A downspout roll forming machine is an important equipment used for manufacturing rainwater drainage downspouts and gutters from metal coils. This guide provides a comprehensive overview of downspout roll forming machines covering their working, types, applications, specifications, selection factors, installation, operation, maintenance and more.
Overview of Downspout Roll Forming Machine
A downspout roll forming machine is designed to transform metal coils into formed profiles for rainwater drainage systems in buildings.
What are Downspouts?
Downspouts, also known as rainwater downpipes, are vertical conduits used to collect and direct rainwater drainage from rooftop gutters down to the ground or storm water system. They are typically made from formed metal sheets.
Working of Downspout Roll Forming Machine
A downspout roll forming machine takes metal coil as input and converts it into formed downspout profiles by passing through consecutive forming stations. Each station progressively forms the sheet using rollers until the final profile is achieved. The formed downspout is then cut into lengths as required.
Advanced downspout roll forming machines allow quick changeover between different profiles through quick die change systems.
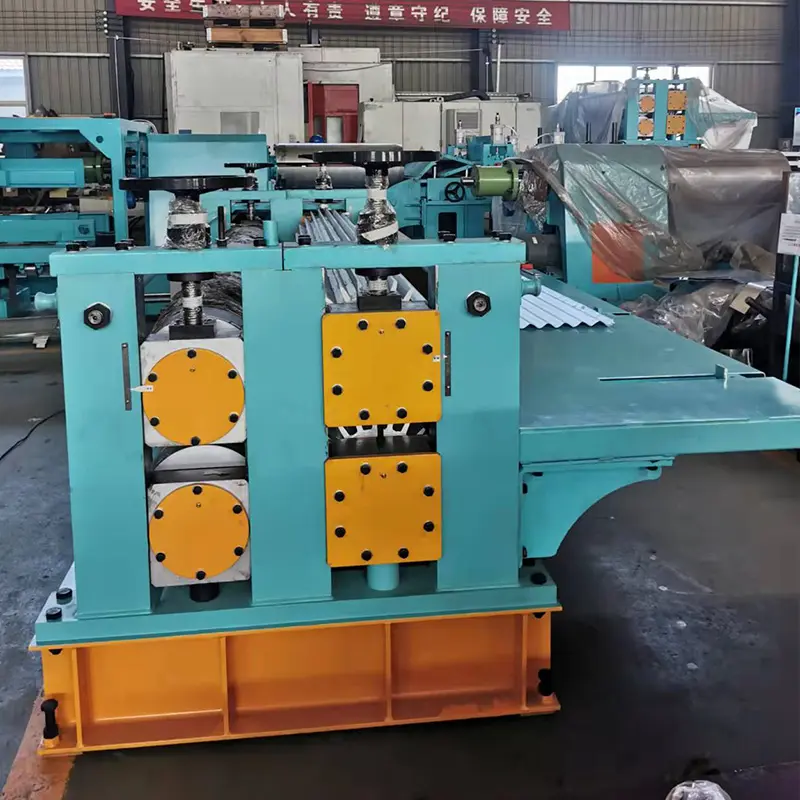
Types of Downspout Roll Forming Machines
Downspout roll forming machines are available in different configurations to suit different production requirements:
Based on Automation
- Manual: Require operator intervention at each station
- Semi-automatic: Automatic sheet feeding but manual profile changeover
- Fully automatic: Auto feeding, profiling, cut-off and stacking
Based on Production Speed
- Low speed: Up to 10 m/min
- Medium speed: 10 – 40 m/min
- High speed: Above 40 m/min
Higher speeds increase production capacity.
Based on Forming Stations
- 10-12 station for simple profiles
- 16-24 stations for complex double layer downspouts
- More stations allow more profile shapes
Based on Control System
- Mechanical manual control using levers
- Hydraulic automatic control for synchronization
- Servo motor with PLC/CNC control for precision and flexibility
Applications of Downspouts Produced by Roll Forming
Downspouts produced using roll forming machines are used in:
- Drainage systems for residential, commercial and industrial buildings
- Large warehouses, factories, aircraft hangars drainage
- Stadiums, auditoriums, exhibition halls water drainage
- Sloped roofs drainage for apartments, villas etc.
- Drainage around dams, bridges, underground sections
- Storm water harvesting and rainwater redirection
- Temporary structures like shelters and marquees
Roll formed downspouts offer faster, economical production compared to site fabrication.
