Overview
Floor deck machines, also known as floor decking roll formers or decking roll forming machines, are specialized equipment used in the construction industry for producing corrugated steel decking or composite floor deck panels. These durable and versatile panels are designed to serve as a permanent form for concrete slabs in steel and concrete composite floor systems.
Floor deck machines continuously form corrugated sheets from coiled steel coils, enabling efficient and cost-effective production of decking panels on-site or in a manufacturing facility. By combining the strength of steel with the rigidity of concrete, these composite floor systems offer numerous advantages in terms of structural integrity, fire resistance, and overall performance.
Floor Deck Machine: The Heart of Composite Floor Construction
Composite floor systems have become increasingly popular in modern construction due to their ability to provide a solid, fire-resistant base for buildings while offering design flexibility and cost-effectiveness. At the core of this construction method lies the floor deck machine, a specialized piece of equipment that continuously forms corrugated steel sheets into decking panels.
These machines are designed to handle coiled steel coils, which are fed into the machine and progressively cold-formed into the desired decking profile. The process involves a series of precision rollers that gradually shape the steel into the corrugated pattern, creating a strong yet lightweight floor deck panel.
One of the key advantages of using floor deck machines is the ability to produce decking panels on-site, eliminating the need for transportation and reducing overall project costs. Additionally, these machines can be configured to produce a variety of decking profiles, catering to different project requirements and design specifications.
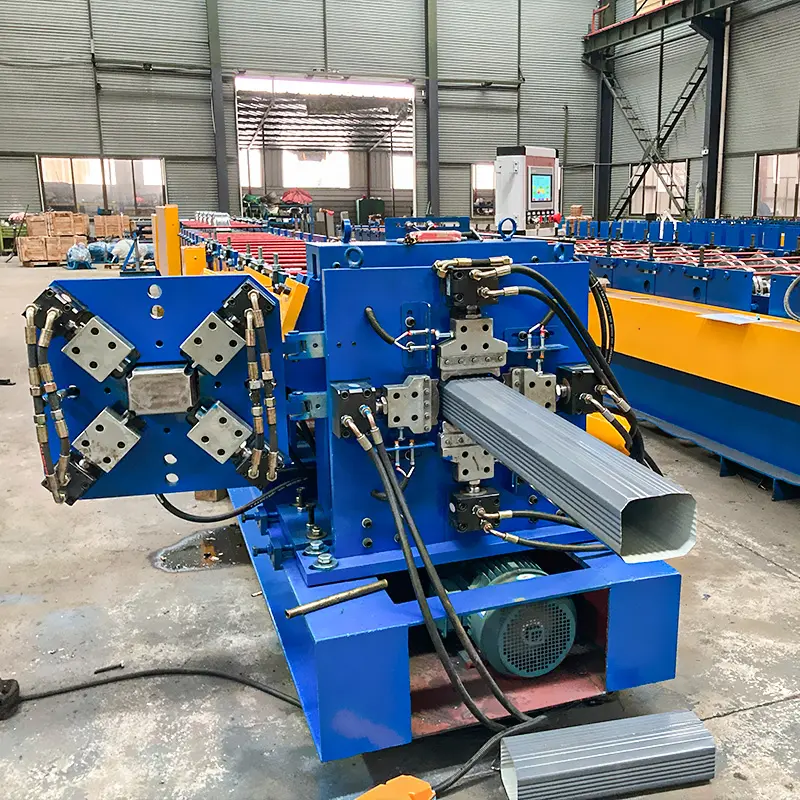
Types of Floor Deck Machines
Floor deck machines come in various configurations to meet the diverse needs of the construction industry. Here are some common types:
Machine Type | Description |
---|---|
Mobile Floor Deck Machines | These machines are designed to be portable and can be easily transported between construction sites, making them ideal for on-site decking production. They are typically mounted on trailers or skids for easy relocation. |
Stationary Floor Deck Machines | As the name suggests, these machines are designed for permanent installation in a manufacturing facility or dedicated production area. They offer higher production capacities and are suitable for large-scale decking projects. |
Multi-Profile Floor Deck Machines | These versatile machines can produce multiple decking profiles by using interchangeable roller sets. This flexibility allows contractors to meet various project requirements with a single machine. |
Automated Floor Deck Machines | Advanced floor deck machines feature automation systems for material handling, profile adjustments, and quality control. These machines offer increased productivity and consistent decking quality. |
The Working Process of Floor Deck Machines
Floor deck machines operate on a continuous roll-forming principle, where a coiled steel strip is progressively shaped into the desired decking profile. The process typically involves the following steps:
- Material Feeding: The coiled steel strip is loaded onto a decoiler, which feeds the material into the machine at a controlled rate.
