Square tube roll forming machines are used to form metal coils into square or rectangular hollow tubes and profiles. This versatile equipment is widely utilized to produce structural steel tubes, fence posts, road guard rails, scaffolding, and various industrial applications.
This comprehensive guide will cover all key aspects of square tube roll forming machine technology to help you understand how it works and select the right system.
Overview of Square Tube Roll Forming Process
Roll forming is a continuous bending operation in which sheet or coil material is gradually shaped through a series of contoured rollers until the desired cross-sectional profile is achieved.
This incremental cold forming process produces uniform, high-quality hollow tubes and custom profiles with excellent strength-to-weight ratios.
Square tube roll forming utilizes a series of roller stations to sequentially bend the flat strip stock into a square or rectangular closed tube as it passes through the machine:
- Uncoiler and feed section straightens the coil and feeds it into the first forming rolls.
- Forming roll stations gradually bend the material around a mandrel into the square shape.
- Sizing roll stands fine tune the section dimensions.
- Cut off knives slice the tube into desired lengths.
- Finishing operations like punching, notching or hole making can be integrated before cut off.
Compared to other tube manufacturing processes like welding or extrusion, roll forming is fast, efficient, and economizes material use by creating tubes with thin walls and without welding seams.
It allows quick changeovers between different sizes and profiles with the same equipment. Minimal scrap losses combined with high production rates make roll forming very cost-effective for long and short production runs.
Types of Square Tube Roll Forming Machines
Square tube roll forming machines are available in different configurations and complexity levels depending on production needs:
All-In-One Versus Modular Roll Forming Lines
- All-in-one machines have all components like uncoiler, forming sections, cutoff in one integrated line. Compact and economical for low volume production.
- Modular roll forming lines allow combining standalone roll forming mills, loopers, cutoffs. Flexible for high output rates and customization.
Fixed Versus Adjustable Roll Formers
- Fixed roll formers produce one tube size. Less expensive for high volume of one profile.
- Quick change roll formers allow fast size changeovers with minimum downtime using collapsible or removable roll stands. Added flexibility.
Manual Versus Automated Roll Forming Systems
- Manual roll forming machines require an operator to feed coils through the line. Economical option for low labor cost regions.
- Automated roll forming lines have powered unwinding, feeding and cutoff. Reduce labor and increase efficiency. Costlier initial investment.
Table 1: Comparison of Square Tube Roll Forming Machines
Machine Type | Key Features | Benefits | Limitations |
---|---|---|---|
All-in-One | Compact integrated production line | Lower cost, smaller footprint | Limited output |
Modular | Flexible combination of roll former mills, loopers, cutoffs | Higher capacity, customization | Complex, higher budget |
Fixed | Rolls fixed for one profile | Lower cost, specialized output | Size changeover delays |
Adjustable | Interchangeable/collapsible rolls | Quick changeovers, flexible sizes | Added complexity, expense |
Manual | Requires operator to feed coil | Lower budget | Labor dependent, slower |
Automated | Powered unwind, feed and cutoff | Less labor, higher efficiency | Higher initial cost |
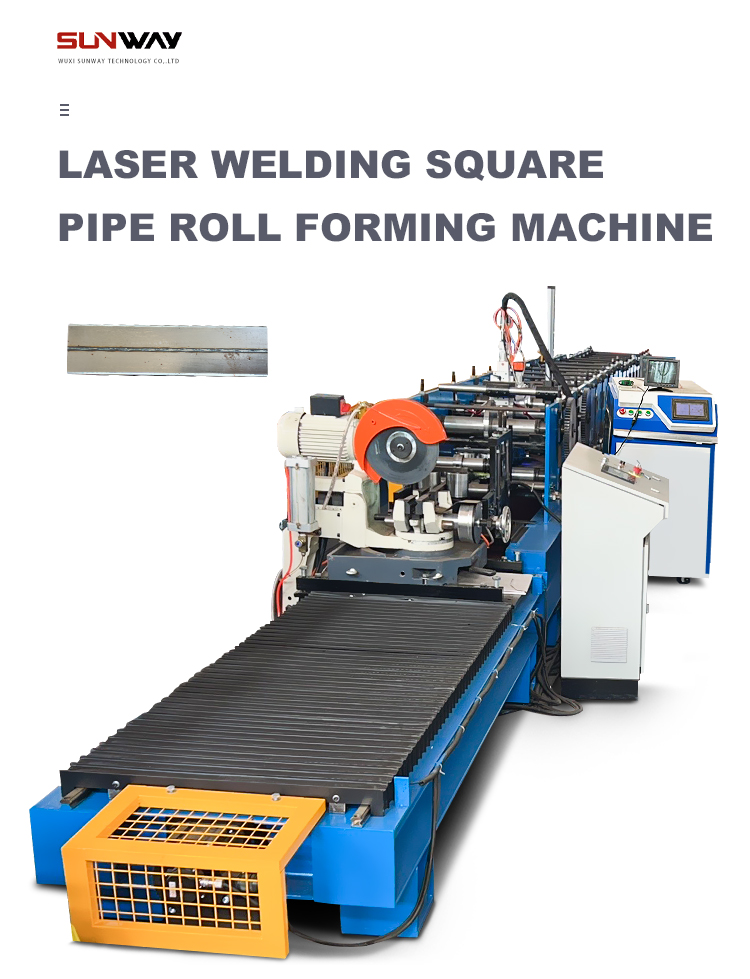
Key Components of Square Tube Roll Forming Lines
A complete production line has several important equipment modules working together:
- Decoiler or uncoiler to hold and unroll the raw coil material.
