Overview of profile roll forming machine
profile roll forming machine is a continuous bending operation in which sheet or coil stock is gradually formed into the desired cross-sectional shape through a series of consecutive forming stations. The forming stations consist of opposing rolls that continuously bend and shape the moving strip of stock until the final profile is achieved.
Profile roll forming allows efficient and cost-effective production of metal parts with custom cross-sections. It is commonly used to manufacture parts like wall panels, roofing, door frames, racking systems, highway products, furniture components and more. The flexibility of roll forming allows creating almost any open cross-section profile.
Some of the key advantages of profile roll forming include:
- Highly automated process with low labor requirements
- Capable of high production rates and volumes
- Consistent and repeatable shaping of profiles
- Wide range of shapes and sizes can be formed
- Low tooling costs compared to other processes
- Minimal material waste since stock is formed progressively
- Applicable to various metals like steel, aluminum, brass etc.
Roll forming does require a higher initial investment in equipment compared to methods like brake pressing or stamping. However, profile roll forming becomes economical for large production lots given the high throughput and low operating costs. It is ideal for producing long lengths of repetitive profile cross-sections.
Profile Roll Forming Process
The profile roll forming process consists of multiple steps:
- Coil or sheet stock is loaded into a de-coiler or feed unit which straightens the strip.
- The stock is fed longitudinally through a series of rolling stations.
- Each stand of rolls makes a series of bends until the desired profile shape is incrementally formed.
- Cut-off dies produce pieces of required length as the profile exits the roll former.
- Formed sections are collected on a take-off table.
The gradual bending of stock through successive stands is the key to the roll forming process. The number of roll stands required depends on the complexity of the part shape being formed. Typical machines have between 3 and 16 forming stations.
Roll Forming Machine Components
Profile roll forming machines have three main sections:
- Stock feeding – De-coiler, straightener and feed unit
- Forming – Consecutive roll stands for bending sheet progressively
- Cutting – Shears or saws for cutting profiles to length
Here are the key components in a roll former:
Machine Section | Components |
---|---|
Stock Feeding | Coil hold down, de-coiler, feed rolls, stock guides, pinch rolls, sheet straightener |
Forming | Roll housing, top & bottom rolls, gearboxes, roll shafts |
Cutting | Cut-off press, flying die shear, end crushers |
Control | PLC, HMI, line controls |
Other | Guards, base frame, motors, hydraulics |
Roll Designs
The roll tooling is central to creating the desired profile shape. Roll forming depends on the precise bending action of contoured rolls to incrementally form the sections. Roll designs are customized to produce the exact geometry of the part being made.
Here are some common roll designs used:
- Circle forming – Used to form curved shapes and radii
- Pinch – Squeezes the metal to a smaller section
- Edge – Creates a bend at the edge of the profile
- Fin – For making small bends inward or outward
- Rigid – General support rolls for holding shape
The roll pass design is first developed by analysis of the part shape. Roll geometry is iteratively refined to achieve the required bending increments and minimum stress forming. Roll materials are selected based on the stock properties and production volumes. Common materials include hardened steel, iron, and rubber/polyurethane for high volumes.
Design Considerations
Some key considerations in profile roll forming design:
- Part tolerances – Roll design must account for springback and meet tolerance specs
- Strip properties – Yield strength, hardness and thickness influence roll loads
- Production rate – Line speed impacts roll load capacity and motor sizing
- Strip width – Max width depends on machine capacity and part geometry
- Material type – Roll materials selected based on hardness of stock metal
- Lubrication – Friction reduction allows better material flow in forming
- Grain orientation – Roll design must consider sheet metal grain direction
Thorough roll pass development and FEA analysis is carried out to optimize the roll tooling design before manufacturing. Pilot production runs help verify the tooling before full production.
profile roll forming machine Process
The profile roll forming process produces parts by bending and shaping sheet or coil stock longitudinally as it moves through consecutive pairs of contoured rolls. Each stand of rolls makes a series of precise bends until the final cross-section profile is formed incrementally.
How Roll Forming Works
- Sheet or coil material is loaded into a de-coiler which feeds the strip through a straightener into the roll former.
- The feed rolls grip the stock and move it forward through the roll forming stations.
- As the strip engages the first stand, initial shaping of the profile occurs.
