Z Purlin Machines are specialized equipment used to manufacture Z-shaped cold-formed steel structural components called Z purlins. These purlins are widely utilized in the construction industry for supporting roof decks, wall panels, and other structural elements in industrial, commercial, and residential buildings.
Z purlins are characterized by their distinctive zigzag or Z-shaped cross-section, which provides enhanced load-bearing capacity and structural integrity. The Z purlin roll forming machine is designed to take flat steel coils or sheets as input material and progressively shape them through a series of precision rollers, ultimately producing the desired Z purlin profile.
The process of roll forming Z purlins involves unwinding the steel coil, straightening the material, and then passing it through a series of consecutive roller stations. Each roller station is responsible for gradually bending and shaping the steel strip until it takes on the desired Z purlin configuration. The final stage often involves cutting the formed Z purlins to the required lengths using an integrated or separate cutting mechanism.
Z purlin roll forming machines are highly automated and can produce consistent, high-quality Z purlins at rapid rates, making them an essential piece of equipment for steel construction companies, metal building manufacturers, and other related industries.
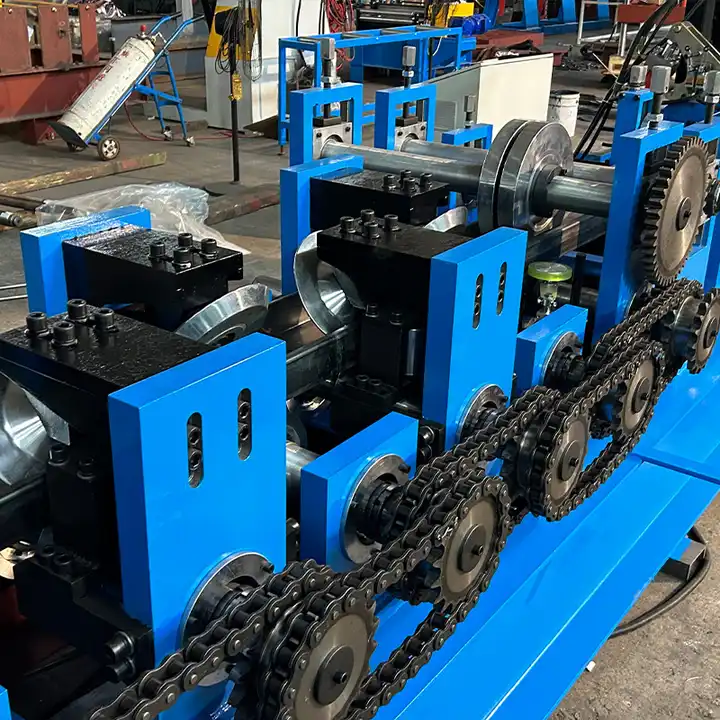
Z Purlin Machine: Types and Configurations
Z purlin roll forming machines come in different configurations to meet the diverse needs of manufacturers and construction projects. Here’s a table outlining the various types of Z purlin machines:
Machine Type | Description |
---|---|
Entry-Level Z Purlin Machines | Suitable for small-scale operations or startups, these machines offer basic functionalities and are typically more affordable. |
Mid-Range Z Purlin Machines | Designed for medium-sized manufacturing facilities, these machines strike a balance between advanced features and cost-effectiveness. |
High-End Z Purlin Machines | Equipped with cutting-edge technology and advanced capabilities, these machines cater to large-scale construction projects and high-volume production demands. |
Customized Z Purlin Machines | Tailored to meet specific project requirements or unique Z purlin profiles, these machines are designed and built according to customer specifications. |
The choice of machine type depends on factors such as production volume, project scope, budget, and the desired level of automation and precision.
Z Purlin Machine: Working Principle
The working principle of a Z purlin roll forming machine revolves around a series of precisely calibrated roller stations that progressively shape flat steel coils or sheets into the desired Z purlin profile. Let’s break down the process step by step:
- Material Feeding: The machine begins by feeding a continuous strip of flat steel coil or sheet material into the entry point of the roller system.
- Straightening: To ensure precise forming, the steel strip undergoes a straightening process to eliminate any initial curvature or irregularities.
- Progressive Roll Forming: The straightened steel strip then enters the main roll forming section, where a sequence of roller stations gradually bends and shapes the material into the characteristic Z purlin profile. Each roller station is responsible for a specific stage of the forming process, gradually transforming the flat steel strip into the desired zigzag shape.