- Feeding mechanism to smoothly pull and straighten the strip.
- Forming stations with contoured rollers that gradually form the flat strip into a square tube.
- Sizing stations to calibrate the tube dimensions.
- Cut off press to cut tubes into set lengths.
- Finishing punching, notching, hole making.
- Exit table for finished tubes.
Advanced roll forming systems also integrate a looper or accumulation tower to allow continuous production as cut off press operates, and a cooling table for heat treatment.
Table 2: Key Components of Square Tube Roll Forming Machines
Component | Purpose | Considerations |
---|---|---|
Decoiler | Hold and unroll coil | Payoff reel, capacity, motorized |
Feeding Mechanism | Pulls & aligns strip | Number of stands, straightener type |
Forming Stations | Gradually forms profile | Number of stands, roller design |
Sizing Stations | Calibrates dimensions | Number of stands, roller diameter |
Cut Off Press | Cuts tubes to length | Blade type, automation features |
Finishing | Punching, notching, holes | Application needs |
Looper/Tower | Allows continuous running | Height, accumulation method |
Cooling Table | Controlled cooling | Length, cooling flow control |
Design Considerations for Square Tube Roll Forming
Key aspects to consider in square tube roll forming machine design:
- Roller dimensions – Pitch circle diameter determines bend radius. Roller width impacts pressure distribution.
- Number of roller stands – More stands allow gradual bending to avoid cracking. 8-10 is common.
- Mandrel design – Internal mandrels support inside profile. Mandrel bending radius affects tube dimensions.
- Roll separating force – Force to push forming rolls apart for entry and exit of material.
- Roll bearings – Withstand high loads. Linear bearings common for precision and extended service life.
- Roll parallelism – Rolls must be precisely parallel to avoid twisting.
- Roll materials – Ductile materials like alloy steel withstand deforming forces during bending.
- Lubrication – Prevents galling and facilitates material flow. Oil, grease, graphite, boron nitride used.
- Motor sizing – Determines production speed. AC vector drives offer precision control.
- Frame rigidity – Minimizes deflection under loads. Roll centers remain constant.
Table 3: Square Tube Roll Forming Machine Design Considerations
Design Aspect | Importance | Best Practices |
---|---|---|
Roller Dimensions | Critical | Optimize bend radius, pressure distribution |
Number of Stands | Vital | 8-10 stations common for gradual bending |
Mandrel Design | Essential | Match mandrel radius to desired tube size |
Roll Separating Force | Key | Use pneumatic or hydraulic cylinders |
Roll Bearings | Important | Use heavy-duty linear guide bearings |
Roll Parallelism | Extremely Important | Precision alignment, no twist |
Roll Materials | Significant | Use hardened alloy steel |
Lubrication | Necessary | Oil, grease, graphite, boron nitride |
Motor Sizing | Critical | AC vector drive for speed control |
Frame Rigidity | Very Important | Minimize deflection under load |
Pro Tip: Work with experienced roll forming machine manufacturers during the design process to leverage their expertise in component sizing, material requirements, and equipment engineering.
