Roofing corrugated sheet roll forming machines produce corrugated metal panels from coil feedstock for roofing and siding construction products. This guide reviews corrugated sheet roll former types, components, processes, customization, operation and maintenance to inform manufacturers.
Roofing Corrugated Sheet Roll Forming Machine Overview
Roofing corrugated sheet roll formers transform flat metal coil stock into profiled corrugated panels used across industrial and commercial roofing applications. Key attributes:
- High hourly production volumes lower per piece cost
- Flexibility producing various corrugation profiles
- Reduced material waste versus stamping processes
- Continuous lights out production after coil loading
Reviewing line configurations, specifications, customization options and maintenance procedures assists manufacturers maximizing productivity.
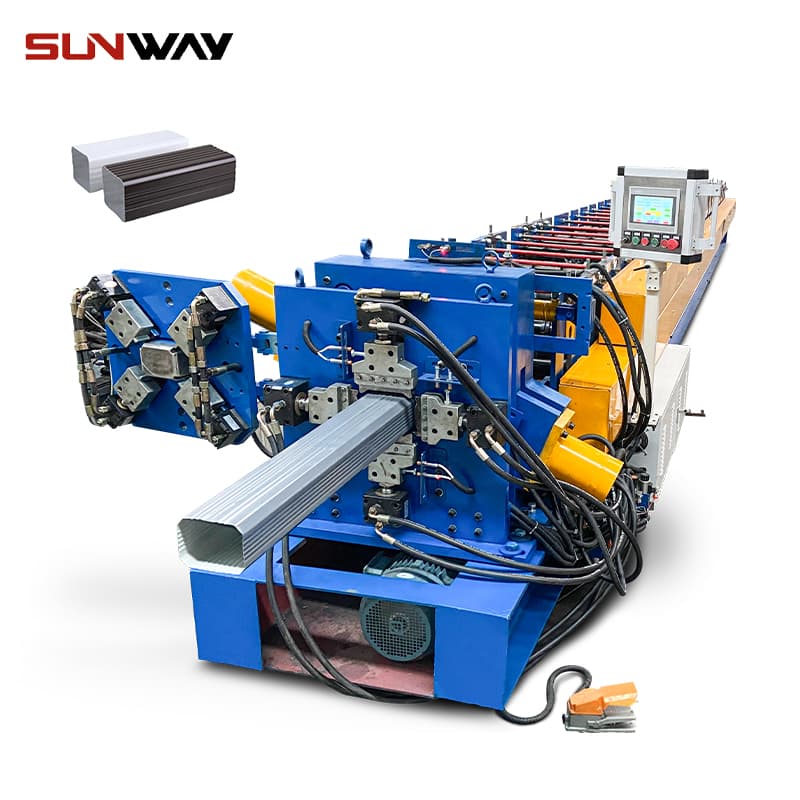
Types of Roofing Corrugated Sheet Roll Formers
Common roll former types include:
Type | Description |
---|---|
Mechanical | Hydraulic powered stations via mechanical gearboxes |
Servo Electric | Independent servo motors control stations |
Single Layer Lines | For standard smaller corrugation sizes |
Double Layer Lines | Profile both sides simultaneously |
Table 1: Roofing corrugated sheet roll former types covering mechanical versus servo configurations plus single and double layer machines
While electric servo precision enables faster product changeover, mechanical gears provide affordable reliability at slower running speeds. Multi-layer machines boost output for standard commodities.
Roll Forming Process for Corrugated Roof Sheeting
The multi-stage roll forming process flow generally entails:
Decoiling – Coil stock enters powered decoiler holding tension
Feeding – Feed rolls pull steel through subsequent stations
Pre-forming – Sheet lightly forms into early wave pattern
Corrugating – Successive stands shape distinct ridges and valleys
Cutting – Hydraulic shear slices pieces to length
Counting – Automated counters tally sheets
Stacking – Formed sheets placed onto powered exit conveyor tables
Synchronizing these steps enables high volume corrugated panel production.
Key Components of Corrugated Roofing Roll Lines
Typical sub systems include:
- Decoiler – Holds coil strip feeding line input
- Feed System – Pulls stock into first forming stand
- Forming Stands – Progressively corrugate the sheet
- Hydraulics System – Powers mechanical gearbox drive
- PLC Control System – Automates speed and piece counting
- Cutter – Slices corrugated sheets to length
- Exit Conveyor – Stacks or removes finished parts
Interlinking these engineered modules maximizes efficiency for metal roofing components.
-
Electrical Cabinet Frame Roll Forming Machine
-
Din Rail Roll Forming Machine
-
Cable Ladder Roll Forming Machine
-
PV Mounting Bracket C Shape Profile Roll Forming Machine
-
Cable Tray Roll Forming Machine
-
Steel Coil Cut To Length Line Machine
-
Steel Coil Cut To Length Line Machine
-
Steel Coil Cut To Length Line Machine
-
PV Mounting Bracket Roll Forming Machine (HAT / Omega Profile)
Customizing Roofing Corrugated Roll Formers
Although standardized, common customization considerations include:
- Tooling – Special roll sets match customer panel geometries
- Speed – Servo electric drives for faster cycles
- Automation Range – Monitoring and robotic stacking/packaging integration
- Decoiler Capacity – Larger coils mean fewer loading stoppages
- Integrated Painting – Inline liquid or powder coating
- Secondary Operations – Custom post-forming fabrication steps
Detailing such engineering requirements in requests for quotes allows pricing specialty customization supporting business goals.
