Overview of CZ Purlin Machine
The CZ purlin machine, also known as the C/Z purlin roll forming machine, is a specialized equipment used in the construction industry to manufacture purlins – the horizontal structural elements that support the roofing system of a building. These machines have gained immense popularity due to their ability to produce high-quality purlins efficiently and cost-effectively.
Purlins are typically made from galvanized steel or other metal alloys and are designed to transfer the load from the roof to the main structural components of the building, such as trusses or rafters. The CZ purlin machine takes flat metal coils as input and roll-forms them into the desired purlin profile through a series of precision-controlled roller stations.
This highly automated process not only ensures consistent quality and dimensional accuracy but also significantly reduces material waste and labor costs compared to traditional fabrication methods. The CZ purlin machine is a vital component in the construction industry, enabling faster and more economical construction of commercial, industrial, and residential buildings.
Comprehensive Guide to CZ Purlin Machines
Purlins are an integral part of the structural framework in modern construction, and the demand for efficient and cost-effective purlin manufacturing has led to the development of CZ purlin machines. These machines are designed to produce high-quality purlins from flat metal coils through a continuous roll-forming process.
The CZ purlin machine typically consists of the following main components:
- Decoiler: This component holds and feeds the flat metal coil into the machine.
- Roll-forming stations: A series of precisely calibrated roller stations that gradually bend and shape the flat metal into the desired purlin profile.
- Cut-off station: This station cuts the continuously formed purlin into desired lengths.
- Stacking or collection system: The finished purlins are neatly stacked or collected at the end of the line.
The roll-forming process in a CZ purlin machine is highly automated and controlled by computer numerical control (CNC) systems, ensuring consistent quality and precise dimensions. The machines can be configured to produce various purlin profiles, such as C-sections, Z-sections, or sigma (Σ) shapes, depending on the specific requirements of the construction project.
One of the key advantages of CZ purlin machines is their ability to produce purlins with minimal material waste. The continuous roll-forming process maximizes the utilization of the metal coil, reducing the amount of scrap generated compared to traditional fabrication methods.
Additionally, these machines are designed for high-speed production, enabling construction companies to meet tight project deadlines and reduce labor costs. The automated nature of the process also enhances worker safety by minimizing manual handling and exposure to potential hazards.
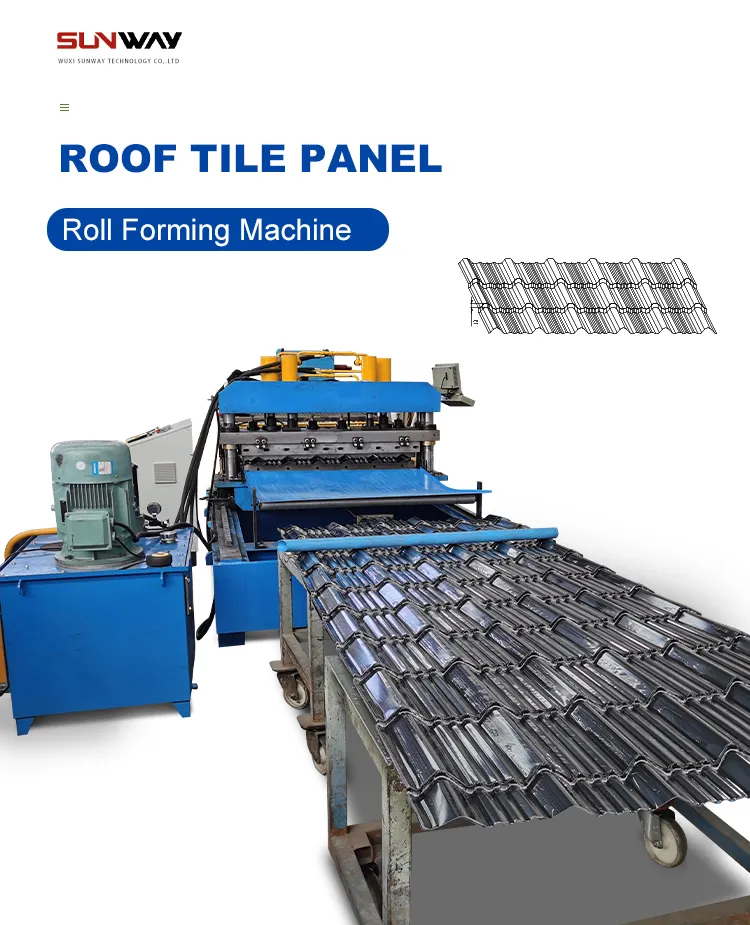
Types of CZ Purlin Machines
CZ purlin machines come in various configurations and capabilities, catering to the diverse needs of the construction industry. Here are some common types of CZ purlin machines:
Machine Type | Description |
---|---|
Standard CZ Purlin Machine | This type of machine is designed to produce standard C and Z purlin profiles in common dimensions used in most construction projects. |
Heavy-Duty CZ Purlin Machine | Designed for manufacturing larger and heavier purlin profiles used in industrial or commercial buildings with increased load-bearing requirements. These machines can handle thicker and stronger metal materials. |
Multi-Profile CZ Purlin Machine | These versatile machines can be configured to produce a variety of purlin profiles, including C, Z, sigma (Σ), and other custom shapes, offering flexibility for different project requirements. |
