Carriage board, also known as top hat or C-profile, is a versatile roll formed section used extensively in light steel framing for walls, floors, roofs and other building components. Carriage board roll forming machines are designed specifically to produce these hat channel profiles efficiently.
This guide provides a comprehensive overview of carriage board roll formers covering their working, types, specifications, applications, advantages, and more.
Introduction to Carriage Board Roll Forming Machines
Carriage board roll forming machines are a specialized type of metal roll forming equipment engineered to produce top hat or C-profiles from coiled steel strips.
Key features:
- High productivity continuous processing
- Capable of high forming speeds
- Quick changeover between profiles
- Durable construction for heavy industrial use
- Advanced drives for precision and efficiency
- User-friendly controls and operation
Carriage board profiles are an important light gauge steel framing component for wall studs, floor joists, roof trusses and other structural parts in residential and commercial construction.
Roll forming is an ideal process for producing lengths of uniform carriage board in bulk in different sizes.
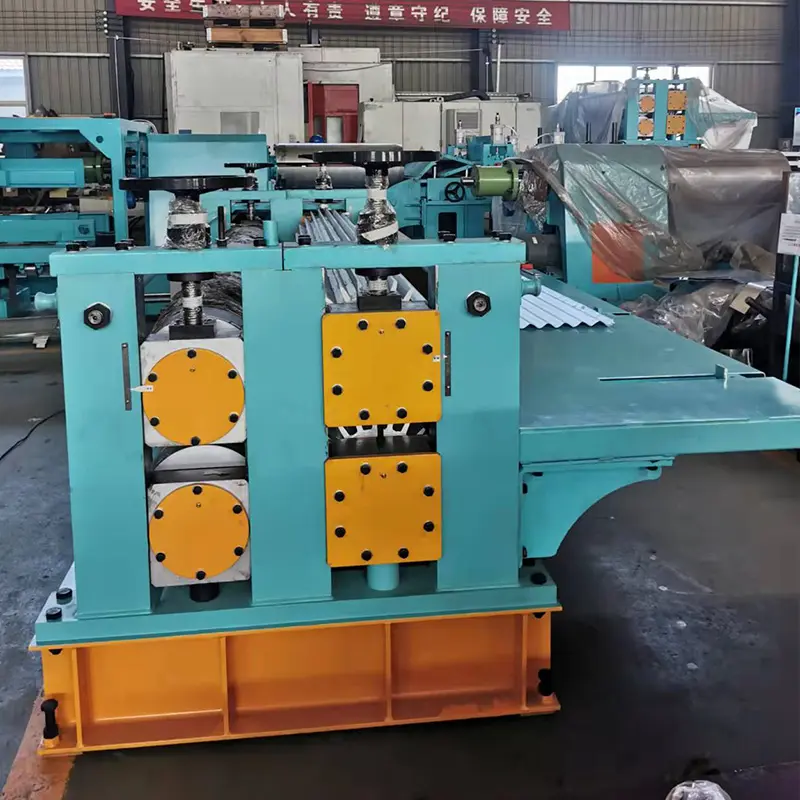
Working Principle of Carriage Board Roll Formers
Carriage board roll forming machines operate on the principle of incremental bending of strip material through a series of roller stations to gradually form the hat-shaped cross-section.
The key processes involved are:
- Coiled steel strip fed into the roller forming section
- The strip passes through a series of roller stations
- Rollers progressively bend the strip through calibrated angles
- Forming flanges and web until final C-profile is achieved
- Formed profile cut to length by built-in cutoff press
- Formed boards stacked for next process
Advanced tooling design allows fast changeovers between different carriage board dimensions through quick roller changes.
