A iniş borusu rulo şekillendirme makinesi metal bobinlerden yağmur suyu drenaj iniş boruları ve olukları üretmek için kullanılan önemli bir ekipmandır. Bu kılavuz, iniş borusu rulo şekillendirme makinelerinin çalışması, türleri, uygulamaları, teknik özellikleri, seçim faktörleri, kurulumu, çalıştırılması, bakımı ve daha fazlasını kapsayan kapsamlı bir genel bakış sağlar.
İniş Borusu Rulo Şekillendirme Makinesine Genel Bakış
Bir iniş borusu rulo şekillendirme makinesi, metal bobinleri binalardaki yağmur suyu drenaj sistemleri için şekillendirilmiş profillere dönüştürmek üzere tasarlanmıştır.
İniş boruları nedir?
Yağmur suyu iniş boruları olarak da bilinen iniş boruları, yağmur suyu drenajını çatı oluklarından yere veya yağmur suyu sistemine toplamak ve yönlendirmek için kullanılan dikey kanallardır. Tipik olarak şekillendirilmiş metal levhalardan yapılırlar.
İniş borusu Rulo Şekillendirme Makinesinin Çalışması
Bir iniş borusu rulo şekillendirme makinesi, metal bobini girdi olarak alır ve ardışık şekillendirme istasyonlarından geçirerek şekillendirilmiş iniş borusu profillerine dönüştürür. Her istasyon, nihai profil elde edilene kadar silindirler kullanarak sacı aşamalı olarak şekillendirir. Şekillendirilen iniş borusu daha sonra gerektiği gibi uzunluklar halinde kesilir.
Gelişmiş iniş borusu rulo şekillendirme makineleri, hızlı kalıp değiştirme sistemleri sayesinde farklı profiller arasında hızlı geçiş sağlar.
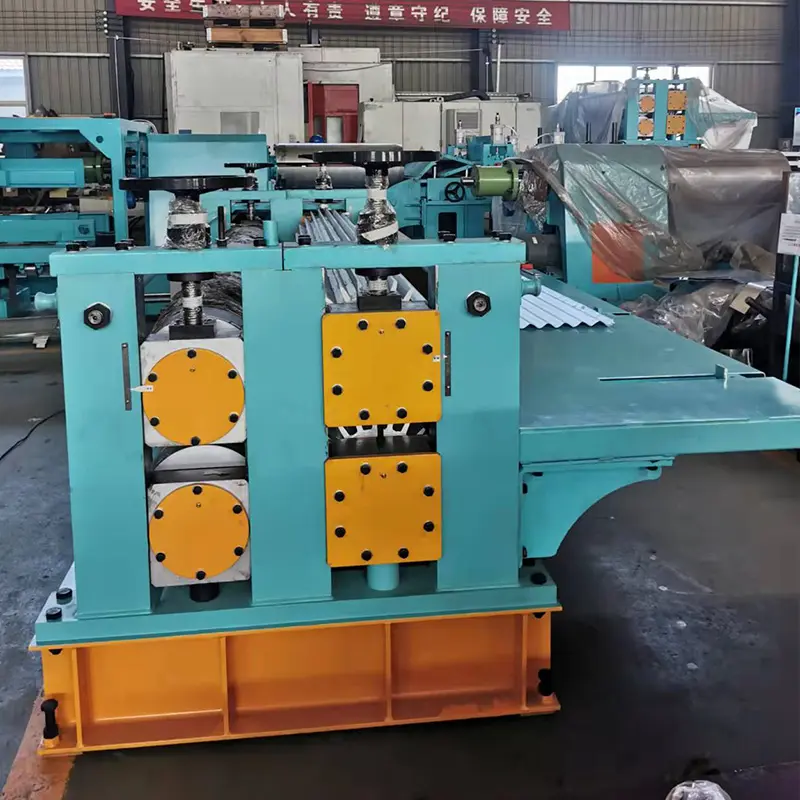
Türleri İniş Borusu Rulo Şekillendirme Makineleri
İniş borusu rulo şekillendirme makineleri, farklı üretim gereksinimlerine uyacak şekilde farklı konfigürasyonlarda mevcuttur:
Otomasyona Dayalı
- Manuel: Her istasyonda operatör müdahalesi gerektirir
- Yarı otomatik: Otomatik sac besleme ancak manuel profil değiştirme
- Tam otomatik: Otomatik besleme, profil oluşturma, kesme ve istifleme
Üretim Hızına Göre
- Düşük hız: 10 m/dak'ya kadar
- Orta hız: 10 - 40 m/dak
- Yüksek hız: 40 m/dak üzerinde
Daha yüksek hızlar üretim kapasitesini artırır.