- At each subsequent stand, incremental bends are made until the final shape is attained.
- The profiled section exits the last station and is cut to desired lengths.
- Formed parts are collected on a take-off table.
The key advantage of roll forming is the gradual bending of stock through a series of small increments. The bending sequence and roll design allows material flow without excessive thinning or tearing. The process exerts precise control over stock deformation to create the required cross-section.
Correct roll pass design is crucial for successfully shaping parts within tolerance limits. Roll forming relies on compression alone to bend the stock. No tensile forces are applied during forming. The rolls only squeeze and press the strip longitudinally as it moves through the machine.
Roll Forming Steps
Here are the sequence of steps in profile roll forming process:
1. Feeding
- Sheet or coil stock loaded into a de-coiler or feed unit
- Automatic feed rolls with pinch rolls grip and feed the strip
- Sheet straightener removes coil curvature and initial bends
**2. Incremental Bending **
- Stock enters first roll stand and initial bends are made
- At each subsequent stand, bending progresses further
- Rolls are precision machined to required contours
- Final profile shape achieved gradually over repeating stands
3. Cutting
- Formed profile section automatically fed to cutting station
- Shearing dies or saws cut parts to specified length
- Common cut lengths range from 3 ft to 16 ft
4. Collection
- Cut parts are stacked on take-off tables or conveyors
- Tables allow sections to be conveniently bundled and transported
5. Finishing
- Optional – end finishing, hole punching, markings etc.
- Automated operations possible for high volumes
Roll Forming Benefits
Roll forming provides important benefits:
- High production rates up to 200 ft/min possible
- Consistent and repetitive shaping of profiles
- Low forces involved so less wear on tooling
- Allows unlimited part lengths
- Minimal material waste as stock is formed progressively
- Lower cost than stamping or press braking for long runs
- Wide range of shapes and geometries can be produced
- Ideal for high-strength materials like HSLA steel
- Common for high volumes of 50,000 to 500,000 pieces
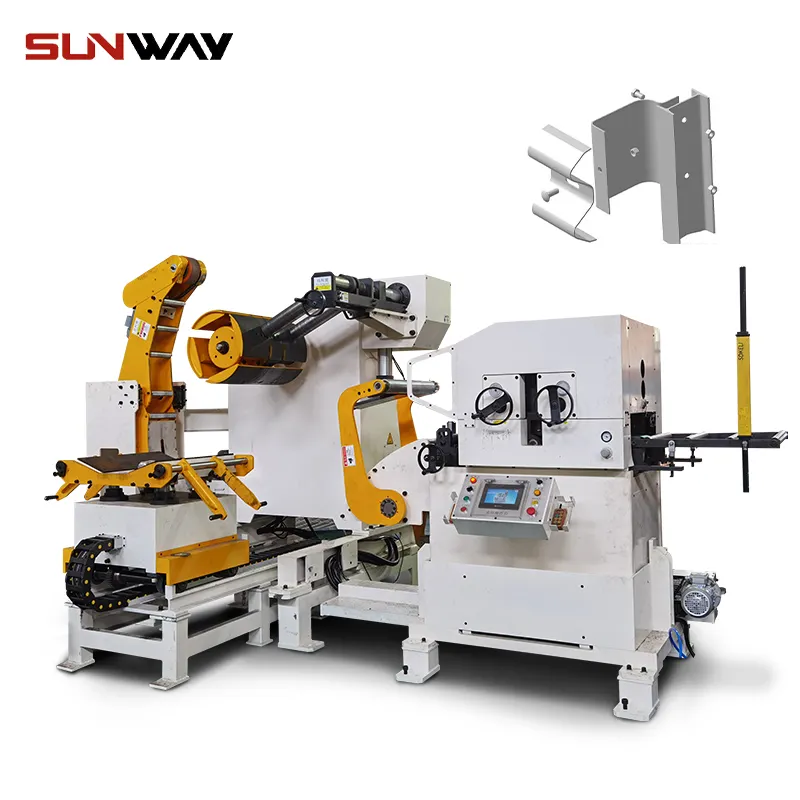
Profile Roll Forming Machines
Profile roll forming machines are custom engineered systems designed to produce metal parts with a specified cross-sectional shape. Key aspects of roll formers include:
Feed System
- De-coiler or uncoiler for sheet or coil stock
- Feed roll stands with pinch rolls
- Sheet straightener and thickness gauges
- Stock guides and support rolls
Forming Stations
- Series of roll forming stands
- Top and bottom roll shafts with geared couplings
- Interlocked roll housings for rigidity
- Roll contour and geometry customized for part shape
Cut-Off System
- Shearing die, circular saw or razor for cut-offs
- Post-cut tables or exit conveyors
- Bundling systems for handling finished parts
Machine Frame
- Heavy welded steel base frame
- Side walls for roll enclosures and safety
- Guards around moving parts
Drives
- Main motor coupled to input shaft
- Gear reducers for each roll stand
- Servo feeds for de-coiler and cut-off
- Sensors for automation and control
Roll Former Configurations
There are three common types of profile roll forming machine configurations:
In-line
- Sections are formed and cut longitudinally
- Each piece has consistent profile along length
- Common for parts up to 25 ft long
- High production rates up to 200 ft/min
Rotary
- Strip is fed into circular roll sets