Typical Specifications of Square Tube Roll Forming Machines
Technical specifications depend on production needs. Typical parameters include:
- Tube sizes – 50×50 mm to 400×400 mm square sizes possible. Rectangular sizes also produced.
- Thickness range – 0.3 mm to 3 mm. Optimal is 1 to 2 mm for most applications.
- Width range – Up to 2000 mm wide coils can be processed.
- Lengths – Tubes from 1 to 6 m long commonly produced. Extended lengths possible.
- Materials – Mild steel, stainless steel, aluminum, copper alloys.
- Finishing options – Punching, notching, hole making.
- Production speed – 10 to 15 m/min typical. Higher speeds possible with automated lines.
- Drive types – Electric servo, hydraulic, pneumatic.
Table 4: Typical Specifications of Square Tube Roll Forming Machines
Parameter | Typical Values |
---|---|
Tube Sizes | 50×50 mm to 400×400 mm |
Thickness Range | 0.3 to 3 mm |
Width Range | Up to 2000 mm |
Lengths | 1 to 6 m |
Materials | Mild steel, stainless, aluminum etc. |
Finishing Options | Punching, notching, holes |
Production Speed | 10 to 15 m/min |
Drive Types | Electric, hydraulic, pneumatic |
Speed and dimensional accuracy are enhanced with features like precision ground bearing seats, AC vector drives, and integrated rollers and components from quality suppliers.
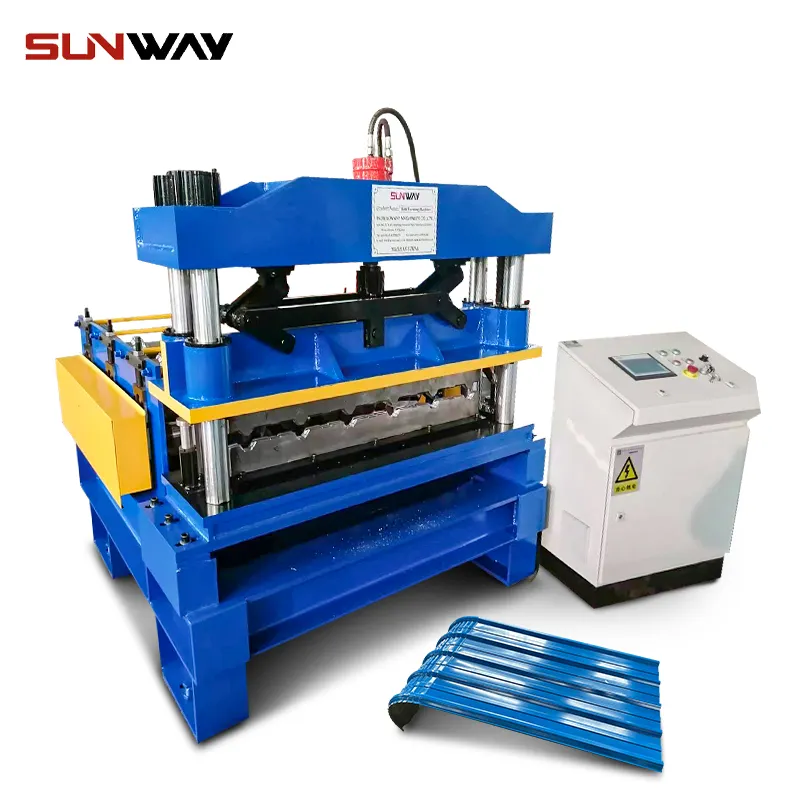
Applications and Uses of Square Tube Profiles
Key applications where square tube profiles from roll forming are used include:
Structural Applications
- Building and construction frames
- Scaffolding
- Trailers, conveyor systems
- Crane beams
- Agricultural equipment
Decorative Applications
- Furniture frames
- Railing and balustrades
- Gates, fences, handrails
- Store fixtures
Automotive Applications
- Chassis, axles, stabilizers
- Exhaust pipes
- Tow bars, roof racks
Square tube profiles offer excellent strength for structural applications combined with aesthetic appeal for decorative uses. Other benefits include good corrosion resistance and dimensional stability.
Table 5: Applications of Square Tube Profiles from Roll Forming
Category | Applications |
---|---|
Structural | Building frames, scaffolding, conveyors |
Decorative | Furniture, railings, fences |
Automotive | Chassis, axles, exhaust pipes |
Choosing a Square Tube Roll Forming Machine Supplier
Key factors when selecting a square tube roll forming machine partner:
- Experience – Number of years providing roll forming solutions. Longer track record preferable.