- Straightening: The steel strip passes through a series of straightening rollers to remove any curvature or irregularities from the coiling process.
- Forming: The straightened steel strip then enters the forming section, where a series of precision rollers gradually shape the material into the desired corrugated decking profile.
- Slitting (Optional): In some cases, the formed decking panel may need to be slit or cut to the required width, which is accomplished by integrated slitting mechanisms.
- Cutting: Once the desired length is reached, the formed decking panel is cut to size using a shear or flying shear mechanism.
- Stacking: The finished decking panels are then stacked or bundled for transportation or installation.
Throughout the process, various quality control measures are implemented to ensure dimensional accuracy, consistent profile formation, and overall product quality.
Material Feeding and Forming
Process | Description |
---|---|
Material Feeding | Coiled steel strips, typically in gauges ranging from 16 to 24, are loaded onto a decoiler or uncoiler mechanism. The strip is then fed into the machine at a controlled rate to ensure consistent material flow. |
Straightening | Before forming, the steel strip passes through a series of straightening rollers to remove any curvature or irregularities caused by the coiling process. This step ensures a flat and consistent material feed for precise profile formation. |
Forming | The straightened steel strip enters the forming section, where a series of precision rollers gradually shape the material into the desired corrugated decking profile. The rollers are arranged in a specific configuration to progressively bend and form the steel into the required shape. |
Slitting (Optional) | In some cases, the formed decking panel may need to be slit or cut to a specific width. This is accomplished by integrated slitting mechanisms, which use shear blades or rolling slitters to trim the panel to the desired width. |
The forming process is highly customizable, allowing manufacturers to produce a wide range of decking profiles to meet various project requirements and design specifications.
-
Vineyard Post Roll Forming Machine
-
Auto Size Changeable Sigma Purlin Roll Forming Machine
-
Auto Size Changeable C Z Purlin Roll Forming Machine
-
Auto Size Changeable Z Purlin Roll Forming Machine
-
Auto Size Changeable C U Purlin Roll Forming Machine
-
Electrical Cabinet Frame Roll Forming Machine
-
Din Rail Roll Forming Machine
-
Cable Ladder Roll Forming Machine
-
PV Mounting Bracket C Shape Profile Roll Forming Machine
Decking Design and Customization
Floor deck machines offer a high degree of design flexibility, enabling manufacturers to produce a variety of decking profiles to meet specific project requirements. The design of the decking profile plays a crucial role in determining the overall performance and load-bearing capacity of the composite floor system.
Design Aspect | Description |
---|---|
Profile Depth | The depth of the corrugations or embossments in the decking profile affects the overall strength and load-bearing capacity of the panel. Deeper profiles generally provide higher strength but may require more material. |
Rib Spacing | The spacing between the ribs or corrugations in the decking profile influences the distribution of loads and the overall stiffness of the panel. Closer rib spacing typically results in increased load-bearing capacity. |
Embossments | Embossments or indentations can be incorporated into the decking profile to enhance the mechanical bond between the steel deck and the concrete slab, improving the overall composite action. |
Acoustic Performance | Certain decking profiles are designed to provide improved acoustic performance by incorporating perforations or patterns that help reduce noise transmission. |
Fire Resistance | The design of the decking profile can also contribute to the fire resistance of the composite floor system, with certain profiles offering enhanced fire protection through their shape and material thickness. |
Many floor deck machines allow for easy changeover between different roller sets, enabling manufacturers to quickly switch between decking profiles to meet varying project demands.
Material Options for Floor Deck Machines
Floor deck machines can process a range of materials, depending on the specific application and project requirements. The most commonly used materials include:
Material | Description |
---|---|
Galvanized Steel | Galvanized steel is the predominant material choice for floor decking applications due to its strength, durability, and corrosion resistance. It is available in various gauges and coatings to meet different performance requirements. |
Stainless Steel | Stainless steel decking is suitable for applications that demand high corrosion resistance, such as in coastal or chemical environments. However, it tends to be more expensive than galvanized steel. |
Aluminum | Aluminum decking offers a lightweight alternative to steel, making it suitable for applications where weight is a critical factor. It also provides excellent corrosion resistance but may have lower structural strength compared to steel. |
Cold-Rolled Steel | Cold-rolled steel can be used for decking applications, particularly in non-structural or light-duty applications. It offers a cost-effective option but may have lower strength and durability compared to galvanized steel. |
The choice of material will depend on factors such as the intended application, load requirements, environmental conditions, and project budget.
