oem door shutter roll forming machine shape metal coils into customized profiles by progressively bending the material through a series of roller dies. OEM door shutter roll forming machines are designed specifically to produce rolled metal door shutters and rolling grilles used for safety, security, ventilation, or space separation.
Key details:
- Produce metal door shutters and grilles up to 3m wide from coil stock
- Form complex custom profiles through incremental cold rolling process
- Automated operation with high production efficiency
- Require tooling design and manufacture for custom profile shapes
- Used by door shutter manufacturers and metal fabrication shops
OEM Door Shutter Roll Forming Machine Equipment Guide
Equipment Type | Description |
---|---|
Coil lines | Uncoil and feed metal coil stock |
Roll forming stations | Bend sheet incrementally through roller dies |
Punching/cutting | Punch holes or trim profiles to length |
Hardware insertion | Automatically insert hinges/guides |
Support equipment | Decoilers, straighteners, levelers |
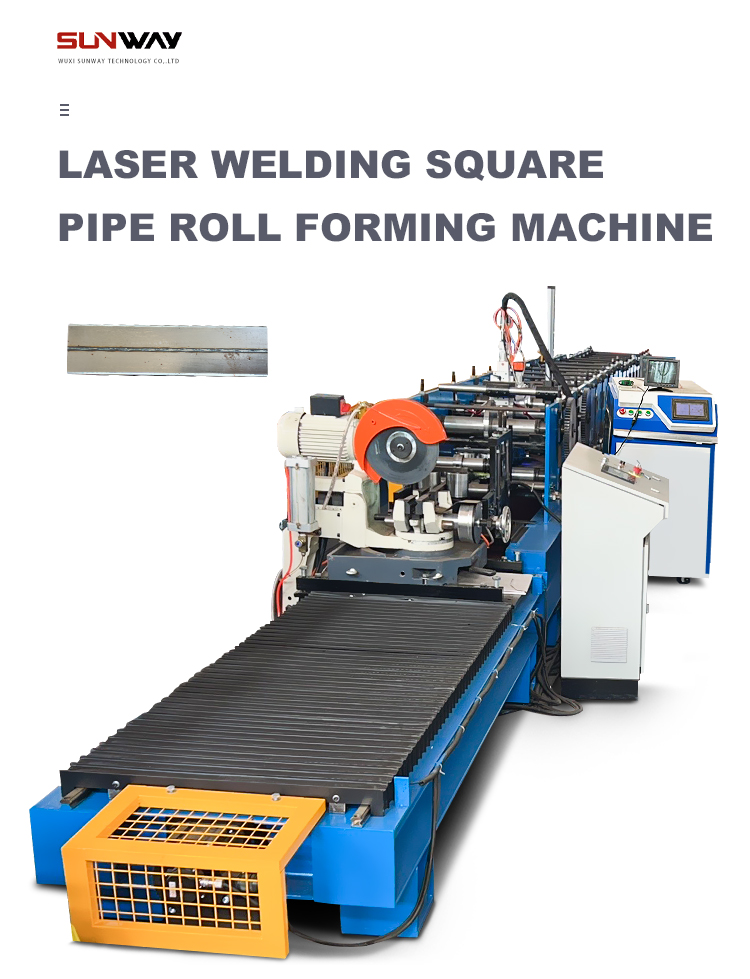
OEM Door Shutter Roll Forming Machine Types
Type | Description |
---|---|
Interlocked roll forming lines | Combine multiple stations for high automation |
Compact machines | Small footprint, lower cost, manual operation |
Customized lines | Tailored to produce specific profiles |
Double/triple structures | Multi-profile and shaped forming |
Roll and punch lines | Integrated punching and cutting |
Working Principle of OEM Door Shutter Roll Forming Machines
OEM door shutter roll forming machines produce longitudinally bent metal profiles from flat strip steel or aluminum coils. The material feeding system uncoils the metal sheet and feeds it through a series of roller dies at each successive forming station.
The roller dies bend the sheet incrementally to the desired profile shape without excessive thinning or stretching the material. Cutting units trim the continuously formed profiles to specified lengths for the end application. Automated lines with multiple roll forming stations, punching, hardware insertion allow high-volume production of finished door shutter products.
Customized tooling is mounted on the roll forming stations to create the desired shape profiles. Common door shutter profiles include round ribbed, angle iron, rectangular hollow, grille, perforated sheets. The flexibility of roller die tooling allows forming complex asymmetric shapes.
Insertion of embedded hinges, endlocks and guides can be integrated on automated OEM door shutter lines. Conveyors collect and stack finished products. Support equipment like decoilers, straighteners, and levelers enhance process stability.