Selecting Roofing Corrugated Roll Former Suppliers
When evaluating suppliers, recommended criteria includes:
- Specialization – Seek dedicated roll former machine vendors
- Experience – Review manufacturer lineage and client portfolio
- Design Services – Offer engineering support for custom needs
- Quality – Require all steel welded equipment
- Validation – Look for quality management system certifications
- Services – Installation, operator training and maintenance packages
- Pricing – Validate turnkey pricing ensuring feature parity
Vetting numerous manufacturers on tailored engineering, production prowess and ongoing services support provides confidence when investing in major factory automation.
Roofing Corrugated Roll Former Pricing
Budget estimates for complete roll forming lines span:
- Base Machine – Around $100,000 starting point
- Size customization – For longer decoilers add $5,000-$15,000
- Servo upgrades – Adds $20,000-$50,000 versus base mechanical drives
- Conveyors/Transfers – $5,000-$15,000 depending on automation
- Install/Transport – Typically extra $15,000-$25,000 for professional integration
Factor $150,000 to $250,000+ for turnkey lines aligning prices to standard versus customized specifications ultimately matching target business throughput and flexibility prerequisites demanded.
Operating and Maintaining Roofing Corrugated Roll Formers
To sustain production levels across years, recommended practices encompass:
Daily Cleaning – Clear line debris inhibiting transfers
Scheduled Inspections – Monthly inspect hydraulics, electrics and alignments
Roll Maintenance – Lubricate/resurface standings experiencing scratches quarterly
Recalibration – Annual overhaul inspecting sensors, alignments and clearances
Consistent monitoring enables catching wear early preventing unplanned downtime through replacing components proactively well aligned optimizing budgeting cycles.
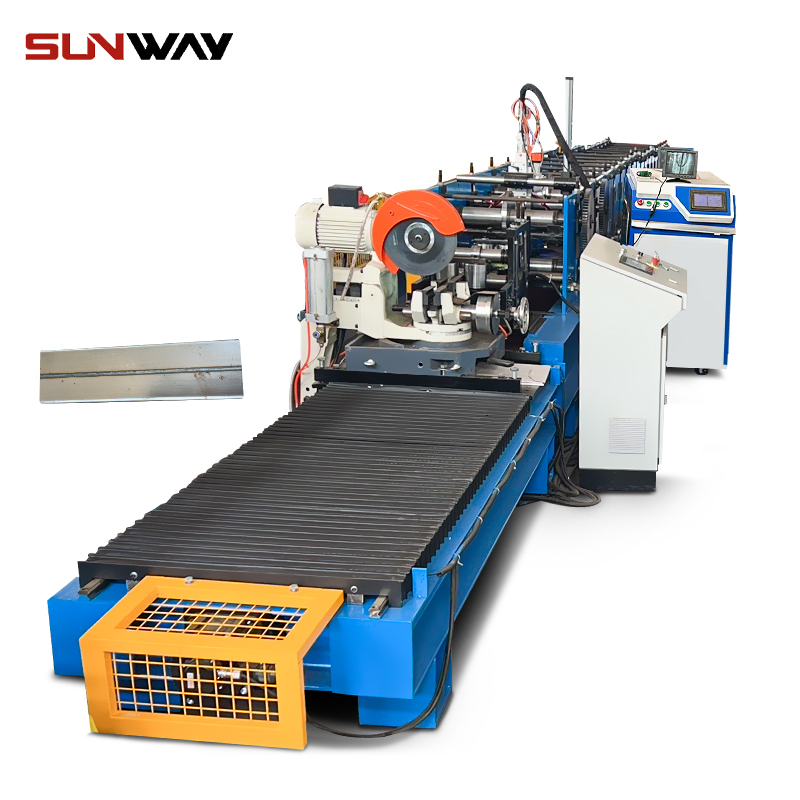
Common Roll Former versus Stamp Press Comparison
Consideration | Roll Forming | Stamping Presses |
---|---|---|
Setup Time | Hours | Days |
Lead Time | Weeks | Months |
Tooling Cost | Tens of thousands | Hundreds of thousands |
Material Utilization | 95%+ | 60% |
Short Run Capability | Strong | Limited |
Product Complexity | Simpler profiles | High complexity achievable |
Table 2. Comparing roll forming against large stamping press approaches for corrugated building products
For flexibility enabling mixed products across varying batch sizes, roll forming solutions merit consideration evaluating optimal fabrication system investments matching business throughput targets.
FAQ
Q: What thickness and hardness levels can lines accommodate?
A: Most handle 0.4–1 mm steel and stainless steel across harness levels up to T1-Temper 300 series stainless with customized solutions beyond.
Q: What causes scratching on finished roofing panels?
A: Buildup on roll dies, press alignment drift or inadequate blowoff occasionally requiring increased vigilant monitoring ensuring pristine surface quality.
Q: Can a single line handle multiple corrugated profile types?
A: Yes, additional roll sets allow mixed products by enabling faster changeovers between various building panel geometries.
Q: What is the production speed range on these machines?
A: Mechanical lines typically operate around 20 meters per minute. Servo electric lines can achieve 100+ meters contingent upon installed power, press tonnage and stock feed capabilities.