The construction industry is experiencing a seismic shift, thanks to advances in prefabrication and modular building technologies. Among the key enablers of this transformation are Prefabricated Wall Panel Roll Forming Machines, which play a vital role in creating precise, durable, and customizable wall panels for modern construction projects. From residential housing to commercial buildings and industrial facilities, prefabricated wall panels are becoming the go-to solution for fast, efficient, and sustainable construction.
In this guide, we’ll explore Prefabricated Wall Panel Roll Forming Machines, diving into their features, applications, technological advancements, benefits, pricing, and insights into why Wuxi Sunway Machinery is a leader in this space. Whether you’re a construction professional or a manufacturing expert, this article will provide everything you need to know about these transformative machines.
What is Prefabricated Wall Panel Roll Forming Machines?
Prefabricated Wall Panel Roll Forming Machines are highly specialized equipment used to manufacture steel wall panels and profiles for prefabricated and modular construction. The machine processes steel coils into specific panel designs, combining high-speed production with precision engineering. These panels are then assembled into prefabricated walls, which can be quickly installed on-site.
The roll-forming process involves feeding a coil of raw material through a series of rollers that progressively shape it into the desired dimensions and profiles. Modern machines also integrate additional features such as punching, cutting, and embossing to further customize the panels, making them compatible with various architectural and structural requirements.
In an era where speed, sustainability, and efficiency define the construction industry, Prefabricated Wall Panel Roll Forming Machines are helping manufacturers and builders stay ahead of the curve.
Applications of Prefabricated Wall Panels
Prefabricated wall panels are used in a variety of construction projects, ranging from residential to industrial applications. Here are some of their most common uses:
1. Residential Construction
- Use Case: Prefabricated wall panels are widely adopted in housing projects for exterior and interior walls.
- Why It Matters: They reduce construction time, ensure uniform quality, and can be easily customized for aesthetic and functional requirements.
2. Commercial Buildings
- Use Case: Office buildings, retail stores, and warehouses often use prefabricated wall panels for both structural and non-structural walls.
- Why It Matters: Panels provide a cost-effective and durable solution for large-scale projects.
3. Industrial Facilities
- Use Case: Factories, workshops, and storage units benefit from the strength and durability of steel prefabricated wall panels.
- Why It Matters: These panels are designed to withstand harsh conditions, including heavy loads, high winds, and extreme temperatures.
4. Modular Construction
- Use Case: Prefabricated wall panels are essential in modular construction, where entire sections of buildings are pre-assembled off-site.
- Why It Matters: They enable rapid assembly and disassembly, offering flexibility and reusability.
5. Temporary Structures
- Use Case: Prefabricated wall panels are used in temporary setups like disaster relief shelters, event spaces, and pop-up stores.
- Why It Matters: Lightweight and easy-to-install panels ensure quick deployment and removal.
6. Energy-Efficient Buildings
- Use Case: Panels are integrated into green building designs, often featuring thermal insulation and weatherproofing layers.
- Why It Matters: Enhances energy efficiency while reducing a building’s carbon footprint.
Key Features of Wuxi Sunway Prefabricated Wall Panel Roll Forming Machines
When it comes to manufacturing high-quality wall panels, Wuxi Sunway Machinery offers state-of-the-art solutions. Here’s what makes their Prefabricated Wall Panel Roll Forming Machines stand out:
1. Customizable Panel Designs
- What It Does: Produces wall panels in various sizes, thicknesses, and profiles, including flat, ribbed, and corrugated designs.
- Why It’s Important: Allows manufacturers to cater to diverse construction needs and architectural styles.
2. High-Speed Production
- Performance: Capable of producing up to 25 meters of wall panels per minute.
- Why It Matters: Ensures fast production to meet tight project deadlines without compromising quality.
3. Integrated Punching and Embossing Systems
- Features: Punching systems create holes or slots for electrical conduits and plumbing, while embossing adds texture for aesthetic appeal or functional purposes.
- Why It’s Important: Reduces the need for secondary operations, saving time and labor.
4. Precision Cutting Technology
- Technology Used: Servo-controlled cutting systems deliver burr-free, clean edges.
- Why It Matters: Enhances panel quality and reduces material waste.
5. Material Versatility
- Supported Materials:
- Galvanized steel
- Aluminum
- Cold-rolled steel
- Pre-painted steel
- Thickness Range: 0.4mm–1.5mm
- Why It’s Crucial: Ensures compatibility with different building requirements, from lightweight to heavy-duty applications.
6. PLC-Controlled Automation
- Features:
- Fully programmable logic controllers (PLC) with a user-friendly touchscreen interface.
- Stores multiple panel designs and production parameters.
- Real-time monitoring and error detection.
