Roll forming machines are used to produce long sheet metal profiles with complex cross-sections. One common application is the production of ridge caps used in roofing. A ridge cap is the metal piece that sits at the peak of a roof and covers the intersection where two sloping sections meet. Ridge caps help protect this vulnerable part of the roof from water infiltration.
How Ridge Caps Are Used in Roofing
Ridge caps serve several important functions for roof performance and durability:
- Provide an extra barrier to prevent rain, snow, and debris from entering at the roof ridge
- Cover up the seam where two roof planes intersect to create a clean, finished look
- Anchor the ends of the roofing material on either side
- Allow for expansion and contraction of the roof deck and material due to temperature changes
Ridge caps are commonly made from galvanized steel, aluminum, copper, or other metal alloys. The material type depends on the type of roofing material being used, desired lifespan, and architectural aesthetics.
They are designed to overlap the roofing material along both sides of the roof ridge. The cap is often fastened with exposed screws, nails, or clips to provide a decorative touch and ensure it is securely attached. Caps may feature venting holes to allow warm air to escape the attic space.
Overall, ridge caps protect the most vulnerable area of the roof from weather damage, add an attractive finishing touch, and help extend the roof’s lifespan.
How Ridge Caps Are Formed by Roll Forming Machines
Roll forming is an ideal process for producing ridge caps and other long sheet metal components with custom cross-sections. Here is an overview of how roll forming machines create ridge caps:
Continuous Process
- Roll forming is a continuous process rather than stamping each part individually. This allows for fast production of ridge caps in long lengths.
Shaping Through Rollers
- Sheet metal coils are fed into the roll forming machine. The sheet passes through a series of roller stations.
- Rollers are machined to gradually bend and shape the sheet into the desired ridge cap profile.
- With each progressive rolling station, the sheet is bent and formed a little more until reaching the final cap shape.
Efficient Use of Material
- Roll forming allows ridge caps to be produced with minimal material waste compared to stamping.
- The sheet is precisely formed to the desired shape and width without cutting away material.
- Roll forming may produce ridge caps with decorative ribs or contours to enhance rigidity with thinner material.
Versatile for Different Profiles
- Roll sets can be switched out on the machine to produce different ridge cap configurations.
- Various cap widths, rib patterns, and side angles can be formed.
- Quick roll set changeovers allow for efficient production of various roofing accessories.
Continuous Cap Lengths
- Ridge caps are produced in long continuous lengths rather than individual pieces.
- Lengths are simply cut to the specific size later after forming.
- Roll formed ridge caps can be made in 20+ foot sections for fewer seams on long roofs.
Overall, roll forming provides an optimal automated process for mass producing custom ridge caps that would be complicated and slow to make with stamping or manual methods.
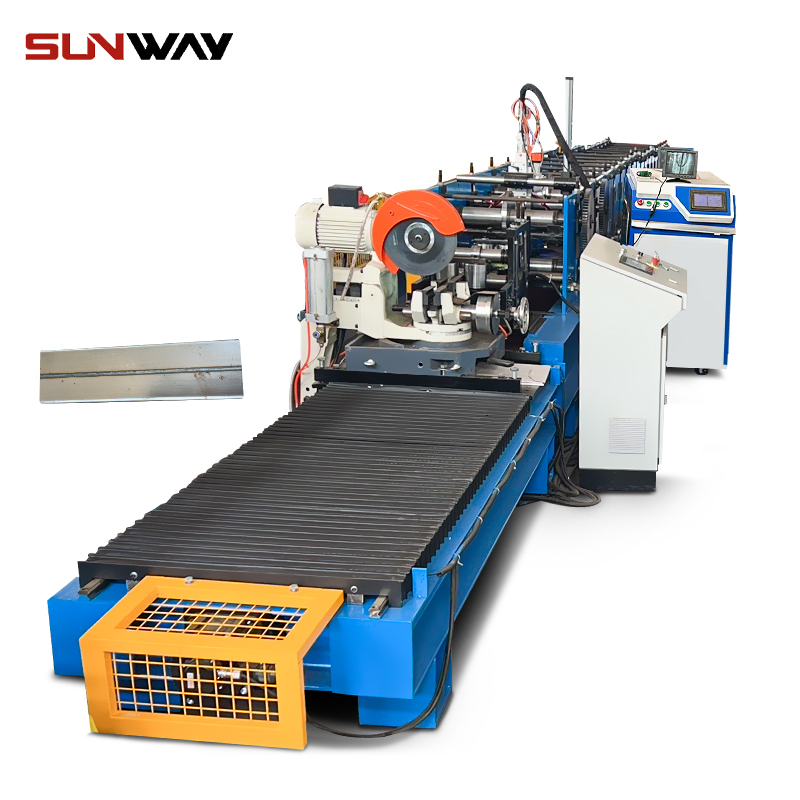
Key Components of a Ridge Cap Roll Forming Machine
