Visión general de la perfiladora
perfiladora es una operación de curvado continuo en la que las láminas o bobinas se van conformando gradualmente hasta alcanzar la forma transversal deseada a través de una serie de estaciones de conformado consecutivas. Las estaciones de conformado constan de rodillos opuestos que doblan y conforman continuamente la tira de material en movimiento hasta conseguir el perfil final.
El perfilado permite una producción eficaz y rentable de piezas metálicas con secciones transversales personalizadas. Se utiliza habitualmente para fabricar piezas como paneles de pared, tejados, marcos de puertas, sistemas de estanterías, productos para carreteras, componentes de muebles y mucho más. La flexibilidad del perfilado permite crear casi cualquier perfil de sección transversal abierta.
Algunas de las principales ventajas del perfilado son:
- Proceso altamente automatizado con escasa necesidad de mano de obra
- Capaz de producir grandes volúmenes
- Conformación coherente y repetible de perfiles
- Se pueden moldear formas y tamaños muy diversos
- Bajos costes de utillaje en comparación con otros procesos
- Mínimo desperdicio de material, ya que las existencias se forman progresivamente
- Aplicable a diversos metales como acero, aluminio, latón, etc.
El perfilado requiere una mayor inversión inicial en equipos en comparación con métodos como el prensado con freno o el estampado. Sin embargo, el perfilado resulta económico para grandes lotes de producción, dado el alto rendimiento y los bajos costes operativos. Es ideal para producir grandes longitudes de secciones transversales de perfil repetitivas.
Proceso de perfilado
El proceso de perfilado consta de varias fases:
- Las bobinas o chapas se cargan en una desbobinadora o unidad de alimentación que endereza la banda.
- El material se alimenta longitudinalmente a través de una serie de estaciones de laminado.
- Cada soporte de rodillos realiza una serie de dobleces hasta que se forma incrementalmente la forma de perfil deseada.
- Los troqueles de corte producen piezas de la longitud requerida a medida que el perfil sale de la laminadora.
- Las secciones formadas se recogen en una mesa de despegue.
La clave del proceso de perfilado es el curvado gradual de la materia prima a través de soportes sucesivos. El número de estaciones de perfilado necesarias depende de la complejidad de la forma de la pieza. Las máquinas típicas tienen entre 3 y 16 estaciones de conformado.
Componentes de la máquina formadora de rollos
Las perfiladoras tienen tres secciones principales:
- Alimentación animal - Desenrollador, enderezador y unidad de alimentación
- Formando - Soportes de rodillos consecutivos para curvar la chapa progresivamente
- Corte - Cizallas o sierras para cortar perfiles a medida
Estos son los componentes clave de una laminadora:
Sección de máquinas | Componentes |
---|---|
Alimentación del ganado | Sujeción de bobinas, desenrollador, rodillos de alimentación, guías de material, rodillos de arrastre, enderezadora de hojas |
Formando | Caja de rodillos, rodillos superiores e inferiores, cajas de engranajes, ejes de rodillos |
Corte | Prensas de corte, cizallas de matriz volante, trituradoras de extremos |
Controlar | PLC, HMI, controles de línea |
Otro | Protecciones, bastidor base, motores, sistema hidráulico |
Diseños de rollos
El utillaje de rodillos es fundamental para crear la forma de perfil deseada. La conformación por rodillos depende de la acción de flexión precisa de los rodillos contorneados para conformar las secciones de forma incremental. Los diseños de los rodillos se personalizan para producir la geometría exacta de la pieza que se está fabricando.
Estos son algunos de los diseños de rollos más utilizados:
- Formación de círculos - Se utiliza para formar formas curvas y radios
- Pellizcar - Aprieta el metal a una sección más pequeña
- Borde - Crea una curva en el borde del perfil
- Fin - Para hacer pequeñas curvas hacia dentro o hacia fuera
- Rígido - Rodillos de soporte general para mantener la forma
El diseño de la pasada del rodillo se desarrolla primero mediante el análisis de la forma de la pieza. La geometría del rodillo se refina de forma iterativa para conseguir los incrementos de flexión requeridos y el mínimo esfuerzo de conformado. Los materiales de los rodillos se seleccionan en función de las propiedades del material y los volúmenes de producción. Los materiales más comunes son el acero endurecido, el hierro y el caucho/poliuretano para grandes volúmenes.
Consideraciones sobre el diseño
Algunas consideraciones clave en el diseño de perfiladoras:
- Tolerancias de las piezas - El diseño del rodillo debe tener en cuenta la recuperación elástica y cumplir las especificaciones de tolerancia
- Propiedades de la banda - El límite elástico, la dureza y el grosor influyen en las cargas de los rodillos
- Índice de producción - La velocidad de la línea influye en la capacidad de carga del rodillo y en el tamaño del motor
- Ancho de banda - La anchura máxima depende de la capacidad de la máquina y de la geometría de la pieza
- Tipo de material - Materiales de los rodillos seleccionados en función de la dureza del metal en bruto
- Lubricación - La reducción de la fricción permite un mejor flujo de material en el conformado
- Orientación del grano - El diseño del rodillo debe tener en cuenta la dirección de la veta de la chapa
Se lleva a cabo un minucioso desarrollo de pasadas de rodillo y análisis de elementos finitos para optimizar el diseño del utillaje de rodillo antes de la fabricación. Las series de producción piloto ayudan a verificar el utillaje antes de la producción completa.
perfiladora Proceso
El proceso de perfilado produce piezas doblando y conformando longitudinalmente chapas o bobinas a medida que pasan por pares consecutivos de rodillos contorneados. Cada par de rodillos realiza una serie de curvaturas precisas hasta que se forma incrementalmente el perfil de sección transversal final.