- Why It’s Revolutionary: Simplifies operation and ensures consistent production quality.
7. Eco-Friendly Design
- What It Offers: Energy-efficient motors and process optimization reduce electricity consumption and waste.
- Why It Matters: Supports sustainable manufacturing practices.
8. Compact and Modular Design
- What It Does: Offers a space-saving design that integrates seamlessly into existing production lines.
- Why It Matters: Optimizes factory floor space and allows for easy upgrades.
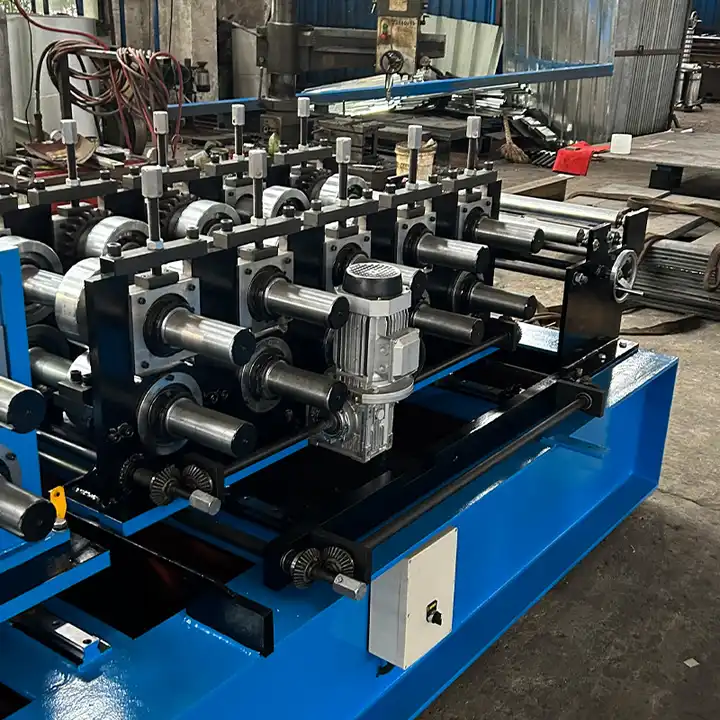
Production Workflow of Prefabricated Wall Panel Roll Forming Machines
The production process is streamlined for efficiency and precision. Below is an overview of the workflow:
1. Decoiling
- Steel or aluminum coils are loaded onto the decoiler, which feeds the material into the machine.
2. Leveling
- A leveling system ensures the material is flat and free of warping before it enters the roll-forming section.
3. Roll Forming
- The material passes through a series of rollers, which progressively shape it into the desired panel profile.
4. Punching and Embossing
- Integrated units add holes, slots, or textures to the panels as needed.
5. Cutting
- A servo-controlled cutting system trims the panels to the required lengths with precision.
6. Stacking
- Finished panels are automatically stacked for easy packaging and transportation.
Pricing of Prefabricated Wall Panel Roll Forming Machines
The cost of Prefabricated Wall Panel Roll Forming Machines depend on its features, production capacity, and level of automation. Below is a general pricing guide for 2025:
Machine Type | Capabilities | Price Range (USD) |
---|---|---|
Basic Machines | Standard wall panel production | $80,000–$120,000 |
High-Speed Machines | Enhanced speed with punching and embossing | $120,000–$180,000 |
Fully Customizable Machines | Advanced features and multi-profile capability | $180,000–$250,000 |
For tailored pricing and financing options, contact Wuxi Sunway Machinery.
Advantages of Using Prefabricated Wall Panel Roll Forming Machines
Investing in Prefabricated Wall Panel Roll Forming Machines offer numerous benefits for manufacturers:
1. Speed and Efficiency
- High-speed production reduces lead times and increases output.
2. Customization
- Allows for the creation of various panel designs, catering to different construction needs.
3. Precision
- Advanced automation ensures consistent quality, minimizing defects and rework.
4. Cost Savings
- Reduces material waste and labor costs, improving overall profitability.
5. Sustainability
- Eco-friendly features support green manufacturing initiatives.
FAQs About Prefabricated Wall Panel Roll Forming Machines
Question | Answer |
---|---|
What is the production speed? | Machines can produce up to 25 meters per minute, depending on material and profile. |
Can the machine produce custom profiles? | Yes, programmable settings allow for custom dimensions and designs. |
What materials are compatible? | Galvanized steel, aluminum, cold-rolled steel, and pre-painted steel. |
Is operator training included? | Yes, comprehensive training is provided with every machine purchase. |
What is the warranty period? | All Sunway machines come with a 12-month warranty, with extended options available. |
How long does installation take? | Installation and commissioning typically take 5–10 days, depending on factory setup. |
Does Sunway provide after-sales support? | Absolutely! Sunway offers full technical support, including spare parts and troubleshooting. |
Global Trends Driving the Demand for Prefabricated Wall Panel Roll Forming Machines
The construction industry is evolving rapidly, driven by technology, urbanization, and the need for sustainable infrastructure. Let’s explore the key trends influencing the demand for Prefabricated Wall Panel Roll Forming Machines in 2025:
1. The Rise of Modular Construction
- The Numbers: The global modular construction market is expected to grow to $157 billion by 2030, with a compound annual growth rate (CAGR) of 7.1%.