- Rotation forms profile around mandrel
- Used for making rings and rounded shapes
- Lower production rates than in-line
Wheel Machines
- Roll dies mounted on rotating circular wheels
- Wheels spin to form bends and shapes
- Portable and adjustable for short runs
- Production up to 60 ft/min
In-line roll formers are the predominant type used in industrial plants because of their continuous high production capability.
Roll Former Sizes
Profile roll forming machines are available in a wide range of sizes:
Machine Rating | Forming Width | Strip Thickness |
---|---|---|
Light-duty | Up to 18 in | 26 – 16 gauge |
Intermediate | Up to 24 in | 16 – 10 gauge |
Standard | Up to 72 in | 10 – 3 gauge |
Heavy-duty | Up to 120 in | 3 gauge – 1/4 in |
- Small roll formers are used for short production runs.
- Medium capacity machines used for typical fabrication shop work.
- Large roll formers for high volumes in major plants.
Key factors determining machine size:
- Maximum strip width needed
- Thickness range of metals used
- Complexity of part shapes
- Production volumes and rates
- Overall length of profiles
Roll Forming Design
Design of the roll forming process requires thorough engineering analysis. The objective is to determine the optimal roll pass sequences and tooling design to produce the desired part shape.
Roll Pass Design
The roll pass design defines the precise bending sequence at each station along the machine:
- First step is to determine the order of bends required to form the profile.
- The total bend angle is divided into increments spread over the roll stands.
- Roll contours and positions are analyzed to achieve the bending angles.
- Several iterations made to optimize the roll pass schedule.
- Analysis done using software tools like CAD, FEA, roll design programs.
- Pilot runs conducted to verify tooling before full production.
The total number of roll stands is decided based on:
- Complexity of finished profile shape
- Metal properties – thickness, yield strength
- Tolerances required on part dimensions
- Maximum angle to be formed at each station
Correct roll pass design is key to quality roll formed parts. It prevents defects like buckling, splitting and springback in the formed sections.
Roll Design
Roll tooling design requires:
- Determining roll contours to match part geometry
- Analysis of progressive bending steps and deduced roll shape
- Material selection for rolls based on forces and wear
- Shaft design with proper diameters and bearings
- Proper roll geometries to avoid issues like twisting or distortion
- FEA analysis to optimize roll shapes and loading
- Pilot production runs to verify tooling performance
Rolls are usually machined from materials like D2 tool steel, iron or rubber/polyurethane. Typical roll diameters range from 5” to 8”. Rolls have a crowned contour to compensate for deflections. Proper roll alignment and housing rigidity are critical for quality parts.
Roll Forming Analysis
Engineering analysis in roll design involves:
- Part CAD Models – Creating 3D models of finished profile shape
- Bending Analysis – Determining sequence of bends and roll angles
- FEA Modeling – Simulating rolling forces and material stresses
- Roll Design – CAD modeling of contours based on bend deductions
- Machine Design – Sizing motors, shafts, and couplings based on loads
- Deflection – Analyzing roll stacks, shafts and housing deformations
- Tool Path – Simulating strip movement through roll sequence
Such analysis ensures the roll tooling produces the required part shape and tolerances. It also prevents defects such as buckling, cracking or springback of the formed sections.
