Introduction to Purlin Roll Forming
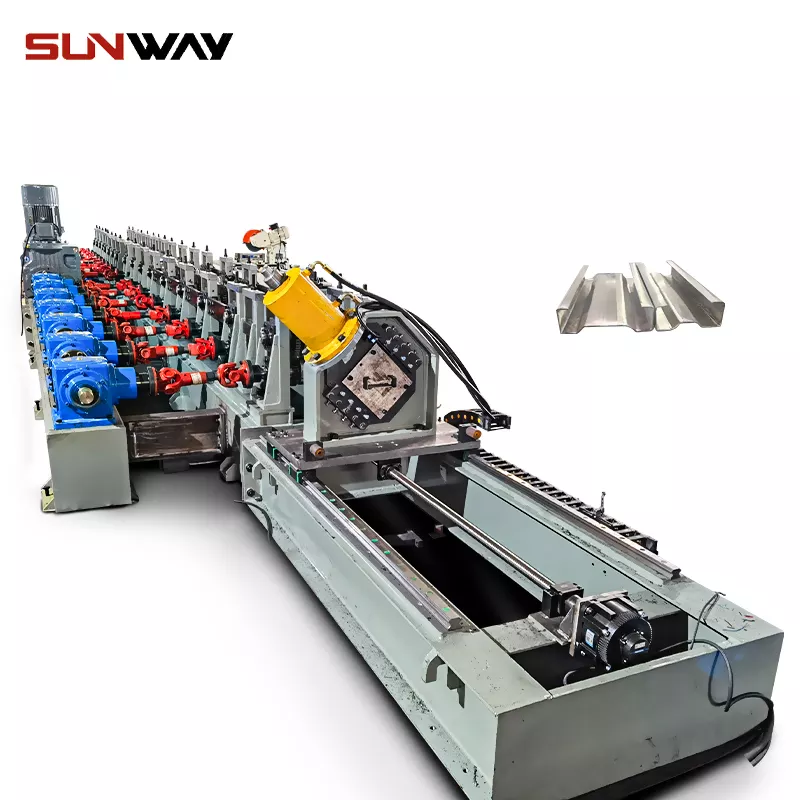
Purlin roll forming is a manufacturing process used to create various types of purlins, which are structural components typically used in construction and industrial applications. Purlins are long, narrow beams that are installed horizontally between structural supports to provide additional support for roof and wall panels.
The purlin roll forming process involves feeding a strip of metal through a series of rollers that gradually bend and shape the metal into the desired profile. Different types of purlins can be produced using this process, including C-purlins, Z-purlins, and U-purlins.
C-purlins have a unique profile that resembles the letter “C” and are typically used in roof and wall framing applications. Z-purlins, on the other hand, have a profile that resembles the letter “Z” and are often used in applications where more support is needed. U-purlins have a profile that resembles the letter “U” and are often used in applications where the purlin is required to support heavy loads.
In summary, purlin roll forming is a manufacturing process used to create various types of purlins, including C-purlins, Z-purlins, and U-purlins. These components are essential for providing additional support in construction and industrial applications, and the roll forming process allows for precise and efficient production of these components.
