Roll forming is a metalworking process in which sheet metal is progressively formed into a desired cross-section by passing through a series of complementary pairs of rollers. Steel roll forming machines are essential equipment used to continuously bend metal sheet into customized profiles with a robust structural framework.
This comprehensive guide covers everything you need to know about steel roll forming machines including:
Overview
- What is a steel roll forming machine?
- Working principle
- Major components
- Roll forming vs other bending processes
- Applications and benefits
- Roll formed profiles
Types of Steel Roll Forming Machines
- Coil lines
- Modular machines
- Portable roll forming machines
- Custom roll forming machines
Main Components of a Roll Forming Machine
- Uncoiler
- Roll forming mill
- Cutoff device
- Control panel
Specifications
- Size parameters
- Roll change design
- Speed and strips width
- Power and transmission
- Material thickness
- Roll adjustment and changeover
Roll Tooling Design
- Roll pass design
- Roll cluster configuration
- Roller dimensions
- Roll materials
Process Standards and Tolerances
- Profile tolerances
- Strip tolerances
- Roll design standards
Manufacturers and Suppliers
- Top roll forming machine brands
- Pricing comparison
- Chinese manufacturers vs European manufacturers
**Installation and Commissioning **
- Site planning and preparation
- Leveling and alignment
- Trial runs and adjustment
- Safety measures
Operation and Maintenance
- Operating guidelines
- Speed and feed optimization
- Roller care and lubrication
- Tooling changeover
- Troubleshooting guide
How to Select a Roll Forming Machine
- Required production rate
- Material type and thickness
- Profile shape and complexity
- Length of profiles
- Budget
Advantages of Roll Forming
- High production rates
- Consistent and quality profiles
- Design flexibility
- Cost efficiency
- Minimal material wastage
- Applicable to diverse materials
Limitations of Roll Forming Process
- High initial tooling cost
- Long lead time for tooling
- Fixed cross-section
- Limitation on material strength
- Not suitable for short or bendable parts
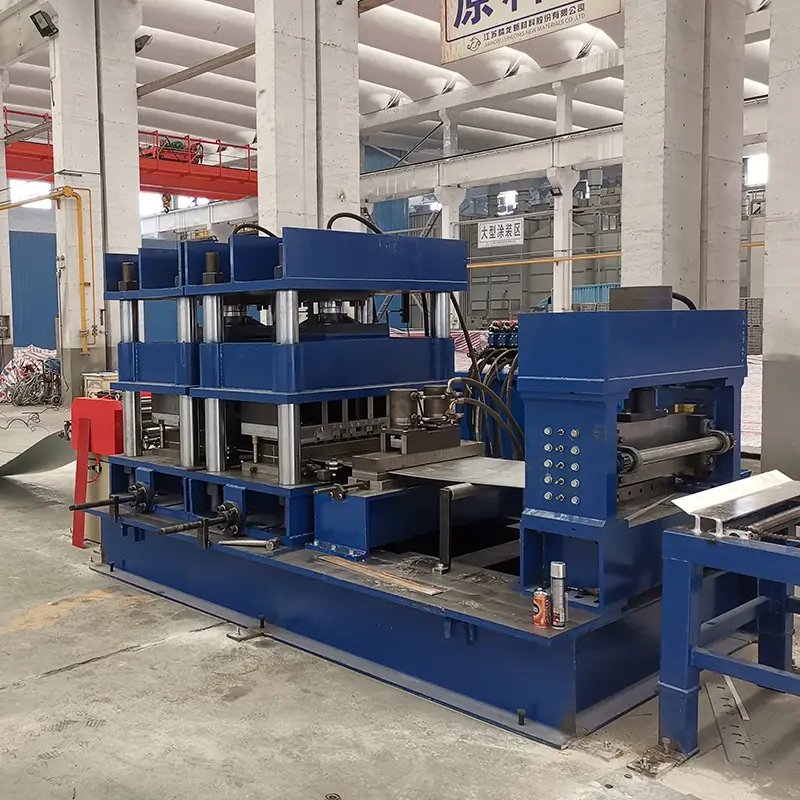
Overview of Steel Roll Forming Machines
Roll forming machines are a unique type of metal fabrication equipment used to transform metal coils or sheets into customized longitudinal profiles with a long length. The roll forming process involves sequential bending of the strip material through a series of roller passes until the desired cross-section profile is achieved continuously. Steel roll formed sections find wide-ranging applications in construction, infrastructure, automobile, railways, shipbuilding, appliances, and packaging industries.