Cómo funciona el perfilado
- El material en hojas o bobinas se carga en un desbobinador que introduce la banda en la laminadora a través de una enderezadora.
- Los rodillos de alimentación agarran el material y lo hacen avanzar a través de las estaciones de perfilado.
- Cuando la banda entra en contacto con el primer soporte, se produce la conformación inicial del perfil.
- En cada soporte posterior, se realizan dobleces incrementales hasta alcanzar la forma final.
- La sección perfilada sale de la última estación y se corta a las longitudes deseadas.
- Las piezas conformadas se recogen en una mesa de despegue.
La principal ventaja del perfilado es el curvado gradual del material mediante una serie de pequeños incrementos. La secuencia de doblado y el diseño del rodillo permiten que el material fluya sin adelgazamiento ni desgarro excesivos. El proceso ejerce un control preciso sobre la deformación del material para crear la sección transversal deseada.
El diseño correcto de la pasada de rodillo es crucial para conformar con éxito las piezas dentro de los límites de tolerancia. El perfilado se basa únicamente en la compresión para doblar la pieza. No se aplican fuerzas de tracción durante el conformado. Los rodillos sólo aprietan y presionan la banda longitudinalmente a medida que avanza por la máquina.
Pasos del perfilado
He aquí la secuencia de pasos del proceso de perfilado:
1. Alimentación
- Material en hojas o bobinas cargado en un desbobinador o unidad de alimentación
- Los rodillos de alimentación automática con rodillos de arrastre agarran y alimentan la banda
- La enderezadora de hojas elimina la curvatura de la bobina y las curvaturas iniciales
**2. Flexión incremental **
- El material entra en el primer puesto de laminación y se realizan los doblados iniciales
- En cada soporte posterior, la flexión progresa más
- Los rodillos se mecanizan con precisión según los contornos requeridos
- La forma final del perfil se consigue gradualmente mediante repeticiones
3. Corte
- Sección de perfil formada alimentada automáticamente a la estación de corte
- Las cizallas o sierras cortan las piezas a la longitud especificada
- Las longitudes de corte habituales oscilan entre 3 y 16 pies.
4. Recogida
- Las piezas cortadas se apilan en mesas de salida o cintas transportadoras
- Las mesas permiten agrupar y transportar cómodamente las secciones
5. Acabado
- Opcional: acabado final, perforación, marcas, etc.
- Posibilidad de operaciones automatizadas para grandes volúmenes
Ventajas del perfilado
El perfilado ofrece importantes ventajas:
- Posibilidad de altas velocidades de producción de hasta 200 pies/min
- Conformación coherente y repetitiva de perfiles
- Fuerzas reducidas, por lo que el desgaste de las herramientas es menor
- Permite longitudes de pieza ilimitadas
- Mínimo desperdicio de material, ya que las existencias se forman progresivamente
- Menor coste que el estampado o el plegado en prensa para tiradas largas
- Posibilidad de producir una amplia gama de formas y geometrías
- Ideal para materiales de alta resistencia como el acero HSLA
- Común para grandes volúmenes de 50.000 a 500.000 piezas
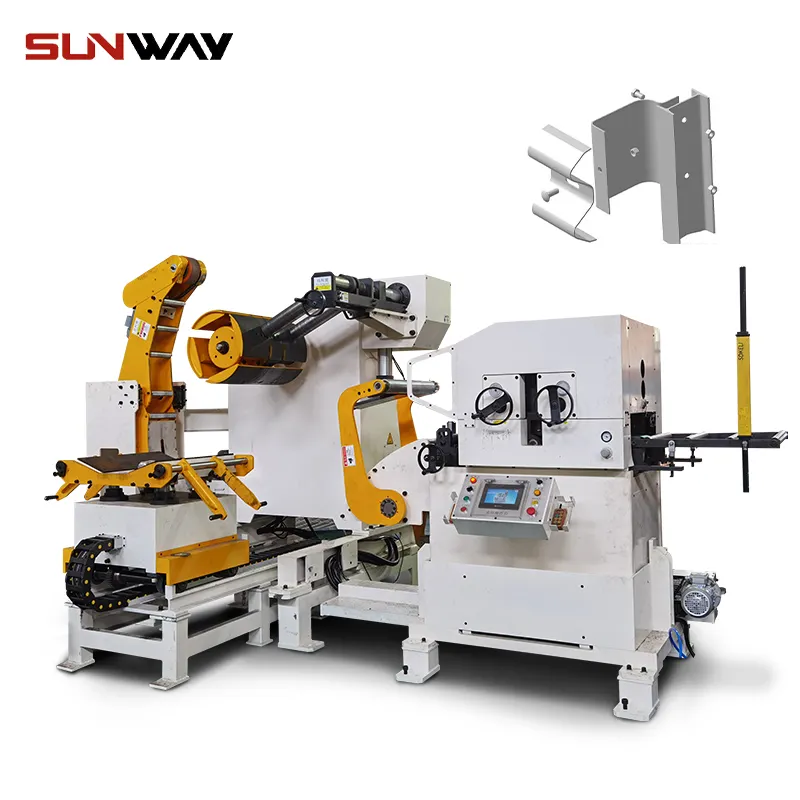
Perfiladoras
Perfiladoras son sistemas diseñados a medida para producir piezas metálicas con una forma de sección transversal específica. Entre los aspectos clave de las perfiladoras se incluyen:
Sistema de alimentación
- Desbobinador o desbobinador de chapas o bobinas
- Soportes de rodillos de alimentación con rodillos de arrastre
- Enderezadora de chapas y medidores de espesor
- Guías de stock y rodillos de apoyo
Estaciones de formación
- Serie de soportes de perfilado
- Ejes de balanceo superior e inferior con acoplamientos dentados
- Carcasas de rodillos entrelazadas para mayor rigidez
- Contorno y geometría del rodillo adaptados a la forma de la pieza
Sistema de corte
- Matriz de corte, sierra circular o navaja para recortes
- Mesas de postcorte o transportadores de salida
- Sistemas de empaquetado para la manipulación de piezas acabadas
Bastidor de la máquina
- Bastidor de acero soldado de gran resistencia
- Paredes laterales de protección y seguridad
- Protecciones alrededor de las piezas móviles
Unidades
- Motor principal acoplado al eje de entrada
- Reductores para cada portabobinas
- Servoalimentación para desbobinado y corte
- Sensores para automatización y control
Configuraciones de laminadores
Existen tres tipos comunes de configuraciones de perfiladoras:
En línea
- Las secciones se forman y cortan longitudinalmente
- Cada pieza tiene un perfil uniforme en toda su longitud
- Común para piezas de hasta 25 pies de longitud
- Altas velocidades de producción de hasta 200 pies/min
Rotary
- La banda se introduce en juegos de rodillos circulares
- La rotación forma el perfil alrededor del mandril
- Se utiliza para hacer anillos y formas redondeadas
- Menores índices de producción que en línea
Máquinas de ruedas
- Troqueles de rodillo montados sobre ruedas circulares giratorias
- Las ruedas giran para formar curvas y figuras
- Portátil y ajustable para recorridos cortos
- Producción de hasta 60 pies/min
Las perfiladoras en línea son el tipo predominante utilizado en las plantas industriales debido a su elevada capacidad de producción continua.
