Overview
A step beam machine, also known as a roll forming machine or a floor decking machine, is a specialized equipment used for forming long, continuous profiles from flat metal coils or sheets. These machines are widely employed in the construction industry for manufacturing various structural components, including floor decks, roof decks, purlins, wall panels, and other building materials.
The step beam machine derives its name from the unique forming process it employs. The process involves feeding a continuous flat metal strip through a series of consecutive roller stations, each of which progressively bends and shapes the material into the desired profile. This step-by-step forming method allows for the creation of complex cross-sectional shapes with high precision and consistency.
Present Equipment Guide
The step beam machine is a versatile and efficient solution for producing long-length structural components. It offers several advantages over traditional manufacturing methods, such as reduced material waste, increased production efficiency, and the ability to create custom shapes tailored to specific project requirements.
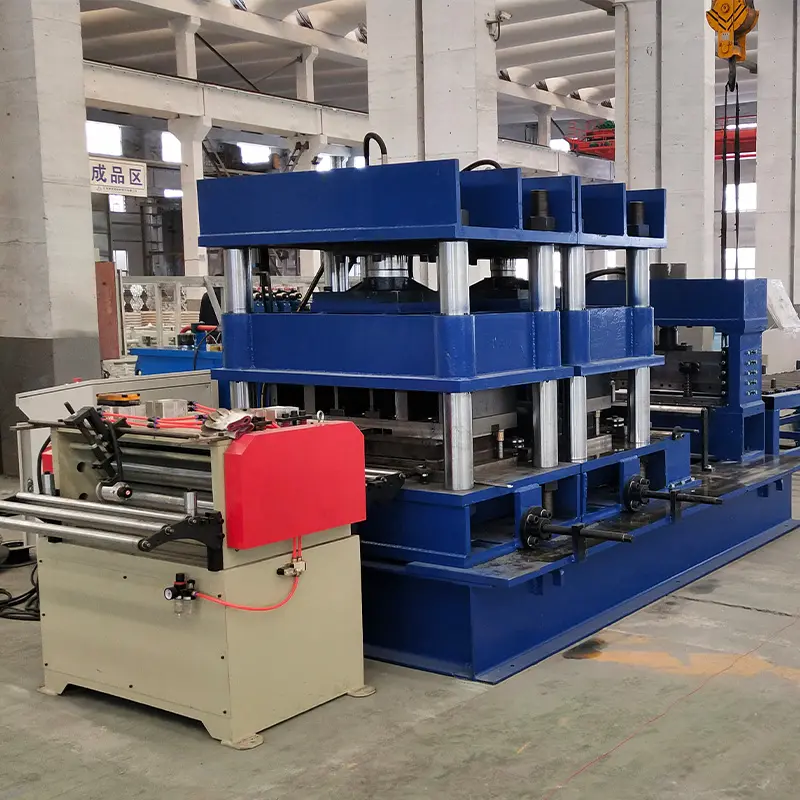
Key Features of Step Beam Machines
- Continuous Forming Process: The machine operates by continuously feeding a flat metal strip through a series of roller stations, progressively shaping the material into the desired profile.
- Roll Forming Tooling: Each roller station is equipped with specially designed rolls or tooling that bend and shape the material with precision.
- Variable Profiles: Step beam machines can be configured to produce a wide range of profiles, from simple C-shapes to complex structural components with multiple bends and features.
- High Production Rates: These machines offer high production rates, allowing for efficient manufacturing of large quantities of components.
- Material Versatility: Step beam machines can process various materials, including steel, aluminum, stainless steel, and other metals, depending on the application requirements.
- Inline Punching and Cutting: Many step beam machines incorporate inline punching and cutting capabilities, enabling the creation of holes, slots, or cut-to-length components within the same production line.
