Обзор профилегибочного станка
профилегибочная машина представляет собой непрерывную операцию гибки, при которой листовой или рулонный материал постепенно формируется в требуемую форму поперечного сечения через ряд последовательных формовочных станций. Станции формовки состоят из противоположных валков, которые непрерывно изгибают и придают форму движущейся полосе материала до получения конечного профиля.
Профильная прокатка позволяет эффективно и с минимальными затратами производить металлические детали нестандартного сечения. Она обычно используется для производства таких деталей, как стеновые панели, кровля, дверные коробки, стеллажные системы, дорожные изделия, элементы мебели и многое другое. Гибкость роликовой прокатки позволяет создавать практически любые профили открытого сечения.
Среди основных преимуществ профильной прокатки можно назвать следующие:
- Высокоавтоматизированный процесс с низкими трудозатратами
- Способны обеспечить высокие темпы и объемы производства
- Последовательное и повторяющееся формирование профилей
- Возможно формирование широкого спектра форм и размеров
- Низкие затраты на оснастку по сравнению с другими процессами
- Минимальные отходы материала, так как запасы формируются постепенно
- Применяется для различных металлов, таких как сталь, алюминий, латунь и т.д.
Рулонная штамповка требует больших первоначальных инвестиций в оборудование по сравнению с такими методами, как прессование или штамповка. Однако, благодаря высокой производительности и низким эксплуатационным расходам, профильная роликовая штамповка становится экономически выгодной для крупных партий продукции. Она идеально подходит для производства длинных профилей повторяющегося сечения.
Процесс прокатки профиля
Процесс прокатки профиля состоит из нескольких этапов:
- Рулоны или листы загружаются в разматыватель или устройство подачи, которое выпрямляет полосу.
- Материал подается в продольном направлении через ряд прокатных станций.
- Каждый валок выполняет серию изгибов, пока не будет сформирована желаемая форма профиля.
- Отрезные штампы производят заготовки необходимой длины по мере выхода профиля из вальцовочного станка.
- Сформированные секции собираются на столе для снятия.
Постепенное изгибание заготовки через последовательные клети является ключевым моментом в процессе валковой формовки. Количество необходимых клетей зависит от сложности формы формируемой детали. Обычно машины имеют от 3 до 16 формовочных станций.
Компоненты валковой формовочной машины
Профилегибочные станки состоят из трех основных секций:
- Кормление запасов - Разматыватель, правильная машина и устройство подачи
- Формирование - Последовательные валковые стенды для постепенной гибки листа
- Резка - Ножницы или пилы для резки профилей по длине
Вот основные компоненты валкообразователя:
Машинная секция | Компоненты |
---|---|
Кормление скота | Удержание рулона, размотка рулона, подающие валки, направляющие для запасов, прижимные валки, листоправильная машина |
Формирование | Корпус валков, верхние и нижние валки, редукторы, валы |
Резка | Отрезной пресс, ножницы с летучим штампом, концевые дробилки |
Управление | ПЛК, ЧМИ, линейные устройства управления |
Другой | Ограждения, рама основания, двигатели, гидравлика |
Ролл-дизайн
Валковая оснастка играет центральную роль в создании желаемой формы профиля. Валковая формовка зависит от точного изгиба валков с контурами для постепенного формирования профилей. Конструкция валков разрабатывается индивидуально для получения точной геометрии изготавливаемой детали.
Вот некоторые распространенные варианты исполнения валов:
- Формирование круга - Используется для формирования криволинейных форм и радиусов
- Pinch - Сжимает металл до меньшего размера
- Край - Создает изгиб на краю профиля
- Фин - Для создания небольших изгибов внутрь или наружу
- Жесткий - Валики для поддержания формы
Конструкция прохода валков сначала разрабатывается на основе анализа формы детали. Геометрия валков итерационно уточняется для достижения требуемых приращений изгиба и минимального напряжения при формовании. Материалы валков выбираются в зависимости от свойств заготовки и объемов производства. Обычные материалы включают закаленную сталь, железо и резину/полиуретан для больших объемов.
Конструктивные соображения
Некоторые ключевые моменты при проектировании профильной прокатки:
- Допуски деталей - Конструкция валков должна учитывать пружинящий изгиб и соответствовать спецификациям допусков
- Свойства полос - Предел текучести, твердость и толщина влияют на нагрузку на валки
- Уровень производства - Скорость линии влияет на грузоподъемность валов и размер двигателя
- Ширина полосы - Максимальная ширина зависит от производительности станка и геометрии детали
- Тип материала - Материалы валков выбираются в зависимости от твердости исходного металла
- Смазка - Уменьшение трения обеспечивает лучшую подачу материала при формовании
- Ориентация зерен - При проектировании валков необходимо учитывать направление зерна листового металла
Для оптимизации конструкции валковой оснастки перед производством проводится тщательная разработка проходов валков и анализ FEA. Экспериментальное производство помогает проверить оснастку перед полным производством.
профилегибочная машина Процесс
Процесс профильной прокатки производит детали путем изгиба и придания продольной формы листовому или рулонному материалу при прохождении его через последовательные пары контурных валков. Каждая пара валков выполняет серию точных изгибов до тех пор, пока не будет сформирован окончательный профиль поперечного сечения.
Как работает роликовая формовка
- Листовой или рулонный материал загружается в разматыватель, который подает полосу через правильную машину в валковый пресс.
- Подающие валки захватывают материал и перемещают его вперед через валковые формовочные станции.