Formadora de rollos
Las perfiladoras están disponibles en una amplia gama de tamaños:
Clasificación de la máquina | Anchura de conformado | Espesor de banda |
---|---|---|
Trabajo ligero | Hasta 18 pulg. | Calibre 26 - 16 |
Intermedio | Hasta 24 pulgadas | Calibre 16 - 10 |
Estándar | Hasta 72 pulgadas | Calibre 10 - 3 |
Para trabajos pesados | Hasta 120 pulg. | Calibre 3 - 1/4 pulg. |
- Las pequeñas perfiladoras se utilizan para series cortas.
- Máquinas de capacidad media utilizadas para trabajos típicos de taller de fabricación.
- Grandes perfiladoras para grandes volúmenes en grandes plantas.
Factores clave que determinan el tamaño de la máquina:
- Anchura máxima de banda necesaria
- Gama de espesores de los metales utilizados
- Complejidad de las formas de las piezas
- Volúmenes y ritmos de producción
- Longitud total de los perfiles
Diseño de perfilado
El diseño del proceso de perfilado requiere un minucioso análisis de ingeniería. El objetivo es determinar las secuencias de paso de rodillo y el diseño de utillaje óptimos para producir la forma de pieza deseada.
Diseño Roll Pass
El diseño de paso de rodillo define la secuencia precisa de plegado en cada estación a lo largo de la máquina:
- El primer paso consiste en determinar el orden de las curvas necesarias para formar el perfil.
- El ángulo de curvatura total se divide en incrementos repartidos entre los soportes de los rodillos.
- Se analizan los contornos y las posiciones de los rodillos para conseguir los ángulos de flexión.
- Varias iteraciones realizadas para optimizar el programa de pasadas de rodillo.
- El análisis se realiza utilizando herramientas de software como CAD, FEA, programas de diseño de rodillos.
- Se realizan pruebas piloto para verificar el utillaje antes de la producción total.
El número total de puestos de rodillo se decide en función de:
- Complejidad de la forma del perfil acabado
- Propiedades del metal: grosor, límite elástico
- Tolerancias requeridas en las dimensiones de las piezas
- Ángulo máximo a formar en cada estación
El diseño correcto del paso de rodillo es clave para obtener piezas conformadas de calidad. Evita defectos como el pandeo, la rotura y el springback en las secciones conformadas.
Diseño de rollos
El diseño de herramientas para rodillos requiere:
- Determinación de los contornos de los rodillos para que coincidan con la geometría de la pieza
- Análisis de los pasos de flexión progresiva y forma del rodillo deducida
- Selección del material de los rodillos en función de las fuerzas y el desgaste
- Diseño del eje con diámetros y cojinetes adecuados
- Geometrías de rodillo adecuadas para evitar problemas como la torsión o la distorsión
- Análisis de elementos finitos para optimizar la forma y la carga de los rodillos
- Tiradas de producción piloto para verificar el rendimiento de las herramientas
Los rodillos suelen mecanizarse a partir de materiales como acero D2 para herramientas, hierro o caucho/poliuretano. Los diámetros típicos de los rodillos oscilan entre 5" y 8". Los rodillos tienen un contorno coronado para compensar las desviaciones. La correcta alineación de los rodillos y la rigidez de la carcasa son fundamentales para obtener piezas de calidad.
Análisis de perfilado
El análisis de ingeniería en el diseño de rodillos implica:
- Modelos CAD de piezas - Creación de modelos 3D de perfiles acabados
- Análisis de flexión - Determinación de la secuencia de curvas y ángulos de balanceo
- Modelado FEA - Simulación de las fuerzas de rodadura y las tensiones del material
- Diseño de rollos - Modelado CAD de contornos basado en deducciones de curvatura
- Diseño de máquinas - Dimensionamiento de motores, ejes y acoplamientos en función de las cargas
- Desviación - Análisis de las deformaciones de las pilas de rodillos, los ejes y las carcasas
- Trayectoria de la herramienta - Simulación del movimiento de la banda a través de la secuencia de rodillos
Este análisis garantiza que el utillaje de rodillos produce la forma de pieza y las tolerancias requeridas. También evita defectos como el pandeo, el agrietamiento o el springback de las secciones conformadas.