Downspout Roll Forming Machine Specifications
Downspout roll forming machines are available in different specifications based on production requirements:
Specifications | Typical Range |
---|---|
Forming Speed | 10 – 80 m/min |
Forming Stations | 10 – 24 |
Metal Thickness | 0.3 – 1 mm |
Max Coil Width | 1000 – 1250 mm |
Min Downspout Size | 50 x 50 mm |
Max Downspout Size | 300 x 300 mm |
Power Consumption | 15 – 50 kW |
Cutting Mode | Auto/Semi-auto/Manual |
Control System | Mechanical, Hydraulic, Servo, PLC |
Machine Size | 10 – 25 m Long x 2 – 3 m Wide |
Machine Weight | 6000 – 15000 kg |
These parameters can be customized as per production needs.
Design and Working Standards
Downspout roll forming machines need to follow certain design standards:
- Use of high-tensile steel frames to minimize vibration at high speeds
- Decoupled drive design to allow speed variation between stations
- Hardened rollers and guides for reduced wear and smooth sheet flow
- Multi-axis powered decoilers for consistent sheet feeding
- Precision gearing and gear boxes for accurate profile forming
- Hydraulic press system for uniform pressure application
- Safety features like emergency stops, light curtains
- Dust proof electrical cabinet and controls
The roll tooling and bending sequence should be optimized using FEA analysis for uniform material flow without cracks or thinning.
Choosing a Downspout Roll Forming Machine Manufacturer
Here are some tips for choosing a good downspout roll forming machine manufacturer:
Parameter | What to Look For |
---|---|
Experience | Number of years in business, long operating history |
Production Facility | In-house manufacturing with quality control |
Customization | Ability to customize machine to needs |
Quality | Advanced automation for consistent quality |
Certification | ISO 9001, CE certifications |
Service | Installation support, operator training |
Cost | Competitive pricing and payment terms |
Delivery | Ready inventory of standard models |
Location | Distance for logistics and service |
- Check sample profiles from machines for quality
- Ensure availability of technical support after purchase
- Compare pricing and delivery lead times
- Visit factory if possible to inspect manufacturing process
- Choose reputed manufacturer for reliable equipment
This helps get high performance roll forming machines suited for requirements.
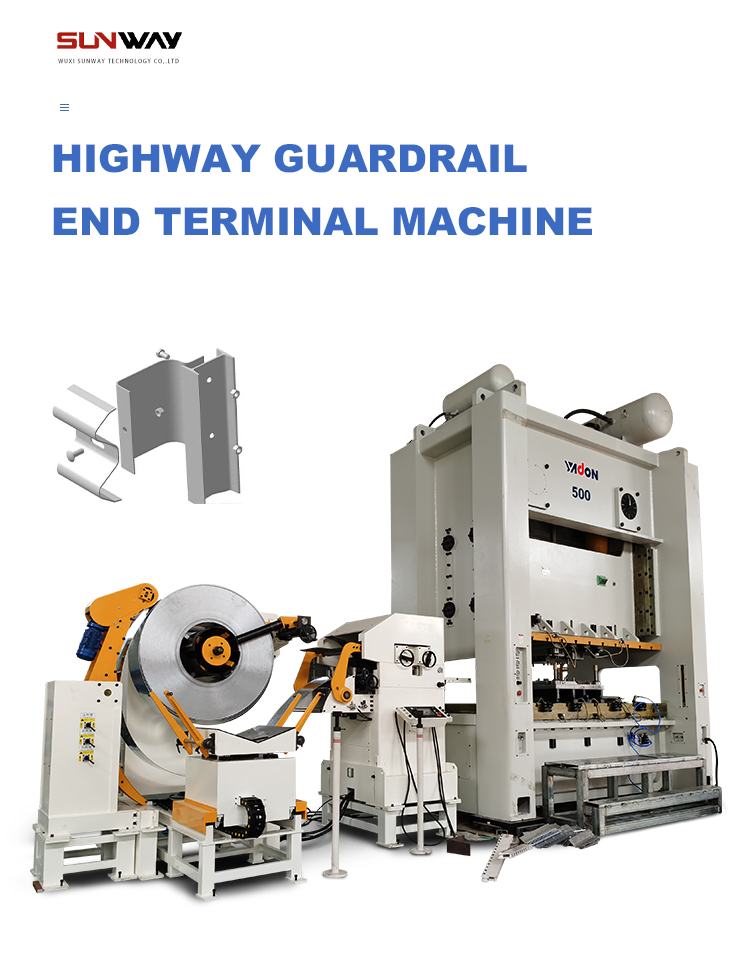
Downspout Roll Forming Machine Installation
Proper installation is key for smooth functioning of the downspout roll forming line:
- Prepare concrete foundation and position machine using lifting equipment
- Level the machine frame using shims and grout as required
- Assemble the roll forming sections according to drawing
- Install the decoiler, straightener, join stations using alignments
- Connect the gearbox drive shafts between stations
- Wire up the electrical switches, drives and controls
- Install the guards around gears, rollers and other moving parts
- Lube oil circulation and hydraulics functioning if any
- Ground the machine properly through earth pits
- Trial run the machine and make adjustments as needed
Correct installation as per manufacturer’s manual is important for safety and performance.