Şekillendirme İstasyonlarına Göre
- Basit profiller için 10-12 istasyon
- Karmaşık çift katmanlı iniş boruları için 16-24 istasyon
- Daha fazla istasyon daha fazla profil şekline izin verir
Kontrol Sistemine Dayalı
- Kollar kullanılarak mekanik manuel kontrol
- Senkronizasyon için hidrolik otomatik kontrol
- Hassasiyet ve esneklik için PLC/CNC kontrollü servo motor
Rulo Şekillendirme ile Üretilen İniş Borularının Uygulamaları
Rulo şekillendirme makineleri kullanılarak üretilen iniş boruları:
- Konut, ticari ve endüstriyel binalar için drenaj sistemleri
- Büyük depolar, fabrikalar, uçak hangarları drenajı
- Stadyumlar, oditoryumlar, sergi salonları su drenajı
- Apartmanlar, villalar vb. için eğimli çatı drenajı.
- Barajlar, köprüler, yeraltı bölümleri etrafındaki drenaj
- Yağmur suyu hasadı ve yağmur suyunun yeniden yönlendirilmesi
- Barınaklar ve çadırlar gibi geçici yapılar
Rulo formlu iniş boruları, saha imalatına kıyasla daha hızlı ve ekonomik üretim sunar.
Downspout Rulo Şekillendirme Makinesi Özellikleri
İniş borusu rulo şekillendirme makineleri, üretim gereksinimlerine göre farklı özelliklerde mevcuttur:
Teknik Özellikler | Tipik Aralık |
---|---|
Şekillendirme Hızı | 10 - 80 m/dak |
Şekillendirme İstasyonları | 10 – 24 |
Metal Kalınlığı | 0,3 - 1 mm |
Maksimum Bobin Genişliği | 1000 - 1250 mm |
Min İniş Borusu Boyutu | 50 x 50 mm |
Maksimum İniş Borusu Boyutu | 300 x 300 mm |
Güç Tüketimi | 15 - 50 kW |
Kesme Modu | Otomatik/Yarı otomatik/Manuel |
Kontrol Sistemi | Mekanik, Hidrolik, Servo, PLC |
Makine Boyutu | 10 - 25 m Uzunluğunda x 2 - 3 m Genişliğinde |
Makine Ağırlığı | 6000 - 15000 kg |
Bu parametreler üretim ihtiyaçlarına göre özelleştirilebilir.
Tasarım ve Çalışma Standartları
İniş borusu rulo şekillendirme makinelerinin belirli tasarım standartlarına uyması gerekir:
- Yüksek hızlarda titreşimi en aza indirmek için yüksek gerilimli çelik çerçevelerin kullanılması
- İstasyonlar arasında hız değişimine izin vermek için ayrılmış tahrik tasarımı
- Daha az aşınma ve düzgün sac akışı için sertleştirilmiş makaralar ve kılavuzlar
- Tutarlı sac besleme için çok eksenli motorlu açıcılar
- Hassas profil şekillendirme için hassas dişliler ve dişli kutuları
- Eşit basınç uygulaması için hidrolik pres sistemi
- Acil durdurma, ışık perdeleri gibi güvenlik özellikleri
- Toz geçirmez elektrik kabini ve kontroller
Merdane takımı ve bükme sırası, çatlak veya incelme olmadan düzgün malzeme akışı için FEA analizi kullanılarak optimize edilmelidir.