Materiales en rollo
La selección de los materiales adecuados para los rodillos es importante para obtener un perfilado de calidad y una larga vida útil de las herramientas. Factores clave en la elección del material de los rodillos:
Dureza
- La dureza del rodillo debe ser superior a la del material
- Evita la deformación del rodillo bajo presión
- Rodillos de acero templado para la mayoría de los metales
Fuerza
- Los rodillos deben soportar fuerzas de flexión sin fatigarse
- Alta resistencia necesaria para soportar cargas de conformado
- La resistencia determina los diámetros admisibles de los rodillos
Resistencia al desgaste
- Los materiales de los rodillos deben resistir los daños causados por la fricción
- Crítico para grandes volúmenes de producción
- Se utilizan aleaciones especiales si el material es abrasivo
Endurecimiento del trabajo
- La presión de contacto no debe endurecer excesivamente los rodillos
- Provoca daños en la superficie y baja calidad de las piezas
- Los revestimientos de baja fricción ayudan a superar este problema
Material | Descripción | Aplicaciones |
---|---|---|
Acero endurecido | Acero al carbono medio, tratado térmicamente | El más común, utilizado para la mayoría de los metales |
Adamita | Fundición centrifugada de hierro con alto contenido en níquel | Aceros al carbono y HSLA de alta producción |
Caucho/Poliuretano | Rodillos de uretano o caucho de alta dureza | Metales sensibles como cobre, latón, aluminio |
Hierro | Fundición dúctil, distintas durezas | Rodillos de preformado, metales de baja dureza |
También se utilizan combinaciones de materiales en una misma máquina, con soportes de preconformado de hierro y soportes de acabado de acero. Los rodillos de goma/uretano ayudan a conformar metales blandos reduciendo la fricción.
La selección adecuada del material de los rodillos garantiza un bajo índice de desgaste y la capacidad de soportar las altas presiones que se producen en el perfilado. De este modo, se obtienen volúmenes de producción máximos y se minimiza el reafilado o la sustitución de los rodillos.
Aplicaciones de perfilado
El perfilado se utiliza para producir una amplia variedad de piezas en todos los sectores industriales:
Construcción
- Paneles de pared, revestimientos, tejados, montantes, vigas
- Barandillas, marcos, soportes solares, sistemas de drenaje
- Ángulo, tubo, canales para estructuras
**Automoción **
- Vigas de puerta, barras de techo, soportes, travesaños
- Armazones de asiento, estribos, parachoques
- Componentes de la tapicería exterior
**HVAC **
- Conductos de aire y accesorios
- Canalones, rejillas, registros, difusores
Manipulación de materiales
- Bastidores, estanterías, cintas transportadoras
- Carros, contenedores, taquillas, armarios de almacenamiento
Muebles
- Marcos, armarios, estantes, asas
- Escritorios, archivadores, mobiliario comercial
Eléctrico
- Luminarias, bandejas de cables, cajas de empalmes
- Carcasas de paneles, canaletas, bastidores fotovoltaicos
Transporte
- Enganches, barandillas, peldaños, bastidores para camiones y remolques
- Barreras de seguridad vial
Además, los perfiles arquitectónicos decorativos, los expositores, las exposiciones, la señalización y los paneles de carrocería de vagones de ferrocarril y camiones se suelen conformar con rodillo.
La flexibilidad para crear secciones transversales abiertas ilimitadas hace que el perfilado sea ideal para producir tanto piezas normalizadas como personalizadas.
Comparación del perfilado con otros procesos
El perfilado tiene ventajas y limitaciones en comparación con otros procesos de conformado de metales:
Frente al plegado con plegadora
- Menor coste de equipamiento que las grandes plegadoras
- Sin costes de utillaje para matrices de doblado
- Mayor rendimiento
- Limitadas a perfiles abiertos, las plegadoras pueden hacer formas cerradas
- Tamaño limitado en el perfilado por la capacidad de la máquina
- Prensas plegadoras Cambio más rápido entre piezas
- Las prensas plegadoras pueden tener límites de material más gruesos
Versus Estampación
- Costes de utillaje muy inferiores a los de las matrices de estampación
- Posibilidad de lotes pequeños frente a la estampación optimizada para grandes volúmenes
- Mayor aprovechamiento del material en el perfilado
- Más limitaciones de tamaño en la estampación
- El estampado puede producir formas de sección cerrada que no son posibles con el perfilado
- Mayor coste inicial del equipo de perfilado
Versus Extrusión
- El utillaje de bajo coste ofrece flexibilidad de laminado para cambiar piezas
- La extrusión sólo produce una sección transversal fija en longitudes continuas
- El perfilado tiene límites de anchura en función de la capacidad de la máquina
- La extrusión no es práctica para series cortas
Corte por láser o chorro de agua
- Sin zona afectada por el calor ni alabeo como en el corte por láser
- Bajo desperdicio de material en comparación con la pérdida de chatarra por cizallamiento
- Capaz de producir con flexibilidad formas cerradas a medida, a diferencia del perfilado
- Posibilidad de plazos de entrega muy cortos con la preparación de herramientas de corte frente a la de rodillos
- Sin limitaciones de forma o grosor como en el perfilado
Considerar tanto las ventajas como las limitaciones ayuda a determinar la selección óptima del proceso para una aplicación de producción. El perfilado ofrece ventajas para series largas, dado el elevado coste inicial de la máquina.