- Impact on Wall Panels: Prefabricated wall panels are a cornerstone of modular construction, offering speed and efficiency.
- Why It Matters: Roll-forming machines enable manufacturers to produce panels at scale, meeting the increasing demand for modular buildings.
2. Growing Urbanization
- The Context: By 2050, nearly 68% of the world’s population will live in urban areas, driving the need for affordable and efficient housing.
- Impact on Wall Panel Manufacturing: High-density urban housing projects require cost-effective, durable, and quick-to-install wall panels.
- Machine Relevance: High-speed roll-forming machines can produce wall panels rapidly, reducing construction timelines.
3. Sustainability and Green Building Initiatives
- The Push: Governments and organizations are emphasizing eco-friendly construction practices to reduce carbon emissions.
- Impact on Wall Panels: Panels with insulation and weatherproofing features are essential for energy-efficient buildings.
- Why It’s Important: Roll-forming machines help create lightweight, recyclable panels that align with green building standards.
4. Increased Demand for Disaster-Resilient Structures
- The Trend: Areas prone to natural disasters, like hurricanes and earthquakes, require buildings with strong and durable wall panels.
- Impact on Panel Design: Steel prefabricated panels are preferred for their ability to withstand extreme conditions.
- Machine Relevance: Roll-forming machines can produce high-strength panels tailored to these requirements.
5. Technological Integration in Construction
- What’s Happening: The adoption of Building Information Modeling (BIM) and other digital tools is streamlining construction processes.
- Impact on Wall Panel Production: Panels need to meet precise specifications to integrate seamlessly with BIM workflows.
- Why It’s Exciting: Roll-forming machines with programmable settings ensure precision and compatibility with modern construction technologies.
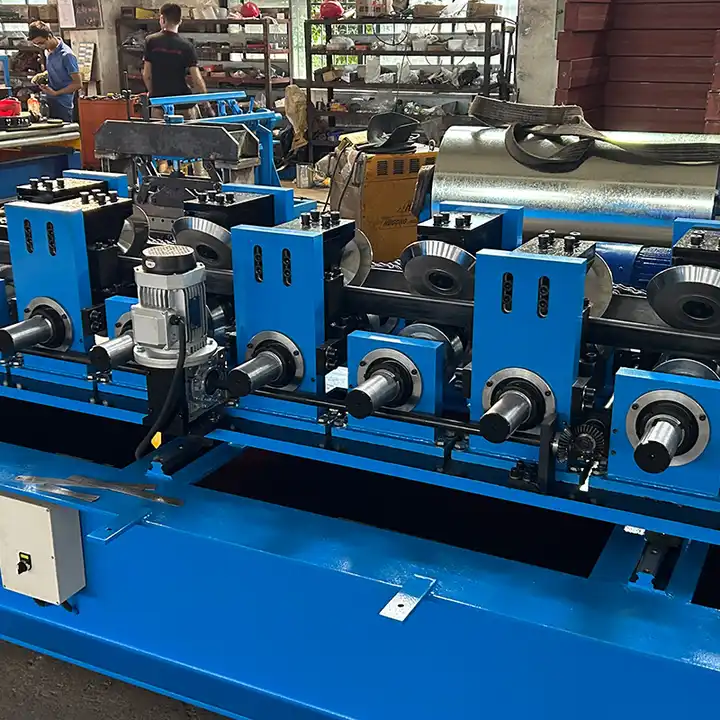
Technological Advancements in Prefabricated Wall Panel Roll Forming Machines
The evolution of Prefabricated Wall Panel Roll Forming Machines has been fueled by technological innovations. Here are the key advancements shaping their future:
1. IoT-Enabled Smart Machines
- What It Does: IoT (Internet of Things) integration allows machines to connect to a centralized platform for monitoring and diagnostics.
- Benefits:
- Real-time performance tracking optimizes production.
- Predictive maintenance reduces downtime.
- Remote monitoring enhances operational convenience.
2. Multi-Profile Capabilities
- What It Offers: Modern machines can switch between different panel profiles, such as ribbed, corrugated, and flat, without manual intervention.
- Why It’s Revolutionary: Saves time and expands the range of products manufacturers can offer.