Suppliers and Price Range
Floor deck machines are typically manufactured by specialized equipment companies that cater to the construction and steel forming industries. Some of the leading suppliers of floor deck machines include:
Supplier | Location | Price Range (Approximate) |
---|---|---|
Samco Machinery | Canada | $50,000 – $500,000 |
Bradbury Group | United States | $75,000 – $400,000 |
Schlüter Systems | Germany | $80,000 – $350,000 |
Rees M-tec | Germany | $60,000 – $300,000 |
Colt Solutions | United Kingdom | $70,000 – $450,000 |
The price range for floor deck machines can vary significantly depending on factors such as machine type, production capacity, automation level, and additional features. Entry-level or basic models may start around $50,000, while advanced, high-capacity machines can cost upwards of $500,000.
It’s important to note that these prices are approximate and can fluctuate based on market conditions, customization requirements, and additional components or accessories. It’s advisable to consult with reputable suppliers and obtain quotes based on your specific needs and project requirements.
Installation, Operation, and Maintenance
Proper installation, operation, and maintenance are crucial for ensuring the efficient and safe performance of floor deck machines.
Aspect | Description |
---|---|
Installation | Floor deck machines, particularly larger stationary models, often require specialized installation and setup procedures. This may involve securing the machine to a solid foundation, aligning components, and connecting utilities such as electricity and compressed air. Manufacturers typically provide detailed installation manuals and may offer on-site commissioning services. |
Operation | Operating a floor deck machine requires trained personnel who are familiar with the machine’s controls, safety protocols, and quality assurance procedures. Operators must ensure proper material feeding, monitor the forming process, and make necessary adjustments to maintain consistent decking quality. |
Maintenance | Regular maintenance is essential to extend the service life of floor deck machines and prevent breakdowns or production disruptions. This includes routine inspections, lubrication, roller replacements, and calibration of various components. Manufacturers typically provide maintenance schedules and recommended procedures in the machine’s operating manual. |
Failure to properly install, operate, or maintain floor deck machines can lead to safety hazards, equipment damage, and production delays, ultimately impacting project timelines and costs.
Choosing the Right Supplier
When selecting a supplier for floor deck machines, there are several factors to consider:
Factor | Description |
---|---|
Reputation and Experience | Look for suppliers with a proven track record in the construction and steel forming industry. Reputable suppliers with extensive experience are more likely to provide reliable equipment, technical support, and after-sales service. |
Product Range and Customization | Consider suppliers that offer a diverse range of floor deck machines, catering to different production capacities, decking profiles, and project requirements. Customization options can also be beneficial for tailoring the machine to your specific needs. |
Service and Support | Evaluate the level of service and support provided by the supplier, including installation assistance, training, spare parts availability, and prompt technical support in case of issues or breakdowns. |
Warranty and Guarantees | Review the warranty terms and any performance guarantees offered by the supplier. This can provide peace of mind and protect your investment in case of manufacturing defects or equipment failures. |
Price and Value | While price is a consideration, it’s essential to evaluate the overall value proposition offered by the supplier. Factors such as quality, durability, and long-term operational costs should be weighed against the initial purchase price. |
By carefully evaluating potential suppliers based on these factors, you can increase the likelihood of selecting a reliable partner who can provide high-quality floor deck machines and support your construction projects effectively.
Pros and Cons of Floor Deck Machines
Like any specialized equipment, floor deck machines have both advantages and limitations that should be considered:
Advantages
- On-Site Production: Floor deck machines enable the production of decking panels directly at the construction site, eliminating the need for transportation and reducing associated costs.
- Versatility: Many floor deck machines can produce a variety of decking profiles, catering to different project requirements and design specifications.
- Efficiency: The continuous roll-forming process allows for efficient and cost-effective production of decking panels, reducing material waste and labor costs.
- Quality Control: Floor deck machines incorporate various quality control measures to ensure consistent profile formation, dimensional accuracy, and overall product quality.
- Customization: Manufacturers can customize the decking profiles to meet specific load requirements, fire resistance ratings, or acoustic performance needs.
Limitations
- Initial Investment: Floor deck machines can be a significant capital investment, especially for larger stationary models or advanced automated systems.
- Space Requirements: Larger floor deck machines may require substantial floor space for installation and operation, which can be a challenge in space-constrained construction sites or facilities.
- Maintenance and Downtime: Regular maintenance and periodic replacement of components, such as rollers and shear blades, are necessary to ensure optimal performance and minimize downtime.
- Skilled Labor: Operating floor deck machines requires trained personnel who are familiar with the equipment, safety protocols, and quality assurance procedures.