Roll Materials
Selection of suitable roll materials is important for quality profile forming and long tooling life. Key factors in roll material choice:
Hardness
- Roll hardness must be greater than stock hardness
- Prevents roll deformation under pressure
- Hardened steel rolls used for most metals
Strength
- Rolls must withstand bending forces without fatigue
- High strength needed to support forming loads
- Strength determines permissible roll diameters
Wear Resistance
- Roll materials must resist damage from friction
- Critical for high production volumes
- Special alloys used if stock is abrasive
Work Hardening
- Contact pressure must not excessively work harden rolls
- Leads to surface damage and poor part quality
- Low friction coatings help overcome this
Material | Description | Applications |
---|---|---|
Hardened Steel | Medium carbon steel, heat treated | Most common, used for majority of metals |
Adamite | Centrifugally cast high nickel iron | High production carbon & HSLA steels |
Rubber/Polyurethane | High durometer urethane or rubber rolls | Sensitive metals like copper, brass, aluminum |
Iron | Ductile iron, various hardness | Pre-forming rolls, low hardness metals |
Combinations of materials are also used on a single machine, with pre-forming stands made of iron and finishing stands utilizing steel. Rubber/urethane rolls help when forming soft metals by reducing friction.
Proper roll material selection ensures low wear rates and ability to withstand the high pressures involved in roll forming. It results in maximum production volumes and minimizes roll re-grinding or replacement.
Roll Forming Applications
Profile roll forming is used to produce a wide variety of parts across industries:
Construction
- Wall panels, siding, roofing, studs, joists
- Railings, frames, solar mounts, drainage systems
- Angle, tube, channels for structures
**Automotive **
- Door beams, roof rails, brackets, cross members
- Seat frames, running boards, bumpers
- Exterior trim components
**HVAC **
- Air ducts and fittings
- Gutters, louvers, registers, diffusers
Material Handling
- Rack frames, shelving, conveyors
- Carts, bins, lockers, storage cabinets
Furniture
- Frames, enclosures, shelves, handles
- Desks, file cabinets, shop fittings
Electrical
- Lighting fixtures, cable trays, junction boxes
- Panel enclosures, raceways, Solar PV frames
Transportation
- Hitches, railings, steps, frames for trucks and trailers
- Highway safety barriers
In addition, decorative architectural profiles, displays, exhibits, signage, rail car and truck body panels are commonly roll formed.
The flexibility to create unlimited open cross-sections makes roll forming ideal for producing both standardized as well as custom parts.
Comparing Roll Forming With Other Processes
Profile roll forming has both advantages and limitations compared to other metal forming processes:
Versus Press Brake Bending
- Lower equipment cost than large press brakes
- No tooling costs for bend dies
- Higher throughput rates
- Limited to open profiles, press brakes can do closed shapes
- Size limited in roll forming by machine capacity
- Press brakes faster changeover between parts
- Press brakes can have thicker material limits
Versus Stamping
- Much lower tooling costs compared to stamping dies
- Small lot sizes feasible versus stamping optimized for high volumes
- Higher material utilization in roll forming
- More size limitations in stamping
- Stamping can produce closed-section forms not possible in roll forming
- Higher initial equipment cost for roll forming
Versus Extrusion
- Low cost tooling gives roll forming flexibility to change parts
- Extrusion only produces a fixed cross-section in continuous lengths
- Roll forming has width limits based on machine capacity
- Extrusion not practical for short production runs
Versus Laser/Waterjet Cutting
- No heat affected zone or warping as in laser cutting
- Low material waste compared to shearing scrap loss
- Able to flexibly produce custom closed shapes unlike roll forming
- Very short lead times possible with cutting versus roll tooling prep
- No shape or thickness limitations like in roll forming
Considering both advantages and limitations helps determine optimal process selection for a production application. Roll forming provides benefits for long production runs given the high initial machine cost.