- Punching and Cutting: Depending on the machine configuration, additional stations may be included to perform operations such as punching holes for fasteners or cutting the formed Z purlins to the required lengths.
- Stacking and Packaging: The finished Z purlins are then stacked or packaged for transportation and delivery to construction sites or further processing facilities.
Throughout the roll forming process, precise control over parameters such as roller alignment, material tension, and forming speed is crucial to ensure consistent and high-quality Z purlin production.
Z Purlin Machine: Material Feeding and Forming Capabilities
Z purlin roll forming machines are designed to handle a variety of steel materials, each with its unique characteristics and forming requirements. The table below outlines the common material types and their corresponding forming capabilities:
Material Type | Description | Forming Capabilities |
---|---|---|
Galvanized Steel Coils | Steel coils coated with a protective zinc layer for enhanced corrosion resistance. | Suitable for both light-duty and heavy-duty applications, these materials can be formed into a wide range of Z purlin profiles. |
Stainless Steel Coils | Highly durable and corrosion-resistant steel coils, often used in harsh or demanding environments. | Stainless steel coils can be formed into Z purlins for applications requiring superior corrosion resistance, such as coastal or chemical plant constructions. |
Pre-Painted Steel Coils | Steel coils with a pre-applied paint or coating, offering a range of color options and aesthetic finishes. | These coils can be formed into Z purlins for applications where appearance and color are important considerations, such as commercial or residential buildings. |
Aluminum Coils | Lightweight and corrosion-resistant aluminum coils, offering excellent strength-to-weight ratio. | Aluminum coils can be formed into Z purlins for applications where weight reduction is a priority, such as roofing systems or portable structures. |
The choice of material depends on factors such as project requirements, environmental conditions, load-bearing capacity needs, and aesthetic considerations.
-
Highway Guardrail End Terminal Forming Machine
-
Highway U/C Post Roll Forming Machine
-
2 Waves Highway Guardrail Roll Forming Machine
-
3 Waves Highway Guardrail Roll Forming Machine
-
Vineyard Post Roll Forming Machine
-
Auto Size Changeable Sigma Purlin Roll Forming Machine
-
Auto Size Changeable C Z Purlin Roll Forming Machine
-
Auto Size Changeable Z Purlin Roll Forming Machine
-
Auto Size Changeable C U Purlin Roll Forming Machine
Z Purlin Machine: Design and Customization Options
Z purlin roll forming machines offer various design and customization options to accommodate specific project needs and Z purlin profiles. The table below highlights some common customization features:
Customization Option | Description |
---|---|
Roller Configuration | The number, size, and arrangement of rollers can be customized to produce different Z purlin profiles or accommodate varying material thicknesses. |
Punching and Cutting Stations | Machines can be equipped with integrated punching and cutting stations to create holes for fasteners or cut Z purlins to precise lengths. |
Automation and Control Systems | Advanced automation and control systems can be incorporated for improved precision, efficiency, and ease of operation. |
Material Handling and Packaging | Customized material handling and packaging solutions can be integrated to streamline the production process and ensure efficient transportation and storage of Z purlins. |
Roller Surface Treatments | Rollers can be treated with specialized coatings or surface finishes to enhance durability, reduce friction, and improve forming quality. |
By customizing these features, manufacturers can tailor Z purlin roll forming machines to meet the specific requirements of their projects, ensuring optimal performance and output quality.
Z Purlin Machine: Industrial Applications
Z purlins manufactured by roll forming machines find widespread applications across various sectors of the construction industry. Here are some of the primary industrial applications:
- Industrial and Commercial Buildings: Z purlins are extensively used in the construction of industrial facilities, warehouses, retail centers, and other commercial buildings, providing structural support for roof decks and wall panels.
- Agricultural Structures: The durability and cost-effectiveness of Z purlins make them suitable for agricultural structures such as barns, storage facilities, and livestock shelters.
- Residential Construction: In residential projects, Z purlins can be employed in the construction of roofing systems, providing structural integrity and load-bearing capacity.
- Infrastructural Projects: Z purlins find applications in infrastructure projects, including bridges, overpasses, and other civil engineering structures, where structural strength and reliability are paramount.