Portable CZ Purlin Machine | Compact and mobile machines that can be easily transported to construction sites for on-site purlin production, reducing transportation costs and ensuring timely delivery. |
Fully Automated CZ Purlin Machine | These advanced machines are equipped with automated material handling systems, such as robotic loaders and unloaders, minimizing human intervention and maximizing production efficiency. |
The choice of CZ purlin machine type depends on factors such as the project scale, purlin specifications, production volume requirements, and budget considerations.
Working Process of a CZ Purlin Machine
The CZ purlin machine operates through a continuous roll-forming process, where flat metal coils are gradually shaped into the desired purlin profile. Here’s a step-by-step overview of the working process:
- Material Feeding: The flat metal coil, typically made of galvanized steel or aluminum, is loaded onto the decoiler at the beginning of the machine line.
- Roll-Forming Stations: As the metal coil is fed into the machine, it passes through a series of precisely calibrated roller stations. Each roller station progressively bends and shapes the flat metal into the desired purlin profile through a combination of rolling and pressing operations.
- Profile Shaping: The roll-forming stations are designed to gradually form the metal into the required C, Z, or sigma (Σ) purlin profile. The number of roller stations and their configurations vary depending on the complexity of the desired profile.
- Punching and Notching: Depending on the specific requirements, the machine can be equipped with punching and notching stations to create holes, slots, or notches in the purlin for easy installation or integration with other building components.
- Cut-off Station: Once the desired purlin length is achieved, the continuously formed purlin is cut to the specified length at the cut-off station, typically using a flying shear or a hydraulic shear.
- Stacking or Collection: The finished purlins are then neatly stacked or collected at the end of the machine line, ready for transportation to the construction site or further processing, if required.
Throughout the process, the CZ purlin machine is controlled by a computerized system, ensuring precise dimensions, consistent quality, and efficient production. The roll-forming process minimizes material waste and enables the production of purlins with tight tolerances, meeting the stringent requirements of the construction industry.
Material Feeding in CZ Purlin Machines
Material Feeding Components | Description |
---|---|
Decoiler | A large spool or reel that holds and feeds the flat metal coil into the machine. It is designed to smoothly and consistently unwind the coil without causing deformations or damage to the material. |
Straightener | As the metal coil is unwound, it may have slight bends or deformations. The straightener uses a series of rollers to straighten and flatten the metal before it enters the roll-forming stations. |
Lubrication System | Some CZ purlin machines are equipped with an automatic lubrication system that applies a thin layer of lubricant to the metal strip, reducing friction and wear on the rollers during the roll-forming process. |
Coil Handling Systems | Larger machines may include coil handling systems, such as coil cars or cranes, to facilitate the loading and unloading of heavy metal coils onto the decoiler. |
Proper material feeding is crucial for the smooth operation of the CZ purlin machine and ensuring consistent quality of the final product. Manufacturers often offer various coil handling options and material feeding configurations to accommodate different coil sizes, materials, and production requirements.
omizable roll-forming station configurations to accommodate various purlin profiles and specifications.