What is a Steel Roll Forming Machine?
A roll forming machine is specialized equipment with a series of roller stations along a linear path that progressively shape flat strip stock into a longitudinal structural beam or open profile of fixed cross-section. As the coils pass through each roller station, it is continuously bent a few degrees at a time without any abrupt forming stage. The roll tooling is designed and set to gradually bend the strip stock incrementally through small deformations into the final channel, I-beam, angle, tube, or custom shape. Based on the configuration, these machines can process steel, stainless steel, or aluminum coils weighing several tons into finished profiles hundreds of feet long at high production speeds.
Working Principle of Roll Forming Machines
The working principle involves continuously passing metal strips from a coil through a series of roller dies to plastically deform the material incrementally through a series of small bending steps. The roller pairs are designed to apply targeted bending forces sequentially to shape the strips into the desired form. Typically between 15 to 20 roller stations comprising male and female roller pair sets are required to gradually bend a flat strip into a fully formed section. The roller configuration and design calculations ensure complete material deformation without any localized thinning or stretching. The strip is fed through the mill using tractor drives or pinch rolls with adjustable speed based on the forming limits. The profiles coming out of the final station are cut to required lengths by a cutoff press or saw.
Major Components of a Roll Forming Line
The main components of a roll forming machine line are:
- Uncoiler – To hold the coil of sheet metal and feed into the mill
- Feeding rolls – Grips and feeds the strip through the mill at a constant speed
- Forming stations – Series of top and bottom rollers that progressively bend the strip
- Cutoff press – Shears the profile strips to required length
- Controls – To monitor and adjust operational parameters
- Frame – Houses the stations and provides rigidity
Roll Forming vs Other Metal Bending Processes
Roll forming is distinct from other common metal bending processes like press braking as it does not involve abrupt one-time bending of the workpiece between a punch and die. The key differences are:
- Press Brake Bending – Discrete bending steps to form cross-section in a press
- Roll Forming – Continuous/incremental bending through roller stations
- Extrusion – Material pushed through a die opening to create a shape
- Roll Bending – Simple gradual bending between two rollers
While press brakes can achieve complex custom shapes through staged forming, roll forming is ideal for continuous production of fixed profile sections in long lengths.
Applications and Benefits of Roll Formed Sections
Some of the key applications of roll formed steel profiles include:
- Purlins, girts, door frames in steel buildings
- Rack posts, truck frames, roof bows in automotive industry
- Formwork systems in construction
- Scaffolding, solar panel frames
- Rails, passenger coach interior panels in railways
- Appliance housings, electronic enclosures
- Furniture frames and storage systems
- Highway guard rails and signage
The advantages of roll formed parts which make them suitable for such applications are:
- High dimensional accuracy and repeatability
- Consistent quality with excellent surface finish
- High production rate up to 100 m/min
- Cold forming retains original material strength
- Fixed cross-section allows easy assembly
- Lower production cost than alternate methods
- Ideal for high strength steels and exotic alloys
- Minimal material wastage as no offcuts
Roll Formed Profiles and Shapes
Some common roll formed sections include:
- Channels– U shaped with inwards facing flanges
- Zeds / Sigmas– Z shape with flanges on both sides
- Panels– Broad flat strip with stiffening ribs
- Open beams– I beam, T beam
- Closed beams– Rectangular, round or oval tubes
- angles – L shaped simple bend with equal or unequal legs
- Hat sections– U shape with outward bent flanges
- Door frames– Combined bends to make door jambs
These profiles can have straight, tapered, curved or variable sections based on the design of the roll tooling. Custom profiles are possible for specialized applications.