- Modular and Prefabricated Buildings: The versatility of Z purlins makes them ideal for modular and prefabricated building systems, allowing for efficient transportation and assembly.
The widespread adoption of Z purlins in these diverse applications highlights the importance of reliable and efficient Z purlin roll forming machines in meeting the ever-growing demands of the construction industry.
Z Purlin Machine: Material Feeding and Straightening
Consistent and accurate material feeding and straightening are crucial steps in the Z purlin roll forming process. The table below outlines the key aspects of material feeding and straightening in Z purlin machines:
Aspect | Description |
---|---|
Coil Handling and Decoiling | Z purlin machines are equipped with robust coil handling and decoiling mechanisms to ensure smooth and controlled unwinding of the steel coil. This prevents material misalignment and ensures a consistent feed rate. |
Straightening Rollers | Straightening rollers are employed to remove any curvature or irregularities in the steel strip before it enters the roll forming section. This step is crucial for achieving precise forming and maintaining dimensional accuracy. |
Tension Control | Precise tension control systems are integrated to maintain the appropriate level of material tension throughout the feeding and straightening process. Proper tension ensures consistent material movement and prevents wrinkles or deformations. |
Material Guiding | Material guiding systems, such as roller tables or guides, ensure that the steel strip is properly aligned and fed into the roll forming section without any deviation or misalignment. |
Safety Features | Safety features, such as emergency stop buttons and guarding mechanisms, are incorporated to protect operators and prevent accidents during material feeding and straightening operations. |
By ensuring accurate material feeding and straightening, Z purlin roll forming machines can produce consistent and high-quality Z purlins that meet the stringent specifications required in the construction industry.
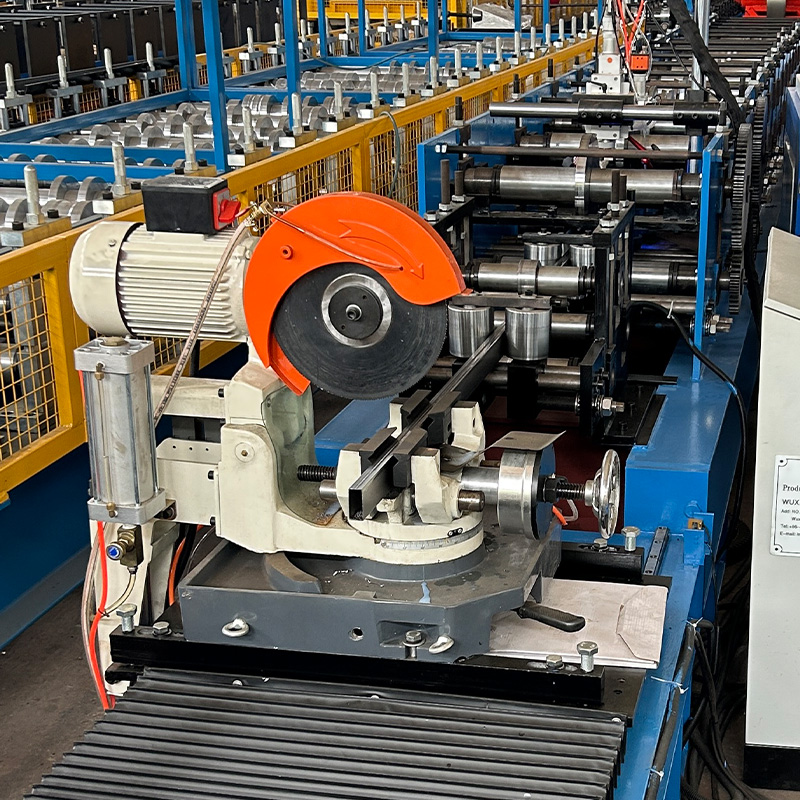
Z Purlin Machine: Roll Forming and Shaping
The heart of a Z purlin roll forming machine lies in its roll forming and shaping capabilities. This section of the machine is responsible for progressively transforming flat steel strips into the desired Z purlin profile. The table below outlines the key aspects of roll forming and shaping in Z purlin machines:
Aspect | Description |
---|---|
Roller Stations | A series of precisely calibrated roller stations are arranged in a specific sequence to gradually bend and shape the steel strip into the Z purlin profile. Each roller station is designed to perform a specific forming operation. |
Roller Configuration | The number, size, and arrangement of rollers in each station can be customized to produce different Z purlin profiles or accommodate varying material thicknesses and strengths. |
Roller Surface Treatments | Rollers may be treated with specialized coatings or surface finishes to enhance durability, reduce friction, and improve forming quality. This ensures consistent and precise forming over extended production runs. |
Forming Speed and Precision | Advanced control systems and servo motors allow for precise control over the forming speed and roller movements, ensuring accurate and consistent Z purlin profiles. |
Material Monitoring | Sensors and monitoring systems are employed to track the material’s progress through the roll forming section, ensuring proper alignment and detecting any potential issues or deformations. |
Adjustability and Changeover | Many Z purlin machines offer quick changeover capabilities, allowing manufacturers to easily switch between different Z purlin profiles or material types, improving production flexibility and minimizing downtime. |
By combining advanced roll forming technologies with precise roller configurations and control systems, Z purlin roll forming machines can produce high-quality Z purlins that meet the stringent structural and dimensional requirements of the construction industry.