Common Mistakes in Purlin Roll Forming
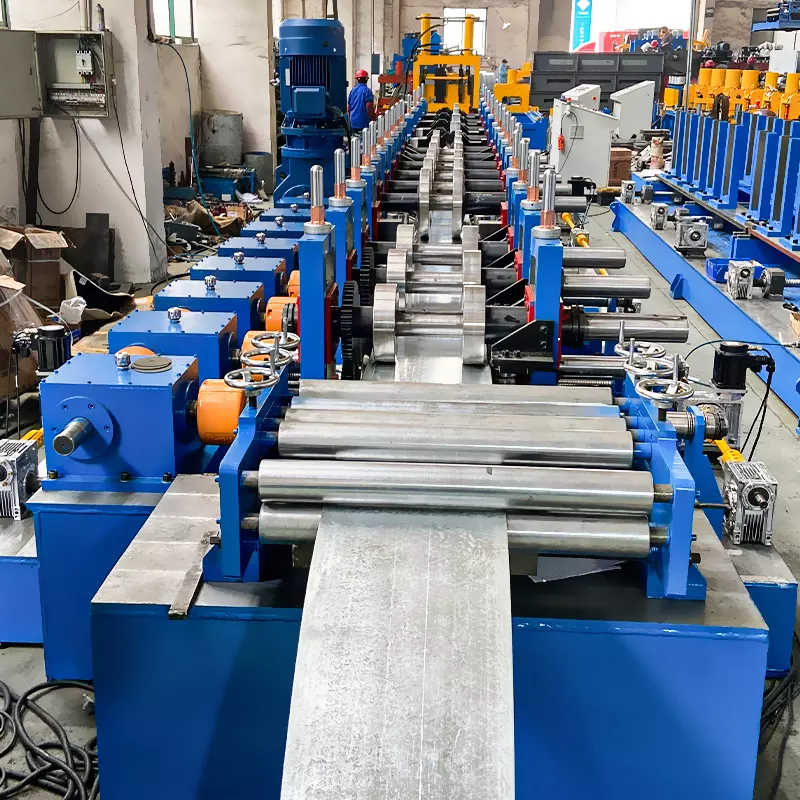
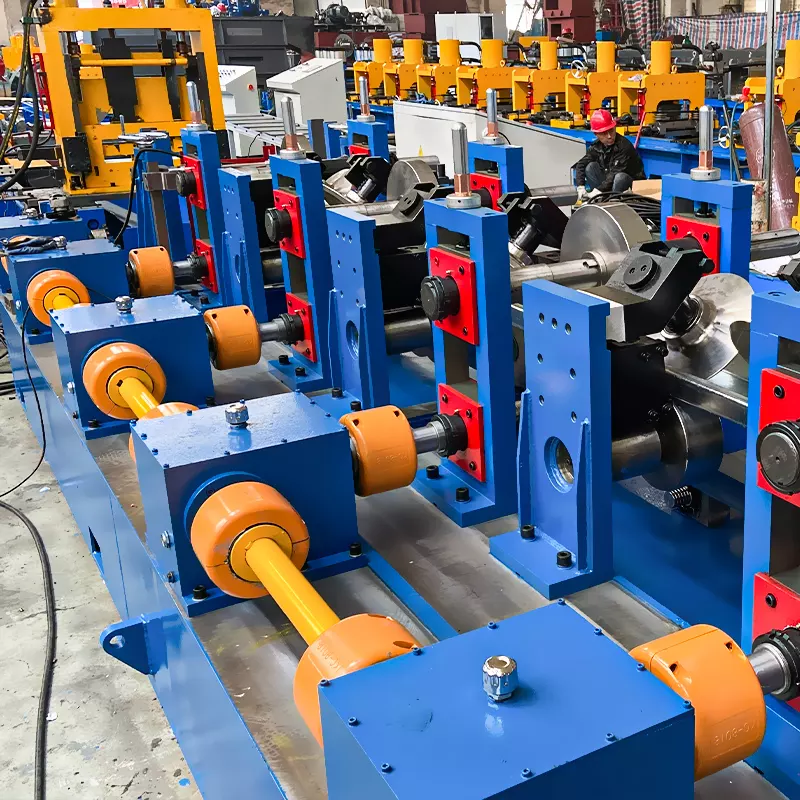
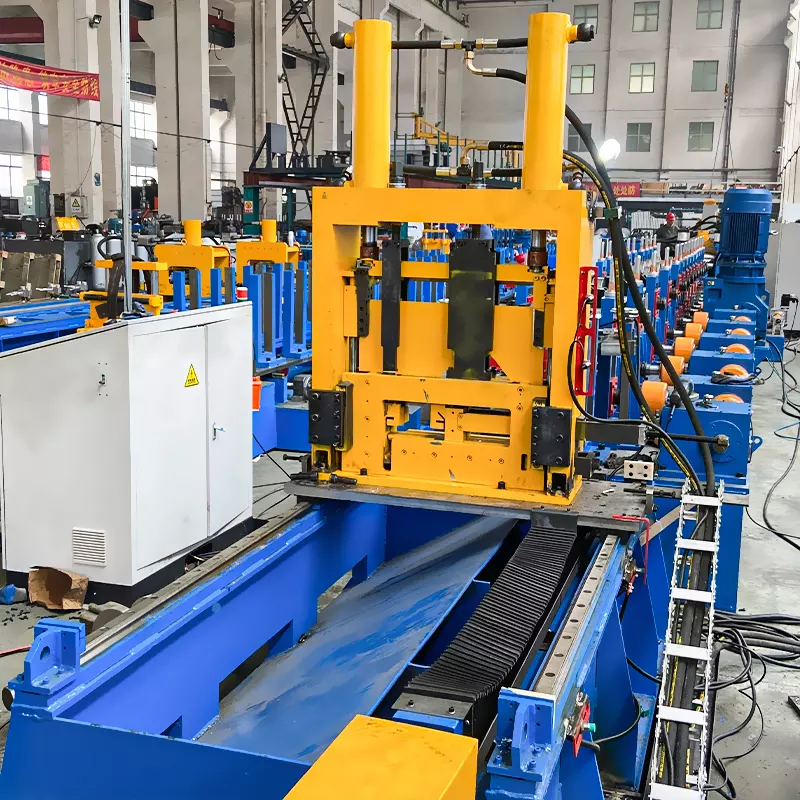
Here are some of the most common mistakes made during purlin roll forming:
- Material Selection: One of the most common mistakes in purlin roll forming is using the wrong material. This can lead to issues such as excessive waste, material distortion, and product defects. Using the right material, with the correct thickness and tensile strength, is essential for producing high-quality purlins.
- Tooling Design: Another common mistake is poor tooling design. Tooling design can affect the quality and consistency of the finished product. Some common tooling design mistakes include using incorrect tooling clearance, inadequate tooling strength, or poorly designed forming rolls.
- Machine Setup: The setup of the roll forming machine can also impact the quality of the finished product. Some common machine setup mistakes include improper alignment, incorrect tension settings, or inadequate lubrication. These mistakes can lead to inconsistent product quality, machine breakdowns, and increased downtime.
- Quality Control: Failing to implement proper quality control measures is another common mistake in purlin roll forming. This can include not inspecting finished products for defects or not measuring key parameters such as dimensional accuracy and strength. Without proper quality control measures, it is difficult to ensure that the finished product meets the required standards.
By identifying these common mistakes, manufacturers can take steps to optimize their purlin roll forming processes and improve the quality of their products. It is essential to pay close attention to material selection, tooling design, machine setup, and quality control to produce high-quality purlins consistently.
Material Selection for purlin roll forming
Selecting the right material for purlin roll forming is crucial to ensure the quality and efficiency of the process. Material selection involves considering factors such as thickness, width, and tensile strength.
Choosing the wrong material can lead to several problems, such as excessive waste, material distortion, and product defects. For instance, using a material that is too thin can result in purlins that are weaker than required, leading to failures in the structure. On the other hand, using a material that is too thick can lead to difficulties in the roll forming process, causing material wastage and increasing production costs.
Tensile strength is another critical factor to consider in material selection. The strength of the material needs to match the intended application, ensuring that the purlins can support the required loads without bending or breaking. If the material selected does not meet the required strength, the purlin will fail, leading to costly repairs and safety hazards.
Furthermore, material distortion is another problem that can arise from using the wrong material. If the material is not suitable for the roll forming process, it can become deformed or bent during the process, leading to inconsistent purlin quality.
In summary, selecting the right material for purlin roll forming is critical to ensure that the finished product meets the required specifications. Choosing the right material helps avoid problems such as excessive waste, material distortion, and product defects, which can impact the safety, quality, and cost-effectiveness of the final product. It is, therefore, essential to carefully consider the material’s thickness, width, and tensile strength to ensure optimal performance of the purlin roll forming process.