Roll Forming Defects
Some potential defects that can occur in profile roll forming:
Buckling
- Rippling or wrinkling along web or flange
- Due to excessive compression
- Inadequate width-to-thickness ratio
- Increase hold-down pressure
Twisting
- Finished profile twists longitudinally
- Rolls not properly aligned
- Improper spacing between roll stands
- Adjust roll alignment
Foldover
- Formed flange folds onto web
- Excessive compression
- Increase bottom roll diameter
Surface Markings
- Roller imprints visible on surfaces
- Excessive roll pressure
- Install
Splitting
- Cracks along neutral axis of formed profile
- Metal exceeds ductility limits in forming
- Increase radius in bend deduction
- Adjust roll pass schedule
Flaring
- Formed flanges spread outward
- Insufficient roll containment
- Misaligned top and bottom rolls
- Adjust roll alignment
Non-Fill
- Web does not contact bottom roll
- Preventing complete forming
- Worn or damaged rolls
- Increase roll diameter
Springback
- Part shape not maintained after exiting last stand
- Elastic recovery of metal
- Over-bending and over-forming can compensate
Thickness Variation
- Inconsistent material thickness along part
- Improper relation between rolls
- Increase bottom roll diameter
Surface Damage
- Dents, gouges, scratches on formed areas
- Debris buildup on rolls causing marks
- Lubricate material or rolls
- Clean roll surfaces
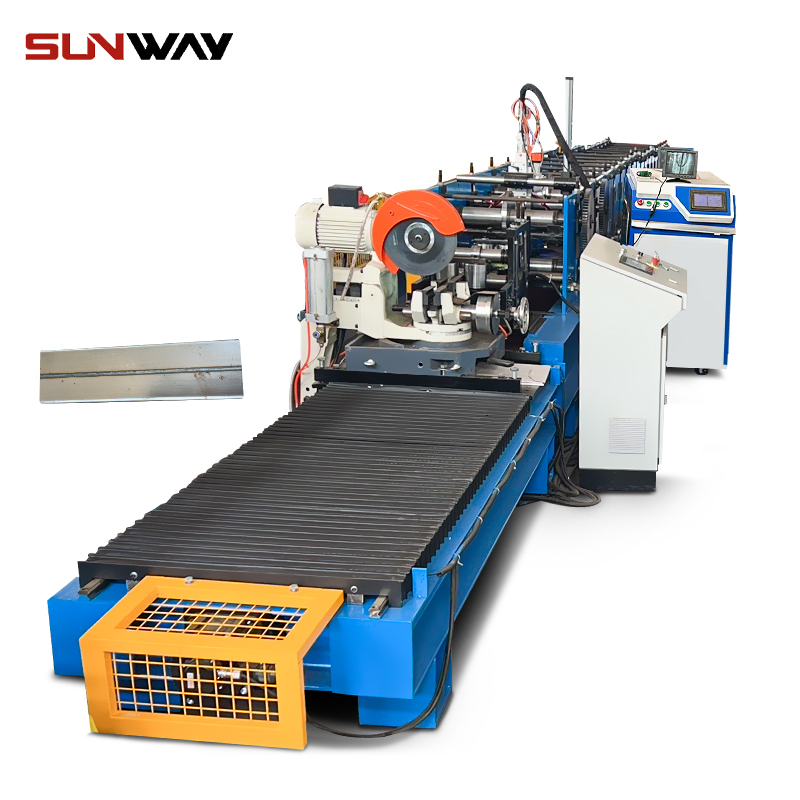
Lubrication in Roll Forming
Lubrication is critical in profile roll forming to:
- Reduce friction between the rolls and sheet metal
- Allow easier bending and material flow
- Prevent surface damage to the formed profiles
Benefits of effective lubrication:
- Lower forming loads on the rolls and tooling
- Avoid galling and transfer of material to rolls
- Enable higher line speeds and production rates
- Improve surface quality of finished parts
- Reduce roll wear to maximize service life
Common lubrication methods:
Roll Lubrication
- Direct lubricant applied to roll surfaces
- Drip systems to keep rolls coated
- Reduces friction as sheet engages rolls
Stock Lubrication
- Sheet or coil coated before de-coiler
- Correct amount applied for full production run
- Consistent lubrication through all stands
Mist Spray
- Air mist lubrication sprayed on surfaces
- Low quantity evenly distributed
- Clean application with no excess buildup
Environments
- Systems to spray oil or coolant internally
- Help provide cleaner shop air quality
Synthetic lubricants are commonly used for roll forming instead of oil-based products. They offer clean operation, long life and minimal mess to handle formed parts. Proper recycling systems can extend the service life of synthetic lubricants in roll forming.