Z Purlin Machine: Punching, Cutting, and Finishing
In addition to roll forming and shaping, many Z purlin machines incorporate punching, cutting, and finishing stations to enhance the functionality and versatility of the produced Z purlins. The table below outlines the key aspects of these operations:
Operation | Description |
---|---|
Punching | Punching stations are integrated into the machine to create precise holes or openings in the formed Z purlins. These holes are typically used for fasteners, allowing the Z purlins to be securely attached to other structural components during installation. |
Cutting | Cutting stations, often employing specialized blades or shears, are used to cut the formed Z purlins to the desired lengths. This ensures that the Z purlins meet the specific requirements of the construction project or application. |
Finishing | Depending on the application and customer requirements, Z purlin machines may include finishing stations for tasks such as deburring, chamfering, or applying protective coatings or paint to the formed Z purlins. |
Automation and Control | Advanced automation and control systems ensure precise positioning and synchronization of the punching, cutting, and finishing operations, ensuring consistent and accurate results. |
Material Handling | Integrated material handling systems, such as conveyors or stacking mechanisms, are employed to efficiently move the finished Z purlins to the next stage of the production process or packaging area. |
By incorporating these additional operations, Z purlin roll forming machines can provide comprehensive solutions, streamlining the manufacturing process and ensuring that the produced Z purlins meet all necessary specifications and requirements for their intended applications.
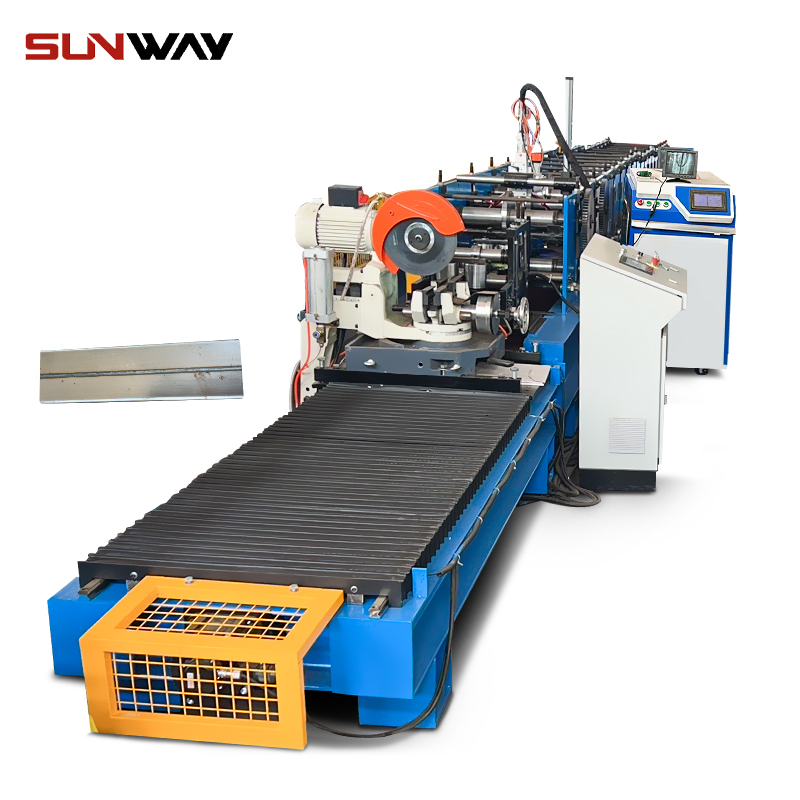
Z Purlin Machine: Stacking and Packaging
Once the Z purlins have been formed, punched, cut, and finished, they must be properly stacked and packaged for transportation and storage. The table below outlines the key aspects of stacking and packaging in Z purlin roll forming machines:
Aspect | Description |
---|---|
Stacking Mechanisms | Automated stacking mechanisms are employed to neatly and efficiently stack the finished Z purlins, ensuring proper alignment and minimizing the risk of damage during handling and transportation. |
Banding and Strapping | Banding or strapping systems are used to securely bundle stacks of Z purlins, preventing them from shifting or becoming dislodged during transportation or storage. |
Packaging Options | Depending on the customer’s requirements and the intended application, Z purlins can be packaged in various ways, such as wooden crates, metal containers, or wrapped in protective materials. |