Material Handling in OEM Door Shutter Roll Forming
Process Stage | Equipment Used |
---|---|
Stock material | Metal coils (steel, aluminum) |
Uncoiling | Powered decoilers |
Feeding | Rollers, pinch rolls, guides |
Straightening | Roller levelers |
Profile forming | Roll forming stations with custom tooling |
Cutting | Pneumatic/hydraulic cut-off knives |
Hardware insertion | Automatic pick-place mechanisms |
Stack/collect | Motorized conveyors, boxes |
OEM Door Shutter Roll Forming Machine Design
The design of OEM roll forming lines for door shutter production involves:
- Defining target profile shape and dimensions
- Component layout planning considering production workflow
- Tooling design for custom profile forming
- Programming of automatic control logic
- Integrating safety features and guards
- Allowing flexibility for future profile variations
The line layout includes the arrangement of uncoiling and feeding first, then roll forming stations, followed by punching/cutting units, and finally, product collection. Ergonomic factors for operator access are incorporated.
CAD software creates models of custom profile designs as inputs for machining the roller dies. The tolling is mounted sequentially on modular stand housing frames.
PLC programming coordinates actors likeservos, sensors to automate feeding, forming, cutting in synch. Operator screens display machine status. CE-compliant safety mechanisms are installed.
Designed with upgrades in mind, door shutter profiles can be changed by altering roller die tooling without needing entire new systems.
-
Rolling Shutter Slat Roll Forming Machine
-
Electrical Cabinet Frame Roll Forming Machine
-
Din Rail Roll Forming Machine
-
Cable Ladder Roll Forming Machine
-
PV Mounting Bracket C Shape Profile Roll Forming Machine
-
Cable Tray Roll Forming Machine
-
Steel Coil Cut To Length Line Machine
-
Steel Coil Cut To Length Line Machine
-
Steel Coil Cut To Length Line Machine
Punching and Cutting Equipment in Roll Forming Lines
Operation | Method | Equipment |
---|---|---|
Cutting to length | Pneumatic/hydraulic knives | Swing arm cut-offs |
Hole punching | Pneumatic punch heads | Eccentric C-frame punch presses |
Forming slots/louvers | Rotating slitters | Helical slitter heads |
Trimming edges | Tilting circular shears | Double blade shears |
Combined operations | Integrated modules | Punch-shear combo units |
Hardware Insertion Equipment
Hardware components like hinges, guides, end locks are inserted automatically into formed profiles on high-end lines. Rotary indexing tables position profiles precisely for synchronized pick-place mechanisms to insert hardware at preset locations.
Servo-controlled axes push components into profile cavities. Systems can be customized for specific hardware items and profiles. Sensors confirm correct insertion before profiles get cut to finished shutter length.
Degree of Customization Offered
OEM door shutter roll forming machinery can be supplied in standardized designs for general profiles or customizable machines tailored to site-specific requirements:
Standardized:
- Cost-effective for high-volume commodity profiles
- Limited flexibility for profile variations
Customized:
- Profile tooling designed for unique shapes
- Automation modules fit production needs
- Expensive initial development
- Flexible capacity scaling
Hybrid Approach:
- Platform model adaptable to new tooling
- Some custom add-ons like auto-packaging
- Balances cost, flexibility
Suppliers and Price Range of OEM Door Shutter Roll Forming Machines
Manufacturer | Location | Price Range |
---|---|---|
Dahching | Taiwan | $40,000 – $100,000 |
Formtek | India | $35,000 – $150,000 |
Jouanel | France | $250,000 – $1,500,000 |
Metform | Turkey | $60,000 – $250,000 |
Rollvis | Netherlands | $150,000 – $2,500,000 |
Price varies based on:
- Line automation level
- Production output requirements
- Width capacity needed
- Degree of customization
- Additional modules integrated
Installation and Commissioning
Proper installation by technicians ensures optimum machine performance:
- Civil works preparation of floor and utilities
- Positioning and fastening down components
- Coupling mechanical shafts/joints
- Connecting electric actuators/sensors
- Integrating subsystems uniformly
- Testing individual function execution
- Debugging hardware/software bugs
- Trial forming operations
- Parameter optimization for profiles
Thorough on-site commissioning verifies safe, reliable working before final handover.