Types of Carriage Board Roll Forming Machines
Carriage board roll formers are available in different types based on size, production speed, automation levels and other factors:
By Roller Stations
Type | Details |
---|---|
10 Roller | Basic economical model |
12 Roller | Standard configuration |
16 Roller | For complex profiles |
By Automation Level
Type | Description |
---|---|
Manual | Manual material feeding and offloading |
Semi-Auto | Auto feeding but manual offload |
Fully Auto | Auto material in and out with stacker |
By Production Speed
Type | Speed |
---|---|
Standard | Up to 80 m/min |
High Speed | Up to 120 m/min |
Ultra High Speed | 150 – 200 m/min |
Customized Carriage Board Lines
- Tailor-made to specific production requirements
- Integrate decoiler, stacker, punching, cutting
- For high volume roll forming lines
Main Components of Carriage Board Roll Forming Machines
Carriage board roll forming machines consist of several specialized components engineered to work together:
Roller Stations
- Forming stations with hardened rollers
- Progressively bend strip through calibrated angles
- Quick change design for fast size changeovers
Forming Rollers
- Hardened and ground for precision
- Designed for forming loads and friction
- Different profiles may need specific rollers
Strip Feeding System
- Feeds strip from coiled steel into rollers
- Consists of straightener, feed rolls, servo drive
- Controls feed rate to match line speed
Hydraulic Cutoff Press
- Cuts profile to length at output
- Hydraulic powered clamping
- Also presses and punches holes if needed
Electrical Control System
- Touchscreen HMI for control and monitoring
- PLC automates production
- VFD motor drives with speed control
Specifications of Carriage Board Roll Forming Machines
Carriage board roll forming machines are available in a range of specifications and capabilities to match production needs:
Machine Dimensions
Specification | Details |
---|---|
Length | 6m to 12m typically |
Width | 1.5m to 2.5m |
Height | 1.8m to 2.2m |
Weight | 3500 kg to 6000 kg |
Forming Capability Range
Parameter | Range |
---|---|
Metal thickness | 0.45 – 1.2 mm |
Profile depth | 50 – 300mm |
Flange width | 20 – 80mm |
Forming speed | Up to 200 m/min |
Main Drives and Motors
- Main motor: 11 kW to 22 kW
- Hydraulic power pack: 7.5 kW to 15 kW
- Screw air compressor: 1.5 kW to 3 kW
- Servo motor for strip feeding: 1.5 kW to 7.5 kW
Power Supply Requirements
- Voltage: 380V to 415V, 3 Phase
- Frequency: 50 Hz
- Current: 25A to 60A based on motor rating
Applications and Uses of Carriage Board Profiles
Key applications and uses of carriage board roll formed profiles:
Construction and Building
- Wall studs in light gauge steel framing
- Floor joists and roof trusses
- Structural purlins and girts
- Wall sheathing support and bracing
Infrastructure and Industrial
- Platforms, walkways, catwalks
- Mezzanine floors
- Safety railings and ladders
- Equipment support structures
Transportation and Automotive
- Truck and trailer bodies
- Cargo containers
- Railway freight cars
- Bus and motorcoach flooring
Carriage board combines high strength with lightweight making it suitable for numerous structural uses across industries.
Benefits of Using Carriage Board Roll Forming Machines
Using dedicated carriage board roll forming machines offers significant benefits versus other production methods:
- High productivity of up to 200 meters per minute
- Capability to produce various standard and custom profiles
- Fast changeovers between different profile sizes
- Consistent quality and tolerances
- Cost effective versus other forming processes
- Minimal material waste
- Lower energy consumption than batch methods
- Compact equipment footprint
- Easy to operate with low skilled labor
- High uptime and reliability
Automated carriage board roll forming lines deliver maximum efficiency and throughput for high volume requirements.
How to Choose a Carriage Board Roll Forming Machine
Key factors to consider when selecting a carriage board roll former:
- Reputed manufacturer with proven equipment quality
- Production speed rating aligns with output needs
- Profile size range meets current and future needs
- Automation options like decoiler, stacker etc.
- Heavy duty construction for durability
- Quick changeover and easy maintenance
- Experience supplying to range of industries
- Responsive after-sales service and support
- Overall value for money based on productivity
Partnering with an expert supplier like XYZ Machinery ensures selecting equipment optimized for specific production targets.