Bir seçim İniş borusu Rulo Şekillendirme Makinesi Üretici firma
İşte iyi bir iniş borusu rulo şekillendirme makinesi üreticisi seçmek için bazı ipuçları:
Parametre | Nelere Dikkat Edilmeli |
---|---|
Deneyim | İşletmedeki yıl sayısı, uzun faaliyet geçmişi |
Üretim Tesisi | Kalite kontrollü şirket içi üretim |
Özelleştirme | Makineyi ihtiyaçlara göre özelleştirebilme |
Kalite | Tutarlı kalite için gelişmiş otomasyon |
Sertifikasyon | ISO 9001, CE sertifikaları |
Hizmet | Kurulum desteği, operatör eğitimi |
Maliyet | Rekabetçi fiyatlandırma ve ödeme koşulları |
Teslimat | Standart modellerin hazır envanteri |
Konum | Lojistik ve hizmet için mesafe |
- Makinelerden gelen örnek profillerin kalitesini kontrol edin
- Satın alma sonrasında teknik desteğin kullanılabilirliğini sağlamak
- Fiyatlandırma ve teslimat sürelerini karşılaştırın
- Üretim sürecini incelemek için mümkünse fabrikayı ziyaret edin
- Güvenilir ekipman için tanınmış bir üretici seçin
Bu, gereksinimlere uygun yüksek performanslı rulo şekillendirme makinelerinin elde edilmesine yardımcı olur.
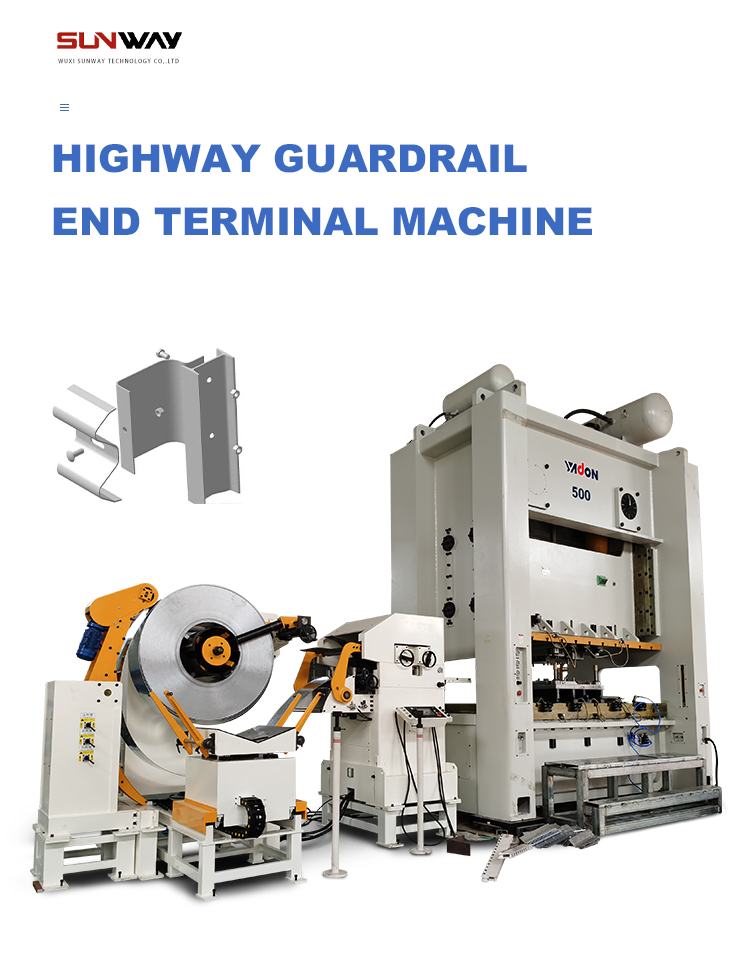
İniş Borusu Rulo Şekillendirme Makinesi Kurulumu
Doğru kurulum, iniş borusu rulo şekillendirme hattının sorunsuz çalışması için çok önemlidir:
- Beton temel hazırlama ve kaldırma ekipmanı kullanarak makineyi konumlandırma
- Gerektiği gibi şim ve harç kullanarak makine çerçevesini düzleştirin
- Rulo şekillendirme bölümlerini çizime göre monte edin
- Açıcı, düzleştirici ve birleştirme istasyonlarını hizalamaları kullanarak kurun
- İstasyonlar arasında şanzıman tahrik millerini bağlayın
- Elektrik anahtarlarını, sürücüleri ve kontrolleri bağlayın
- Koruyucuları dişlilerin, silindirlerin ve diğer hareketli parçaların etrafına takın
- Yağlama yağı sirkülasyonu ve varsa hidroliklerin çalışması
- Makineyi toprak çukurları aracılığıyla düzgün bir şekilde topraklayın
- Makineyi deneme çalıştırması yapın ve gerektiğinde ayarlamalar yapın
Üretici kılavuzuna göre doğru kurulum, güvenlik ve performans için önemlidir.