Roll forming machines contain a series of equipment modules and components that work together to shape sheet metal coils into formed parts like ridge caps:
Uncoiler
- Holds a large coil of flat sheet metal to be fed into the roll forming section.
- Smoothly unrolls and guides the sheet off the coil into the rollers.
- Includes mechanisms to maintain proper tension on the uncoiling sheet.
Feed Table
- Provides an extended surface for smoothly feeding the metal sheet into the rolling stations.
- Allows for stable material feed at the start of the forming process.
Roller Stations
- Contain machined rollers specifically designed to progressively shape the sheet.
- Number of roller stations varies based on complexity of the part profile.
- Ridge caps typically require 10 – 25 rolling stations for full forming.
Forming Rollers
- Hardened steel rollers machined to precise shapes matching the desired profiles.
- Rollers apply pressure to bend the sheet a small increment with each station.
- Top and bottom rollers rotate in sync to progressively form the sheet.
Guide Roller Assemblies
- Support and guide the sheet through the rolling stations while allowing feeding.
- Help control sheet alignment and prevent sideways drift during forming.
- Guide rollers rotate freely to avoid surface marking defects.
Shear Station
- Automatically cuts the formed ridge caps once they reach the desired length.
- Precise length control helps minimize material waste after forming.
- Shearing blades are designed for clean cuts without deforming the cap profile.
Exit Conveyor
- Receives the finished cut ridge caps and conveys them out of the machine.
- Allows formed parts to gently stack for easy unloading.
Control System
- Automates and monitors the roll forming process for consistency.
- Allows operators to set forming parameters and program jobs.
- Interlocked safety controls help prevent unsafe operating conditions.
Design Factors for Quality Ridge Cap Production
Producing strong, durable ridge caps via roll forming requires careful design consideration in several areas:
Roll Tooling Design
- Rollers must be precision machined to match the desired cap profile and angles.
- Roller contours control material flow to avoid thinning and tearing during forming.
- Proper roll design distributes material evenly to maintain uniform cap thickness.
Material Thickness
- Ridge cap material thickness is selected based on roofing type and load requirements.
- Thicker material (0.032+ in) may be needed for heavy tile roofs to avoid deformation.
- Thinner material can be used for lighter composite shingle and metal roofs.
Number of Rolling Stations
- More stations make for gradual forming and lower rolls forces on the material.
- 12 – 18 stations are typical for most ridge cap profiles.
- Highly complex or extruded profiles may require 20+ stations.
Rolling Speed
- Slower sheet feeding spreads forming across more stations for better control.
- Faster rolling requires optimal roller design to avoid defects.
- Speed is set based on cap profile complexity and machine capability.
Sheet Metal Properties
- Ductile sheet with good formability characteristics avoids cracking issues.
- Pre-painted materials require lubrication and special handling to minimize scratches.
- Brittle and ultra-high-strength alloys are more difficult to successfully form.