-
Highway Guardrail End Terminal Forming Machine
-
Highway U/C Post Roll Forming Machine
-
2 Waves Highway Guardrail Roll Forming Machine
-
3 Waves Highway Guardrail Roll Forming Machine
-
Auto Size Changeable Sigma Purlin Roll Forming Machine
-
Auto Size Changeable C Z Purlin Roll Forming Machine
-
Auto Size Changeable Z Purlin Roll Forming Machine
-
Auto Size Changeable C U Purlin Roll Forming Machine
-
Electrical Cabinet Frame Roll Forming Machine
Design and Customization of CZ Purlin Machines
Design and Customization Options | Description |
---|---|
Purlin Profile Options | CZ purlin machines can be designed to produce a variety of purlin profiles, including C-sections, Z-sections, sigma (Σ) shapes, and custom profiles tailored to specific project requirements. |
Material Compatibility | Machines can be configured to handle different metal materials, such as galvanized steel, aluminum, or stainless steel, depending on the application and environmental conditions. |
Line Speed and Production Capacity | Manufacturers offer machines with varying line speeds and production capacities to meet diverse project demands, from small-scale residential construction to large commercial or industrial projects. |
Automation and Control Systems | Advanced CZ purlin machines can be equipped with fully automated material handling systems, robotic loaders and unloaders, and sophisticated control systems for enhanced efficiency and production monitoring. |
Integration with Other Systems | Some machines can be integrated with downstream processes, such as coating or painting systems, for a seamless manufacturing workflow. |
Customized Roll-Forming Stations | Roll-forming stations can be customized to accommodate specific purlin profiles, enabling manufacturers to produce unique or proprietary purlin designs. |
The ability to customize and tailor CZ purlin machines to specific project requirements is a significant advantage, ensuring that construction companies can produce purlins that meet the exact specifications and standards required.
Slicing and Cut-Off in CZ Purlin Machines
Slicing and Cut-Off Components | Description |
---|---|
Cut-Off Station | This station is responsible for cutting the continuously formed purlin into desired lengths. Commonly used cutting mechanisms include flying shears, hydraulic shears, or saw blades. |
Length Control System | Precise length control systems, often computer-controlled, ensure that the purlins are cut to the exact specified lengths, minimizing material waste and ensuring dimensional accuracy. |
Scrap Removal System | After the purlins are cut, the scrap material is removed from the line using conveyors, suction systems, or other waste handling mechanisms. |
End Treatment Stations | Some machines include end treatment stations where the cut ends of the purlins can be deburred, flattened, or treated to enhance their appearance and prevent sharp edges. |
The slicing and cut-off process is a critical step in the CZ purlin machine operation, as it determines the final length and quality of the purlins. Manufacturers offer various cutting mechanisms and length control systems to accommodate different purlin dimensions and production requirements.
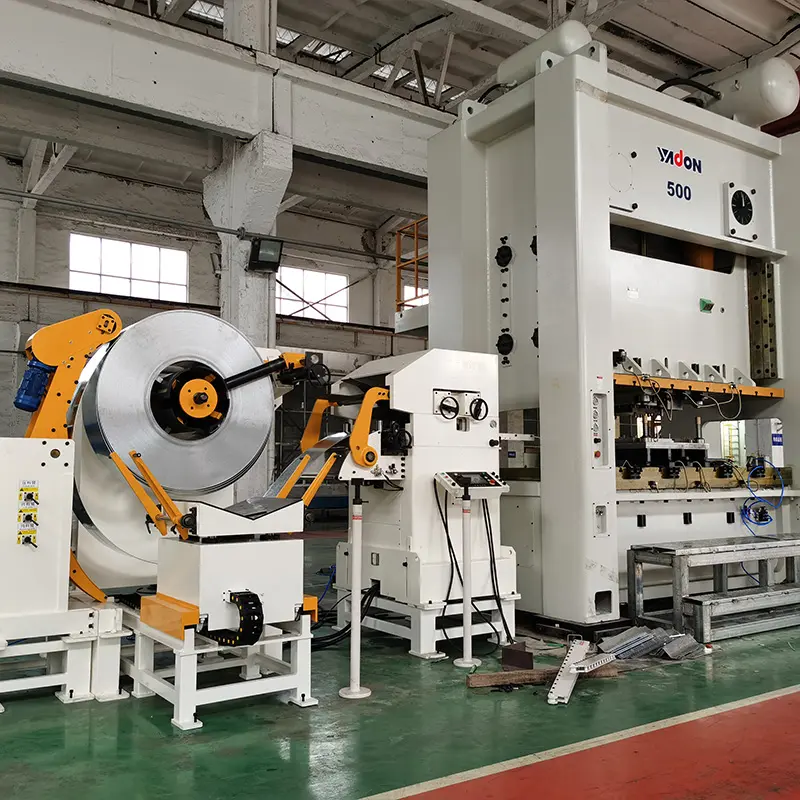
Choosing the Right CZ Purlin Machine Supplier
When selecting a CZ purlin machine supplier, it’s essential to consider several factors to ensure you make an informed decision that meets your specific needs and requirements.