Defectos de perfilado
Algunos defectos potenciales que pueden producirse en el perfilado:
Pandeo
- Ondulaciones o arrugas a lo largo del alma o de la brida
- Debido a una compresión excesiva
- Relación anchura/espesor inadecuada
- Aumentar la presión de retención
Torsión
- El perfil acabado se tuerce longitudinalmente
- Rodillos mal alineados
- Espaciado inadecuado entre los soportes de los rodillos
- Ajustar la alineación del rodillo
Foldover
- La brida formada se pliega sobre el alma
- Compresión excesiva
- Aumentar el diámetro del rodillo inferior
Marcas superficiales
- Huellas de rodillo visibles en las superficies
- Presión excesiva del rodillo
- Instale
Dividir
- Grietas a lo largo del eje neutro del perfil conformado
- El metal supera los límites de ductilidad en el conformado
- Aumentar el radio en la deducción de la curva
- Ajustar el calendario de pasadas
Abocardado
- Las bridas formadas se extienden hacia fuera
- Insuficiente contención del rollo
- Rodillos superior e inferior desalineados
- Ajustar la alineación del rodillo
Sin relleno
- La banda no entra en contacto con el rodillo inferior
- Evitar la formación completa
- Rodillos desgastados o dañados
- Aumentar el diámetro del rodillo
Springback
- La forma de la pieza no se mantiene después de salir del último soporte
- Recuperación elástica del metal
- La sobreflexión y la sobreformación pueden compensar
Variación del grosor
- Espesor de material incoherente a lo largo de la pieza
- Relación inadecuada entre los rodillos
- Aumentar el diámetro del rodillo inferior
Daños superficiales
- Abolladuras, desportilladuras, arañazos en las zonas formadas
- Acumulación de residuos en los rodillos que provoca marcas
- Lubricar el material o los rodillos
- Superficies limpias de los rodillos
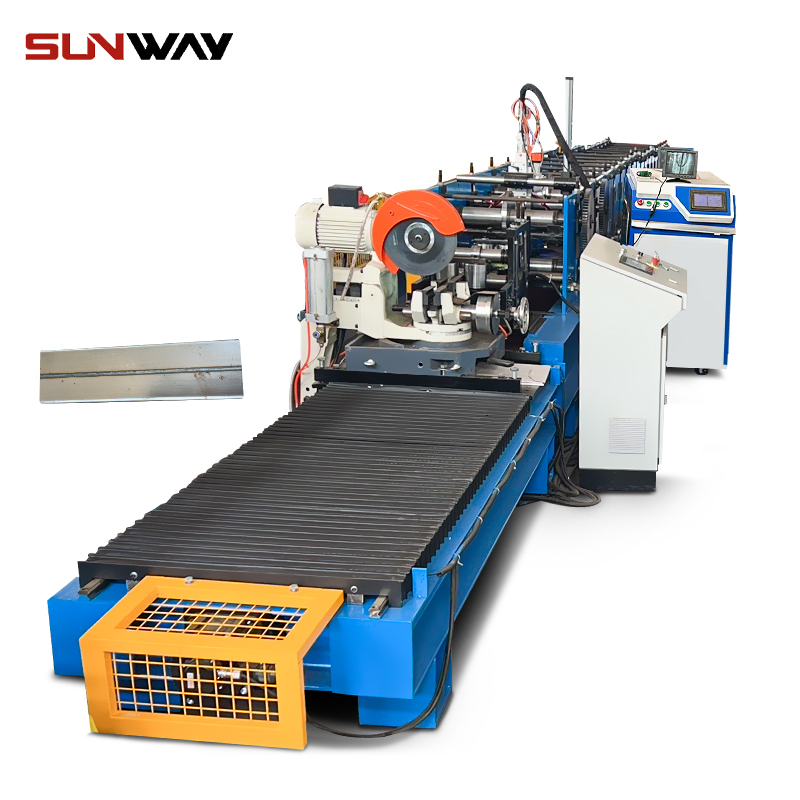
Lubricación en el perfilado
La lubricación es fundamental en el perfilado para:
- Reducir la fricción entre los rodillos y la chapa
- Facilitan el plegado y el flujo de material
- Evitar daños en la superficie de los perfiles conformados
Beneficios de una lubricación eficaz:
- Menores cargas de conformado en los rodillos y el utillaje
- Evita el gripado y la transferencia de material a los rodillos
- Mayor velocidad de línea y producción
- Mejorar la calidad superficial de las piezas acabadas
- Reduce el desgaste de los rodillos para maximizar la vida útil
Métodos habituales de lubricación:
Lubricación de rodillos
- Lubricante directo aplicado a las superficies de los rodillos
- Sistemas de goteo para mantener los rollos recubiertos
- Reduce la fricción cuando la hoja se engancha a los rodillos
Lubricación de existencias
- Chapa o bobina recubierta antes del desenrollador
- Cantidad correcta aplicada a toda la producción
- Lubricación constante en todos los soportes
Rociador
- Lubricación por niebla de aire pulverizada sobre superficies
- Baja cantidad distribuida uniformemente
- Aplicación limpia sin acumulación excesiva
Entornos
- Sistemas para rociar aceite o refrigerante internamente
- Contribuir a una calidad del aire más limpia en el taller
Los lubricantes sintéticos se utilizan habitualmente para el perfilado en lugar de productos a base de aceite. Ofrecen un funcionamiento limpio, una larga vida útil y una mínima suciedad para manipular las piezas conformadas. Los sistemas de reciclaje adecuados pueden prolongar la vida útil de los lubricantes sintéticos en el perfilado.