Material Handling and Loading | Integrated material handling systems, such as conveyors or forklifts, facilitate the efficient movement and loading of packaged Z purlins onto trucks or storage areas. |
Labeling and Identification | Clear labeling and identification systems are employed to ensure proper tracking and inventory management of the packaged Z purlins, aiding in organization and reducing the risk of mix-ups or errors. |
By implementing efficient stacking and packaging systems, Z purlin roll forming machines can ensure the safe and secure transportation and storage of the produced Z purlins, minimizing the risk of damage and facilitating smooth logistics and inventory management.
Z Purlin Machine: Automation and Control Systems
Modern Z purlin roll forming machines are equipped with advanced automation and control systems to ensure precise and consistent production, as well as efficient operation. The table below outlines the key aspects of automation and control systems in Z purlin machines:
Aspect | Description |
---|---|
Programmable Logic Controllers (PLCs) | PLCs are the core control systems in Z purlin machines, responsible for coordinating and regulating various operations, such as material feeding, roll forming, punching, cutting, and material handling. |
Human-Machine Interfaces (HMIs) | User-friendly HMIs, often in the form of touch screens or control panels, allow operators to monitor and control the machine’s operations, adjust parameters, and access diagnostic information. |
Servo Motor Control | Precise servo motor control systems are employed to accurately position and control the movement of rollers, punches, and cutting mechanisms, ensuring consistent and accurate forming and processing. |
Material Tracking and Monitoring | Advanced sensors and monitoring systems track the material’s progress through the machine, ensuring proper alignment, detecting potential issues, and enabling real-time adjustments as needed. |
Data Logging and Reporting | Integrated data logging and reporting capabilities allow manufacturers to track production data, monitor machine performance, and generate reports for analysis and quality control purposes. |
Remote Monitoring and Diagnostics | Some Z purlin machines may incorporate remote monitoring and diagnostic capabilities, allowing technicians to monitor the machine’s performance, diagnose issues, and provide remote support or software updates. |
By leveraging these advanced automation and control systems, Z purlin roll forming machines can achieve high levels of precision, consistency, and efficiency, while also providing enhanced monitoring, data collection, and remote support capabilities.