İniş Borusu Rulo Şekillendirme Makinesinin Çalışması ve İşleyişi
Bir iniş borusu rulo şekillendirme makinesinin çalıştırılması aşağıdaki adımları içerir:
Çalışma Öncesi Kontroller ve Ayarlar
- Elektrik kablolarını, hidroliği, yağlamayı kontrol edin
- Açıcıyı yeterli bobin ağırlığı gerginliği ile ayarlayın
- Malzeme kalınlığına bağlı olarak kesme presi ayarını yapın
- Her istasyondaki silindirleri uygun tabaka akışı için ayarlayın
- Durakları gerekli iniş borusu kesim uzunluğuna göre ayarlayın
- Çalışma sırasında eğrilmeyi önlemek için kılavuzları doğru şekilde ayarlayın
- Koşu yolu üzerindeki malzeme artıklarını veya yağ kalıntılarını temizleyin
Makinenin Çalıştırılması
- Makineyi jog modunda çalıştırın ve her bir istasyonu gözlemleyin
- Bobin açıcıyı açın ve tabakayı istasyonlardan besleyin
- Çalışma hızına ulaşmak için panelden hızı kademeli olarak artırın
- Açıcı gerginliğini, kesme presi ayarını gerektiği gibi ayarlayın
- Varsa otomatik kesme ve istiflemeyi başlatın
- Uygun profil oluşumunu sağladıktan sonra üretimi çalıştırın
Operasyon Sırasında
- Silindirlerin konturunu aşınmaya karşı izleyin ve periyodik olarak ayarlayın
- İstasyonlardaki anormal sesleri dinleyin, durun ve inceleyin
- Tüm hareketli parçaların uygun şekilde yağlandığından emin olun
- Profil boyutlarını mastarlar kullanarak periyodik olarak test edin
- Bobin değişiminden önce hattı durdurun ve artık sacı çıkarın
- Makine etrafındaki yağ döküntülerini veya metal hurdaları temizleyin
Kapatma
- Tüm malzemeyi temizlemek için hızı kademeli olarak sıfıra düşürün
- Açıcı, düzleştirici ve kesme istasyonlarına giden gücü kapatın
- Ana gücü kapatın ve elektriksel olarak kilitleyin
- Bir sonraki kullanım için alanı ve makineyi iyice temizleyin
Standart çalışma prosedürlerine uyulması kalite ve güvenlik açısından önemlidir.
Bakım İniş Borusu Rulo Şekillendirme Makineleri
Düzenli bakım faaliyetleri, iniş borusu rulo şekillendirme makinelerinin sorunsuz çalışmasını sağlar:
Etkinlik | Frekans | Yöntem |
---|---|---|
Temizlik | Günlük | Makine alanındaki hurdaları, yağ döküntülerini ve tozu temizleyin |
Teftiş | Günlük | Anormal gürültü, ısınma, sızıntı olup olmadığını kontrol edin |
Yağlama | Haftalık | Yatakları, dişlileri gresleyin, zincir yağı uygulayın |
Silindir Denetimi | Aylık | Konturu kontrol edin, aşınmış makaraları değiştirin |
Sürücü Denetimi | Aylık | Zincir/kayış gerginliğini kontrol edin, gerekirse ayarlayın/değiştirin |
Elektrik Malzemeleri | Üç Aylık | Gevşek bağlantıları, izolasyonları kontrol edin, gerekirse onarın |
Hidrolik | Üç Aylık | Silindirleri, pompaları, boruları sızıntılara karşı kontrol edin |
Şanzıman | Yıllık | Dişli yağını programa göre değiştirin |
- Temizlik, denetim, yağlama için günlük, haftalık ve aylık programların sürdürülmesi
- Tesis duruşları sırasında önleyici bakım planlayın
- Contalar, rulmanlar, makaralar gibi yeterli yedek parçayı stokta bulundurun
- Teknisyenleri ekipman bakım faaliyetleri konusunda eğitmek
- Sorunları ve iyileştirmeleri takip etmek için bakım kayıtlarını tutmak
Doğru bakım makinenin ömrünü uzatır ve beklenmedik arızaları önler.