Factors to Consider | Description |
---|---|
Reputation and Experience | Look for suppliers with a proven track record in manufacturing high-quality CZ purlin machines. Established companies with extensive experience in the industry are more likely to provide reliable and durable equipment. |
Product Range and Customization | Evaluate the supplier’s product range to ensure they offer the specific machine configurations and customization options you require. This includes the ability to produce various purlin profiles, handle different materials, and accommodate your production capacity needs. |
Technical Support and Service | Choose a supplier that provides comprehensive technical support, training, and after-sales service. This includes access to spare parts, maintenance services, and expert assistance when needed. |
Automation and Technology | Consider suppliers that offer advanced automation and control systems, as well as the ability to integrate with other systems or processes in your manufacturing workflow. This can improve efficiency, productivity, and overall quality. |
Location and Logistics | The supplier’s location and logistics capabilities can impact delivery times, installation, and ongoing support. Evaluate their ability to provide timely delivery and efficient installation services, particularly if you require on-site setup or training. |
Pricing and Payment Terms | While cost should not be the sole deciding factor, it’s essential to consider the overall value proposition and negotiate favorable pricing and payment terms that align with your budget and financial requirements. |
Industry Certifications and Compliance | Ensure that the supplier’s machines meet relevant industry standards, certifications, and compliance regulations, particularly regarding safety and environmental regulations in your region. |
By carefully evaluating these factors, you can select a CZ purlin machine supplier that not only provides high-quality equipment but also offers reliable support, customization options, and a long-term partnership for your business’s success.
Pros and Cons of CZ Purlin Machines
Like any industrial equipment, CZ purlin machines have their advantages and limitations. Understanding these pros and cons can help you make an informed decision and plan accordingly.
Pros | Cons |
---|---|
Efficient Production | High Initial Investment |
Consistent Quality | Requires Skilled Operators |
Reduced Material Waste | Limited Flexibility for Complex Shapes |
Increased Worker Safety | Maintenance and Downtime |
Cost-Effective in the Long Run | Potential for Noise and Environmental Impact |
Versatility in Purlin Profiles | Space Requirements |
Automated and Precise | Dependence on Reliable Material Supply |
Advantages of CZ Purlin Machines
- Efficient Production: CZ purlin machines are designed for high-speed, continuous production, enabling construction companies to meet tight project deadlines and reduce labor costs.
- Consistent Quality: The automated roll-forming process and precise control systems ensure consistent quality and dimensional accuracy of the purlins, meeting stringent construction standards.
- Reduced Material Waste: The continuous roll-forming process maximizes the utilization of the metal coil, minimizing material waste compared to traditional fabrication methods.
- Increased Worker Safety: By automating the purlin manufacturing process, CZ purlin machines reduce the need for manual handling and exposure to potential hazards, enhancing worker safety.
- Cost-Effective in the Long Run: While the initial investment in a CZ purlin machine can be substantial, the efficiency and material savings can lead to significant cost savings over time, especially for large-scale construction projects.
- Versatility in Purlin Profiles: Many CZ purlin machines can be configured to produce a variety of purlin profiles, including C-sections, Z-sections, sigma (Σ) shapes, and custom designs, offering flexibility to meet diverse project requirements.
Limitations of CZ Purlin Machines
- High Initial Investment: Purchasing and installing a CZ purlin machine can be a significant capital investment, which may not be feasible for smaller construction companies or projects with limited budgets.
- Requires Skilled Operators: While highly automated, CZ purlin machines still require skilled operators for setup, monitoring, and maintenance, which can add to operational costs and training requirements.