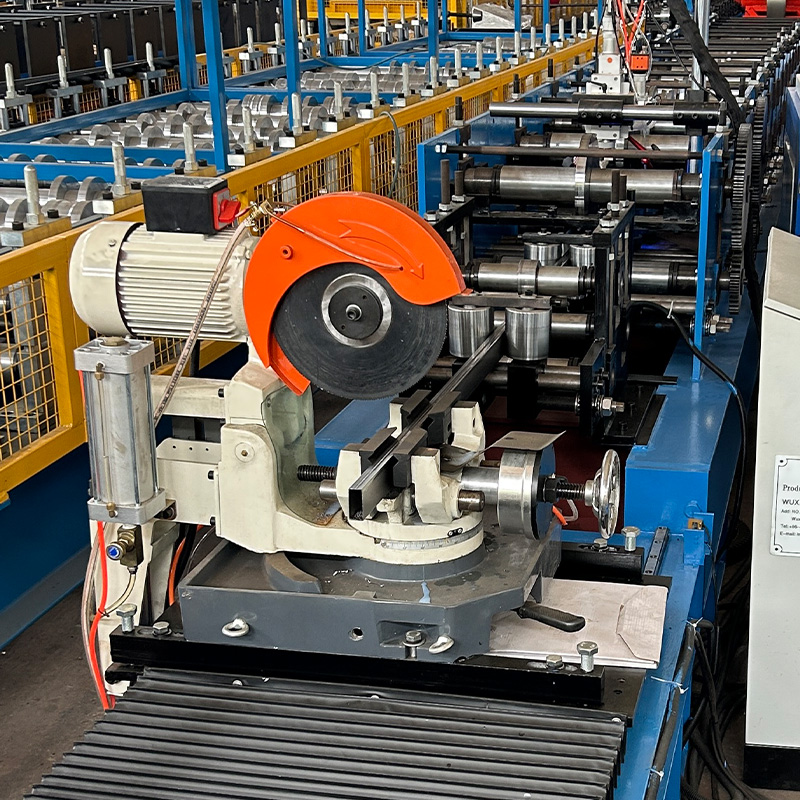
Z Purlin Machine: Maintenance and Troubleshooting
Regular maintenance and effective troubleshooting are crucial for ensuring the long-term performance and reliability of Z purlin roll forming machines. The table below outlines the key aspects of maintenance and troubleshooting for these machines:
Aspect | Description |
---|---|
Preventive Maintenance | Implementing a comprehensive preventive maintenance program is essential to minimize downtime and extend the machine’s lifespan. This may include regular inspections, lubrication, and replacement of wear parts, such as rollers, bearings, and cutting blades. |
Calibration and Alignment | Periodic calibration and alignment of rollers, punches, and cutting mechanisms are necessary to maintain precision and accuracy, ensuring consistent Z purlin quality. |
Tooling and Spare Parts Management | Effective tooling and spare parts management is crucial to minimize production disruptions. Maintaining an adequate inventory of frequently replaced components, such as rollers and cutting blades, can reduce downtime and facilitate efficient maintenance. |
Operator Training | Providing comprehensive training to operators on proper machine operation |
Z Purlin Machine: Choosing the Right Supplier
Selecting the right supplier for a Z purlin roll forming machine is crucial to ensure quality, reliability, and long-term support. The table below outlines key factors to consider when choosing a supplier:
Factor | Description |
---|---|
Reputation and Experience | Consider suppliers with a proven track record and extensive experience in manufacturing Z purlin roll forming machines. Reputable suppliers with a strong industry presence are more likely to provide high-quality equipment and reliable support. |
Product Range and Customization | Evaluate the supplier’s product range and their ability to offer customized solutions tailored to your specific requirements, such as unique Z purlin profiles or integration with existing production lines. |
Technical Expertise and Support | Assess the supplier’s technical expertise and the level of support they offer. Look for suppliers with knowledgeable engineers and technicians who can provide guidance, training, and prompt troubleshooting assistance when needed. |
After-Sales Service and Spare Parts Availability | Consider suppliers that offer comprehensive after-sales service, including spare parts availability, maintenance contracts, and on-site support. This ensures minimal downtime and efficient resolutions to any issues that may arise. |
Warranty and Guarantees | Evaluate the supplier’s warranty and guarantee terms for their Z purlin roll forming machines. A comprehensive warranty can provide peace of mind and protect your investment in the long run. |
Pricing and Value for Money | While price should not be the sole deciding factor, it is essential to consider the overall value for money offered by the supplier. Assess the machine’s capabilities, quality, and long-term costs against the initial investment. |
Customer Testimonials and References | Request customer testimonials and references from the supplier to gain insights into their customer service, machine performance, and overall satisfaction levels. Positive reviews from existing customers can be a good indicator of a reliable supplier. |
By carefully evaluating these factors, you can increase the chances of finding a reputable and trustworthy supplier who can provide a high-quality Z purlin roll forming machine that meets your specific requirements and ensures long-term satisfaction.