- Когда полоса попадает на первый стенд, происходит начальное формирование профиля.
- На каждой последующей стойке делаются дополнительные изгибы, пока не будет достигнута окончательная форма.
- Профилированный профиль выходит с последней станции и разрезается на отрезки нужной длины.
- Сформированные детали собираются на столе для снятия.
Ключевым преимуществом валковой формовки является постепенное сгибание заготовки через серию небольших приемов. Последовательность гибки и конструкция валков обеспечивают подачу материала без чрезмерного утонения или разрыва. Процесс обеспечивает точный контроль над деформацией заготовки для создания требуемого сечения.
Правильная конструкция прохода валков имеет решающее значение для успешного формования деталей в пределах допусков. Для изгибания заготовки валковая формовка опирается только на сжатие. Во время формовки не прикладываются растягивающие усилия. Валки только сжимают и давят на полосу в продольном направлении по мере ее прохождения через машину.
Этапы формовки рулонов
Вот последовательность этапов процесса прокатки профиля:
1. Кормление
- Листовой или рулонный материал, загружаемый в разматыватель или устройство подачи
- Автоматические подающие валики с прижимными роликами захватывают и подают ленту
- Листоправильная машина устраняет кривизну рулона и начальные изгибы
**2. Инкрементный изгиб **
- Заготовка поступает на первый валковый стенд и производится первоначальная гибка
- На каждой последующей стойке изгиб прогрессирует дальше
- Валки обрабатываются с высокой точностью по требуемым контурам
- Окончательная форма профиля достигается постепенно при многократном повторении стендов
3. Резка
- Сформированный профиль автоматически подается на станцию резки
- Ножницы или пилы разрезают детали на части заданной длины
- Обычная длина отрезков составляет от 3 до 16 футов
4. Коллекция
- Вырезанные детали укладываются на столы для снятия или конвейеры
- Столы позволяют удобно складывать и перевозить секции
5. Отделка
- Дополнительно - отделка торцов, пробивка отверстий, маркировка и т.д.
- Автоматизированные операции при больших объемах
Преимущества роликовой формовки
Рулонная формовка обеспечивает важные преимущества:
- Возможна высокая производительность до 200 футов в минуту
- Последовательное и повторяющееся формирование профилей
- Малые усилия, поэтому меньший износ инструмента
- Позволяет использовать детали неограниченной длины
- Минимальные отходы материала, так как запасы формируются постепенно
- Более низкая стоимость по сравнению со штамповкой или листогибочным прессом при больших объемах производства
- Возможно изготовление широкого спектра форм и геометрий
- Идеально подходит для высокопрочных материалов, таких как сталь HSLA
- Обычно для больших объемов от 50 000 до 500 000 штук
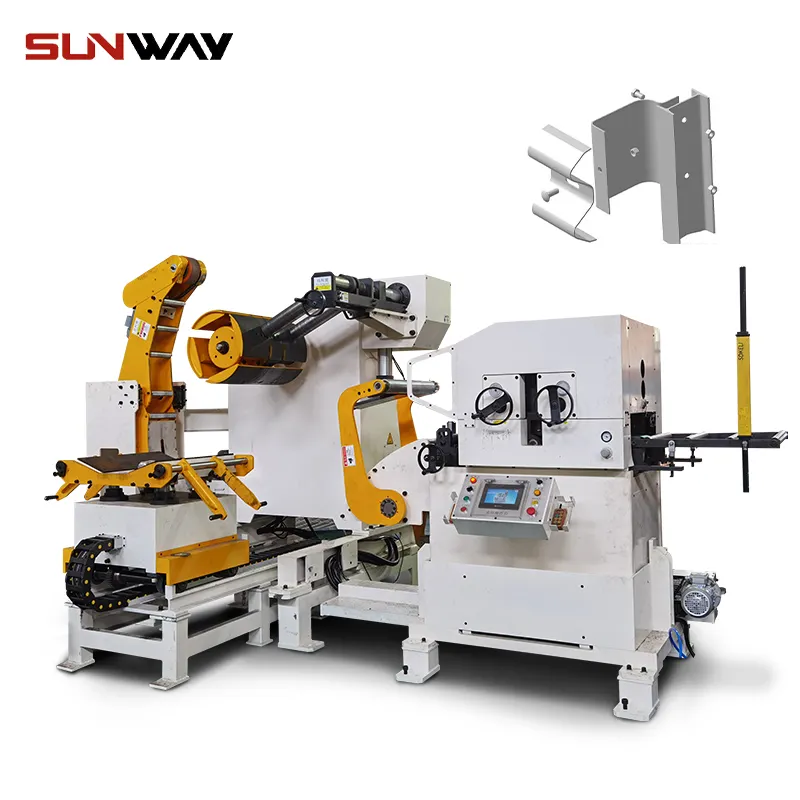
Профилегибочные станки
Профилегибочные машины Это специализированные системы, предназначенные для производства металлических деталей с заданной формой поперечного сечения. Ключевые аспекты валковых формовщиков включают:
Система подачи
- Разматыватель или разматыватель для листового или рулонного материала
- Стойки для подающих валков с прижимными валками
- Листоправильные машины и толщиномеры
- Направляющие и опорные валики
Станции формовки
- Серия клетей для прокатки
- Верхний и нижний валы с зубчатыми муфтами
- Взаимосвязанные корпуса валов обеспечивают жесткость
- Контур и геометрия валков подстраиваются под форму детали
Система отключения
- Ножницы, циркулярная пила или бритва для обрезков
- Столы для последующей резки или выходные конвейеры
- Системы пакетирования для обработки готовых деталей
Рама машины
- Прочная стальная сварная рама основания
- Боковые стенки для ограждения рулонов и обеспечения безопасности
- Ограждения вокруг движущихся частей
Приводы
- Главный двигатель, соединенный с входным валом
- Редукторы для каждой клети
- Сервоподача для разматывания и отрезания
- Датчики для автоматизации и управления
Конфигурации валковых формирователей
Существует три распространенных типа конфигураций профилегибочных машин:
В линию
- Секции формируются и разрезаются в продольном направлении
- Каждая деталь имеет одинаковый профиль по всей длине
- Обычно для деталей длиной до 25 футов
- Высокая производительность до 200 футов в минуту
Роторный
- Лента подается в комплекты круглых валков
- Вращение формирует профиль вокруг оправки
- Используется для изготовления колец и округлых форм
- Более низкая производительность по сравнению с поточной
Колесные машины
- Валковые штампы, установленные на вращающихся круговых колесах
- Колеса вращаются, образуя изгибы и формы
- Портативный и регулируемый для коротких пробежек
- Производительность до 60 футов в минуту
Поточные валковые формовочные машины являются преобладающим типом, используемым на промышленных предприятиях, благодаря их непрерывной высокой производительности.
