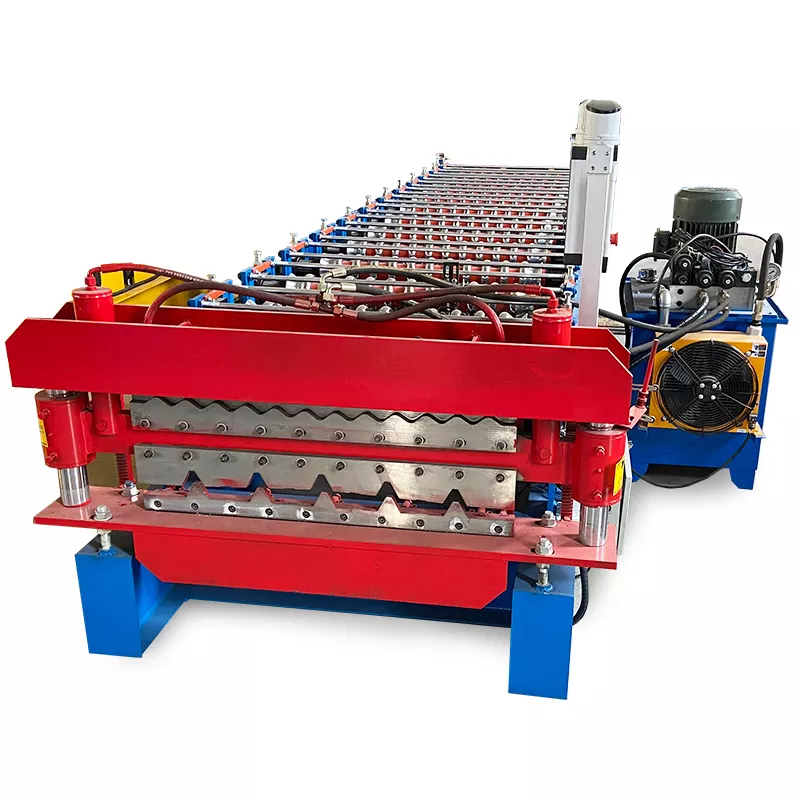
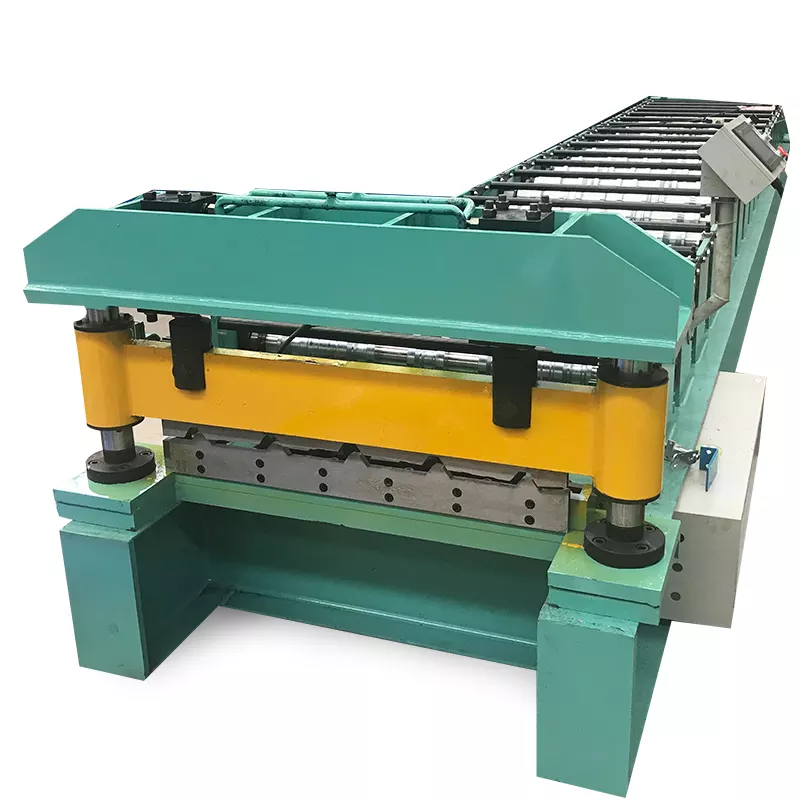
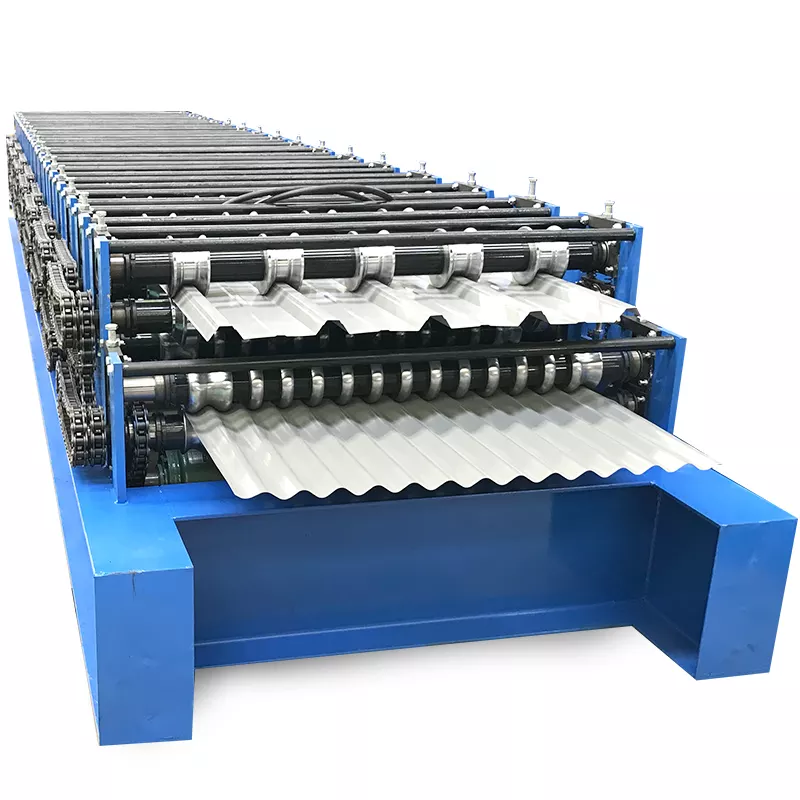
Using width corrugated sheet roll forming machines has several advantages over other manufacturing methods. Here are some of the advantages of using width corrugated sheet roll forming machines:
- High Production Speed: Width corrugated sheet roll forming machines can produce corrugated sheets at a high rate of speed, which allows for large quantities to be produced quickly and efficiently.
- Cost-Effectiveness: Width corrugated sheet roll forming machines are highly cost-effective when compared to other manufacturing methods. The machines are designed to operate continuously, with minimal downtime, which reduces the overall cost of production.
- Precision: Width corrugated sheet roll forming machines are highly precise and can produce corrugated sheets with consistent quality and accuracy. This is important for industries that require high-quality products with specific measurements and dimensions.
- Customization: Width corrugated sheet roll forming machines can be customized to meet specific production requirements, such as the size and shape of the corrugated sheet, the thickness and type of metal, and the hole patterns required.
- Minimal Material Waste: Width corrugated sheet roll forming machines produce very little material waste, which helps to minimize the overall cost of production and is better for the environment.
Overall, using width corrugated sheet roll forming machines offers several advantages over other manufacturing methods, making them a popular choice in industries such as construction, roofing, and industrial manufacturing.
In summary, width corrugated sheet roll forming machines offer several advantages over other manufacturing methods, including high production speed, cost-effectiveness, precision, customization, and minimal material waste. By understanding the mechanics and components of width corrugated sheet roll forming machines, businesses can make informed decisions when it comes to purchasing, maintaining, and operating these machines. With their ability to produce corrugated sheets quickly, accurately, and with consistent quality, width corrugated sheet roll forming machines are an essential tool for industries that require high-quality, durable, and reliable corrugated sheets.