Secondary Operations
Secondary operations are often performed on roll formed parts:
Cutting
- Shearing or sawing to final finished lengths
- Hole punching for fasteners or hangers
- Notching and slotting to fit other components
- Trim and edge deburring for cosmetics
Bending
- End tabs, flanges, brackets added with press brakes
- Formed interlocks and pockets for connections
- Hems and seams for panel joins
Finishing
- Painting and powder coating for appearance and protection
- Hot dip galvanizing or plating for corrosion resistance
- Priming and passivation for metals like stainless steel
Hardware
- Addition of embedded nuts, studs, captive fasteners
- Mounting clips, brackets and clips installed
Assembly
- Joining roll formed sections to panels or frames
- Integration of insulation, glass, electronics, lighting
- Welding and fastening additional components
Such secondary processes help create finished parts or sub-assemblies from the roll formed profiles. Automation allows integrating multiple operations in a continuous production line.
Roll Forming Equipment Suppliers
Some leading manufacturers of profile roll forming equipment include:
- Samco Machinery – Complete range of roll formers for production and prototyping applications
- Metform International – Roll forming machines for a wide range of industries
- Dahlstrom Motors – Custom roll former engineering and manufacturing
- Formtek – Roll formers for HVAC, drainage, panels, racking, automotive
- Bradbury Group – Leading supplier of flat sheet and coil processing equipment
- Shibo Mechanical Engineering – Taiwanese manufacturer of roll forming machines
- Comet Machinery – Production roll formers and portable wheel machines
- KNUTH – German engineered roll forming machines and tools
- Botou Xianfa – Roll forming equipment manufacturer from China
- EZForm – Canadian based leading roll forming machine producer
When selecting roll forming equipment, important factors to consider include:
- Forming width and thickness capacity required
- Overall machine length based on part dimensions
- Number of roll stands needed for profile shape
- Production rates and volumes
- Controls, automation, ease of setup
- Availability of roll design services
- Experience with similar applications
- Global presence for service and support
Leading roll former manufacturers provide complete design assistance and roll tooling services in addition to the forming equipment.
Roll Forming Costs
The economics of profile roll forming:
Machine Cost
- $50,000 to $500,000+ depending on size and features
- Larger, automated machines with more capabilities cost more
Tooling Cost
- $2,000 to $20,000+ per tooling set
- More roll stands and complexity increases cost
**Operation Cost **
- Labor 1-2 operators typically for loading/offloading
- Low maintenance and tooling replacement costs
- Energy consumption ~50-100 kWh per ton of production
Production Rates
- Up to 200 ft/min line speed on high speed machines
- 10,000 to 100,000+ ft per shift possible
Payback Period
- ~1-3 years after break even quantity
- Significant for large production volumes
- Long lifespan of machines – over 20 years
Cost Per Piece
- $0.10 to $2 per piece depending on complexity
- Economics improve with higher volumes due to low running costs
Roll forming becomes economical for large production lots – typically over 50,000 pieces. For lower quantities, other processes like laser cutting or press brakes may be more cost effective. The flexibility of roll forming allows producing both low and high volumes on the same machine.
Roll Forming Process Control
Effective process control ensures high quality and productivity in roll forming:
Line Speed
- Production rate and throughput directly tied to line speed
- Speed optimized to balance throughput versus quality
Roll Pressure
- Adequate pressure needed for good forming
- Excess pressure causes defects and roll wear
- Force sensors help optimize pressure
Strip Tension
- Sufficient tension needed for smooth feeding
- Minimizes buckling and helps material flow
- Load cells on strip monitor tension
Roll Wear
- Worn rolls cause marking and dimensional errors
- Online roll measurement systems detect wear
- Rolls replaced based on indicators
Lubrication
- Adequate lubrication prevents scratching
- Sensors verify proper lubricant levels
- Pumps modulate flow based on line speed
Automation
- Programmable controllers coordinate machines
- HMI displays and interfaces for control
- Diagnostics monitor process health
Modern roll formers employ comprehensive monitoring and networked controls to automatically maintain optimal forming conditions. This prevents rejects, enables maximum production rates, and reduces downtime.