Размеры формирователя рулонов
Профилегибочные станки выпускаются в широком диапазоне размеров:
Рейтинг машин | Ширина формовки | Толщина полосы |
---|---|---|
Легкие | До 18 дюймов | 26 - 16 калибр |
Промежуточный | До 24 дюймов | 16 - 10 калибр |
Стандарт | До 72 дюймов | 10 - 3 калибр |
Сверхмощный | До 120 дюймов | 3 калибр - 1/4 дюйма |
- Небольшие валковые формовочные машины используются для изготовления коротких партий продукции.
- Станки средней мощности, используемые для типичных работ в производственных цехах.
- Большие валковые формовочные машины для больших объемов производства на крупных заводах.
Ключевые факторы, определяющие размер машины:
- Необходимая максимальная ширина полосы
- Диапазон толщины используемых металлов
- Сложность форм деталей
- Объемы и темпы производства
- Общая длина профилей
Конструкция роликовой формовки
Проектирование процесса валковой формовки требует тщательного инженерного анализа. Цель состоит в определении оптимальной последовательности проходов валков и конструкции инструмента для получения детали требуемой формы.
Конструкция роликового прохода
Конструкция прохода валков определяет точную последовательность гибки на каждом участке станка:
- Сначала нужно определить порядок сгибов, необходимых для формирования профиля.
- Общий угол изгиба делится на приращения, распределенные по клети вала.
- Для достижения углов изгиба анализируются контуры и положения валков.
- Несколько итераций для оптимизации графика прохода валков.
- Анализ выполняется с помощью программных средств, таких как CAD, FEA, программы проектирования валов.
- Опытные партии проводятся для проверки оснастки перед полным производством.
Общее количество ролл-стендов определяется на основе:
- Сложность формы готового профиля
- Свойства металла - толщина, предел текучести
- Необходимые допуски на размеры деталей
- Максимальный угол, образуемый на каждой станции
Правильная конструкция прохода валков является ключевым фактором для получения качественных деталей. Она предотвращает такие дефекты, как смятие, раскалывание и пружинящая спинка в формованных секциях.
Дизайн рулона
Для проектирования валковой оснастки требуется:
- Определение контуров валков для соответствия геометрии детали
- Анализ ступеней прогрессивного изгиба и полученной формы валков
- Выбор материала для валков с учетом усилий и износа
- Конструкция вала с соответствующими диаметрами и подшипниками
- Правильная геометрия валов позволяет избежать таких проблем, как скручивание или деформация
- FEA-анализ для оптимизации формы валов и нагрузки
- Опытные производства для проверки работоспособности оснастки
Валки обычно изготавливаются из таких материалов, как инструментальная сталь D2, железо или резина/полиуретан. Типичные диаметры валов варьируются от 5 до 8 дюймов. Валки имеют корончатый контур для компенсации прогибов. Правильное выравнивание валков и жесткость корпуса очень важны для получения качественных деталей.
Анализ процесса формовки валков
Инженерный анализ при проектировании валов включает в себя:
- Модели CAD деталей - Создание 3D-моделей готовых профилей
- Анализ изгиба - Определение последовательности поворотов и углов крена
- FEA-моделирование - Моделирование сил качения и напряжений в материале
- Дизайн рулона - CAD-моделирование контуров на основе вычетов изгибов
- Проектирование машин - Определение размеров двигателей, валов и муфт в зависимости от нагрузки
- Прогиб - Анализ деформаций валков, валов и корпуса
- Путь инструмента - Имитация движения полосы через последовательность валов
Такой анализ гарантирует, что валковая оснастка обеспечит требуемую форму детали и допуски. Он также предотвращает такие дефекты, как смятие, растрескивание или пружинящий откат сформованных секций.
Рулонные материалы
Выбор подходящего материала валков важен для качественного профилирования и длительного срока службы инструмента. Ключевые факторы при выборе материала валков:
Твердость
- Твердость валков должна быть выше твердости чушек
- Предотвращает деформацию валков под давлением
- Валы из закаленной стали используются для большинства металлов
Прочность
- Валы должны выдерживать изгибающие усилия без усталости
- Высокая прочность, необходимая для выдерживания нагрузки при формовке
- Прочность определяет допустимые диаметры валов
Износостойкость
- Материалы валов должны быть устойчивы к повреждениям от трения
- Критически важно для больших объемов производства
- Специальные сплавы используются, если материал абразивный
Усиление работы
- Контактное давление не должно чрезмерно упрочнять валки.
