China light keel roll forming machines are used to produce cold-formed steel light keel profiles from metal coils. Light keels provide an economical roof truss framing system for warehouses, factories, workshops and agricultural buildings.
This guide provides details on light keel specifications, types of China light keel roll forming machines, components, working principles, design considerations, applications, advantages, limitations and more focusing on Chinese manufacturers.
Overview of China light keel roll forming machine
Light keel roll forming involves:
- Progressively bending metal coil strips into light keel channel shapes
- Feeding coils through a series of roller dies
- Forming the web, flange and lip profiles
- Shearing keels to length
- Stacked assembly of finished keels for supply
Common materials include galvanized steel, pre-painted steel and aluminum strips. Light keels provide cost-effective substitutes to hot-rolled steel sections for roof structures.
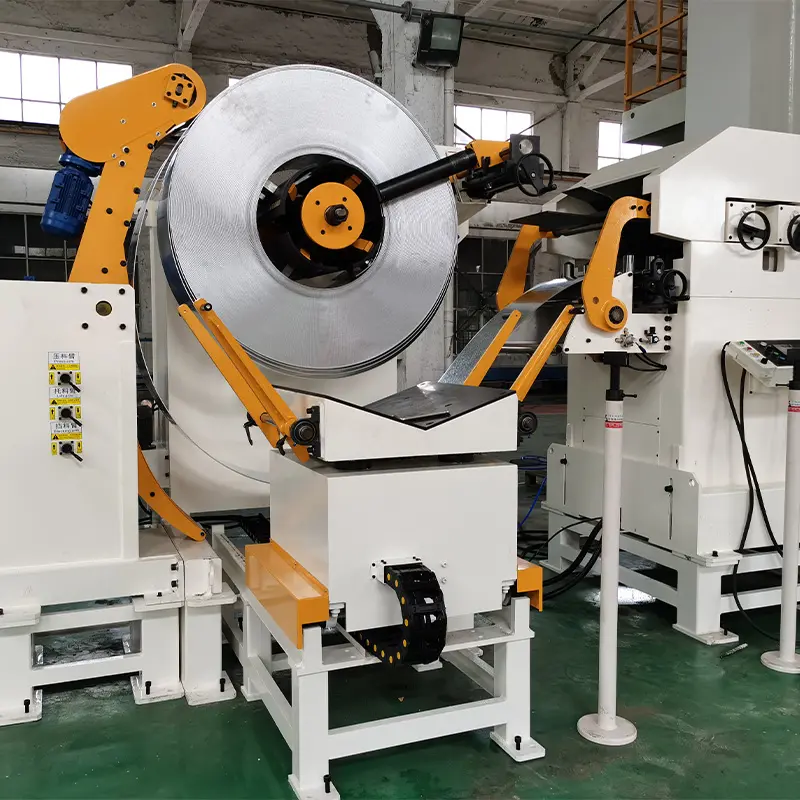
Types of Light Keel Roll Forming Machines
There are two main types of keel roll forming machines:
1. C-Structure Roll Formers
- Form entire keel profile in one forming section
- Simpler design using top and bottom rollers
- Limited to smaller keel sizes
- Production speeds around 10-20 m/min
2. Step Roll Formers
- Keel flanges formed sequentially in separate stands
- Capable of rolling bigger keel sizes
- Run at higher speeds of 40-50 m/min
- Provide better control of flange parameters
Comparison of Light Keel Roll Former Types
Parameter | C-Structure | Step Roll |
---|---|---|
Forming method | Entire profile at one station | Sequential flange forming |
Profile size | Smaller keels <200 mm | Wider keels >250 mm |
Production speed | Slower < 20 m/min | Faster > 40 m/min |
Roll design | Simpler | Complex |
Line length | Shorter | Longer |
Components of Light Keel Rolling Lines
Light keel rolling lines consist of various equipment modules:
Coil Handling
- Decoiler to feed metal coils into process
- Recoiler for taking up processed strips
- Coil cars and loading systems
Sheet Feeding
- Feed tables with rollers
- Sheet guides and sensors
- Edge thickness controllers
Roll Forming Stations
- Progressive die stations for bending
- Forming rollers and support tooling
- Hydraulic press systems
- Servo motor driven rolling
Shearing Unit
- Rotating blades for cutting keels to length
- Length measuring systems
- Scrap choppers and conveyors
Stacker
- Automatic bundling and stacking
- Strapping systems
Control Systems
- PLC controls and HMIs
- Parameter monitoring sensors
- Speed synchronization
- Safety interlock systems
Working Principle of Light Keel Rolling
Light keel roll forming involves:
- Sheet strips unwinding from coils into the feed section
- Feeding the strips through progressive roller dies
- Gradually bending the strips to form web, flanges and lip
- Cutting the formed keels to specified lengths
- Stacked assembly of finished keels
- PLC-based control systems synchronize the equipment stages. The modular arrangement provides flexibility to produce various keel sizes by changing roll sets.