Working and Operation of Downspout Roll Forming Machine
Operating a downspout roll forming machine involves these steps:
Pre-Operation Checks and Settings
- Check electrical wiring, hydraulics, lubrication
- Set up decoiler with adequate coil weight tension
- Set shear press setting depending on material thickness
- Adjust rollers in each station for proper sheet flow
- Set stops as per downspout cut length required
- Set guides properly to avoid skewing during running
- Clear any material scrap or oil residue on the running track
Starting the Machine
- Start the machine in jog mode and observe each station
- Power on the coil decoiler and feed the sheet through the stations
- Gradually increase speed from the panel to reach working speed
- Adjust decoiler tension, shear press setting as needed
- Initiate automatic cut-off and stacking if equipped
- Run production after ensuring proper profile forming
During Operation
- Monitor rollers contour from wear and adjust periodically
- Listen for any abnormal noise at stations, stop and inspect
- Ensure proper lubrication on all moving parts
- Periodically test profile dimensions using gauges
- Stop the line before coil change and remove residual sheet
- Clean oil spills or metal scrap around the machine
Shut Down
- Gradually reduce speed to zero to clear all material
- Switch off power to the decoiler, straightener, and shear stations
- Turn off the main power and lock out electrically
- Clean the area and machine thoroughly for next use
Following standard operating procedures is important for quality and safety.
Maintenance of Downspout Roll Forming Machines
Regular maintenance activities ensure trouble-free working of downspout roll forming machines:
Activity | Frequency | Method |
---|---|---|
Cleaning | Daily | Remove scrap, oil spills, dust from machine area |
Inspection | Daily | Check for abnormal noise, heating, leaks |
Lubrication | Weekly | Grease bearings, gears, apply chain lube |
Roller Inspection | Monthly | Check contour, replace worn rollers |
Drive Inspection | Monthly | Check chain/belt tension, adjust/replace if required |
Electricals | Quarterly | Check loose connections, insulations, repair if needed |
Hydraulics | Quarterly | Check cylinders, pumps, pipes for leakages |
Gearbox | Yearly | Change gear oil as per schedule |
- Maintain daily, weekly, and monthly schedules for cleaning, inspection, lubrication
- Schedule preventive maintenance during plant shutdowns
- Keep sufficient spares like seals, bearings, rollers in stock
- Train technicians on equipment maintenance activities
- Maintain maintenance logs to track issues and improvements
Proper maintenance improves machine life andavoids unexpected breakdowns.
Troubleshooting Issues in Downspout Roll Forming Machines
Some common issues faced in downspout roll forming machines are:
Issue | Possible Causes | Solutions |
---|---|---|
Sheet jamming | Rollers have wear and gaps Improper decoiler tension Guides misaligned | Replace worn rollers Adjust decoiler tension Realign guides |
Profile distortion | Rollers gaps uneven Material feed not straight Station levels uneven | Set roller gaps evenly Adjust material feed alignment Re-level forming stations |
Excessive noise | Loose fasteners Bearing wear Chain sprocket worn | Tighten loose nuts, bolts Replace worn bearings Replace worn sprockets |
Hydraulic oil leak | Hose damage Seal worn out | Replace damaged hoses Change worn seals |
Machine vibration | Station misaligned Foundation bolts loose | Realign stations Tighten foundation bolts |
Analyzing root cause and correcting deficiencies can resolve common roll forming machine issues.