Carriage Board Roll Former Cost Analysis
Carriage board roll forming machine cost depends on:
Initial Purchase Price
Machine Type | Indicative Price Range |
---|---|
Basic Manual | $60,000 to $100,000 |
Fully Automatic | $150,000 to $250,000 |
Large High Speed | $250,000 to $500,000 |
- More roller stations, automation, speed increase costs
- But higher throughput offsets higher price
Operational Costs
- Power consumption: 10 kW to 30 kW range
- Labor: 1 to 2 operators per shift
- Maintenance: Approximately 2% of machine cost
Cost Per Piece Analysis
- Machine cost / lifetime pieces produced
- Higher production volume = lower cost/piece
- Saving from lower scrap also offsets price
- Carriage board roll forming reduces overall cost along the value chain
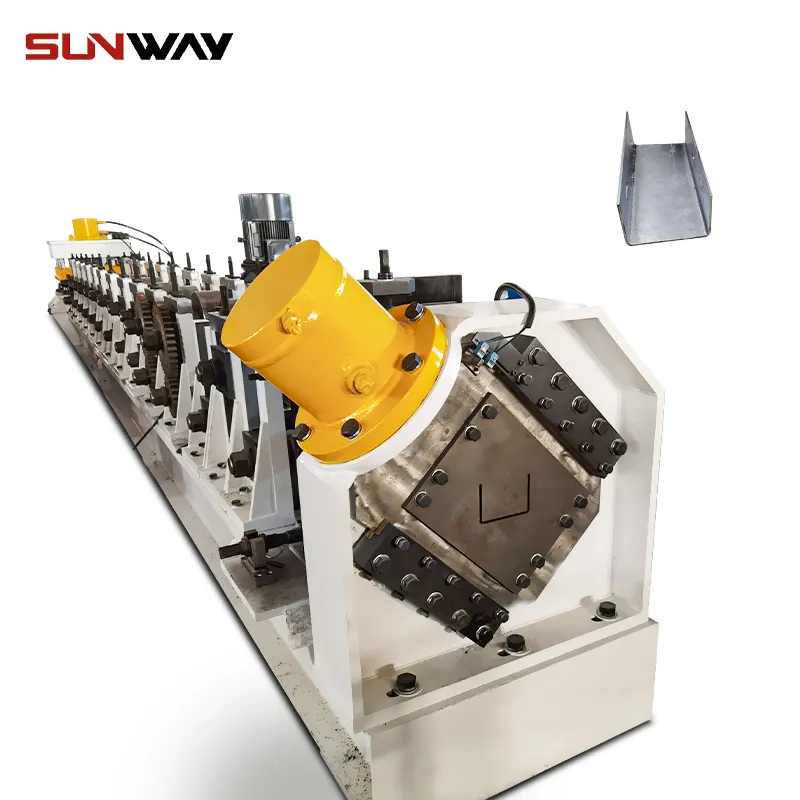
How to Install a Carriage Board Roll Forming Machine
Proper installation is key to achieving optimal performance from a carriage board roll former.
Site Preparation
- Level concrete foundation as per floor plan
- Floor trenches for utilities if needed
- Power supply lines to control panel
- Compressed air and hydraulic lines
- Enough clearance for safe access
Receiving and Positioning
- Unload components safely using forklifts/cranes
- Place machine as per installation drawings
- Use spreader bars for lifting where needed
Assembly and Alignment
- Assemble machine frame as per procedure
- Install forming rollers and make driveline connections
- Align rollers and test for smooth rotation
- Install electrical cabinets and wire up panels
Commissioning and Trial Run
- Check all anchors, mounts and clearances
- Run trial with dummy material to confirm operation
- Monitor for vibrations or abnormal sounds
- Debug any issues before full production
Taking time upfront to properly install the machine pays dividends for the long run.
Operation and Maintenance of Carriage Board Roll Formers
Following proper operating guidelines and maintenance procedures is key to trouble-free functioning of a carriage board roll former over its service life.
Daily Operation
- Visual check of machine before startup
- Monitor strip feeding, profile forming quality
- Allow reasonable warm up and cooldown periods
- Use gauges to check if hydraulic pressure is adequate
- Clean formed scrap pieces
- Lubricate moving parts as needed
Periodic Maintenance
- Schedule downtime for routine maintenance
- Visually inspect all components for wear/damage
- Verify alignment of shafts, sprockets and chains
- Check coolant flow to motors and gearboxes
- Monitor hydraulic fluid levels and filtration
- Replace worn forming rollers
- Refinish contacting roller surfaces
Safety
- Ensure proper guarding around moving parts
- Use lockout/tagout procedures during maintenance
- Check E-stops, pull cords are functional
- Establish electrical safety procedures
- Enforce mandatory PPE for operators
Effective operation and maintenance practices result in maximum uptime and extended machine life.