- Limited Flexibility for Complex Shapes: While CZ purlin machines can produce a variety of standard purlin profiles, they may have limitations in forming highly complex or intricate shapes, which may require additional fabrication processes.
- Maintenance and Downtime: Like any industrial machinery, CZ purlin machines require regular maintenance and may experience downtime for repairs or adjustments, impacting production schedules and efficiency.
- Potential for Noise and Environmental Impact: The roll-forming process and associated machinery can generate noise and potential environmental impacts, such as emissions or waste products, which may require additional measures for compliance with regulations.
- Space Requirements: CZ purlin machines can be large and require substantial floor space, which may be a consideration for construction companies with limited facility space.
- Dependence on Reliable Material Supply: The continuous operation of CZ purlin machines relies on a consistent supply of high-quality metal coils, which may be subject to fluctuations in availability or pricing.
While these limitations should be considered, many construction companies find that the advantages of CZ purlin machines outweigh the potential drawbacks, particularly for large-scale projects or high-volume purlin production requirements.
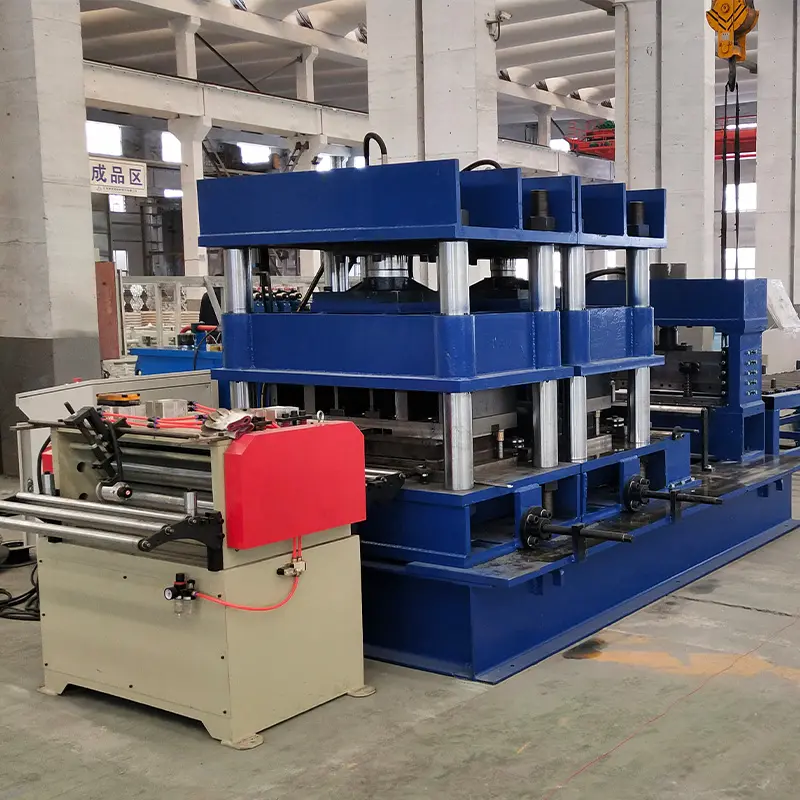
Installation and Operation of CZ Purlin Machines
Proper installation and operation of CZ purlin machines are crucial for achieving optimal performance, efficiency, and safety. Here are some key considerations:
Installation Aspects | Description |
---|---|
Site Preparation | Ensure the installation site has adequate space, a level floor, and sufficient power supply and utilities. |
Foundations and Anchoring | Properly anchor the machine to a solid foundation to minimize vibrations and ensure stability during operation. |
Electrical and Control Systems | Ensure correct wiring and integration of the electrical and control systems, following manufacturer guidelines and local regulations. |
Material Handling Systems | Install and configure material handling systems, such as coil loaders and unloaders, for efficient material flow. |
Safety Guarding and Enclosures | Install appropriate safety guarding and enclosures to protect operators from potential hazards, such as pinch points and moving parts. |
Ventilation and Noise Control | Implement adequate ventilation and noise control measures to maintain a safe and comfortable working environment. |
Operational Aspects | Description |
---|---|
Operator Training | Provide comprehensive training to operators on machine setup, operation, maintenance, and safety procedures. |
Material Selection | Ensure the correct metal coil material, dimensions, and quality are used for the desired purlin profile and application. |
Machine Setup and Calibration | Properly set up and calibrate the machine for the specific purlin profile, dimensions, and production requirements. |
Process Monitoring | Continuously monitor the roll-forming process, ensuring consistent quality and addressing any issues or deviations promptly. |
Maintenance and Servicing | Follow recommended maintenance schedules and servicing procedures to ensure optimal machine performance and longevity. |
Safety Protocols | Strictly adhere to established safety protocols, including lockout/tagout procedures, personal protective equipment (PPE), and emergency response plans. |
By following best practices for installation and operation, construction companies can maximize the productivity, efficiency, and safety of their CZ purlin machines, ensuring high-quality purlin production and minimizing downtime and operational disruptions.