- Приводит к повреждению поверхности и ухудшению качества деталей
- Покрытия с низким коэффициентом трения помогают преодолеть эту проблему
Материал | Описание | Приложения |
---|---|---|
Закаленная сталь | Среднеуглеродистая сталь, термически обработанная | Самый распространенный, используется для большинства металлов |
Адамит | Центробежное литье из высоконикелевого чугуна | Высокопроизводительные углеродистые и HSLA стали |
Резина/полиуретан | Валики из уретана или резины с высоким коэффициентом износа | Чувствительные металлы, такие как медь, латунь, алюминий |
Железо | Ковкий чугун, различная твердость | Валки для предварительной формовки, металлы низкой твердости |
На одном станке также используются комбинации материалов, например, предварительные стенды из железа и финишные стенды из стали. Резиновые/уретановые валки помогают при формовке мягких металлов, уменьшая трение.
Правильный выбор материала валков обеспечивает низкий уровень износа и способность выдерживать высокое давление, возникающее при валковой формовке. Это позволяет достичь максимальных объемов производства и свести к минимуму повторное шлифование или замену валков.
Применение роликовой формовки
Профильная роликовая прокатка используется для производства широкого спектра деталей в различных отраслях промышленности:
Строительство
- Стеновые панели, сайдинг, кровля, стойки, балки
- Перила, рамы, крепления для солнечных батарей, дренажные системы
- Уголок, труба, швеллер для конструкций
**Автомобиль **
- Дверные балки, рейлинги, кронштейны, поперечины
- Каркасы сидений, подножки, бамперы
- Элементы наружной отделки
** ОВК **
- Воздуховоды и фитинги
- Желоба, жалюзи, регистры, диффузоры
Обработка материалов
- Рамы для стеллажей, стеллажи, конвейеры
- Тележки, корзины, шкафчики, шкафы для хранения
Мебель
- Рамы, шкафы, полки, ручки
- Столы, картотеки, торговое оборудование
Электрика
- Осветительные приборы, кабельные лотки, распределительные коробки
- Корпуса для панелей, кабельные трассы, рамы для солнечных батарей
Транспорт
- Сцепные устройства, поручни, ступеньки, рамы для грузовиков и прицепов
- Барьеры безопасности на автомобильных дорогах
Кроме того, в рулонном производстве обычно изготавливают декоративные архитектурные профили, дисплеи, экспонаты, вывески, панели кузова железнодорожных и грузовых вагонов.
Гибкость, позволяющая создавать неограниченное открытое поперечное сечение, делает рулонную штамповку идеальным решением для производства как стандартных, так и нестандартных деталей.
Сравнение роликовой формовки с другими технологическими процессами
Профильная прокатка имеет как преимущества, так и ограничения по сравнению с другими процессами обработки металлов давлением:
Сравнение гибки на листогибочном прессе
- Более низкая стоимость оборудования по сравнению с большими листогибочными прессами
- Отсутствие затрат на оснастку для гибочных штампов
- Более высокая пропускная способность
- Ограничивается открытыми профилями, листогибочные прессы могут делать замкнутые формы
- Размер при прокатке ограничивается производительностью машины
- Прессовые тормоза ускоряют переналадку между деталями
- Листогибочные прессы могут иметь более толстый материал.
Против штамповки
- Значительно меньшие затраты на оснастку по сравнению со штампами для штамповки
- Возможность изготовления небольших партий по сравнению со штамповкой, оптимизированной для больших объемов
- Повышенная эффективность использования материала при валковой формовке
- Больше ограничений по размеру при штамповке
- Штамповка позволяет получать формы замкнутого сечения, невозможные при роликовой штамповке
- Более высокая первоначальная стоимость оборудования для рулонной формовки
Сравнение с экструзией
- Недорогая оснастка обеспечивает гибкость валковой формовки для замены деталей
- Экструзия позволяет получить только фиксированное поперечное сечение в непрерывных отрезках
- Рулонная формовка имеет ограничения по ширине в зависимости от производительности машины
- Экструзия нецелесообразна для коротких партий продукции
Сравнение лазерной и гидроабразивной резки
- Отсутствие зоны термического влияния или коробления, как при лазерной резке
- Низкие отходы материала по сравнению с потерями при стрижке
- Возможность гибкого производства нестандартных замкнутых форм в отличие от роликовой формовки
- Очень короткие сроки изготовления возможны при использовании режущего инструмента по сравнению с валковым.
- Нет ограничений по форме и толщине, как при рулонной штамповке
Учет преимуществ и ограничений помогает определить оптимальный выбор процесса для конкретного производства. Рулонная формовка дает преимущества при длительном производстве, учитывая высокую первоначальную стоимость оборудования.