Operaciones secundarias
A menudo se realizan operaciones secundarias en las piezas perfiladas:
Corte
- Cizallado o aserrado a longitudes finales acabadas
- Perforación para sujetadores o perchas
- Muescas y ranuras para encajar otros componentes
- Recorte y desbarbado de bordes para cosméticos
Doblar
- Pestañas finales, bridas, soportes añadidos con prensas plegadoras
- Enclavamientos formados y cavidades para conexiones
- Dobladillos y costuras de unión de paneles
Acabado
- Pintura y recubrimiento en polvo para mejorar el aspecto y la protección
- Galvanizado o chapado en caliente para resistir la corrosión
- Imprimación y pasivación de metales como el acero inoxidable
Hardware
- Adición de tuercas empotradas, espárragos, fijaciones cautivas
- Clips de montaje, soportes y abrazaderas instalados
Montaje
- Unión de perfiles perfilados a paneles o bastidores
- Integración de aislamiento, vidrio, electrónica e iluminación
- Soldadura y fijación de componentes adicionales
Estos procesos secundarios ayudan a crear piezas acabadas o subconjuntos a partir de los perfiles laminados. La automatización permite integrar múltiples operaciones en una línea de producción continua.
Proveedores de equipos de perfilado
Algunos de los principales fabricantes de equipos de perfilado son:
- Maquinaria Samco - Gama completa de perfiladoras para aplicaciones de producción y prototipos
- Metform Internacional - Perfiladoras para una amplia gama de industrias
- Dahlstrom Motors - Ingeniería y fabricación de laminadoras a medida
- Formtek - Perfiladoras para HVAC, drenaje, paneles, estanterías, automoción
- Grupo Bradbury - Proveedor líder de equipos de procesamiento de chapas planas y bobinas
- Shibo Ingeniería Mecánica - Fabricante taiwanés de perfiladoras
- Maquinaria Comet - Perfiladoras de producción y máquinas de ruedas portátiles
- KNUTH - Máquinas y herramientas alemanas de perfilado
- Botou Xianfa - Fabricante de equipos de perfilado de China
- EZForm - Fabricante canadiense líder de perfiladoras
Al seleccionar el equipo de perfilado, los factores importantes a considerar incluyen:
- Anchura de conformado y capacidad de espesor necesaria
- Longitud total de la máquina en función de las dimensiones de la pieza
- Número de portabobinas necesarios para la forma del perfil
- Índices y volúmenes de producción
- Controles, automatización, facilidad de configuración
- Disponibilidad de servicios de diseño de rollos
- Experiencia con aplicaciones similares
- Presencia mundial de servicio y asistencia
Los principales fabricantes de laminadoras ofrecen asistencia completa en el diseño y servicios de utillaje para laminadoras, además del equipo de conformado.
Costes de perfilado
La economía del perfilado:
Coste de la máquina
- De $50.000 a $500.000+ en función del tamaño y las características
- Las máquinas más grandes, automatizadas y con más funciones cuestan más
Coste de utillaje
- De $2.000 a $20.000+ por juego de herramientas
- Más portabobinas y más complejidad aumentan el coste
**Coste de explotación **
- Mano de obra 1-2 operarios normalmente para carga/descarga
- Bajos costes de mantenimiento y sustitución de herramientas
- Consumo de energía ~50-100 kWh por tonelada de producción
Tasas de producción
- Hasta 200 pies/min de velocidad de línea en máquinas de alta velocidad
- De 10.000 a 100.000+ pies por turno posibles
Periodo de amortización
- ~1-3 años después de la cantidad de equilibrio
- Importante para grandes volúmenes de producción
- Larga vida útil de las máquinas: más de 20 años
Coste por pieza
- $0,10 a $2 por pieza según la complejidad
- La economía mejora con mayores volúmenes gracias a los bajos costes de funcionamiento
El perfilado resulta económico para grandes lotes de producción, normalmente de más de 50.000 piezas. Para cantidades inferiores, otros procesos como el corte por láser o la plegadora pueden resultar más rentables. La flexibilidad del perfilado permite producir grandes y pequeños volúmenes en la misma máquina.
Control del proceso de perfilado
Un control eficaz del proceso garantiza una alta calidad y productividad en el perfilado:
Velocidad de línea
- Velocidad de producción y rendimiento directamente ligados a la velocidad de la línea
- Velocidad optimizada para equilibrar rendimiento y calidad
Presión del rodillo
- Se necesita una presión adecuada para un buen conformado
- El exceso de presión provoca defectos y desgaste de los rodillos
- Los sensores de fuerza ayudan a optimizar la presión
Tensión de banda
- Suficiente tensión necesaria para una alimentación suave
- Minimiza el pandeo y favorece el flujo de material
- Las células de carga de la banda controlan la tensión
Desgaste de rodillos
- Los rodillos desgastados provocan errores de marcado y dimensionales
- Los sistemas de medición de rodillos en línea detectan el desgaste
- Sustitución de rodillos en función de indicadores
Lubricación
- Una lubricación adecuada evita arañazos
- Los sensores verifican los niveles adecuados de lubricante
- Las bombas modulan el caudal en función de la velocidad de la línea
Automatización
- Autómatas programables máquinas de coordenadas
- Pantallas e interfaces HMI para control
- Los diagnósticos controlan el estado del proceso
Las modernas perfiladoras emplean una supervisión exhaustiva y controles en red para mantener automáticamente unas condiciones óptimas de conformado. De este modo se evitan los rechazos, se maximizan los índices de producción y se reducen los tiempos de inactividad.
Problemas comunes en el perfilado
Algunos problemas frecuentes en el perfilado y cómo resolverlos:
Problema: Torsión del perfil conformado
Solución: Asegurar la correcta alineación de los rodillos; Aumentar la distancia entre los soportes de los rodillos; Comprobar el paralelismo de los rodillos.