İniş Borusu Rulo Şekillendirme Makinelerindeki Sorunların Giderilmesi
İniş borusu rulo şekillendirme makinelerinde karşılaşılan bazı yaygın sorunlar şunlardır:
Sorun | Olası Nedenler | Çözümler |
---|---|---|
Yaprak sıkışması | Silindirlerde aşınma ve boşluklar var Yanlış çözücü gerginliği Kılavuzlar yanlış hizalanmış | Aşınmış makaraları değiştirin Açıcı gerginliğini ayarlayın Kılavuzları yeniden hizalayın |
Profil bozulması | Silindir boşlukları düzensiz Malzeme beslemesi düz değil İstasyon seviyeleri dengesiz | Silindir aralıklarını eşit olarak ayarlayın Malzeme besleme hizalamasını ayarlayın Yeniden seviye belirleme istasyonları |
Aşırı gürültü | Gevşek bağlantı elemanları Rulman aşınması Zincir dişlisi aşınmış | Gevşek somunları, cıvataları sıkın Aşınmış rulmanları değiştirin Aşınmış dişlileri değiştirin |
Hidrolik yağ sızıntısı | Hortum hasarı Conta aşınmış | Hasarlı hortumları değiştirin Aşınmış contaları değiştirin |
Makine titreşimi | İstasyon yanlış hizalanmış Temel cıvataları gevşek | İstasyonları yeniden düzenleyin Temel cıvatalarını sıkın |
Kök nedenin analiz edilmesi ve eksikliklerin giderilmesi, yaygın rulo şekillendirme makinesi sorunlarını çözebilir.
İniş Borusu Rulo Şekillendirme Makinelerinin Verimliliğinin Artırılması
İniş borusu rulo şekillendirme makinelerinin verimliliğini artırmanın bazı yolları şunlardır:
- Darboğazları azaltarak hat hızını optimize edin
- Üretim çalışmalarını en üst düzeye çıkarmak için hızlı kalıp değişimlerini planlayın
- Kesme ve istifleme gibi aşağı akış süreçlerini otomatikleştirin
- Girdi hammaddesinin tutarlı kalitesinin sağlanması
- Operatörleri standart işletim prosedürleri konusunda eğitin
- Genel ekipman verimliliğini takip edin ve iyileştirmeleri hedefleyin
- Önleyici bakım sayesinde planlanmamış arıza sürelerini azaltın
- Silindirler gibi aşınan yedek parçalar için yeterli envanter bulundurun
- Zaman içinde servo kontrol, IoT verileri gibi özelliklerle makineyi yükseltin
Doğru girişimlerle, iniş borusu rulo şekillendirme hatlarından önemli verimlilik artışları elde edilebilir.