Maintenance and Troubleshooting for CZ Purlin Machines
Regular maintenance and prompt troubleshooting are essential for ensuring the smooth operation and longevity of CZ purlin machines. Here are some key considerations:
Maintenance Aspects | Description |
---|---|
Preventive Maintenance | Follow the manufacturer’s recommended maintenance schedules for tasks such as lubricating moving parts, inspecting rollers and bearings, and checking electrical components. |
Roller and Tooling Replacement | Replace worn or damaged rollers, tooling, and other components as needed to maintain dimensional accuracy and product quality. |
Calibration and Adjustments | Regularly calibrate and adjust the machine settings to ensure consistent purlin dimensions and profiles. |
Cleaning and Housekeeping | Maintain cleanliness around the machine, removing debris and metal shavings to prevent contamination and potential machine damage. |
Spare Parts Inventory | Maintain an adequate inventory of commonly required spare parts to minimize downtime for repairs and replacements. |
Troubleshooting Aspects | Description |
---|---|
Operator Training | Ensure operators are trained to identify and address common issues, such as material feeding problems, profile deformations, or machine stoppages. |
Diagnostic Tools | Utilize diagnostic tools and equipment, such as vibration analyzers or thermal imaging cameras, to identify potential issues before they escalate. |
Technical Support | Have access to reliable technical support from the machine manufacturer or experienced service providers for more complex issues. |
Root Cause Analysis | Conduct thorough root cause analysis to identify and address underlying issues, rather than just treating symptoms. |
Documentation and Recordkeeping | Maintain detailed documentation and records of maintenance activities, troubleshooting efforts, and machine performance to identify trends and improve processes. |
By implementing a comprehensive maintenance and troubleshooting program, construction companies can maximize the uptime, performance, and lifespan of their CZ purlin machines, ensuring consistent and efficient purlin production while minimizing costly downtime and repairs.
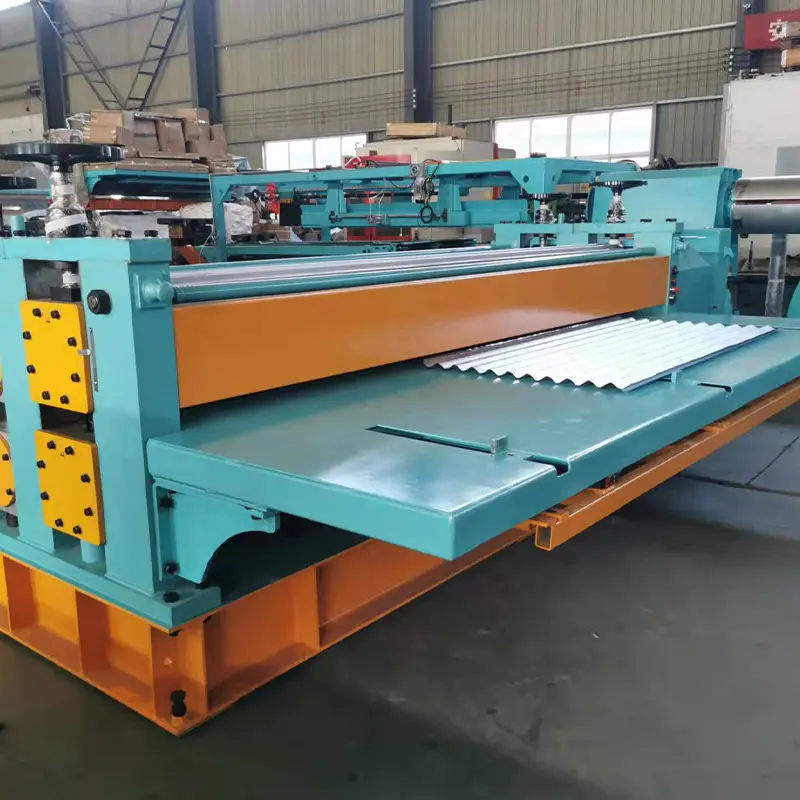
Choosing the Right CZ Purlin Machine
Selecting the appropriate CZ purlin machine is crucial for meeting your specific production requirements and ensuring a successful investment. Here are some key factors to consider:
Factor | Description |
---|---|
Production Volume | Determine your expected production volume and choose a machine with adequate capacity and throughput to meet your needs. |
Purlin Profiles and Dimensions | Ensure the machine can produce the desired purlin profiles and dimensions required for your projects, considering both standard and custom shapes. |
Material Compatibility | Verify that the machine is compatible with the metal materials you plan to use, such as galvanized steel, aluminum, or stainless steel. |
Automation and Control Systems | Consider the level of automation and control systems you require, from basic manual operation to fully automated and integrated systems. |
Footprint and Layout | Evaluate the available floor space and layout of your production facility to ensure the machine can be properly installed and integrated. |
Customization and Flexibility | Assess your need for customization options, such as adjustable roll-forming stations or the ability to produce a variety of purlin profiles. |