Design Considerations for Light Keel Rolling Lines
The key design factors for light keel roll forming lines include:
- Product dimensions – Keel depth, flange width, metal thickness
- Production speed – Feet or meters produced per minute
- Performance features – speed, precision, flexibility
- Automation – Controls, sensors, safety systems
- Roll tooling – Quick changeover, precision and wear life
- Line layout – Material handling, operational ergonomics
- Expandability – Ability to increase future capacity
- Site conditions – Install within available space constraints
- Standards compliance – Applicable structural standards
Matching production targets with keel sizes determines component sizing, layout and overall line design.
Applications of Light Keel Rolling Lines
The major applications of rolled light keel sections include:
- Roof truss systems for factories, workshops
- Framing for agricultural, storage buildings
- Trusses for canopies, walkway covers
- Rafters for purlin roofing systems
- Secondary structural members
- Building mezzanines and flooring
Light keels provide cost-effective substitutes to hot-rolled steel sections for light to medium load non-residential structures while enabling faster construction.
Benefits of Using Light Keel Roll Forming
Key benefits of the light keel roll forming process:
- Highly productive continuous forming
- Consistent dimensional accuracy
- Scalable production by adding roll stands
- Flexibility to change profiles with quick roll changes
- Lower costs than hot-rolled steel sections
- In-house production improves lead times
- Lighter keel sections reduce transportation costs
- Suitable for long spans upto 15 meters
- Allow customized keel profiles and sizes
- Less skilled labor required compared to site welding
Automated roll forming provides a cost and time efficient method for mass producing light steel keels.
Limitations of Light Keel Roll Forming
Some limitations of the light keel roll forming process:
- High initial equipment capital cost
- Substantial space requirements
- Limited to straight profiles only
- Increased structural analysis needed
- Lower stiffness than hot-rolled sections
- Requires experienced technical operators
- Additional connection design considerations
- Can be prone to web buckling issues
- Noise emission requiring mitigation measures
The process may not be feasible for low volume production or applications needing heavy sections.
Key Chinese Manufacturers of Light Keel Rolling Equipment
Some leading China-based suppliers of light keel roll forming lines include:
Major China Light Keel Roll Former Manufacturers
Company | Location |
---|---|
Legend | Jiangsu |
Union Machinery | Wuxi |
Spirol | Shanghai |
JinDeRan | Tianjin |
Frontwave | Guangdong |
These companies offer standard and customized light keel rolling line solutions for capacities from 10 to 100 meters per minute. Complete lines include decoilers, roll stands, cutting and stacking systems.
Equipment Cost Range
Production Speed | Indicative Pricing |
---|---|
10 m/min | $50,000 – $100,000 |
25 m/min | $100,000 – $250,000 |
50 m/min | $200,000 – $500,000 |
75+ m/min | Over $500,000 |
Pricing varies based on production speed, automation and optional accessories. Field installation supervision and training are also available.
Installation and Operation
Key measures for light keel roll forming line installation and operation:
- Proper material handling space for coils and finished products
- Levelled mounting and anchoring of equipment
- Aligning and coupling drive shafts
- Electrical, utility and compressed air connections
- Trial runs to verify keel quality
- Documenting forming parameters and settings
- Operator training on procedures
- Safety protocols like interlocks, guards
- Preventive maintenance schedules
Proper installation and operation training from the supplier’s engineers is key for maximizing production line performance. Strict safety measures are essential.
Maintenance Requirements
Proactive maintenance practices for light keel rolling lines:
- Periodic inspection of mechanical drives
- Lubricating bearings, motors, gears
- Checking roll condition; replacing worn rolls
- Sharpening or replacing shear blades
- Sensor cleaning and calibration
- Checking hydraulic systems and pipes
- Inspecting guards and safety devices
- Electrical, pneumatic systems checks
- HVAC maintenance for control panels
- Noise monitoring and mitigation
- Documentation and tracking
Timely maintenance as advised by the manufacturer ensures maximum production uptime at the required quality and safety levels.
Selection Considerations for Light Keel Roll Forming Equipment
Key factors for choosing light keel roll forming equipment:
- Production capacity – line speed matches needed output
- **Profile dimensions **– capability to produce the required sizes and thicknesses
- Performance features – speed, precision, flexibility
- Automation – ease of operation and control
- Roll tooling – design, quick change ability and costs
- Material handling – decoiler capacity, finished product stacking
- Quality standards – consistency, tolerances, finishes
- Costs – competitive pricing considering capabilities and local service
- Manufacturer reputation – experience, proven reliability
- After-sales service – installation support, training, maintenance
Selecting the right supplier with suitable production capacity, efficient roll designs, automated controls and local service provides a long-term value advantage.