Machine Setup of the roll forming machine
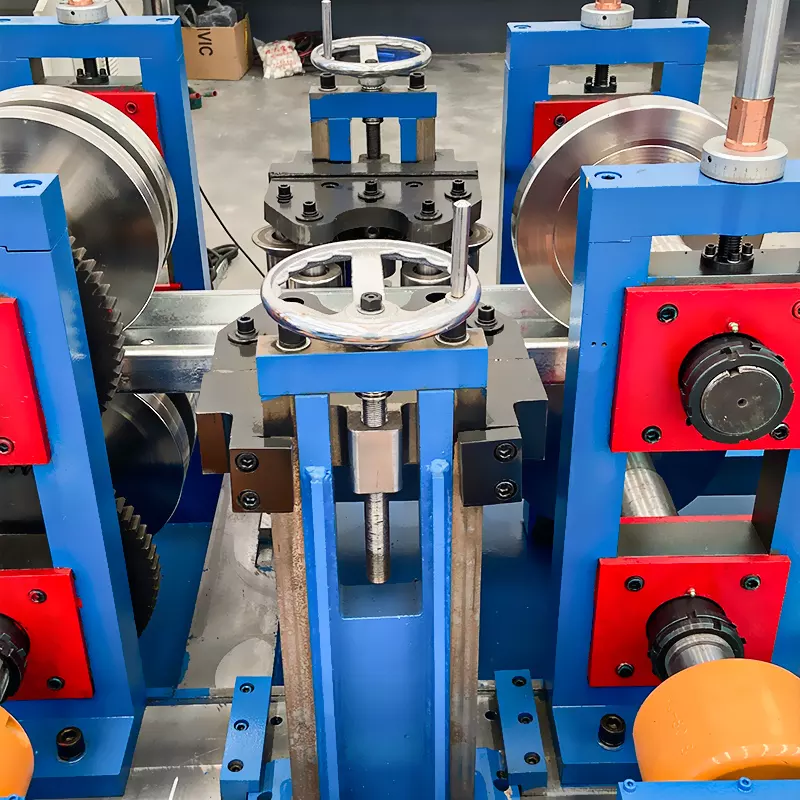
The setup of the roll forming machine is a critical factor in the quality of the finished product. Even the slightest errors during setup can have a significant impact on the purlin’s final shape, strength, and dimensional accuracy. Here are some common mistakes in machine setup and how they can affect the finished product:
- Improper Alignment: Improper alignment of the roll forming machine can lead to inconsistent purlin quality. Misaligned components can cause the material to feed through the machine unevenly, leading to dimensional inaccuracies and even product defects.
- Incorrect Tension Settings: Tension settings play a vital role in the roll forming process. If the tension is set too high, it can cause material stretching and deformation, leading to dimensional inaccuracies and product defects. Conversely, if the tension is too low, it can cause material slippage, leading to production delays and material wastage.
- Inadequate Lubrication: Proper lubrication is critical in ensuring the smooth operation of the roll forming machine. Inadequate lubrication can cause friction between components, leading to machine breakdowns and production delays. It can also cause material distortion and product defects.
- Tooling Setup: Incorrect tooling setup can lead to dimensional inaccuracies and product defects. Poorly set up tooling can result in a lack of proper support, causing the material to bow or twist, leading to dimensional inaccuracies.
In summary, the setup of the roll forming machine plays a vital role in the quality of the finished product. Machine setup errors such as improper alignment, incorrect tension settings, inadequate lubrication, and tooling setup can lead to dimensional inaccuracies, material distortion, and product defects. Proper attention to detail and care during machine setup can help to avoid these mistakes and improve the quality and efficiency of the purlin roll forming process.