Problema: Distorsión del perfil tras salir del último puesto
Solución: Aumentar el diámetro del rodillo inferior; emplear soportes de rodillo para el perfil acabado
Problema: Volteo de la brida durante el conformado
Solución: Reducir la compresión; Aumentar la anchura de la pestaña; Comprobar el contorno del rodillo
Problema: La banda no toca el rodillo inferior
Solución: Aumentar el diámetro del rodillo inferior; Ajustar el programa de pasadas del rodillo
Problema: Carga excesiva en cajas de cambios y utillaje
Solución: Lubricar el material; Reducir la velocidad de la línea; Comprobar la alineación del rodillo
Problema: Marcas de rodillo visibles en la superficie encofrada
Solución: Sustituir los rodillos dañados; Aumentar la lubricación; Reducir la presión de los rodillos
Problema: División a lo largo de las uniones del alma y el ala
Solución: Aumentar los radios de curvatura; Utilizar más soportes de preformado; Comprobar la ductilidad del material
Problema: Tolerancias de perfil deficientes
Solución: Tener en cuenta la recuperación elástica en el diseño de los rodillos.
Problema: Arañazos en piezas conformadas
Solución: Limpiar las superficies de los rodillos; Mejorar la lubricación; Comprobar la calidad de la superficie del material
Seguridad en el perfilado
Prácticas de seguridad para las operaciones de perfilado:
- Encerrar los portarrollos en protecciones
- Puertas de acceso con enclavamiento que apagan la máquina si se abren
- Rotular de forma visible los botones de parada de emergencia
- Sensores para detener el funcionamiento si se detecta una parte del cuerpo
- Procedimientos de bloqueo y etiquetado para el mantenimiento
- Utilice cepillos o embudos para el lubricante en lugar de manipularlo directamente
- Equipos para la elevación y manipulación seguras de herramientas pesadas
- Los trabajadores llevan el EPI adecuado: gafas de seguridad, guantes, ropa no holgada
- Ventilación adecuada para controlar la neblina de aceite y los humos
- Aislamiento de zonas muy ruidosas con cerramientos acústicos
- Inspecciones periódicas de herramientas, protecciones, sensores, enclavamientos
- Formación sobre procedimientos operativos seguros y precauciones
- Establezca zonas de seguridad y restrinja el acceso cerca de la máquina
El perfilado implica riesgos significativos derivados de las piezas giratorias, las altas presiones y los bordes afilados. Seguir unas prácticas de seguridad exhaustivas es fundamental para evitar lesiones. Deben aplicarse medidas de protección de las máquinas, procedimientos de bloqueo, formación de los trabajadores y uso de EPI.
Control de calidad de perfilado
Prácticas de control de calidad en el perfilado:
- Inspección de la primera pieza del perfil conformado
- Comprobaciones dimensionales con calibres y MMC
- Control de la variación del espesor a lo largo de la pieza
- Inspección del acabado superficial de las zonas conformadas
- Examen visual para detectar defectos
- Control de las cantidades correctas de lubricación
- Medición de la anchura del alma, del ala y de los ángulos de curvatura
- Verificación de las longitudes de corte y de la calidad de la perforación
- Comprobación de torsión, curvatura y planitud
- Pruebas de funcionamiento para validar nuevas herramientas y cambios en los procesos
- Control estadístico de procesos Seguimiento de defectos
- Análisis de las capacidades de las dimensiones críticas
- Documentación de los parámetros y tolerancias del proceso
- Formación de los operarios sobre los procedimientos de inspección
- Acciones correctivas cuando se producen defectos
Con las medidas de control de calidad adecuadas, la repetibilidad del proceso de perfilado garantiza la producción constante de piezas dentro de las tolerancias requeridas. El seguimiento estadístico ayuda a identificar áreas de mejora.
Resolución de problemas en el proceso de perfilado
Técnicas de localización de averías cuando surgen problemas en el perfilado:
- Parar la máquina e inspeccionar primero cuidadosamente la sección formada
- Revisar los cambios o ajustes recientes en los procesos
- Comprobar el desgaste de los rodillos, las cantidades de lubricación y la alineación de las bandas.
- Verificar las propiedades y el estado del material en stock
- Intente reducir la velocidad de la línea gradualmente
- Ajustar las presiones y la alineación de los portabobinas individuales
- Estudiar el diseño del paso de rodillos y la configuración de las herramientas
- Revisar la formación de los operarios y el cumplimiento de los procedimientos
- Analizar la causa raíz del defecto específico observado
- Pequeños lotes piloto para aislar sistemáticamente el problema
- Inspección y medición del perfil conformado en varias ubicaciones
- Iterar el utillaje sólo para problemas crónicos una vez agotados otros remedios.
- Consulte a expertos en diseño de rodillos para solucionar problemas de conformado difíciles
- Considerar el ensayo de materiales si los defectos se deben a la composición
- Documentar todas las conclusiones y medidas correctoras adoptadas
Una cuidadosa localización de averías ayuda a identificar los factores que contribuyen a un problema de perfilado. Para centrarse exclusivamente en el utillaje, hay que tener en cuenta otras posibles causas relacionadas con el material, los métodos, el personal o la máquina.