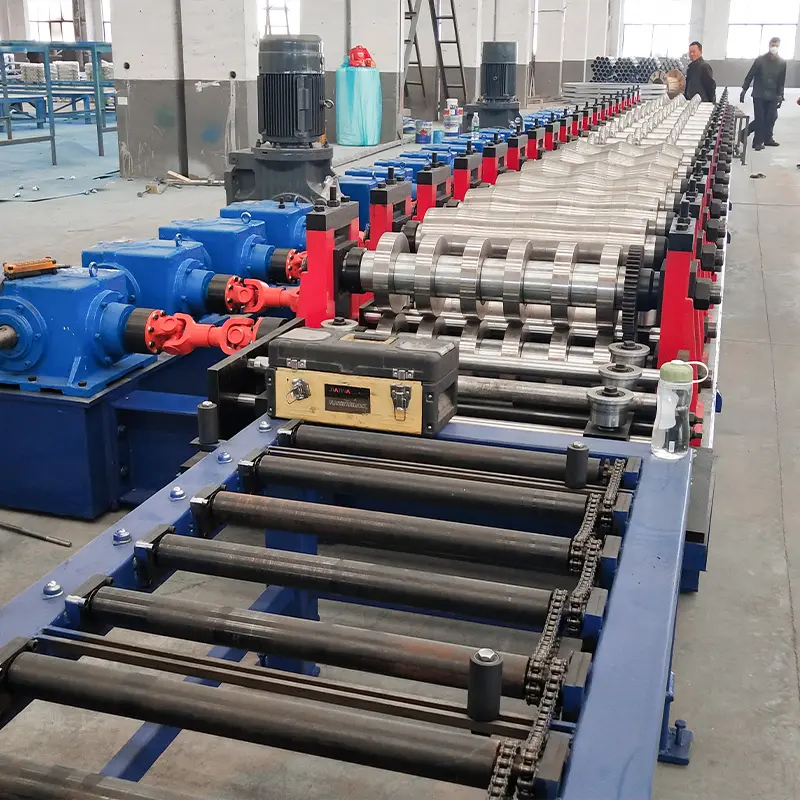
Z Purlin Machine: Pros and Cons
Like any industrial equipment, Z purlin roll forming machines have their advantages and limitations. Understanding these pros and cons can help manufacturers make informed decisions and optimize their production processes. The table below outlines the key pros and cons of Z purlin roll forming machines:
Pros | Cons |
---|---|
High Production Rates: Z purlin roll forming machines can produce consistent and high-quality Z purlins at rapid rates, enabling efficient and cost-effective production. | Initial Investment: The purchase and installation of a Z purlin roll forming machine can represent a significant initial investment, particularly for high-end or customized machines. |
Consistent Quality: Advanced automation and control systems ensure precise and consistent forming, resulting in Z purlins that meet stringent quality standards. | Specialized Skills Required: Operating and maintaining Z purlin roll forming machines may require specialized skills and training, which can increase personnel costs. |
Material Efficiency: By utilizing coiled steel as input material, Z purlin roll forming machines minimize material waste and promote efficient use of resources. | Limited Flexibility: While customization options are available, Z purlin roll forming machines are primarily designed for producing a specific range of Z purlin profiles, limiting their flexibility for other applications. |
Versatility: Z purlin roll forming machines can accommodate various steel materials, including galvanized, stainless, and pre-painted coils, enabling versatile production capabilities. | Maintenance Requirements: Regular maintenance, calibration, and replacement of wear parts are necessary to ensure optimal performance and minimize downtime. |
Automation and Integration: Many Z purlin roll forming machines offer advanced automation features and can be integrated with other production processes for streamlined operations. | Space Requirements: Depending on the machine size and configuration, Z purlin roll forming machines may require significant floor space, which can be a consideration for manufacturers with limited facility space. |
Customization Options: Manufacturers can customize various aspects of the machine, such as roller configurations, punching and cutting stations, and material handling systems, to meet specific project requirements. | Energy Consumption: Depending on the machine’s size and production volumes, Z purlin roll forming machines can have significant energy consumption, impacting operating costs. |
By weighing these pros and cons, manufacturers can make informed decisions about whether investing in a Z purlin roll forming machine aligns with their production goals, budget, and operational requirements.