Careful engineering of these parameters results in a robust roll forming process capable of efficient, high-quality ridge cap production.
Standard vs Custom Ridge Cap Roll Forming Machines
Roll forming machines for roofing products are available in standard catalog models or custom configurations:
Standard Ridge Cap Machines
- Mass produced models designed for common roofing applications.
- Typically make popular corrugated and ribbed ridge cap configurations.
- Use pre-designed common roll sets that are interchangeable.
- Offered in different size ranges based on output speed and sheet width needs.
- Provide an economical option for basic ridge cap production rolls.
Custom Ridge Cap Machines
- Designed and built to order for specialized roofing products.
- Engineered with custom roll sets for unique cap designs.
- Capable of complex profiles beyond standard machines.
- Built with extra roll stations, guides, and features as needed.
- Programmable for fast roll set changeovers between different caps.
- Allows manufacturers to create proprietary ridge cap designs.
- Higher machine investment but enables broader product offerings.
Standard machines work well for common ridge cap applications, while custom machines enable production of specialized roofing components that set a company apart in the market.
Technical Specifications to Look for in Ridge Cap Machines
Key technical factors to evaluate when purchasing ridge cap roll forming equipment:
- Sheet Width Capacity: Determines maximum cap width that can be formed. Common ranges are 18 – 24 inches for roofing.
- Sheet Thickness Capacity: Indicates the minimum and maximum material thicknesses the machine can accept.
- Roller Adjustment Range: The extent that top and bottom rollers can adjust to set different profile heights.
- Number of Rolling Stations: More stations allow for better control on complex shapes. 12 – 18 is typical.
- Roller Material and Hardness: Structural steel or alloy rollers with hardness between 50 – 65 HRC for long life.
- Maximum Rolling Speed: Production rates between 10 – 65 feet per minute are standard. Higher speeds possible with custom machines.
- Installed Power Requirements: Electical supply needs based on motor sizes and number of stations. Often 15 – 50 kW.
- Safety Features: Emergency stops, multi-sensor interlocks, guards, warnings, and other features.
- Programmable Controls: Touchscreen HMI and menus for fast setup between jobs. Memory storage for profiles.
- Connection to Coil Handling: Ability to integrate with uncoilers and straighteners enhances automation.
Reviewing these specifications against current and future production needs will help identify the optimal roll former configuration.
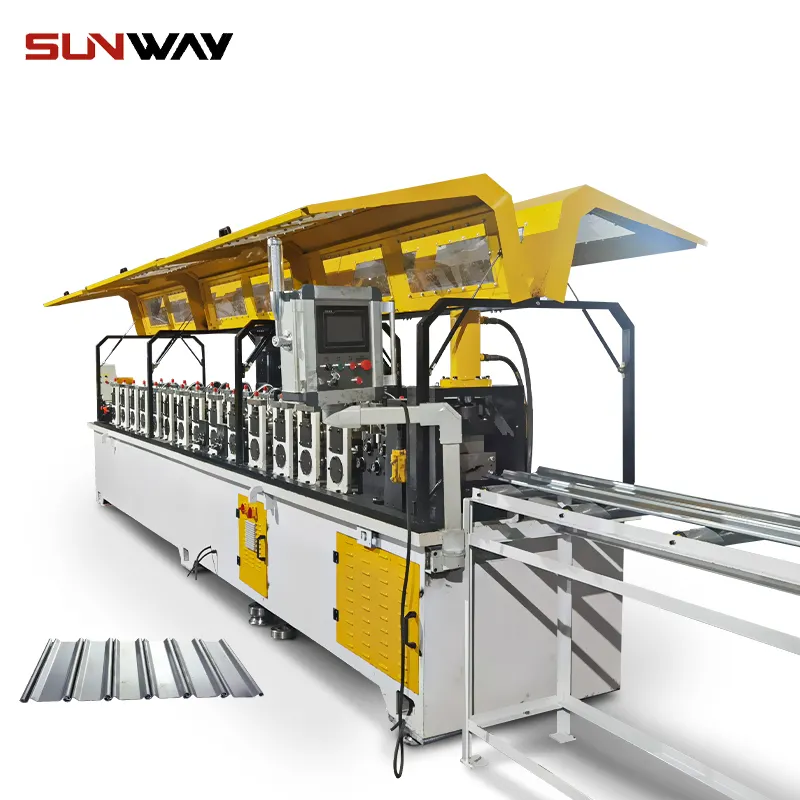
Leading Manufacturers of Ridge Cap Roll Forming Equipment
Some of the top global companies that engineer quality roll forming machines for roofing components like ridge caps include:
- Englert Inc – Offers standard and custom roofing roll formers. Machines for common and complex ridge caps. USA based.