Дефекты роликовой формовки
Некоторые возможные дефекты, которые могут возникнуть при профильной прокатке:
Сгибание
- Складки или морщины вдоль полотна или фланца
- Из-за чрезмерного сжатия
- Недостаточное соотношение ширины и толщины
- Увеличьте давление удержания
Скручивание
- Готовый профиль скручивается в продольном направлении
- Неправильное выравнивание рулонов
- Неправильное расстояние между валковыми клетями
- Отрегулируйте выравнивание валов
Складной
- Сформированный фланец накладывается на полотно
- Чрезмерное сжатие
- Увеличение диаметра нижнего вала
Маркировка поверхности
- Отпечатки роликов видны на поверхностях
- Чрезмерное давление на вал
- Установите
Разделение
- Трещины вдоль нейтральной оси формованного профиля
- Металл превышает пределы пластичности при формовке
- Увеличение радиуса при вычитании изгибов
- Отрегулируйте график прохождения роликов
Факел
- Сформированные фланцы распространяются наружу
- Недостаточная фиксация рулона
- Неправильное расположение верхних и нижних валов
- Отрегулируйте выравнивание валов
Без наполнения
- Полотно не соприкасается с нижним валом
- Предотвращение полного формирования
- Изношенные или поврежденные валики
- Увеличение диаметра вала
Springback
- Форма детали не сохраняется после выхода из последней стойки
- Упругое восстановление металла
- Перегиб и перегиб могут компенсировать
Изменение толщины
- Неоднородная толщина материала вдоль детали
- Неправильное соотношение между валами
- Увеличение диаметра нижнего вала
Повреждение поверхности
- Вмятины, зазубрины, царапины на сформированных участках
- Накапливание мусора на валках приводит к появлению следов
- Смазка материала или рулонов
- Чистые поверхности валков
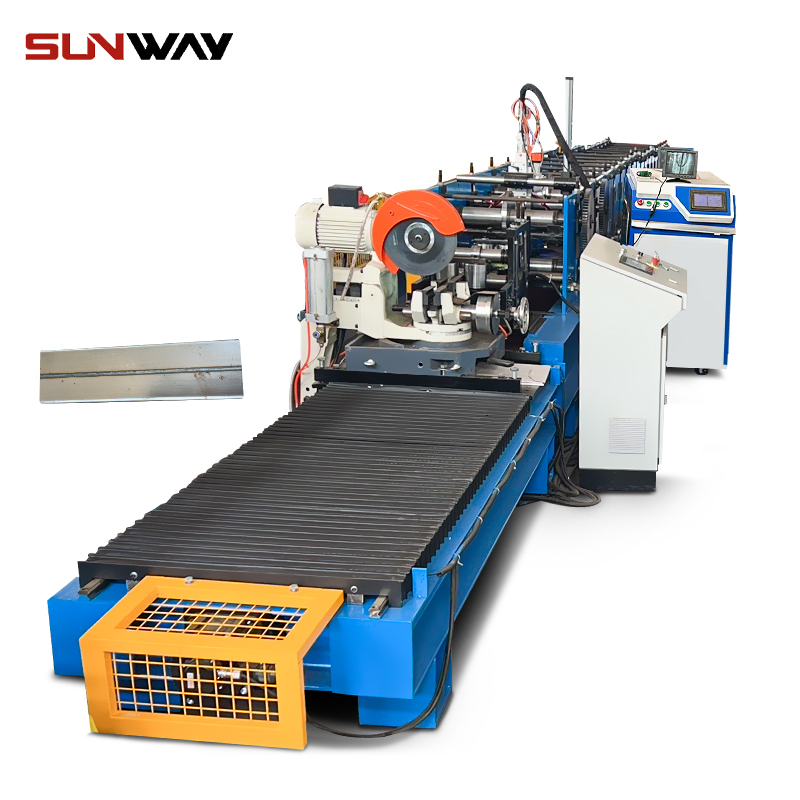
Смазка при формовке валков
Смазка имеет решающее значение при профильной прокатке:
- Уменьшение трения между валками и листовым металлом
- Обеспечивают более легкую гибку и подачу материала
- Предотвращение повреждения поверхности профилей
Преимущества эффективной смазки:
- Снижение нагрузки на валки и оснастку при формовании
- Предотвращение заклинивания и переноса материала на валки
- Обеспечивают более высокую скорость линии и производительность
- Улучшение качества поверхности готовых деталей
- Снижение износа валков для увеличения срока службы
Распространенные методы смазки:
Смазка валов
- Прямое нанесение смазки на поверхность валков
- Капельные системы для поддержания рулонов в покрытом состоянии
- Уменьшает трение при соприкосновении листа с валками
Смазывание запасов
- Лист или рулон с покрытием перед размоткой
- Правильное количество для полного цикла производства
- Постоянная смазка во всех стойках
Туманный спрей
- Распыление смазки в воздушном тумане на поверхности
- Небольшое количество равномерно распределенных
- Чистое нанесение без лишних следов
Окружающая среда
- Системы для внутреннего распыления масла или охлаждающей жидкости
- Помогают обеспечить более чистое качество воздуха в магазине
Синтетические смазочные материалы обычно используются для валковой формовки вместо продуктов на масляной основе. Они обеспечивают чистую работу, длительный срок службы и минимальный уровень загрязнения при обработке формованных деталей. Правильные системы рециркуляции могут продлить срок службы синтетических смазочных материалов для вальцевой штамповки.