Types of Step Beam Machines
Step beam machines are available in different configurations to meet various production requirements and application needs. Here are some common types:
Machine Type | Description |
---|---|
Floor Decking Machine | Designed specifically for producing floor decking panels and components for building constructions. |
Roof Decking Machine | Similar to floor decking machines but optimized for manufacturing roof decking panels and related components. |
Purlin Roll Former | Used for forming purlins, which are structural members used to support roof decking or cladding systems. |
Wall Panel Machine | Configured to produce wall panels and cladding components for various building envelopes. |
Multi-Purpose Roll Former | Versatile machines that can be reconfigured to produce a wide range of profiles by changing the roll tooling. |
Working Process
The step beam machine operates based on a continuous roll forming process, where a flat metal strip is progressively shaped into the desired profile through a series of roller stations. Here’s a general overview of the working process:
- Material Feeding: The flat metal coil or sheet is fed into the machine’s decoiler or feeder unit, ensuring a consistent and controlled material supply.
- Straightening: The material may pass through a straightening unit to remove any existing curvature or irregularities, ensuring a flat and consistent surface for forming.
- Roll Forming: The straightened material then enters the roll forming section, where it passes through a series of roller stations, each with specially designed roll tooling that progressively bends and shapes the material into the desired profile.
- Profile Forming: As the material advances through the roller stations, the cross-sectional shape of the profile gradually takes form, with each roller station contributing to the overall shaping process.
- Inline Operations: Depending on the machine configuration, inline operations such as punching, notching, or cutting may be performed as the formed profile exits the roll forming section.
- Cut-to-Length: If required, the continuous formed profile can be cut to specific lengths using a shear or saw cutting station integrated into the machine.
- Stacking or Packaging: The finished components are then stacked, bundled, or packaged for transportation or further processing, as required by the application.
Material Feeding
Parameter | Description |
---|---|
Decoiler | Responsible for feeding the flat metal coil or sheet into the machine in a controlled and consistent manner. |
Coil Width | Determines the maximum width of the material that can be processed by the machine. |
Coil Thickness | Specifies the range of material thicknesses that the machine can handle, typically ranging from thin gauge to heavy gauge materials. |
Coil Weight | Defines the maximum weight capacity of the decoiler, ensuring proper material handling and feeding. |
-
Rolling Shutter Slat Roll Forming Machine
-
Highway Guardrail End Terminal Forming Machine
-
Highway U/C Post Roll Forming Machine
-
2 Waves Highway Guardrail Roll Forming Machine
-
3 Waves Highway Guardrail Roll Forming Machine
-
Vineyard Post Roll Forming Machine
-
Auto Size Changeable Sigma Purlin Roll Forming Machine
-
Electrical Cabinet Frame Roll Forming Machine
-
Din Rail Roll Forming Machine
Forming Process
Parameter | Description |
---|---|
Roll Tooling | The roll tooling design is crucial for shaping the material into the desired profile. Roll tooling can be customized or interchanged to produce different profiles. |
Number of Roller Stations | The number of roller stations determines the complexity of the profile that can be formed. More stations allow for more intricate shapes and features. |
Roller Diameter | The diameter of the rollers affects the minimum bend radius and the overall forming accuracy. Larger diameters generally provide better forming quality. |
Roller Material | Rollers are typically made from high-strength materials like tool steel or cast iron to withstand the forming forces and wear. |
Roll Adjustment | Roll adjustment mechanisms allow for fine-tuning the roll positions and clearances to achieve precise forming dimensions. |
Design and Customization
Parameter | Description |
---|---|
CAD/CAM Integration | Step beam machines often integrate with Computer-Aided Design (CAD) and Computer-Aided Manufacturing (CAM) software for profile design, tooling development, and machine programming. |
Custom Roll Tooling | Manufacturers can design and produce custom roll tooling to create unique profiles tailored to specific project requirements. |
Prototyping Capabilities | Some step beam machines offer prototyping capabilities, allowing for the production of small batches or sample components before committing to full-scale production. |
Automation and Control | Advanced machines may incorporate automation systems, programmable logic controllers (PLCs), and human-machine interfaces (HMIs) for improved process control and monitoring. |
Slicing and Cutting
Parameter | Description |
---|---|
Shear Cutting | Integrated shear cutting stations allow for trimming or cutting the formed profiles to specific lengths. |
Saw Cutting | Some machines may incorporate saw cutting stations for more precise or intricate cutting operations. |
Punching and Notching | Inline punching and notching capabilities enable the creation of holes, slots, or cutouts in the formed profiles as required. |
Cut-to-Length Accuracy | The precision of the cutting operation is crucial for ensuring consistent component lengths and minimizing material waste. |
Suppliers and Price Range
Step beam machines are manufactured by various industrial equipment suppliers, ranging from specialized roll forming equipment manufacturers to larger conglomerates. Here are some notable suppliers and their approximate price ranges:
Supplier | Price Range (USD) |
---|---|
Bradbury Group | $100,000 – $500,000 |
Engel Machinery | $150,000 – $800,000 |
Samco Machinery | $80,000 – $400,000 |
Roll Former Corporation | $120,000 – $600,000 |
Knuth Machine Tools | $90,000 – $450,000 |
Please note that these prices are approximate and can vary significantly depending on the specific machine configuration, options, and customizations required for your application.