- Formtek Group – Global leader in metal forming equipment. Roofing line includes the VersaCap ridge cap machine.
- Guess Steel Buildings Inc – Provides standard and custom ridge cap roll forming lines made in the USA.
- Metform International – Manufactures MetForm branded roll formers for roofing. Standard and custom ridge cap machines. Based in New Zealand.
- Samco Machinery – Supplies Mach I brand roll forming equipment. Stock and custom roofing roll former configurations.
- Shanghai Metal Corporation – China based company that produces quality standard and custom ridge cap roll forming equipment. Competitive pricing.
- Strippit Inc – Part of LVD Company. Offers S-series roof panel roll formers capable of ridge caps.
When investing in a ridge cap roll forming machine, it is wise to choose an established manufacturer with a track record of reliability in the roofing industry.
Conclusion
Roll formed ridge caps provide roofing contractors and building owners with an attractive and durable solution to cap off roof ridges and peaks while protecting them from rain infiltration. Automated ridge cap roll forming machines allow roofing component manufacturers to efficiently meet demand for these critical products with a variety of style and ventilation options. Properly specifying and operating a ridge cap roll former results in rapid production of straight, consistently formed metal caps that install cleanly and perform reliably on roofs for years of service life.
Roofers can trust roll formed ridge caps to deliver enhanced protection on all types of re-roofing and new construction projects while adding a touch of elegance to roof ridge lines. And for manufacturers, investing in ridge cap roll forming equipment opens up opportunities to profitably supply these high volume roofing accessories. Overall, roll formed ridge caps produced using the latest machine advancements provide benefits for the entire supply chain and improved roof performance for building owners.
FAQ
What materials can be roll formed into ridge caps?
- Many sheet metals can be roll formed into ridge caps including steel, aluminum, copper, zinc, and galvanized steel. Popular choices are hot-dipped galvanized, Galvalume coated steel, and pre-painted galvanized coils.
What thickness of metal should be used?
- For shingle roofs, 26 or 28 gauge steel between 0.018 – 0.032 inches is common. On heavy tile roofs, up to 22 gauge at 0.034 inches may be recommended for strength.
How long of ridge caps can be formed in one piece?
- Roll formed ridge caps are made in continuous lengths over 20 feet long, versus 4 – 10 feet for stamped caps. Longer caps mean fewer seams on the roof ridge.
How fast can ridge caps be produced?
- Standard roll forming speeds are 10 – 65 linear feet per minute. So a 20 ft cap can be formed every 20 – 120 seconds. Custom machines may achieve up to 100 ft/min for high volume production.
How are designs changed for different ridge cap profiles?
- Interchangeable roll sets are used containing top and bottom rollers machined for each specific profile. Roll sets can be swapped in 1 – 4 hours to switch designs.
Can decorative elements be added to ridge caps?
- Yes, roll forming allows for ribs, contours, embossing, and other decorative elements to be formed into the caps for unique designs and extra rigidity.
How are ventilation holes added to ridge caps?
- Punch or lancing stations are incorporated into the roll former to punch vent holes along the length of the cap during the forming process. Hole size, shape and spacing can be customized.