3. Servo-Driven Systems for Precision
- How It Works: Servo motors control cutting and punching systems with exceptional accuracy.
- Advantages:
- Ensures clean edges and accurate hole placement.
- Reduces material waste and enhances product quality.
4. Digital Twin Technology
- What It Is: A virtual replica of the machine that allows manufacturers to simulate production runs.
- Why It’s Transformative:
- Speeds up prototyping and design testing.
- Reduces the risk of errors during full-scale production.
5. Enhanced Safety Features
- Key Features:
- Emergency stop buttons for immediate shutdown.
- Load sensors to prevent overfeeding of materials.
- Safety shields around moving parts to protect operators.
- Why It’s Critical: Ensures a safe working environment without compromising productivity.
6. Compact and Modular Construction
- What It Does: Reduces the machine’s footprint, making it suitable for factories with limited space.
- Why It Matters: Optimizes space while maintaining high production capacity.
Environmental Benefits of Prefabricated Wall Panel Roll Forming Machines
Sustainability is at the forefront of modern construction, and Prefabricated Wall Panel Roll Forming Machines contribute to this goal in several ways:
1. Efficient Material Usage
- What It Does: Optimizes material usage, minimizing scrap and reducing waste.
- Why It Matters: Lowers production costs and environmental impact.
2. Energy Conservation
- The Innovation: Machines equipped with energy-efficient motors consume less electricity during operation.
- Impact: Supports manufacturers in achieving their sustainability goals.
3. Recyclable Outputs
- The Benefit: Steel and aluminum panels produced by these machines are 100% recyclable.
- Why It’s Important: Encourages a circular economy and reduces landfill waste.
4. Localization of Production
- What It Does: Enables manufacturers to produce panels locally, reducing the carbon footprint associated with transportation.
- Outcome: Supports regional economies and sustainability initiatives.
Comparison: Prefabricated Wall Panel Roll Forming Machines vs. Traditional Methods
Here’s how Prefabricated Wall Panel Roll Forming Machines stack up against conventional manufacturing methods like manual welding or extrusion:
Feature | Roll Forming Machine | Traditional Methods |
---|---|---|
Speed | High; up to 25 meters per minute | Slow; dependent on manual labor |
Precision | High; ensures consistent dimensions | Moderate; prone to human error |
Automation | Fully automated with PLC and IoT integration | Mostly manual or semi-automated |
Material Waste | Minimal; optimized processes reduce scrap | Higher; less efficient material usage |
Customization | Easily customizable for various profiles | Limited flexibility; requires separate tooling |
Cost Efficiency | High; lower long-term costs | Lower initial cost, higher operational costs |
Scalability | Ideal for large-scale production | Not suitable for high-volume projects |
Additional FAQs About Prefabricated Wall Panel Roll Forming Machines
Question | Answer |
---|---|
What is the production capacity? | Machines can produce up to 25 meters of panels per minute, depending on material and design. |
Can the machine produce insulated panels? | Yes, with additional features, the machine can create panels that include thermal insulation. |
What materials can be used? | Galvanized steel, aluminum, pre-painted steel, and cold-rolled steel are compatible. |
Is training included with the purchase? | Yes, comprehensive operator training is provided with every purchase. |
What is the machine’s lifespan? | With proper maintenance, the machine can last 10–15 years or more. |
Does Sunway provide spare parts? | Absolutely! Sunway offers a complete range of spare parts and after-sales support. |
Can I customize the machine to my needs? | Yes, Sunway specializes in tailoring machines to meet unique production requirements. |
Why Choose Wuxi Sunway Machinery for Prefabricated Wall Panel Roll Forming Machines?
Here’s why Wuxi Sunway Machinery is the global leader in roll-forming technology:
- Decades of Experience: Proven expertise in delivering roll-forming solutions tailored to global markets.
- Customization: Machines designed to meet specific production and architectural requirements.
- Sustainability: Eco-friendly design minimizes waste and energy consumption.
- Innovation: Cutting-edge technology, including IoT and servo-driven systems.
- Worldwide Reach: Trusted by clients in Asia, Europe, Africa, and the Americas.
- Comprehensive Support: From installation to troubleshooting and spare parts, Sunway provides end-to-end service.
Conclusion: Building Smarter, Faster, and Greener
The Prefabricated Wall Panel Roll Forming Machines are transforming the construction industry by enabling the efficient production of high-quality wall panels. Whether for housing, commercial buildings, or industrial facilities, these machines empower manufacturers to meet the demands of modern construction—quickly, sustainably, and at scale.
Are you ready to elevate your production capabilities? Contact Wuxi Sunway Machinery today to explore their innovative roll-forming solutions. Together, let’s build the future of construction—one wall panel at a time!