Common Problems in Roll Forming
Some frequent issues faced in profile roll forming and how to address them:
Problem: Twisting of formed profile
Solution: Ensure proper roll alignment; Increase distance between roll stands; Check roll parallelism
Problem: Profile distortion after exiting last stand
Solution: Increase bottom roll diameter; Employ roller supports for finished profile
Problem: Flange flipping over during forming
Solution: Reduce compression; Increase flange width; Check roll contours
Problem: Web not contacting bottom roll
Solution: Increase bottom roll diameter; Adjust roll pass schedule
Problem: Excessive load on gearboxes and tooling
Solution: Lubricate material; Reduce line speed; Check roll alignment
Problem: Roller marks visible on formed surface
Solution: Replace damaged rolls; Increase lubrication; Reduce roll pressure
Problem: Splitting along web and flange junctions
Solution: Increase bend radii; Use more pre-forming stands; Check material ductility
Problem: Poor profile tolerances
Solution: Account for springback in roll design; Use over-bending
Problem: Scratches on formed parts
Solution: Clean roll surfaces; Improve lubrication; Check stock surface quality
Roll Forming Safety
Safety practices for roll forming operations:
- Enclose roll stands within protective guards
- Interlocked access doors that shut down machine if opened
- Prominently label emergency stop buttons
- Sensors to halt operation if a body part is detected
- Lockout/tagout procedures for maintenance
- Use brushes or funnels for lubricant instead of direct handling
- Equipment for safe lifting and handling of heavy tooling
- Workers wear proper PPE – safety glasses, gloves, non-loose clothing
- Adequate ventilation to control oil mist and fumes
- Isolation of high noise areas with sound enclosures
- Regular inspections of tooling, guards, sensors, interlocks
- Training on safe operating procedures and precautions
- Establish safety zones and restrict access near the machine
Roll forming involves significant hazards from rotating parts, high pressures and sharp edges. Following comprehensive safety practices is critical for preventing injuries. Machine safeguarding, lockout procedures, worker training and PPE use should all be enforced.
Roll Forming Quality Control
Quality control practices in roll forming:
- First piece inspection of formed profile
- Dimensional checks with gauges and CMM
- Monitoring thickness variation along part length
- Surface finish inspection of formed areas
- Visual examination for defects
- Monitoring correct lubrication amounts
- Measurement of web, flange widths and bend angles
- Verifying cut lengths and hole punch quality
- Checking for twist, bow and flatness
- Test runs to validate new tooling and process changes
- Statistical process control tracking of defects
- Capability analysis of critical dimensions
- Documentation of process parameters and tolerances
- Training operators on inspection procedures
- Corrective actions when defects occur
With adequate quality control measures, the repeatability of the roll forming process ensures consistently produced parts within required tolerances. Statistical tracking helps identify areas for improvement.
Roll Forming Process Troubleshooting
Troubleshooting techniques when problems occur in roll forming:
- Stop machine and inspect formed section carefully first
- Review recent process changes or adjustments
- Check roll wear, lubrication amounts, strip alignment
- Verify stock material properties and condition
- Try reducing line speed incrementally
- Adjust individual roll stand pressures and alignment
- Study roll pass design and tooling setup
- Review operator training and adherence to procedures
- Analyze root cause of specific defect observed
- Pilot run small batches to systematically isolate issue
- Inspect and measure formed profile in multiple locations
- Iterate tooling only for chronic issues after other remedies exhausted
- Consult roll design experts for troubleshooting difficult forming problems
- Consider material testing if defects traced to composition
- Document all findings and corrective actions taken
Careful troubleshooting helps identify the factors contributing to a roll forming issue. A narrow focus on tooling should come only after considering other potential sources related to material, methods, man or machine.