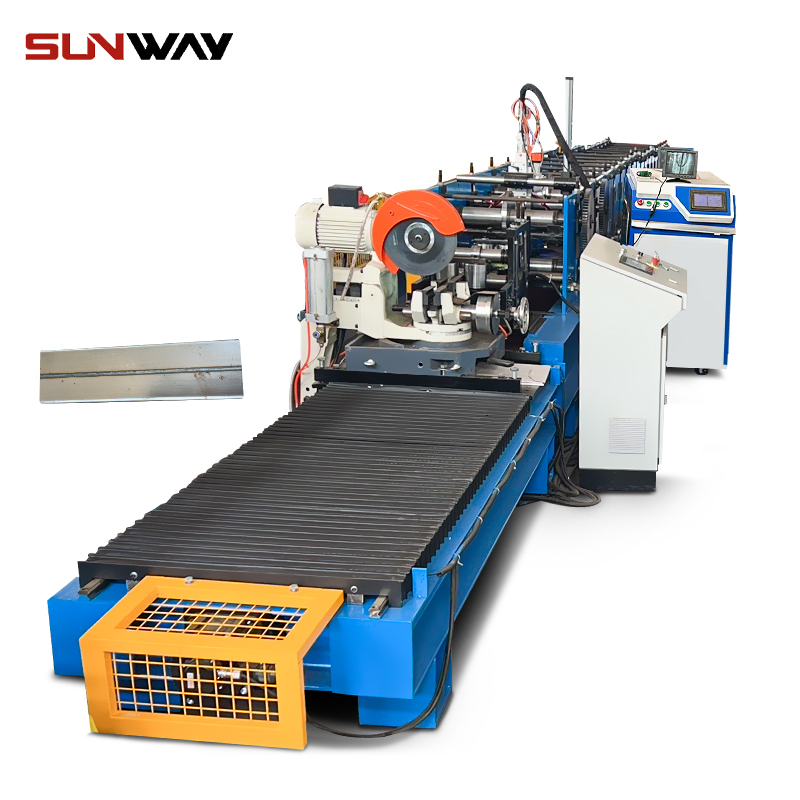
Types of Steel Roll Forming Machines
There are several configurations of roll forming mills and tooling layouts available to produce different steel profiles. The main types are outlined below:
Coil Processing Roll Forming Lines
- Most common type of roll forming machine
- Designed for high production rates
- Typically 30-50 rolling stations
- Handles large coils up to 40 tons
- Automated operation with programmable controls
- Produces repetitively up to 100 m/min speed
- Adds inline processes like punching and welding
- Used by profile manufacturers
Modular and Compact Roll Forming Machines
- Configurable modular stations
- Flexible layouts customized for profiles
- Small footprint for space savings
- Lower investment cost
- Typically 3-10 roll stations
- Production rates up to 20 m/min
- Used for low to medium production scale
- Suitable for small workshops and factories
Portable Roll Forming Machines
- Lightweight and movable designs
- Manual or motorized operation
- Small number of roll stations
- Limited to small profiles
- Lower capacities < 25mm thickness
- For on-site or mobile production
- Useful for limited period production
Custom Roll Forming Machines
- Designed and built for specific profiles
- Optimized roller configuration and passes
- Often automated or PLC controlled
- Dedicated to particular applications
- Production as per volume requirements
- Reduced tooling design time
- Used by profile order suppliers
Shape Rolling Mills
- Capable of variable-section beams
- Specialized 4-roller configuration
- Rollers tilted to continuously vary profile
- Complex control system for roller axes
- Used for tapered beams, varied geometries
Main Components of a Roll Forming Machine
The main sub-systems in a roll forming line are:
Coil Holding Uncoiler
- Holds coiled sheet metal stock
- Mounted on a powered unwind reel
- Releases strip stock into the mill
- Braking to apply desired strip tension
- Guide rollers for correct strip alignment
- Multi-roll levels for quick coil loading