Вторичные операции
Вторичные операции часто выполняются на деталях, изготовленных методом прокатки:
Резка
- Обрезка или распиловка на готовые отрезки
- Пробивание отверстий для крепежа или подвесов
- Насечки и пазы для установки других компонентов
- Обрезка и зачистка кромок для косметики
Изгиб
- Торцевые выступы, фланцы, кронштейны добавляются с помощью листогибочных прессов
- Сформированные блокировки и карманы для соединений
- Швы и швы для соединения панелей
Отделка
- Окраска и порошковое покрытие для придания внешнего вида и защиты
- Горячее цинкование или покрытие для защиты от коррозии
- Грунтование и пассивация металлов, таких как нержавеющая сталь
Оборудование
- Добавление закладных гаек, шпилек, накидных крепежных элементов
- Установленные монтажные зажимы, кронштейны и клипсы
Сборка
- Соединение рулонных профилей с панелями или рамами
- Интеграция изоляции, стекла, электроники, освещения
- Сварка и крепление дополнительных компонентов
Такие вторичные процессы помогают создавать готовые детали или узлы из профилей, изготовленных методом прокатки. Автоматизация позволяет интегрировать несколько операций в непрерывную производственную линию.
Поставщики оборудования для формовки рулонов
Среди ведущих производителей профилегибочного оборудования можно назвать следующих:
- Самко Машинери - Полный ассортимент валковых формовочных машин для производства и изготовления прототипов
- Metform International - Рулонные машины для широкого спектра отраслей промышленности
- Дальстром Моторс - Проектирование и изготовление валкообразователей на заказ
- Формтек - Рулонные формовщики для систем отопления, вентиляции и кондиционирования воздуха, водоотвода, панелей, стеллажей, автомобильной промышленности
- Группа компаний "Брэдбери - Ведущий поставщик оборудования для обработки плоских листов и рулонов
- Шибо Машиностроение - Тайваньский производитель валкового оборудования
- Кометное оборудование - Производственные вальцы и переносные колесные станки
- КНУТ - Немецкие станки и инструменты для формовки валков
- Ботоу Сяньфа - Производитель рулонного оборудования из Китая
- EZForm - Ведущий канадский производитель вальцовочных станков
При выборе валкового оборудования необходимо учитывать следующие важные факторы:
- Требуемая ширина и толщина формовки
- Общая длина станка в зависимости от размеров детали
- Количество прокатных клетей, необходимых для формы профиля
- Темпы и объемы производства
- Управление, автоматизация, простота настройки
- Наличие услуг по проектированию валов
- Опыт работы с аналогичными приложениями
- Глобальное присутствие для обслуживания и поддержки
Ведущие производители валковых машин предоставляют полную помощь в проектировании и услуги по изготовлению валковой оснастки в дополнение к формовочному оборудованию.
Затраты на формовку рулонов
Экономика профильной прокатки:
Стоимость машины
- От $50,000 до $500,000+ в зависимости от размера и характеристик
- Более крупные автоматизированные машины с большими возможностями стоят дороже
Стоимость оснастки
- $2,000 - $20,000+ за комплект оснастки
- Увеличение количества рулонных стоек и сложности увеличивает стоимость
** Стоимость эксплуатации **
- Труд 1-2 операторов, как правило, для погрузки/разгрузки
- Низкие затраты на техническое обслуживание и замену оснастки
- Потребление энергии ~50-100 кВтч на тонну продукции
Производственные тарифы
- Скорость линии до 200 футов в минуту на высокоскоростных машинах
- Возможно выполнение от 10 000 до 100 000+ футов за смену
Срок окупаемости
- ~1-3 года после достижения безубыточного количества
- При больших объемах производства
- Долгий срок службы машин - более 20 лет
Стоимость за штуку
- $0.10 - $2 за штуку в зависимости от сложности
- Экономичность повышается при увеличении объемов благодаря низким эксплуатационным расходам
Рулонная штамповка становится экономически выгодной при изготовлении крупных партий продукции - обычно более 50 000 штук. При меньших объемах более экономически эффективными могут быть другие процессы, такие как лазерная резка или листогибочный пресс. Гибкость роликовой формовки позволяет производить как малые, так и большие объемы на одном и том же станке.
Управление процессом формовки валков
Эффективное управление процессом обеспечивает высокое качество и производительность валковой формовки:
Скорость линии
- Скорость производства и пропускная способность напрямую зависят от скорости линии
- Скорость оптимизирована для обеспечения баланса между производительностью и качеством
Давление в рулоне
- Для качественного формования необходимо достаточное давление
- Избыточное давление вызывает дефекты и износ валов
- Датчики силы помогают оптимизировать давление
Натяжение ленты
- Достаточное натяжение, необходимое для плавной подачи
- Минимизирует смятие и способствует движению материала
- Тензодатчики на ленте контролируют натяжение
Износ валков
- Изношенные валки приводят к ошибкам в маркировке и размерах
- Системы измерения валов в режиме онлайн определяют степень износа
- Замена рулонов на основе показателей
Смазка
- Достаточная смазка предотвращает появление царапин
- Датчики проверяют надлежащий уровень смазки
- Насосы регулируют подачу в зависимости от скорости линии
Автоматизация
- Программируемые контроллеры координатных станков
- Дисплеи и интерфейсы HMI для управления
- Диагностика контролирует состояние процесса
Современные валковые формовочные машины используют комплексный мониторинг и сетевые системы управления для автоматического поддержания оптимальных условий формования. Это предотвращает брак, обеспечивает максимальную производительность и сокращает время простоя.