Installation and Operation
Parameter | Description |
---|---|
Site Preparation | Proper site preparation is essential, including adequate floor space, suitable power supply, and necessary utilities. |
Machine Installation | Professional installation services are typically provided by the supplier or authorized technicians to ensure proper setup and alignment. |
Operator Training | Comprehensive operator training is crucial for safe and efficient machine operation, maintenance, and troubleshooting. |
Production Planning | Effective production planning is necessary to optimize material usage, minimize waste, and maximize throughput. |
Safety Considerations | Step beam machines require strict adherence to safety protocols, including the use of personal protective equipment (PPE) and following established safety procedures. |
Maintenance and Troubleshooting
Parameter | Description |
---|---|
Preventive Maintenance | Regular preventive maintenance, including lubrication, roll inspections, and component replacements, is essential for maintaining optimal machine performance and extending its service life. |
Tooling Maintenance | Proper care and maintenance of roll tooling are crucial to ensure consistent forming quality and prolong tooling life. |
Troubleshooting | Effective troubleshooting procedures and access to technical support from the manufacturer or authorized service providers can help resolve issues and minimize downtime. |
Spare Parts Availability | Ensuring the availability of spare parts and consumables is essential for timely repairs and minimizing production disruptions. |
Choosing a Supplier
When selecting a supplier for a step beam machine, it’s essential to consider various factors to ensure you make an informed decision that meets your specific requirements. Here are some key considerations:
Factor | Description |
---|---|
Reputation and Experience | Choose a supplier with a proven track record in manufacturing high-quality step beam machines and providing reliable customer support. |
Machine Capabilities | Evaluate the supplier’s range of machine capabilities, including the types of profiles they can produce, material handling capabilities, and production rates. |
Customization Options | Assess the supplier’s ability to offer customized solutions tailored to your specific needs, such as custom roll tooling or integrated automation features. |
Service and Support | Consider the supplier’s service and support offerings, including installation assistance, operator training, maintenance services, and spare parts availability. |
Price and Value | While cost is an important factor, it’s essential to consider the overall value proposition, including the machine’s quality, performance, and long-term operational costs. |
Delivery and Lead Times | Evaluate the supplier’s delivery and lead times to ensure they align with your production schedule and project timelines. |
Warranty and Guarantees | Review the supplier’s warranty and guarantee policies to ensure you have adequate protection and support for your investment. |
Pros and Cons
Like any manufacturing equipment, step beam machines have their advantages and limitations. Here’s a comparison of the pros and cons to help you make an informed decision:
Advantages
- High Production Rates: Step beam machines are designed for continuous roll forming, enabling high production rates and efficient manufacturing of long-length components.
- Consistent Quality: The roll forming process ensures consistent dimensional accuracy and quality across the entire length of the formed profiles.
- Material Efficiency: By using continuous coils or sheets as the input material, step beam machines minimize material waste compared to traditional fabrication methods.
- Versatility: With the ability to change roll tooling, step beam machines can produce a wide range of profiles, offering flexibility for various applications.