Roll Forming Mill
- Series of top and bottom roller pairs
- Each roller set bends sheet incrementally
- Rollers mounted between housings and bearing blocks
- Gearing system connects the shafts
- Number of passes depends on profile shape
- Roll clearance, design, and passes determine profile
Punching Unit
- Adds holes or notches in the profile
- By sheet strip punching heads
- Operates inline during roll forming
- Required for fastening or joining
- CNC programmable for position
Cutoff Press/Shear
- Cuts profiles to desired lengths as output
- Hydraulic shear or pneumatic cutoff press
- Automated length measurement
- Alternative to static saw cutoffs
- Provides clean blanking of profiles
Control Panel
- Adjusts operational parameters digitally
- Controls line speed, feeds, and cutting
- Monitoring and instrumentation
- Pre-programmed forming recipes
- Interlocked safety system
Frame and Housing
- Supports roll stations and sub-systems
- Rigid structural framing resists vibration
- Side guiding plates for strip positioning
- Ladders and platforms for access
- Robotic handling integration
Material Feeding System
- Feeds strip through the roller stations
- Electric motor-driven tractor pullers
- Synchronized pinch rolls grip strip stock
- Keeps constant speed without slippage
- Prevent buckling and distortion
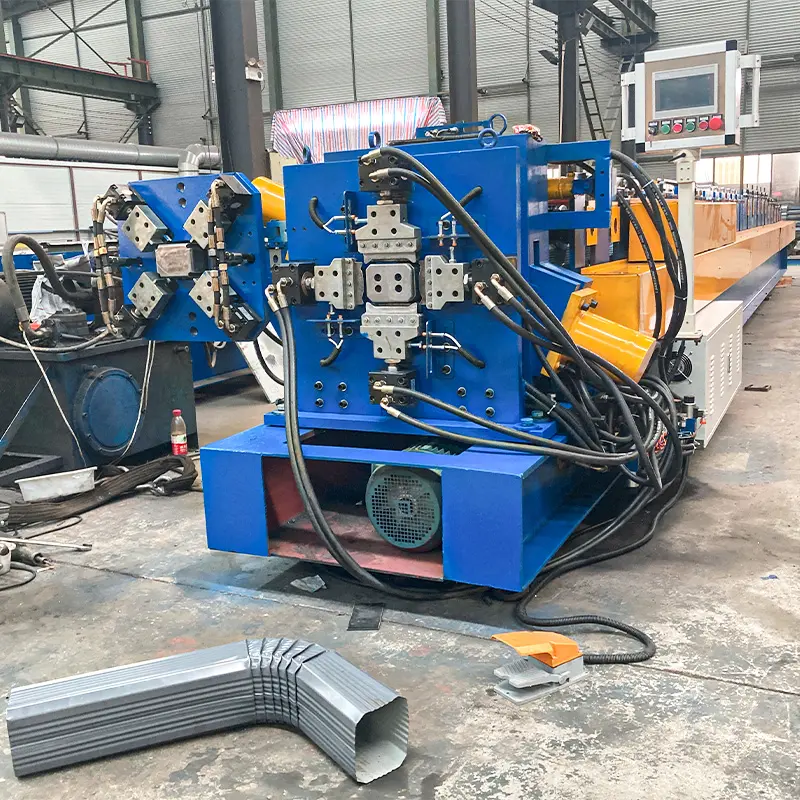
Specifications of Roll Forming Machines
The key specifications and parameters considered while selecting steel roll forming equipment are:
Size Specifications
- Length – Dimension along the forming line
- Height – Floor to top distance for accessibility
- Width – Lateral dimension across the line
- Weight – Depends on frame material and construction
Typical ranges are:
Specification | Range |
---|---|
Length | 3 – 50 meters |
Height | 1.5 – 2 meters |
Width | 1 – 3 meters |
Weight | 1500 – 25000 kg |
Length depends on number of rolling stations while height is based on ease of operation. A wider machine allows larger coil holding capacity. A heavier machine indicates sturdier construction.