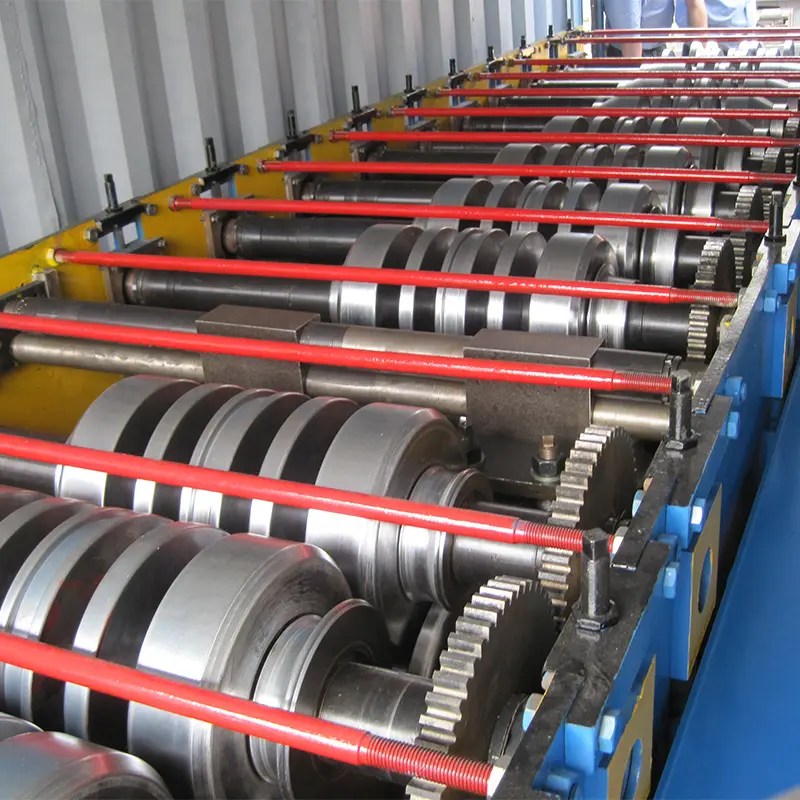
FAQ
Question | Answer |
---|---|
What is a Z purlin roll forming machine? | A Z purlin roll forming machine is a specialized piece of equipment used to manufacture Z-shaped structural components, called Z purlins, from flat steel coils or sheets. These purlins are widely used in the construction industry for supporting roof decks, wall panels, and other structural elements. |
What materials can be used in a Z purlin roll forming machine? | Z purlin roll forming machines are typically designed to work with various types of steel materials, such as galvanized steel coils, stainless steel coils, pre-painted steel coils, and aluminum coils. The choice of material depends on factors like corrosion resistance, strength requirements, and aesthetic considerations. |
Can Z purlin roll forming machines produce different profiles? | Yes, many Z purlin roll forming machines offer customization options, allowing manufacturers to adjust the roller configurations and tooling to produce different Z purlin profiles or accommodate varying material thicknesses and strengths. |
How does a Z purlin roll forming machine work? | The process involves feeding a continuous strip of flat steel coil or sheet material into the machine, where it goes through a series of precisely calibrated roller stations that progressively bend and shape the material into the desired Z purlin profile. Additional operations, such as punching, cutting, and finishing, may also be performed by the machine. |
What are the benefits of using a Z purlin roll forming machine? | Benefits include high production rates, consistent quality, material efficiency, versatility in handling various steel materials, customization options, and the ability to integrate with automated systems for streamlined operations. |
How do I choose the right Z purlin roll forming machine for my needs? | Consider factors such as production volume, Z purlin profile requirements, material types and thicknesses, integration and automation needs, punching and cutting requirements, space constraints, customization and flexibility, budget, and supplier reputation and support. |
What maintenance is required for Z purlin roll forming machines? | Regular maintenance tasks include roller inspection and replacement, lubrication, cutting tool maintenance, calibration and alignment, safety system checks, control system updates, and cleaning and housekeeping. Effective troubleshooting procedures are also crucial. |
Can Z purlin roll forming machines be integrated with other production processes? | Yes, many Z purlin roll forming machines offer advanced automation features and can be integrated with other production processes, such as material handling systems, for streamlined operations and improved efficiency. |
What are the typical applications of Z purlins produced by these machines? | Z purlins are widely used in the construction industry for roofing systems, wall panels, structural framing, modular and prefabricated buildings, agricultural structures, warehousing and storage facilities, infrastructure projects, and renewable energy installations. |
What factors should I consider when choosing a Z purlin roll forming machine supplier? | Consider the supplier’s reputation and experience, product range and customization options, technical expertise and support, after-sales service and spare parts availability, warranty and guarantees, pricing and value for money, and customer testimonials and references. |