Распространенные проблемы при формовке рулонов
Некоторые частые проблемы, возникающие при прокатке профилей, и способы их решения:
Проблема: Скручивание формованного профиля
Решение: Обеспечьте правильное выравнивание валков; Увеличьте расстояние между клетями валков; Проверьте параллельность валков
Проблема: Искажение профиля после выхода из последней стойки
Решение: Увеличение диаметра нижнего вала; Использование роликовых опор для готового профиля
Проблема: Переворачивание фланца при формовке
Решение: Уменьшить сжатие; Увеличить ширину фланца; Проверить контуры валков
Проблема: Полотно не соприкасается с нижним валом
Решение: Увеличить диаметр нижнего валка; Отрегулировать график прохода валков
Проблема: Чрезмерная нагрузка на редукторы и оснастку
Решение: Смазать материал; Снизить скорость линии; Проверить выравнивание валов
Проблема: На поверхности видны следы от валика
Решение: Замените поврежденные валки; Увеличьте смазку; Уменьшите давление на валки
Проблема: Расщепление вдоль стыков полотна и фланца
Решение: Увеличение радиуса изгиба; Использование большего количества стендов для предварительной формовки; Проверка пластичности материала
Проблема: Плохие допуски на профиль
Решение: Учет пружинящей нагрузки при проектировании валов; использование избыточного изгиба
Проблема: Царапины на формованных деталях
Решение: Очистить поверхность валков; Улучшить смазку; Проверить качество поверхности валков
Безопасность при формовке рулонов
Техника безопасности при работе с валками:
- Защитные ограждения для рулонных клетей
- Двери с блокировкой доступа, которые отключают машину при открытии
- Наклейте кнопки аварийной остановки
- Датчики, останавливающие работу при обнаружении части тела
- Процедуры блокировки/таскировки при техническом обслуживании
- Используйте щетки или воронки для смазки вместо прямого обращения
- Оборудование для безопасного подъема и перемещения тяжелых инструментов
- Рабочие надевают надлежащие СИЗ - защитные очки, перчатки, не стесняющую движения одежду
- Достаточная вентиляция для борьбы с масляным туманом и испарениями
- Изоляция зон повышенного шума с помощью звукоизолирующих кожухов
- Регулярные проверки оснастки, защитных устройств, датчиков, блокировок
- Обучение безопасным методам работы и мерам предосторожности
- Установите зоны безопасности и ограничьте доступ вблизи машины
Валковая штамповка сопряжена со значительными опасностями, связанными с вращающимися деталями, высоким давлением и острыми кромками. Соблюдение комплексных мер безопасности имеет решающее значение для предотвращения травм. Необходимо обеспечить защиту станков, процедуры блокировки, обучение работников и использование СИЗ.
Контроль качества прокатки
Практика контроля качества в валковой штамповке:
- Контроль первой части сформированного профиля
- Контроль размеров с помощью измерительных приборов и КИМ
- Контроль изменения толщины по длине детали
- Контроль качества поверхности сформированных участков
- Визуальный осмотр на наличие дефектов
- Контроль правильного количества смазки
- Измерение ширины полотна, фланца и углов изгиба
- Проверка длины отрезков и качества дырокола
- Проверка на скручивание, изгиб и плоскостность
- Тестовые испытания для проверки новой оснастки и изменений в технологическом процессе
- Статистический контроль процессов, отслеживающий дефекты
- Анализ возможностей критических измерений
- Документирование параметров процесса и допусков
- Обучение операторов процедурам проверки
- Корректирующие действия при возникновении дефектов
При надлежащих мерах контроля качества повторяемость процесса валковой формовки обеспечивает стабильное изготовление деталей с требуемыми допусками. Статистическое отслеживание помогает выявить области, требующие улучшения.
Поиск и устранение неисправностей в процессе формовки рулонов
Методы поиска и устранения неисправностей, возникающих в процессе валковой формовки:
- Остановите машину и сначала тщательно осмотрите сформированный участок
- Обзор последних изменений или корректировок процесса
- Проверьте износ валов, количество смазки, выравнивание полос
- Проверка свойств и состояния материалов на складе
- Попробуйте постепенно уменьшить скорость линии
- Регулировка давления и выравнивания отдельных валковых клетей
- Изучите конструкцию валков и настройку инструмента
- Проверьте обучение операторов и соблюдение процедур
- Анализ основной причины обнаруженного дефекта
- Пилотный запуск небольших партий для систематического выявления проблемы
- Проверяйте и измеряйте сформированный профиль в нескольких местах
- Итерационная обработка инструментов применяется только для решения хронических проблем после того, как исчерпаны другие способы их устранения.
- Консультируйтесь с экспертами по конструкции валков для устранения сложных проблем с формовкой
- Рассмотрите возможность тестирования материала, если дефекты связаны с составом
- Документируйте все результаты и предпринятые корректирующие действия
Тщательное устранение неисправностей помогает выявить факторы, способствующие возникновению проблем с валковой формовкой. Узкое внимание к оснастке должно уделяться только после рассмотрения других потенциальных источников, связанных с материалом, методами, человеком или машиной.