Improving Productivity of Downspout Roll Forming Machines
Some ways to improve productivity from downspout roll forming machines are:
- Optimize line speed by reducing bottlenecks
- Schedule rapid die changeovers to maximize production runs
- Automate processes downstream like cut-off and stacking
- Ensure consistent quality of input raw material
- Train operators on standard operating procedures
- Track overall equipment efficiency and target improvements
- Reduce unplanned downtime through preventive maintenance
- Keep sufficient inventory of wearing spares like rollers
- Upgrade machine with features like servo control, IoT data over time
With the right initiatives, substantial productivity gains can be achieved from downspout roll forming lines.
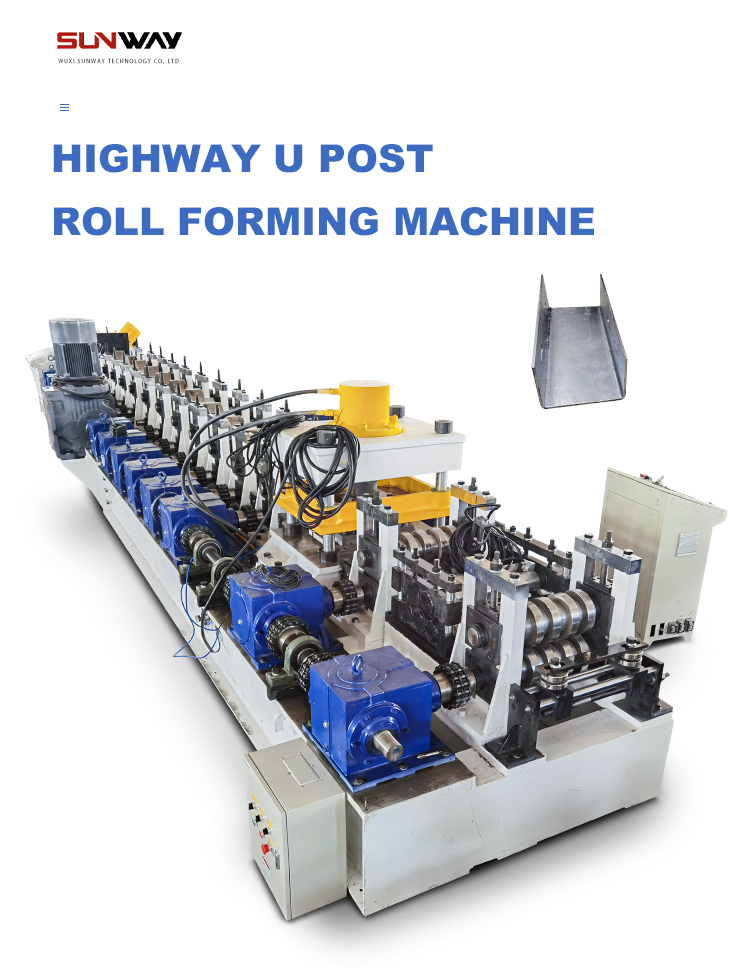
FAQs
Q: What is the typical production capacity of downspout roll forming machines?
A: Production capacity depends on machine speed and profiles – typically 30-50 meters/min resulting in around 500-800 meters/hr output.
Q: What thickness of coils can be used?
A: Machines can typically process 0.3 mm to 1 mm thick coils. Thicker coils may require edge preparation.
Q: What is the typical accuracy achieved?
A: Advanced machines with servo control can achieve ±0.5 mm dimensional accuracy and ±1° angular accuracy.
Q: What is the power consumption of these machines?
A: Power consumption depends on size and ranges from 15 kW for a small 10 station machine up to 50 kW for a large 24 station machine.
Q: What are the regular maintenance activities required?
A: Maintenance involves cleaning, lubrication, inspection of rollers, drives, hydraulics, electrics as per schedule.
Q: What is the typical life span of these machines?
A: With proper maintenance and component replacement when required, lifespan can be 15-20 years.
Q: What factors affect the machine cost?
A: Speed, number of stations, automation level, and optional accessories impact the overall cost.
Q: How much area is required to install the machine?
A: Length is decided by number of stations. Typical area with clearance would be around 30m x 4m for a medium sized line.
Q: What consumables are required during operation?
A: Metal coils, lubricants, hydraulic oil, spare parts like rollers, chains, belts are required as consumables.
Conclusion
The downspout roll forming machine is an efficient equipment that enables high speed production of rainwater downspouts in different sizes and shapes. With the help of this guide, manufacturers can understand all key aspects of selection, installation, operation and maintenance of downspout roll forming machines in order to maximize productivity and product quality.