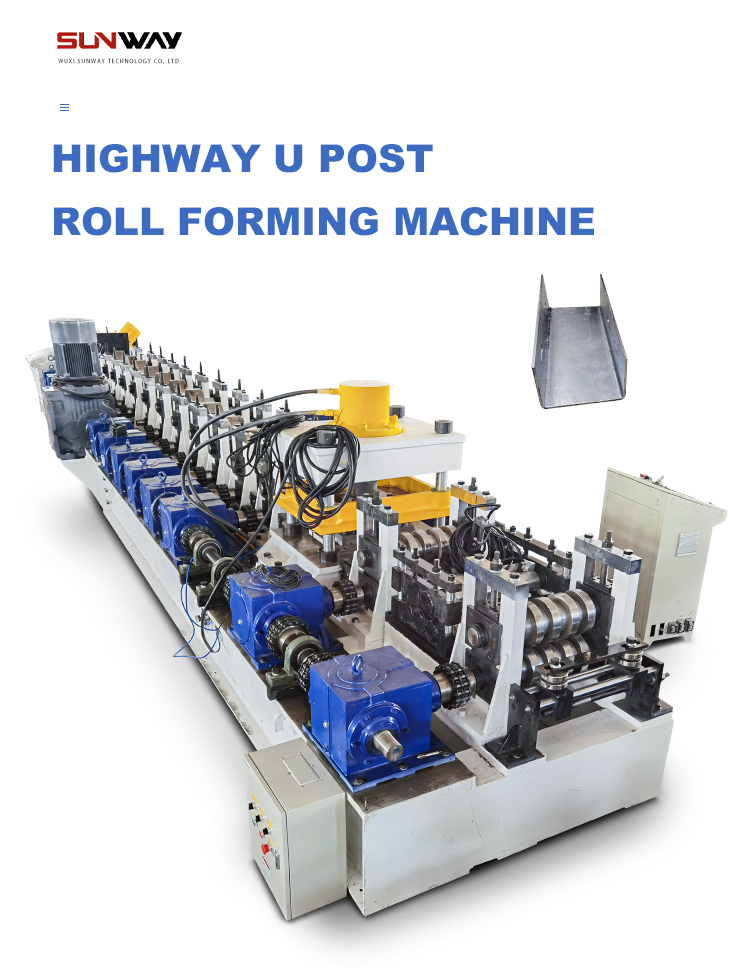
SSS
S: İniş borusu rulo şekillendirme makinelerinin tipik üretim kapasitesi nedir?
C: Üretim kapasitesi makine hızına ve profillere bağlıdır - tipik olarak 30-50 metre/dakika, yaklaşık 500-800 metre/saat çıktı ile sonuçlanır.
S: Hangi kalınlıkta bobinler kullanılabilir?
C: Makineler tipik olarak 0,3 mm ila 1 mm kalınlığındaki bobinleri işleyebilir. Daha kalın bobinler kenar hazırlığı gerektirebilir.
S: Elde edilen tipik doğruluk oranı nedir?
C: Servo kontrollü gelişmiş makineler ±0,5 mm boyutsal doğruluk ve ±1° açısal doğruluk elde edebilir.
S: Bu makinelerin güç tüketimi nedir?
C: Güç tüketimi boyuta bağlıdır ve 10 istasyonlu küçük bir makine için 15 kW'tan 24 istasyonlu büyük bir makine için 50 kW'a kadar değişir.
S: Gerekli düzenli bakım faaliyetleri nelerdir?
C: Bakım, temizlik, yağlama, silindirlerin, tahriklerin, hidroliklerin, elektriklerin programa göre incelenmesini içerir.
S: Bu makinelerin tipik kullanım ömrü ne kadardır?
C: Uygun bakım ve gerektiğinde bileşen değişimi ile kullanım ömrü 15-20 yıl olabilir.
S: Makine maliyetini etkileyen faktörler nelerdir?
C: Hız, istasyon sayısı, otomasyon seviyesi ve isteğe bağlı aksesuarlar toplam maliyeti etkiler.
S: Makineyi kurmak için ne kadar alan gerekiyor?
C: Uzunluğa istasyon sayısına göre karar verilir. Orta büyüklükte bir hat için açıklığı olan tipik alan yaklaşık 30m x 4m olacaktır.
S: Çalışma sırasında hangi sarf malzemeleri gereklidir?
C: Metal bobinler, yağlayıcılar, hidrolik yağ, makaralar, zincirler, kayışlar gibi yedek parçalar sarf malzemesi olarak gereklidir.
Sonuç
İniş borusu rulo şekillendirme makinesi, farklı boyut ve şekillerde yağmur suyu iniş borularının yüksek hızda üretilmesini sağlayan verimli bir ekipmandır. Bu kılavuzun yardımıyla üreticiler, üretkenliği ve ürün kalitesini en üst düzeye çıkarmak için iniş borusu rulo şekillendirme makinelerinin seçimi, kurulumu, çalıştırılması ve bakımı ile ilgili tüm önemli hususları anlayabilirler.