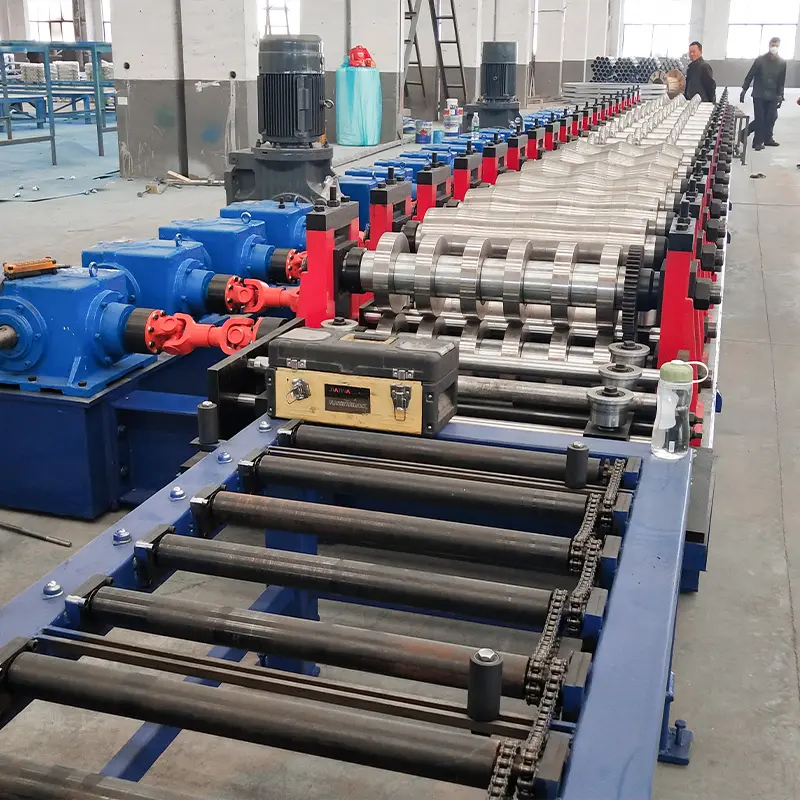
Normas de la industria de perfilado
Las normas de perfilado guían las especificaciones de los equipos, el diseño y el control de calidad:
ASTM A924 - Norma para las chapas de acero utilizadas en el perfilado
ASTM B136 - Norma para materiales de banda de latón para perfilado
AISI D100 - Directrices y tolerancias de perfilado
AWS D1.3 - Directrices de soldadura para máquinas y piezas perfiladas
NSSGA - Guía de perfilado para productos de la industria de los áridos
AISI SG03-3 - Directrices para la estructura de acero conformado en frío
ASTM E290 - Métodos de ensayo de piezas conformadas por laminación
ISO 11562 - Medidas lineales de piezas perfiladas
JIS Z1701 - Métodos de ensayo para productos laminados
Especificación API 5CT - Especificaciones para tuberías de revestimiento y de producción
SAE J136 - Métodos de ensayo de lubricantes
El cumplimiento de las normas del sector garantiza que las piezas perfiladas cumplan las especificaciones exigidas en parámetros como materiales, diseño, dimensiones, pruebas y unión.
Preguntas más frecuentes
P: ¿Qué metales pueden laminarse?
R: El perfilado puede conformar aceros, aceros inoxidables, aluminio, cobre, latón y otros metales dúctiles dentro de los límites de espesor y anchura de la máquina.
P: ¿Qué espesores se pueden laminar?
R: El grosor típico oscila entre calibre 18 y 1/4 pulg. Las máquinas más grandes pueden laminar material de hasta 2,5 cm de grosor. El grosor mínimo oscila entre calibre 26 y 30.
P: ¿Qué tolerancias se pueden alcanzar?
R: Las piezas conformadas por laminación suelen tener tolerancias de +/- 1% de espesor de material. Algunas dimensiones pueden tener tolerancias más estrechas.
P: ¿Qué longitud puede tener una sola pieza perfilada?
R: Las longitudes de producción oscilan entre secciones de 2 y 25 pies, dependiendo del tamaño de la máquina. En teoría, son posibles longitudes ilimitadas.
P: ¿Qué metales requieren lubricación?
R: Lubricación recomendada para la mayoría de los metales, excepto el acero inoxidable. Especialmente útil para latón, cobre y aluminio.
P: ¿Afecta la dirección del grano al perfilado?
R: Sí, el curvado es más fácil transversalmente a la dirección del grano. Por lo general, los perfiles se perfilan en paralelo a la orientación original del grano.
P: ¿Cuántos operarios se necesitan?
R: Normalmente 1-2 operarios - uno en el desenrollador y otro en el extremo de salida. Las máquinas automatizadas pueden no necesitar operario.
P: ¿Cómo de rápidos son los cambios entre perfiles?
R: Los cambios de rodillo y utillaje pueden llevar entre 4 y 8 horas. Algunos utillajes de cambio rápido reducen sustancialmente este tiempo.
P: ¿Qué determina las tolerancias de los perfiles?
R: Las tolerancias dependen de las propiedades del material, la rigidez del utillaje, el número de soportes de rodillos, la lubricación y la velocidad de la línea.
P: ¿Qué limita la anchura máxima?
R: El tamaño del bastidor de la máquina, la rigidez del portabobinas y la potencia de conformado limitan la anchura máxima. Hasta 120 pulgadas en las máquinas más grandes.
P: ¿Qué formas complejas se pueden formar?
R: El perfilado destaca en la alta producción de formas uniformes abiertas. Las plegadoras son mejores para tiradas cortas de perfiles complejos.
P: ¿Qué causa los arañazos en la superficie encofrada?
R: Acumulación de residuos en el trabajo o en el utillaje, lubricación deficiente, utillaje dañado, presiones de rodillo inadecuadas.
P: ¿Por qué es un problema el springback?
R: La recuperación elástica tras la flexión provoca una distorsión de la forma. El exceso de flexión y el apoyo del rodillo inferior pueden compensarlo.
P: ¿Cómo se añaden los agujeros y las muescas?
R: El punzonado, la entalladura o el corte por láser se utilizan después del perfilado para crear agujeros y recortes con la forma necesaria.
P: ¿Por qué el perfilado es más económico que otros métodos?
R: No se necesitan troqueles y los costes de funcionamiento son bajos. Los costes de instalación se amortizan en largas series de producción. Alto aprovechamiento del material.