Roll Changing Design
- Manual – Rollers lifted out of position manually
- automated – Powered shifting of rollers
- Quick change – Rollers detached/attached fast
Manual changing needs more downtime. Automated roll change systems allow fast profile changeovers with minimum downtime loss.
Speed and Strip Width Capacity
- Speed – up to 100 meters/minute
- Width – 50 mm to 1800 mm
- Thickness – 0.15 mm to 8 mm
Higher speeds like 100 m/min require greater horsepower and robust design. Most machines can handle sheet widths from 50 mm to 1500 mm depending on industry. Thickness capacity ranges from thin sheets to 8 mm plates.
Power and Transmission
- Main drive motor capacity – 5 kW to 250 kW
- Independent drives for certain functions
- Gearbox rating matched to loads
- Chain, belt, gear drives, and sprockets
- Overload protection and filtration
The transmission system should smoothly handle loads without overheating or undue wear and tear. Main motor capacity decides maximum forming speed.
Material Thickness Range
- Up to 8 mm thick rolls and plates
- Optimal range 0.5 mm to 2.5 mm
- Thinner strips under 0.3 mm need specialist mills
Standard profiles use 0.5 to 1.5 mm thickness. Specialist mills required for thin strips under 0.3 mm as per industry. Thicker plates need heavy-duty machines.
Roll Adjustment and Changeover
- Vertical – Shim spacers for roller height
- Horizontal – Side support adjustment
- Tilting – Angular roller adjustment
- Individual – Each roller adjusted
Roller height, angle, and lateral position need adjustment during setups. Individual and tilting adjustment allows flexibility but increases complexity.
Roll Tooling Design
Roll tooling design is key to achieving the required profile shape accurately by incremental bending. The main design aspects are:
Roll Pass Design
- Blueprint of position and sequence of roll stands
- Step-by-step bending calculations
- Ensures complete material deformation
- Minimizes thinning and stretching
- Done using special CAD software
The pass schedule is planned based on the number of rolling stations to achieve the full profile shape gradually without defects.
Roll Cluster Configuration
- Arrangement of top and bottom rolls
- Cluster spacing matches strip thickness
- Roll clearance precisely set
- Number of stations estimated initially
- Verified by trial passes
The spacing between top and bottom rollers in the cluster matches the sheet thickness to allow bending without gaps. More complex shapes need more passes.
Roller Size and Dimensions
- Diameter between 100 mm to 400 mm
- Width ~ 50 mm greater than strip
- Larger rolls for heavy loads
- Backing rolls support small rolls
The roller dimensions affect the bending forces and loads involved. Roll width should exceed strip width to fully engage the flanges.
Roll Materials
- Forged and hardened steel
- Iron or steel rolls with coating
- Chilled cast iron rolls
- Combination of materials
Hardened steel provides durability for long runs while coated rolls prevent scratching of surfaces. Cast iron is used for specialized applications.
Process Standards and Tolerances
Roll formed parts need to conform to specified standards for key dimensions and parameters.
Profile Dimensional Tolerances
Feature | Tolerance |
---|---|
Wall thickness | ±10% |
Width | ±1 mm to ±1.5 mm |
Height | ±1 mm |
Bow | 1 mm per 1000 mm |
Twist | 1° per 1000 mm |
Angular Deviation | 1° max |
Tighter tolerances are possible but increase process costs. Common allowable variations are given above.