- Production scale – Supplier capability to deliver small prototyping lines to high output automated lines.
- Customization skills – Expertise in tailored solutions for custom profiles. Quick changeover ability.
- Quality standards – Stringent quality control and testing capability. ISO certified preferable.
- Service record – Responsiveness to service requests, technical support reliability. Check client reviews.
- Pricing – Competitive pricing but avoid very low bids that compromise quality. Consider TCO.
- Lead time – Production and delivery time. 8-12 weeks is standard. Faster response preferred.
Table 6: Selection Criteria for Square Tube Roll Forming Machine Suppliers
Criteria | Best Practices |
---|---|
Experience | Number of years in business, track record |
Production Scale | Prototyping to high volume capability |
Customization Skills | Expertise with custom profiles, quick changeovers |
Quality Standards | Stringent QC, ISO certification |
Service Record | Responsiveness, technical support |
Pricing | Competitive but not very low bids |
Lead Time | 8-12 weeks standard. Faster turnaround better. |
Work with trusted international machine builders like Foshan YSD Roll Forming Machinery or reputable regional suppliers for reliability.
Square Tube Roll Forming Machine Price Considerations
Square tube roll forming machine prices vary based on:
- Production output – Higher capacity lines cost more.
- Automation level – Manual vs automated feeding and cutoff.
- Size range – Wider range needs quick changeover ability.
- Customization – Special profiles increase engineering costs.
- Material – Stainless steel and aluminum cost more than mild steel machines.
- Brand reputation – Premium brands command higher prices.
For small scale manual roll forming machines:
- Basic machine producing one small tube size: $15,000 to $30,000
- Larger variable size range capability: $30,000 to $60,000
For high production automated lines:
- Fixed high capacity single profile lines: $60,000 to $100,000
- Quick changeover flexible lines: $80,000 to $150,000
- Complex multi-profile variable lines: $120,000+
Table 7: Square Tube Roll Forming Machine Price Ranges
Machine Type | Typical Price Range |
---|---|
Small manual roll former, fixed | $15,000 – $30,000 |
Medium manual, quick changeover | $30,000 – $60,000 |
Large automated, fixed profile | $60,000 – $100,000 |
Large automated, variable sizes | $80,000 – $150,000 |
Complex flexible high-output | $120,000+ |
Request detailed quotes from suppliers based on your annual production requirement. Consider long term costs like operation, maintenance, downtime, and changeover time when comparing budget vs premium machines.
Installation and Operation of Square Tube Roll Forming Machines
Proper installation and operation procedures are vital for production efficiency, safety, and machine longevity.
Installation Guidelines
- Place on flat, level concrete flooring. Anchor securely.
- Ensure adequate space around for coil loading and material offloading.
- Install electrical connections per local codes.
- Position ancillary equipment like loopers and cutoff presses appropriately.
- Install safety guards, fences, markings as per safety codes.
- Test run to confirm correct functioning before production.
Operation Guidelines
- Carefully load coils on the decoiler using overhead crane and clamps.
- Thread the strip through the entry guides and rollers. Adjust guides.
- Set the mandrel size and roller spacing for the required tube dimensions.
- Set cutoff press stroke, blade gap as per tube length.
- Start with slow speed trial runs to check strip flow and quality.
- Increase speed gradually after confirming smooth material feed.
- Use thickness gauges to randomly validate tube dimensions.
- Apply lubricants and cooling as needed during production.
- Ensure safety gears and protocols are followed at all stages.
Table 8: Installation and Operation Guidelines for Roll Forming Machines
Stage | Procedure |
---|---|
Installation | Flat, level base Anchor securely Utility connections Safety items |
Operation | Coil loading procedure Material threading Set mandrel, roll spacing Set cutoff press Start slow, increase speed Use gauges to check size Apply lubrication Follow safety protocol |
Thoroughly train machine operators on procedures developed from supplier guidelines to maximize performance.