Best Practices for Purlin Roll Forming
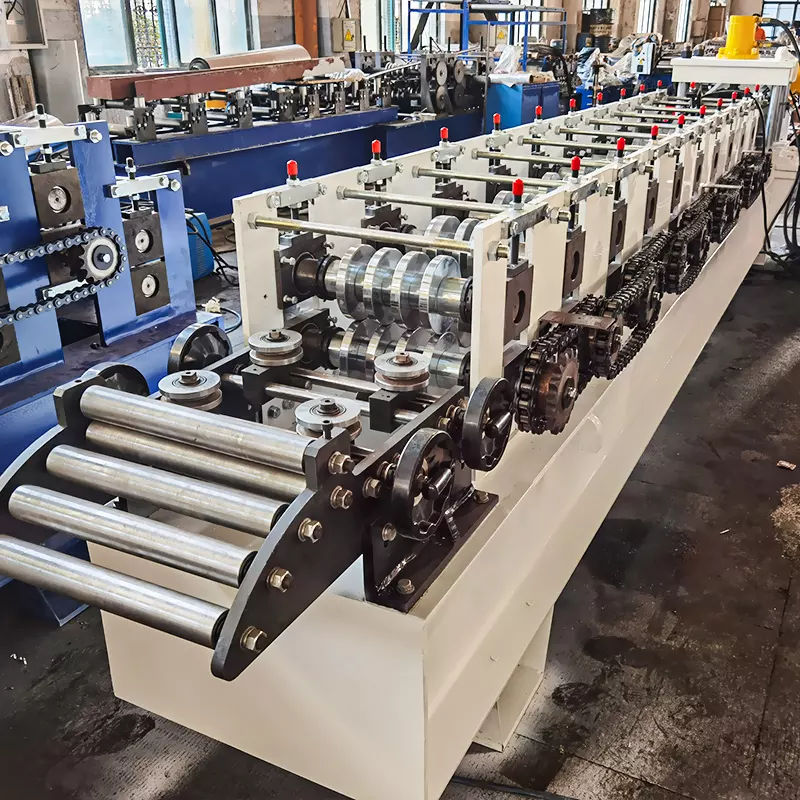
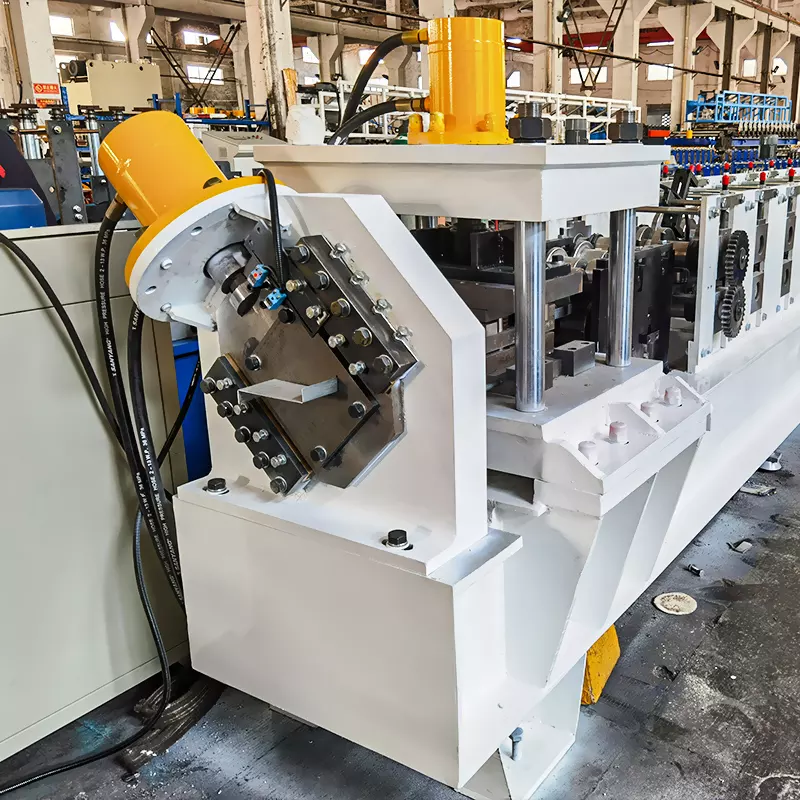
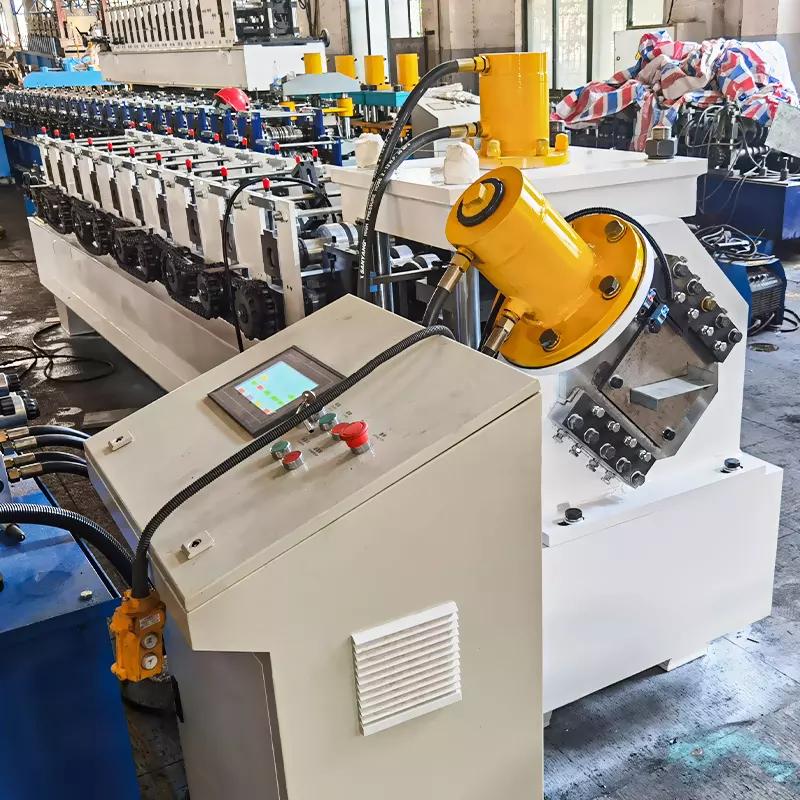
To avoid common mistakes in purlin roll forming and optimize the process, consider the following best practices:
- Material Selection: Choose the right material based on the intended application, considering factors such as thickness, width, and tensile strength. Work with suppliers who provide high-quality materials that meet the required specifications.
- Tooling Design: Ensure proper tooling design, including correct tooling clearance, adequate tooling strength, and well-designed forming rolls. Utilize computer-aided design (CAD) software to model and test tooling designs before production.
- Machine Setup: Set up the roll forming machine correctly, ensuring proper alignment, correct tension settings, adequate lubrication, and appropriate tooling setup. Establish clear machine setup procedures and conduct regular maintenance to ensure consistent quality and efficiency.
- Quality Control: Implement a comprehensive quality control system that includes inspecting finished products for defects, measuring key parameters such as dimensional accuracy and strength, and tracking and analyzing quality data to identify areas for improvement.
- Continuous Improvement: Regularly assess and analyze the purlin roll forming process to identify opportunities for improvement. Consider investing in automation technologies such as robotic handling and in-line inspection systems to increase productivity and quality.
By following these best practices, manufacturers can optimize the purlin roll forming process and produce high-quality purlins consistently. Careful attention to material selection, tooling design, machine setup, quality control, and continuous improvement can help manufacturers avoid common mistakes and improve their bottom line.
In conclusion, avoiding common mistakes in purlin roll forming is crucial to producing high-quality and efficient purlins consistently. Key areas to focus on include material selection, tooling design, machine setup, quality control, and continuous improvement. Proper attention to these areas can help manufacturers avoid common mistakes such as material waste, dimensional inaccuracies, and product defects. By implementing best practices and strategies for optimizing the roll forming process, manufacturers can improve their bottom line and produce purlins that meet or exceed industry standards.