Operation and Control of Roll Forming Lines
- Operator console for monitoring
- HMI touchscreen for commands
- Servo motors drive forming rolls
- PLC automates sequence coordination
- SCADA software for interlinked elements
- Die adjustment via NC manipulators
- Profile quality checking
- Parameter tweaking allowed
- Data logging for analytics
- Protection systems for safety
Maintenance Practices
Activity | Method | Frequency |
---|---|---|
Inspections | Visual checks for abnormalities | Monthly |
Lubrication | Oil/grease refills | Quarterly or on running hours |
Spare parts | Wear items like knives, belts etc. | As needed |
Tool resurfacing | Regrind/machine refinish | Yearly |
Sensor calibration | Reset reference levels | Yearly or on drift |
Record analytics | Production, error logs analysis | Continuous |
Guidelines for Choosing an OEM Door Shutter Roll Forming Machine Supplier
Parameter | Best Practices |
---|---|
Product quality | Samples evaluation, site visits |
Domain experience | Operational history, clientele |
Customization skills | Profile samples, tooling expertise |
Cost factors | Pricing transparency, commercials |
Production efficiency | Output rate commitments > 90% |
Service commitment | Commissioning support, AMCs |
Compliance assurance | ISO, CE certifications |
Upgrade flexibility | Clear provisions to alter future requirements |
Pros and Cons of OEM Door Shutter Roll Forming Machines
Advantages
- Highly productive continuous operation
- Labor cost reduction compared to manual bending
- Dimensional accuracy and repetitive quality
- Capability for complex asymmetric shapes
- Effective cold working avoids heating
- Lower energy consumption than stamping
- Quick changeovers with flexible tooling
- Compact equipment footprint
Limitations
- High initial tooling investment cost
- Limited material thickness capacity
- Profiles may still require secondary deburring
- Precision alignment of components critical
- Risk of deformities if parameters not set correctly
- Fixed PLC logic hampers production agility
- Difficult design alterations once tools made
- Longer lead times for customized lines
Applications of Roll Formed Metal Door Shutters and Grilles
End Use | Example Areas |
---|---|
Safety shutters | Storefronts, garages, windows |
Security doors | Warehouses, factories, residences |
Cages, enclosures | Machinery guards, mezzanines |
Partitions | Office spaces, cleanrooms |
Ventilation | Facades, auditoriums, walkways |
Carriageway doors | Shipyards, parking garages |
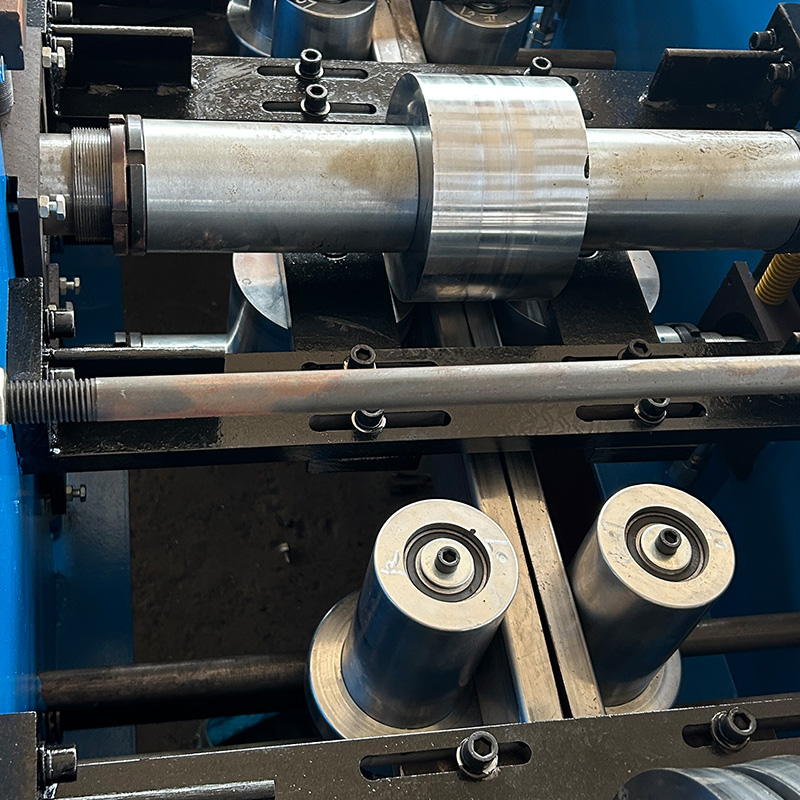
FAQ
Q: What thickness of metal sheet can be roll formed?
A: Standard machines handle 0.5 mm to 2.5 mm sheets. Heavy-duty lines available for up to 4 mm thickness.
Q: How fast is the production rate?
A: 15 to 40 meters/minute based on automation level, product complexity.
Q: What eventually determines equipment price?
A: Production output needs, line length, degree of customization primarily.
Q: Does the process require secondary finishing?
A: Minimal manual deburring may be needed but all forming completed.
Q: What regular maintenance is mandatory?
A: Schedule lubrication, inspections, wear/damage checks, sensor calibrations.
Q: How to calculate required line capacity?
A: Define monthly volume in square meters to produce based on operating hours. Incorporate possible future growth.