Troubleshooting Guide for Carriage Board Roll Formers
Issue | Possible Causes | Corrective Actions |
---|---|---|
Profile distortion | Misaligned rollers, stripper plates | Realign rollers, adjust stripper plates |
Scrap profile sections | Improper roll gaps | Adjust roll gaps as per procedure |
Excessive strip camber | Worn forming rollers | Resurface or replace worn rollers |
Hydraulic oil overheating | Low oil or pump issues | Check level, inspect pump and valves |
Motor overload trip | Mechanical jam, line stall | Clear jam, restart cautiously |
Machine vibration | Misalignment, unsecured part | Align and tighten loose components |
Electrical fault | Loose wiring, short circuit | Inspect wiring for defects |
Scratched material surface | Debris on rolls or material | Clean rollers and improve strip cleaning |
Consulting the machine manual and contacting the manufacturer’s service team helps resolve issues quickly to minimize downtime.
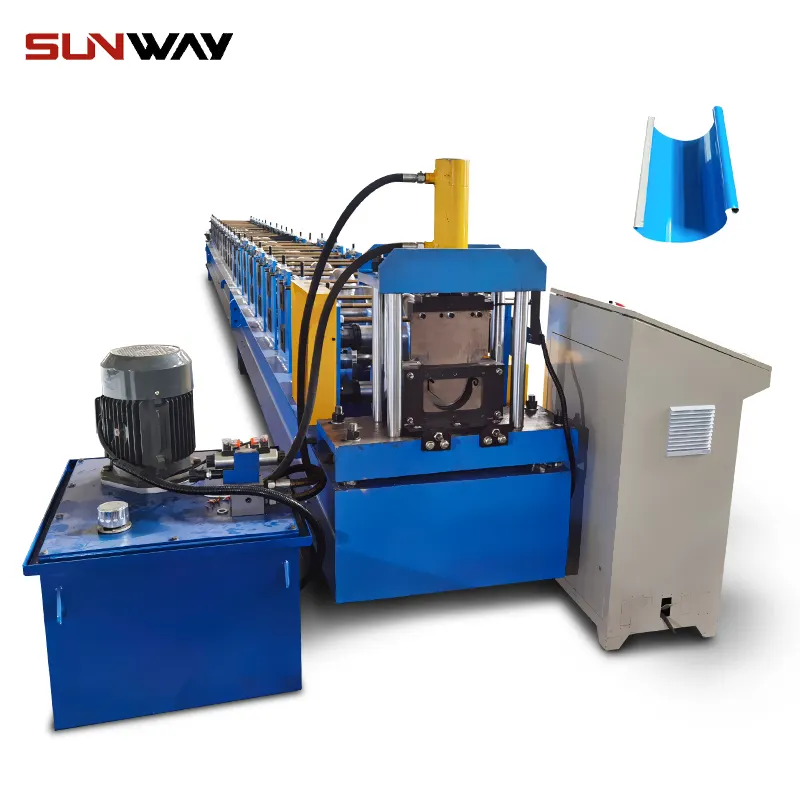
FAQ
Q: How fast is the profile size changeover on carriage board roll formers?
A: On advanced roll formers with quick change features, size changeovers can be completed in 10-15 minutes.
Q: What quantities of carriage board can be produced?
A: Depending on machine speed and run hours, output can range from 100s of feet to over 1000 feet per hour.
Q: What is the tolerance that can be achieved on profiles?
A: Roll formed carriage board typically has a dimensional tolerance of +/- 0.4mm. Superior machines can achieve +/- 0.2mm.
Q: How thick of steel sheet can be roll formed into carriage board?
A: Standard carriage board machines go up to 1.5mm thickness. Heavy duty models can form over 2mm thickness.
Conclusion
Carriage board roll forming lines offer an efficient solution for high volume production of light gauge structural steel profiles like top hats and C-channels. With their fast changeovers, high throughput and reliability, these machines deliver significant productivity and cost benefits versus other profile manufacturing methods. Leading roll former manufacturers offer customized lines engineered specifically to meet the quantity, size variations and quality demands of clients.