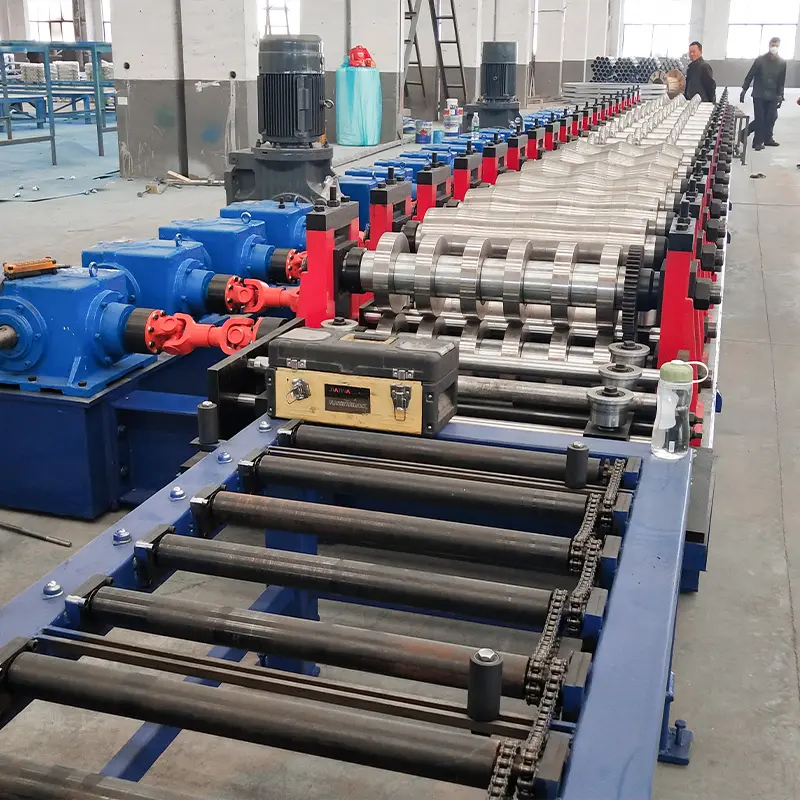
Roll Forming Industry Standards
Roll forming standards guide equipment specifications, design and quality control:
ASTM A924 – Standard for steel sheet metals used in roll forming
ASTM B136 – Standard for brass strip materials for roll forming
AISI D100 – Roll forming guidelines and tolerances
AWS D1.3 – Welding guidelines for roll formed parts and machines
NSSGA – Roll forming guide for aggregate industry products
AISI SG03-3 – Guidelines for cold-formed steel framing
ASTM E290 – Test methods for bend testing of roll formed parts
ISO 11562 – Linear measures of roll formed parts
JIS Z1701 – Testing methods for roll formed products
API Spec 5CT – Specification for casing and tubing
SAE J136 – Lubricant test methods
Adhering to industry standards ensures roll formed parts meet the required specifications across parameters like materials, design, dimensions, testing and joining.
FAQ
Q: What metals can be roll formed?
A: Roll forming can form steels, stainless steels, aluminum, copper, brass and other ductile metals within the machine’s thickness and width limits.
Q: What thickness range can be roll formed?
A: Typical thickness range is 18 ga to 1/4 in. Larger machines can roll form up to 1 in thick material. Minimum thickness around 26 ga to 30 ga.
Q: What tolerances are achievable?
A: Roll formed parts typically hold tolerances of +/- 1% of material thickness. Certain dimensions can be held to closer tolerances.
Q: How long can a single roll formed piece be?
A: Production lengths range from 2 ft up to 25 ft long sections, depending on machine size. Unlimited lengths possible in theory.
Q: What metals require lubrication?
A: Lubrication recommended for most metals except stainless steel. Especially useful for brass, copper and aluminum.
Q: Does grain direction affect roll forming?
A: Yes, bending is easier transverse to grain direction. Profiles are usually roll formed parallel to original grain orientation.
Q: How many operators are required?
A: Typically 1-2 operators – one at the uncoiler and one at the exit end. Automated machines may not need an operator.
Q: How quick are changeovers between profiles?
A: Roll and tooling changes can take 4-8 hours. Some quick change tooling reduces this time substantially.
Q: What determines profile tolerances?
A: Tolerances depend on material properties, tooling rigidity, number of roll stands, lubrication and line speed.
Q: What limits the maximum width?
A: Machine frame size, roll stand rigidity, and forming power restrict max width. Up to 120 in on largest machines.
Q: How complex of shapes can be formed?
A: Roll forming excels at high production of open uniform shapes. Press brakes better for short runs of complex profiles.
Q: What causes scratches on the formed surface?
A: Debris buildup on work or tooling, poor lubrication, damaged tooling, improper roll pressures.
Q: Why is springback a problem?
A: Elastic recovery after bending causes shape distortion. Overbending and bottom roll support can compensate.
Q: How are holes and notches added?
A: Punching, nibbling or laser cutting are used after roll forming to create holes and shaped cutouts as needed.
Q: Why is roll forming more economical than other methods?
A: No dies needed and low operating costs. Setup cost amortized over long production runs. High material utilization.