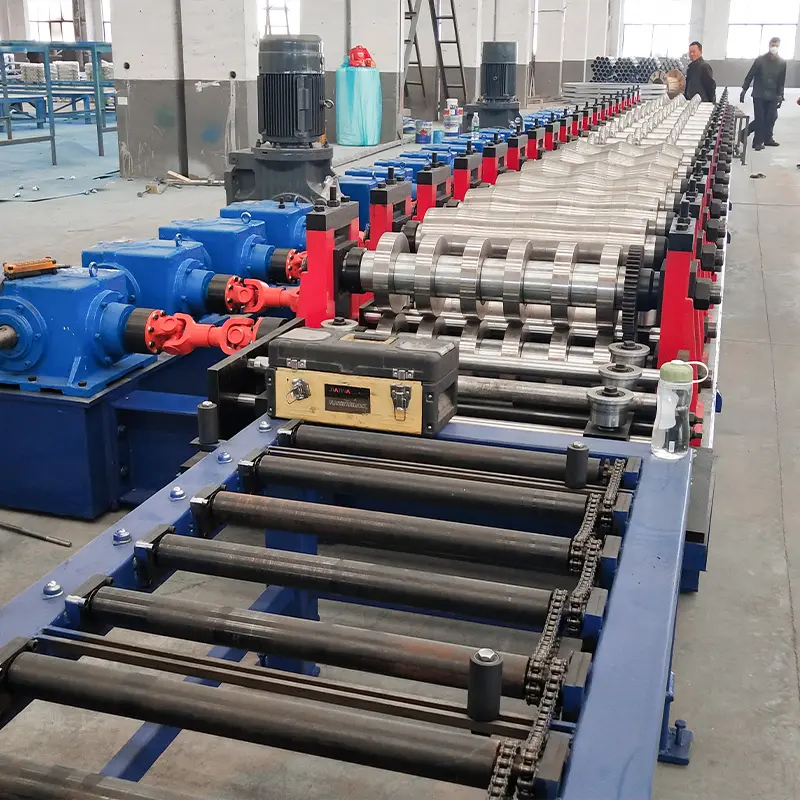
Отраслевые стандарты в области роликовой формовки
Стандарты на прокатку определяют технические характеристики оборудования, дизайн и контроль качества:
ASTM A924 - Стандарт на стальные листы, используемые в валковой штамповке
ASTM B136 - Стандарт на материалы для латунных полос, предназначенных для рулонной штамповки
AISI D100 - Рекомендации и допуски при прокатке
AWS D1.3 - Рекомендации по сварке деталей и машин, изготовленных методом роликовой формовки
NSSGA - Руководство по формовке рулонов для продукции агрегатной промышленности
AISI SG03-3 - Руководство по изготовлению каркасов из холоднодеформированной стали
ASTM E290 - Методы испытаний на изгиб деталей, изготовленных методом прокатки
ISO 11562 - Линейные измерения деталей, изготовленных методом прокатки
JIS Z1701 - Методы испытаний изделий, изготовленных методом прокатки
API Spec 5CT - Технические условия на обсадные и насосно-компрессорные трубы
SAE J136 - Методы испытаний смазочных материалов
Соблюдение отраслевых стандартов гарантирует соответствие деталей, изготовленных методом роликовой формовки, требуемым спецификациям по таким параметрам, как материалы, конструкция, размеры, испытания и соединение.
Часто задаваемые вопросы
Вопрос: Какие металлы могут быть подвергнуты прокатке?
О: Рулонная штамповка может формировать сталь, нержавеющую сталь, алюминий, медь, латунь и другие вязкие металлы в пределах толщины и ширины машины.
В: Какой диапазон толщины может быть уложен в рулон?
О: Обычно толщина материала варьируется от 18 гектаров до 1/4 дюйма. Более крупные машины могут формировать материал толщиной до 1 дюйма. Минимальная толщина - от 26 до 30 га.
В: Какие допуски могут быть достигнуты?
О: Детали, изготовленные методом роликовой формовки, обычно имеют допуски +/- 1% на толщину материала. Некоторые размеры могут быть выдержаны в более жестких допусках.
В: Какой длины может быть один рулон?
О: Производственная длина варьируется от 2 футов до 25 футов в зависимости от размера машины. Теоретически возможна неограниченная длина.
В: Какие металлы требуют смазки?
О: Смазка рекомендуется для большинства металлов, кроме нержавеющей стали. Особенно полезно для латуни, меди и алюминия.
Вопрос: Влияет ли направление зерна на формовку валков?
О: Да, гнуть легче в поперечном направлении. Профили обычно формируются параллельно исходному направлению зерна.
В: Сколько операторов требуется?
О: Обычно 1-2 оператора - один на разматывателе и один на выходе. Автоматизированные машины могут не нуждаться в операторе.
В: Как быстро происходит смена профилей?
О: Смена валов и оснастки может занимать 4-8 часов. Некоторые быстросменные оснастки значительно сокращают это время.
В: Чем определяются допуски на профиль?
О: Допуски зависят от свойств материала, жесткости оснастки, количества валковых клетей, смазки и скорости линии.
В: Что ограничивает максимальную ширину?
О: Размер рамы машины, жесткость подставки для валков и мощность формования ограничивают максимальную ширину. На самых больших машинах - до 120 дюймов.
Вопрос: Какие сложные формы можно сформировать?
О: Рулонная штамповка лучше всего подходит для производства открытых однородных форм. Листогибочные прессы лучше подходят для коротких серий сложных профилей.
В: Что вызывает появление царапин на сформированной поверхности?
О: Налипание мусора на рабочую поверхность или инструмент, плохая смазка, повреждение инструмента, неправильное давление валков.
В: Почему пружинящий откат является проблемой?
О: Восстановление упругости после изгиба приводит к искажению формы. Перегиб и поддержка нижнего валика могут компенсировать это.
В: Как добавляются отверстия и вырезы?
О: Перфорация, высечка или лазерная резка используются после роликовой формовки для создания отверстий и фигурных вырезов по мере необходимости.
Вопрос: Почему валковая формовка экономичнее других методов?
О: Отсутствие необходимости в штампах и низкие эксплуатационные расходы. Затраты на установку амортизируются в течение длительного времени. Высокая степень использования материала.