- Material Limitations: While floor deck machines can process various materials, the range of compatible materials may be limited, and certain materials may require specialized equipment or additional processing steps.
When considering the use of floor deck machines, it’s essential to weigh these pros and cons against your specific project requirements, production demands, and budgetary constraints.
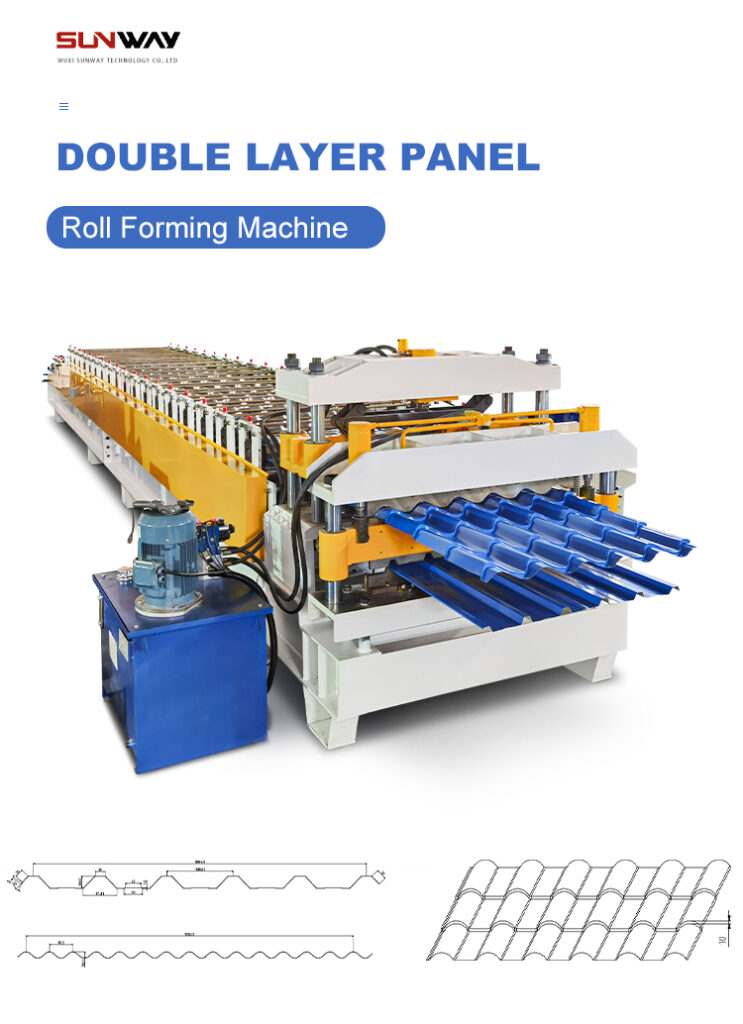
FAQ
Question | Answer |
---|---|
What is the typical production rate of floor deck machines? | The production rate of floor deck machines can vary depending on factors such as the machine’s capacity, the decking profile, and the material being used. Generally, production rates can range from 50 to 300 linear feet per minute for smaller machines, and up to 600 linear feet per minute for larger, high-capacity machines. |
Can floor deck machines produce decking panels for both steel and concrete composite floors? | Yes, floor deck machines are designed to produce corrugated steel decking panels that can be used in both steel and concrete composite floor systems. The decking panels serve as a permanent form for the concrete slab while also providing structural support. |
How are floor deck machines powered? | Most floor deck machines are electrically powered, requiring a suitable power source and electrical connections. Some models may also incorporate pneumatic or hydraulic systems for certain operations, such as material handling or cutting mechanisms. |
What is the typical lifespan of a floor deck machine? | With proper installation, operation, and maintenance, floor deck machines can have a lifespan of 10 to 15 years or more. Regular inspections, lubrication, and replacement of wear components can help extend the machine’s service life. |
Can floor deck machines be customized to produce specialized decking profiles? | Yes, many floor deck machine manufacturers offer customization options, allowing them to produce specialized decking profiles to meet specific project requirements or design specifications. This may involve using custom roller sets or adjusting existing roller configurations. |
How do floor deck machines ensure consistent decking quality? | Floor deck machines incorporate various quality control measures, such as precision rollers, straightening mechanisms, and automated monitoring systems. These measures help ensure consistent profile formation, dimensional accuracy, and overall product quality throughout the production process. |
What are the typical safety considerations when operating a floor deck machine? | Safety considerations include proper machine guarding, emergency stop mechanisms, and adherence to established safety protocols. Operators should receive training on safe operating procedures, wear appropriate personal protective equipment, and follow all manufacturer-provided safety guidelines. |