Strip Feed Tolerances
- Parallelism – 0.5 mm over 1m length
- Squareness – 1 mm to 3 mm typically
- Flatness – 1 mm per meter width
The strip should pass through the mill without deviations to avoid profile errors.
Roll Design Standards
- ASA B209.1 – American national standard
- EN 10169 – European standards
- JIS G3141 – Japanese industrial standard
These standards guide roll materials, surface finish, dimensions, mechanical properties, testing procedures, etc. Compliance ensures quality roll performance.
Manufacturers and Suppliers
Some of the top steel roll forming machine manufacturers across geographies include:
Global Brands
- Samco Machinery (Taiwan)
- Formtek (USA)
- Gasparini (Italy)
- Kohler Maschinenbau (Germany)
- Botou Xianfa Roll Forming (China)
Chinese Manufacturers
- Joung Sun Machinery
- Jidet Forming Machinery
- Ruian Jingpus Roll Forming Machinery
- Botou Totall Roll Forming Machinery
- Hebei Tuozhan Roll Forming Equipment
Indian Manufacturers
- Spiroll Forming Machines
- Samco Emtici Engineering
- JPI Maxivator
- Trimech India
- Kulkarni Group
Price Range
Capacity | Price Range |
---|---|
Small portable | $5000 to $15000 |
Medium production | $20000 to $100000 |
Large automated | $100000 to $300000 |
Jumbo lines | Above $500000 |
Higher the output rate, number of features, and automation, higher is the overall cost of the roll forming equipment.
Chinese vs European Manufacturers
Chinese manufacturers offer cost advantage but European brands provide better quality control, precision, advanced features and reliability along with higher pricing.
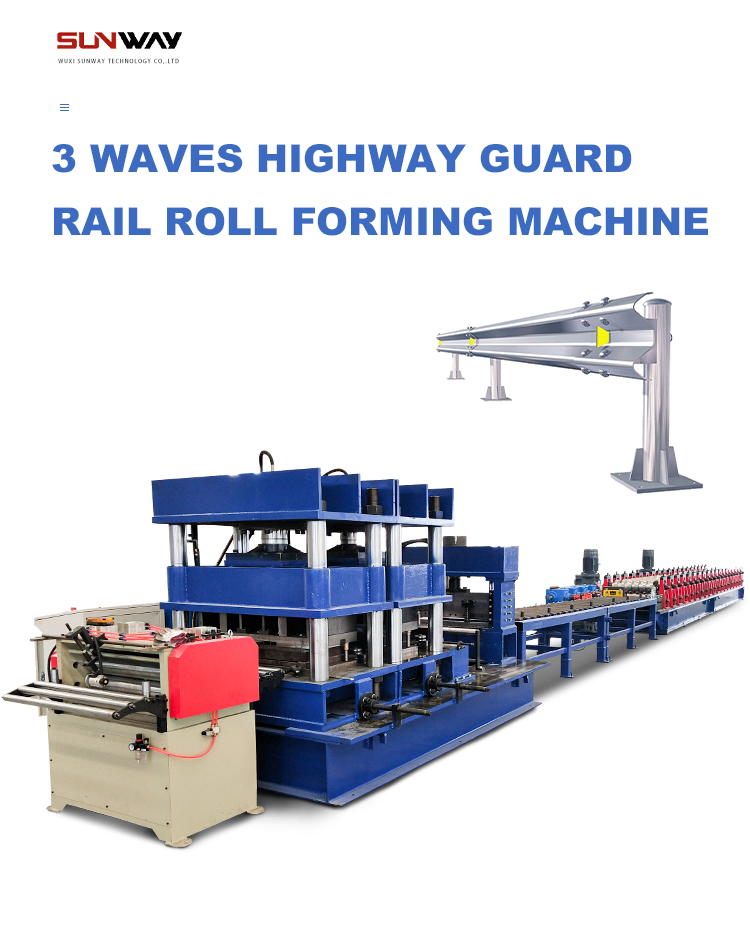
Installation and Commissioning
Proper installation and trial runs are needed before starting full production on a roll forming machine.