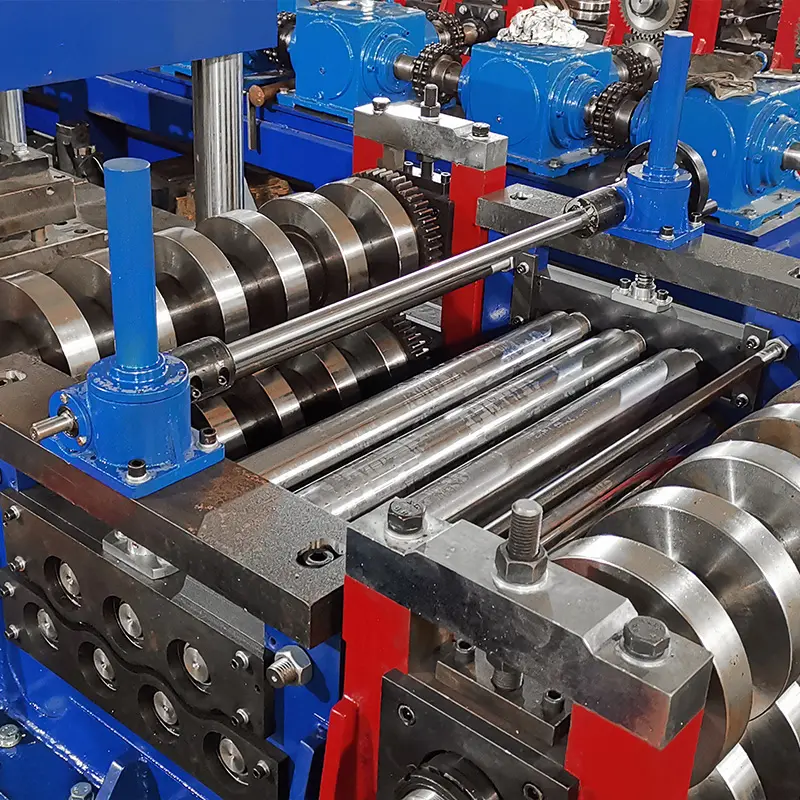
Maintenance of Square Tube Roll Forming Equipment
Consistent maintenance enhances square tube roll forming machine longevity, performance, and safety.
- Perform daily cleaning and inspection, checking bolts, guards, electricals.
- Lubricate rollers, bearings, and moving components as specified.
- Inspect rollers and guides. Replace damaged or worn items immediately.
- Verify hydraulic systems and hoses. Fix leaks promptly.
- Confirm electrical wiring insulation condition. Repair damage.
- Check chain tension, sprockets, gears. Adjust per guidelines.
- Verify pneumatic system connections, pressure, valves.
- Confirm cutting blades are sharp and gap is accurate.
- Check drive belts, pulleys, alignment. Tension belts as needed.
- Fasten any loosened frame bolts to avoid misalignment.
Table 9: Recommended Maintenance Schedule for Roll Forming Machines
Frequency | Tasks |
---|---|
Daily | Inspect guards, bolts, electricals Cleaning |
Weekly | Lubricate rollers, bearings Inspect rollers, guides Check hydraulics, electrics |
Monthly | Verify pneumatics, belts, drive alignment Sharpen/replace blades |
Yearly | Frame rigidity check Motor, drive inspection Replace worn parts |
Keep maintenance logs to track activities and part replacements. Schedule annual maintenance shutdowns for intensive upkeep measures to maximize longevity.
How to Choose the Right Square Tube Size
Follow key considerations when selecting the optimal square tube size:
- Application – Size depends on building structure, fence, conveyor needs.
- Load levels – Larger cross-section for heavy loads. Check max load capacity.
- Span – Longer unsupported spans may need bigger sizes to minimize sagging.
- Deflection limits – Keep deflection within permissible limits under expected load.
- Strength needs – Higher yield strength materials allow thinner walls at same load.
- Weight limits – Heavier tubes add dead load. Check crane capacity.
- Cost – Larger tubes cost more but optimize material use.
- Standards – Follow local construction, building, safety codes.
Perform engineering calculations on shear, bending moments, deflection, and stresses for the application. Seek expert guidance on appropriate design margins and safety factors.
Table 10: Key Considerations for Selecting Square Tube Size
Factor | Guidelines |
---|---|
Application | Structural needs, load type |
Load Levels | Size for max expected load |
Span | Minimize sag, deflection in spans |
Deflection Limits | Check permissible limits |
Strength Needs | Higher strength, thinner walls |
Weight Limits | Heavier tube adds dead load |
Cost | Larger optimizes material but costs more |
Standards | Follow local building, safety codes |
Select a standard tube size that meets engineering requirements, load capacity needs, span limits, and application fit.Validate structural performance through rigorous testing.