- Automation Capabilities: Many modern step beam machines incorporate automation features, such as programmable logic controllers (PLCs) and human-machine interfaces (HMIs), improving process control and efficiency.
Limitations
- Initial Investment: Step beam machines can be a significant capital investment, especially for larger or more specialized configurations.
- Tooling Costs: The cost of custom roll tooling can be substantial, particularly for complex or unique profiles.
- Material Limitations: While step beam machines can process various metals, there may be limitations on the material thickness or strength that can be effectively formed.
- Setup and Changeover Time: Changing roll tooling or reconfiguring the machine for different profiles can be time-consuming, potentially impacting production schedules.
- Maintenance Requirements: Proper maintenance and regular inspections are crucial to ensure consistent performance and prevent costly breakdowns or production disruptions.
Advantages and Applications
Step beam machines offer several advantages over traditional manufacturing methods, making them a preferred choice for many industrial applications. Here are some key advantages and typical applications:
Advantages
- High Production Rates: Step beam machines are designed for continuous roll forming, enabling high production rates and efficient manufacturing of long-length components.
- Consistent Quality: The roll forming process ensures consistent dimensional accuracy and quality across the entire length of the formed profiles.
- Material Efficiency: By using continuous coils or sheets as the input material, step beam machines minimize material waste compared to traditional fabrication methods.
- Versatility: With the ability to change roll tooling, step beam machines can produce a wide range of profiles, offering flexibility for various applications.
- Automation Capabilities: Many modern step beam machines incorporate automation features, such as programmable logic controllers (PLCs) and human-machine interfaces (HMIs), improving process control and efficiency.
Applications
- Construction Industry: Step beam machines are widely used in the construction industry for manufacturing structural components like floor decks, roof decks, purlins, wall panels, and cladding systems.
- Automotive Industry: Certain automotive components, such as body reinforcements, frame members, and structural components, can be produced using step beam machines.
- Aerospace Industry: These machines can be used to manufacture aircraft structural components, such as stringers, frames, and other lightweight, high-strength profiles.
- Agricultural Equipment: Step beam machines are employed in the production of components for agricultural equipment, including grain bins, silos, and farm building structures.
- Furniture Manufacturing: Certain furniture components, like chair frames, table legs, and shelving units, can be produced using step beam machines.
- HVAC Industry: Step beam machines are used to manufacture ductwork, flashing, and other components for heating, ventilation, and air conditioning systems.
Limitations and Considerations
While step beam machines offer numerous advantages, it’s important to consider their limitations and potential drawbacks to make an informed decision. Here are some key limitations and considerations:
Limitations
- Initial Investment: Step beam machines can be a significant capital investment, especially for larger or more specialized configurations.
- Tooling Costs: The cost of custom roll tooling can be substantial, particularly for complex or unique profiles.
- Material Limitations: While step beam machines can process various metals, there may be limitations on the material thickness or strength that can be effectively formed.
- Setup and Changeover Time: Changing roll tooling or reconfiguring the machine for different profiles can be time-consuming, potentially impacting production schedules.
- Maintenance Requirements: Proper maintenance and regular inspections are crucial to ensure consistent performance and prevent costly breakdowns or production disruptions.
Considerations
- Production Volume: Step beam machines are typically best suited for high-volume production runs, as the initial tooling and setup costs can be amortized over a larger output.
- Profile Complexity: More complex profiles with multiple bends or intricate features may require specialized roll tooling or additional machine capabilities, increasing costs and complexity.
- Material Handling: Proper material handling equipment and processes should be in place to ensure efficient feeding of coils or sheets into the machine.
- Skilled Operators: Trained and experienced operators are essential for setting up and operating step beam machines to achieve optimal performance and quality.
- Safety Protocols: Strict safety protocols must be followed to ensure the safe operation of these high-powered machines and prevent injuries or accidents.