Site Planning and Preparation
- Level concrete or steel base
- Sufficient space around for loading coils
- Crane availability for uncoiling
- Coolant, hydraulic, and electrical connections
- Safety fences and guarding
A flat and rigid flooring minimizes vibrations and levelling issues. All peripheral equipment should be connected prior to roll former delivery.
Alignment and Leveling
- Machine properly leveled and aligned
- Check plumb across length and width
- Confirm paralleling and squareness
- Fine tune roller parallelism if needed
- Fix and fill any floor unevenness
The machine needs to be correctly aligned perpendicular and parallel to the floor plane. Any minor defects should be rectified before commissioning.
Trial Runs and Adjustment
- Test run with dummy strips
- Check strip feeding, tracking, and cutting
- Adjust roll heights and clearances
- Monitor forming process and stations
- Conduct speed trials incrementally
- Fine tune guides and controls till optimal
- Confirm profile accuracy after adjustments
- Make iterative modifications if needed
- Maintain records of final machine settings
Multiple test runs should be conducted starting from slow speed to high speed while monitoring the process. Machine settings have to be incrementally adjusted based on test results before starting production.
Safety Measures
- Install safety guards for pinch points
- Enclose guides and hazards zones
- Interlock access doors and panels
- Use two-hand control stations
- Post safety instructions and labels
- Ensure proper staff training
- Follow standard protocols during operation
Adequate safety mechanisms should be in place before clearing the machine for regular production. Workers need to be trained on all procedures and hazards.
Operation and Maintenance
For optimal performance, roll forming machines need proper operation and preventive maintenance.
Operating Guidelines
- Set machine speeds and feeds correctly
- Use recommended lubricants for rolls
- Adjust parameters only within specified range
- Control strip alignment carefully
- Handle coils using lifting equipment
- Ensure no water/moisture ingress
- Follow tool changing protocols
- Keep records of machine settings
The equipment should be operated as per the supplier’s manual for reliable and consistent output. Deviating from set parameters can cause defects.
Speed and Feed Optimization
- Start at slower forming speed
- Gradually increase up to max speed
- Ensure proper material flow without choking
- Reduce speed if strip slips or distorts
- Match feed rolls speed to forming speed
- Lubricate appropriately for higher speeds
The speed should be optimized based on the material type and thickness to avoid quality issues. Sufficient lubrication is necessary for high speed operation.
Roller Care and Lubrication
- Apply machine oil regularly on roll bearings
- Grease roll shaft ends as needed
- Clean rolls to prevent accumulations
- Replace damaged or worn out rolls
- Use coated rolls for corrosion resistance
- Ensure proper roller gap spacing
Rolls should be kept clean and lubricated. Damaged rolls will mark the surface finish. The gap between top and bottom rollers should be set precisely.
Tooling Changeover
- Plan schedule to minimize downtime
- Clean machine thoroughly before change
- Label and document existing setup
- Follow shaft/bearing removal procedure
- Adjust new roller gaps correctly
- Trial run and confirm profile before full production
Tooling changeover requires proper preparation, planning and time to avoid errors. The machine settings should be restored properly after changeover.
Troubleshooting Guide
Defect | Possible Causes |
---|---|
Buckles | Excessive strip tension, feed problems |
Profile distortion | Roller misalignment, loose components |
Surface marks | Debris on rolls, roller damage |
Burrs on cut | Worn out cutting inserts, clearances |
Oil leakage | Shaft seal damage, loose fittings |
Excessive noise | Loose fasteners, bearing damage |
Common machine problems during roll forming and solutions are listed above. Periodic inspection and maintenance prevents unplanned downtime.