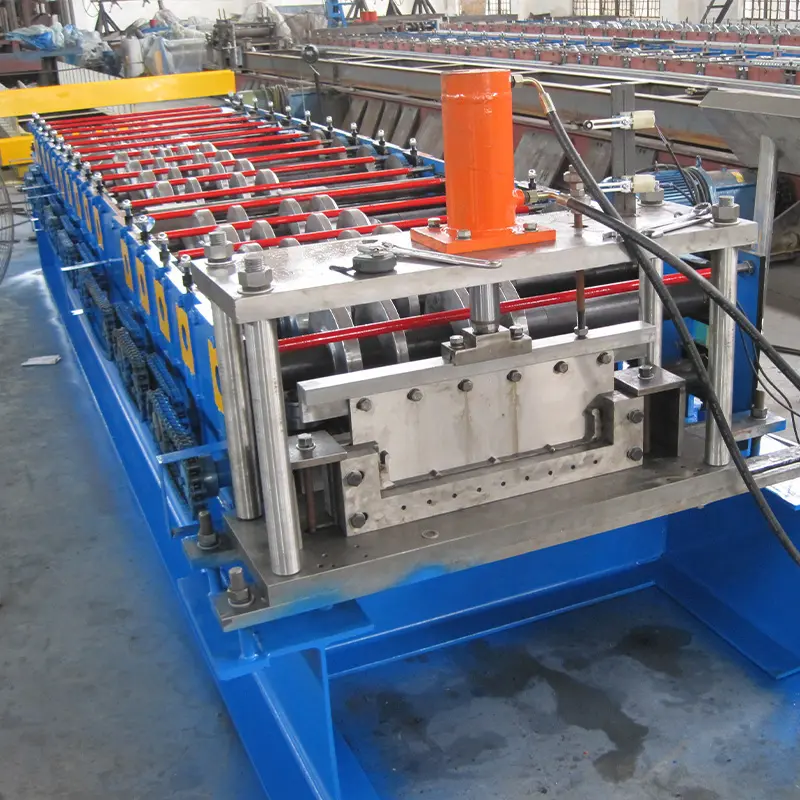
Pros and Cons of Light Keel Roll Forming
Advantages:
- High production volumes
- Lower cost than hot-rolled sections
- Consistent dimensional accuracy
- Flexible equipment for different sizes
- Faster construction with preformed keels
- Lighter sections reduce transportation costs
- Easier integration with roofing systems
Disadvantages:
- High initial equipment investment
- Dedicated lines for each profile
- Space requirements for equipment
- Limitations on keel length
- Requires skilled technical operators
- Additional structural analysis
- Aesthetics may not suit all buildings
FAQs
What are light keels used for?
Light keels provide economical substitutes to hot-rolled sections for roof truss framing systems in factories, workshops, agricultural buildings and aircraft hangars.
How are light keels produced?
Light keels are produced by continuously cold roll forming metal coil strips through a series of roller dies to progressively form the web, flanges and lip to create the keel profile.
What are the benefits of light keels?
Benefits include lower cost than hot-rolled steel, faster construction, flexibility in lengths, and light weight for transportation and handling. They allow customized profiles tailored to requirements.
What steel thickness is used for light keels?
Typical thickness ranges from 0.5 mm to 1.2 mm for most applications. Minimum 0.8 mm thickness is recommended for adequate stiffness. Thicker coils can produce stronger keels.
What factors affect light keel roll forming line design?
Key factors are production speed, keel dimensions, material thickness, performance needs, automation, quick roll changes, and material handling capabilities.
What maintenance is required for light keel rolling lines?
Regular maintenance involves inspecting mechanical drives, roll condition, lubrication, hydraulics, sensors, electrical systems, and safety features. Timely maintenance minimizes unplanned downtime.
What safety measures are needed for light keel rolling equipment?
Critical safety measures include emergency stops, interlocks, machine guarding, safety protocols, and worker training. Noise and dust mitigation may be required.
How to select a light keel roll former supplier?
Consider production capacity, keel size range, automation, roll design, service support and costs. Choose a reliable manufacturer capable of delivering the profiles needed with good quality and line productivity.
What typical speeds can light keel rolling mills achieve?
Typical production speeds range from 10 to 50 meters per minute. Higher speeds are possible with more powerful drives and streamlined material handling.