Integration with Existing Systems | If applicable, consider how the CZ purlin machine will integrate with your existing manufacturing processes or downstream operations. |
Maintenance and Support | Evaluate the manufacturer’s reputation for technical support, spare parts availability, and maintenance services to ensure long-term reliable operation. |
Budget and Return on Investment | Carefully consider the initial investment cost, operational expenses, and potential return on investment (ROI) based on your production requirements and projected savings. |
By thoroughly evaluating these factors and consulting with experienced suppliers or industry experts, you can make an informed decision and select a CZ purlin machine that meets your specific needs, optimizes your production processes, and provides a solid return on investment.
FAQs
Question | Answer |
---|---|
What is a CZ purlin machine? | A CZ purlin machine is a specialized equipment used in the construction industry to manufacture purlins, which are horizontal structural elements that support the roofing system of a building. These machines continuously roll-form flat metal coils into the desired purlin profile through a series of precision-controlled roller stations. |
What types of purlin profiles can CZ purlin machines produce? | CZ purlin machines can produce a variety of purlin profiles, including C-sections, Z-sections, sigma (Σ) shapes, and custom profiles tailored to specific project requirements. |
What materials are commonly used in CZ purlin machines? | Galvanized steel and aluminum are the most common materials used in CZ purlin machines, but some machines can also handle stainless steel or other metal alloys. |
How does a CZ purlin machine reduce material waste? | The continuous roll-forming process in CZ purlin machines maximizes the utilization of the metal coil, significantly reducing material waste compared to traditional fabrication methods. |
What are the advantages of using a CZ purlin machine? | Key advantages include efficient production, consistent quality, reduced material waste, increased worker safety, cost-effectiveness in the long run, and versatility in producing various purlin profiles. |
What factors should be considered when choosing a CZ purlin machine? | Important factors include production volume, purlin profiles and dimensions, material compatibility, automation and control systems, footprint and layout, customization and flexibility, integration with existing systems, maintenance and support, and budget and return on investment. |
How can I ensure the proper installation and operation of a CZ purlin machine? | Proper site preparation, foundations and anchoring, electrical and control systems integration, material handling systems, safety guarding and enclosures, and ventilation and noise control are crucial for installation. Operator training, material selection, machine setup and calibration, process monitoring, maintenance and servicing, and adherence to safety protocols are essential for operation. |
What maintenance and troubleshooting procedures are recommended for CZ purlin machines? | Regular preventive maintenance, roller and tooling replacement, calibration and adjustments, cleaning and housekeeping, and maintaining a spare parts inventory are recommended. Operator training, diagnostic tools, technical support, root cause analysis, and documentation and recordkeeping are essential for effective troubleshooting. |