Comparing Square Versus Rectangular Tube Profiles
Square Tubes
- Uniform strength in all directions – torsional rigidity
- Optimal balance of strength and weight
- Aesthetic appeal for decorative uses
- Easier to join and connect
- Limited size range due to roll forming limits
Rectangular Tubes
- Stronger in one axis – better for unidirectional loads
- Larger web area in beam applications
- Higher second moment of area
- Expanded forming size capabilities
- Harder to connect joints
- Risk of twisting if not braced properly
Table 11: Comparison of Square vs Rectangular Tubes
Parameter | Square Tube | Rectangular Tube |
---|---|---|
Strength | Equal on all sides | Strongest along width axis |
Appearance | Visually appealing | Industrial look |
Size Range | 50 mm to 400 mm typical | Up to 1000 mm width possible |
Connections | Easier to join | Requires gussets for joints |
Applications | Structural and decorative | Beams, frames, structures |
Cost | Lower | 15-20% higher |
For most structural applications, square tubes offer the best balance of functionality, cost, and aesthetics. Rectangular profiles are advantageous where high strength in one direction is needed, like long spanning beams.
Consider both types during the design process and choose the most suitable shape for the specific application loads and requirements. Validate performance through analysis and testing.
Roll Forming Machine Safety Tips
Safety must be the top priority when operating square tube roll forming equipment. Key tips:
- Restrict access to only trained operators.
- Mandatory PPE – safety glasses, gloves, sturdy shoes.
- Ensure adequate lighting in work zones.
- Keep work area clean and free of clutter.
- Do not wear loose clothing, jewelry near moving parts.
- Tie back long hair to avoid entanglement.
- Never reach between rollers during operation.
- Use clamps to handle tubes, not bare hands.
- Follow lockout/tagout procedures for maintenance.
- Install safety mats and fences to restrict access.
- Clearly label steps during machine startup, operation, and shutdown.
- Install emergency stops at accessible locations.
- Regularly inspect guards, interlocks, E-stops.
- Follow local safety codes and display warning placards.
Table 12: Roll Forming Machine Safety Tips
Focus Area | Safe Practices |
---|---|
Access | Allow only trained operators |
PPE | Mandatory safety gear |
Housekeeping | Clean clutter-free space |
Behavior | No loose clothing or jewelry |
Maintenance | Follow lockout/tagout process |
Safeguards | Install fences, mats, barriers |
Labeling | Clear instructions at steps |
Inspection | Check guards, interlocks, E-stops |
Compliance | Follow safety codes and standards |
Incorporate safety at every step from design through daily production. Perform risk assessments and implement all feasible safeguards. Make safety the first priority.
Troubleshooting Common Roll Forming Machine Issues
Some common square tube roll forming machine problems and remedies:
Twisted or warped tubes
- Misaligned rolls – realign precisely parallel
- Roll diameters uneven – replace damaged rolls
- Improper roller gap – set even gaps per procedure
- Strip stock not centered – guide material into roller centerline
Dimensional deviations
- Worn rolls – resurface or replace rolls
- Damaged/incorrect mandrel – replace with right size
- Roll gaps incorrect – reset with precision spacers
- Excessive strip tension – reduce coil brake drag
- Dirty/dry material – increase lubrication
Surface defects
- Roller damage – repair or replace defective rolls
- Debris buildup – clean rollers and guides
- Dry material – use correct lubrication
- Strip slitting issue – improve edge preparation
Uncut tubes
- Blunt blades – sharpen or replace worn blades
- Blade gap too large – decrease gap to specification
- Cutoff press feed misaligned – realign strips into cutoff
- Excessive strip vibration – stabilize material flow into cutoff
Table 13: Troubleshooting Common Roll Forming Machine Issues
Problem | Potential Causes | Solutions |
---|---|---|
Twisted tubes | Misaligned rolls Uneven roll diameters Improper gaps Off-center strip | Realign rolls Replace damaged rolls Set even gaps Center material |
Dimension errors | Worn rolls Wrong mandrel Incorrect gaps Excess tension | Resurface/replace rolls Install right mandrel Reset gaps correctly Reduce coil brake drag |
Surface defects | Roller damage Debris buildup Dry material Poor edge | Repair/replace rolls Clean thoroughly Use proper lubrication Improve edge |
Uncut tubes | Blunt blades Excessive blade gap Feed misalignment Excess vibration | Sharpen/replace blades Decrease blade gap Realign feed Stabilize material flow |
Thoroughly investigate root causes before attempting corrections. Enlist supplier support for troubleshooting difficult quality issues.