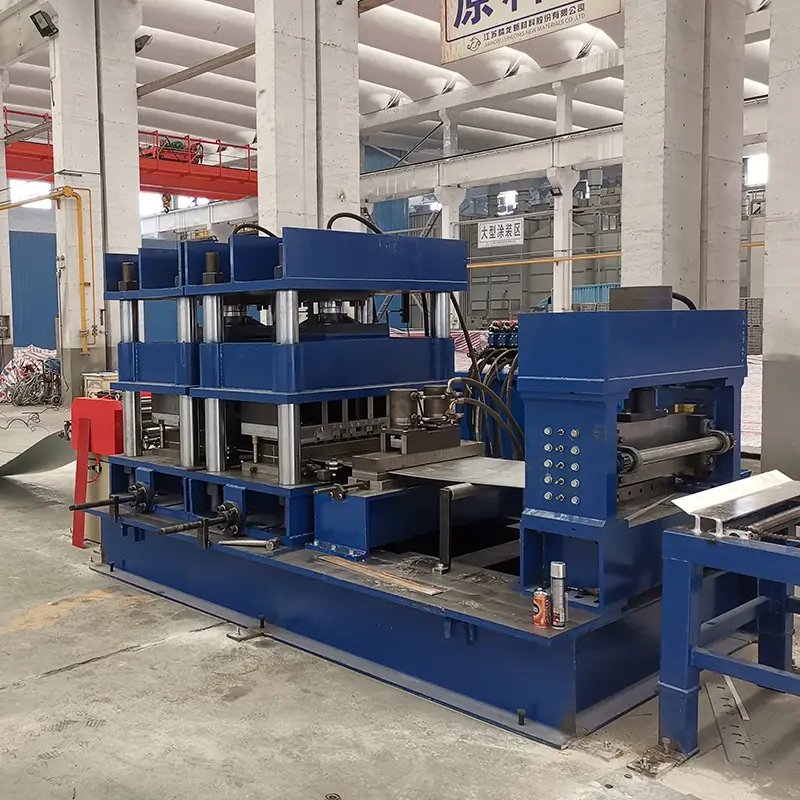
FAQ
What is the typical production rate of a step beam machine?
The production rate of a step beam machine can vary depending on factors such as the machine configuration, material thickness, profile complexity, and line speed. However, most modern step beam machines can produce between 100 and 300 feet (30 to 90 meters) of formed profiles per minute.
Can step beam machines produce curved or bent profiles?
While step beam machines are primarily designed for creating straight, continuous profiles, some specialized configurations can incorporate additional forming stations or rollers to introduce curvature or bends into the formed profiles. However, the degree of curvature and complexity may be limited compared to dedicated roll bending machines.
How often does roll tooling need to be replaced or maintained?
The frequency of roll tooling replacement or maintenance depends on several factors, including the material being processed, the production volume, and the tooling material itself. Generally, roll tooling should be inspected regularly for wear, and preventive maintenance should be performed according to the manufacturer’s recommendations. Proper roll tooling maintenance can significantly extend its service life and ensure consistent forming quality.
Can step beam machines handle different material thicknesses?
Yes, most step beam machines are designed to accommodate a range of material thicknesses, typically ranging from thin gauge (around 0.5 mm or 0.020 inches) to heavy gauge materials (up to 6 mm or 0.25 inches). However, the specific thickness range may vary depending on the machine’s capabilities and the roll tooling design.
How is the roll tooling designed for custom profiles?
Roll tooling for custom profiles is typically designed using computer-aided design (CAD) software, which allows engineers to create detailed 3D models of the desired profile. These models are then used to generate the precise roll contours and specifications for manufacturing the roll tooling. In some cases, prototyping or iterative refinement may be necessary to achieve the desired profile shape and tolerances.
What safety considerations are important when operating a step beam machine?
Safety is a critical consideration when operating step beam machines. Some key safety measures include:
- Proper machine guarding and safety interlocks
- Use of personal protective equipment (PPE) such as safety glasses, gloves, and steel-toed boots
- Adherence to lockout/tagout procedures during maintenance or setup
- Adequate training for operators and maintenance personnel
- Regular inspections and maintenance to ensure proper machine function
- Strict adherence to established safety protocols and procedures