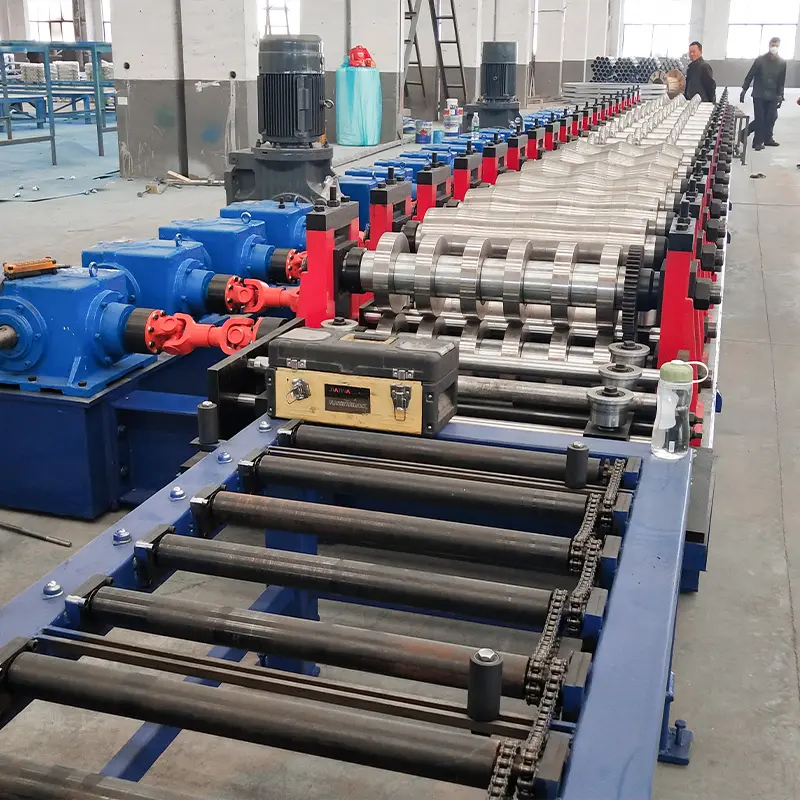
FAQ
Q: What thickness of material can be roll formed?
A: Most roll forming machines can process 0.3 mm to 3 mm thickness. Optimal range is 1 to 2 mm for good formability.
Q: What alloys can be shaped by roll forming?
A: Mild steel, stainless steel, aluminum, copper alloys. Material must have adequate ductility for cold forming.
Q: How long are the tubes produced?
A: Standard lengths are 1 to 6 meters. Extended lengths possible through customized offline cutting.
Q: Can other profiles be produced besides square tube?
A: Yes, rectangular, round, C sections, angles, and custom profiles can also be roll formed.
Q: How fast is the production rate?
A: 10-15 meters per minute normally. Automated high-speed lines can achieve over 30 m/min.
Q: What factors affect the process efficiency?
A: Roller design, precise alignment, lubrication, strip feed rate, and mandrel shape.
Q: How quick are size changeovers?
A: Quick change machines can swap forming rollers & mandrels in 1-2 hours. Fixed roll formers require 4+ hours.
Q: What tolerances are held on tube dimensions?
A: Roll forming can hold +/- 0.5 mm dimensional accuracy. Secondary processes further improve precision.
Q: What safety measures are recommended?
A: Safety guards, barriers, interlocks, E-stops, PPE, training, and safe operating practices.
Q: What regular maintenance is needed?
A: Cleaning, lubrication, inspection of rollers, guides, hydraulics, electrics, pneumatics & other moving parts.
Q: How can roll formed tube quality issues be solved?
A: Thoroughly investigate root cause first. Work with supplier to identify and correct forming practices.
Q: What is better – square versus rectangular tube?
A: Square generally optimum for cost, strength, and appearance. Rectangular benefits long spanning beams.
Q: How to get custom profiles or features?
A: Experienced roll forming partners can design and manufacture custom tooling for special profiles. Share profile drawings to get quote.