How to Select a Roll Forming Machine
The main factors guiding the selection of a steel roll forming equipment are:
Required Production Rate
- Speeds up to 100 m/min possible
- High speeds need heavy duty construction
- Estimate max. rate based on order volumes
- Add buffer capacity ~20% if possible
The nominal production rate should be ascertained based on current and future projected volumes. A buffer capacity is preferred.
Material Type and Thickness
- Mild steel, stainless steel, aluminum etc.
- Thickness range – 0.3 mm to 8 mm
- Compatibility with special alloys if needed
- Capacity for thicker and harder materials
The machine should be suitable for the grades of steel coils that will be processed. Special materials may need customized features.
Profile Shape Complexity
- Number of roller stands indicate complexity
- Close roller spacing for tight bends
- Alternate bending directions
- Special profiles need customization
More complex shapes with sharp bends or alternate directions require additional roller stands and tooling expertise for design.
Length of Finished Profiles
- Standard cutoff every 1 to 6 meters
- Running lengths or custom cutoffs
- Longer profiles may need support
- Additional cutoff presses can be added
Most machines can produce fixed length profiles up to 6 m long. For running length coils, additional support and cutoff systems need to be engineered.
Budget Constraints
- Initial cost – $25,000 to $500,000
- Low cost models have capacity limitations
- Automation increases price
- Import duty, taxes additional
- Secondary processing needed?
Sufficient budget allocation is necessary for the required production scale and features. Total costs depend on customization, automation and secondary processes needed.
Advantages of Roll Forming Process
Roll forming offers significant benefits that make it suitable for high productivity manufacture of structural steel profiles:
High Production Rates
- Up to 100 meters per minute
- Continuous operation with high outputs
- Reduced manpower requirement
- Superior to press brakes or fabrication
- Low cycle times and operation cost
The continuous production with high line speeds results in very high output rates that other processes cannot match.
Consistent and Excellent Profile Quality
- Ensures uniformity along the length
- Dimensional accuracy up to ±1mm
- Fine surface finish
- Repeatable process with precision
- Minimal need for secondary finishing
The incremental forming with precision rollers produces consistent quality with fine tolerances across long component lengths.
Flexible Profile and Shape Design
- Different configurations of roll stands
- Various profile shapes possible
- Custom tooling design for special profiles
- Allows frequent profile changes
- Useful for small batches and variants
With customized roll tooling design, a variety of beam sections can be produced on the same machine with quick changeovers.
Cost Efficiency and Savings
- Lower cost than fabrication
- High material yield up to 90%
- Scrap minimized compared to stamping
- Reduced welding, drilling requirements
- Savings from energy, space and labor
- Low maintenance costs
The high material utilization, low conversion costs and automation results in significant cost benefits compared to other manufacturing processes.
Applicable to Diverse Materials
- All types of steel and metal coils
- Aluminum, copper, brass
- Special alloys, cladded materials
- Pre-painted and coated coils
- Even composites and plastic possible
Roll forming can handle a wide range of metallic materials from low carbon steel to exotics alloys along with painted, coated and laminated coils.
Limitations of Roll Forming Process
Despite the benefits, roll forming also has certain inherent limitations:
High Initial Tooling Cost
- Roll design and pass scheduling
- Trial simulations and tests
- Tooling cost €10000 upwards
- Time consuming process
- Minor design changes need rework
The initial tooling design requires extensive engineering effort and has a long lead time. Design changes after tooling involves additional time and cost.
Fixed Cross-Section Profile
- Cannot make variable shapes
- Limited to longitudinal profiles
- Cannot form complex 3D geometries
- Parts require joining for closed sections
Only fixed cross-section profiles along the length can be produced. Making closed or tapered sections requires additional fabrication and joining.
Strength Limitation of Thin Materials
- Better for under 2 mm thickness
- Thicker strips prone to splitting
- High strength steels crack during bending
- Maximum bend radius constraints
Very thin and high strength materials are susceptible to cracking during roll forming process and have certain forming limits.
Not Suitable for Short Lengths
- Practical minimum ~ 0.5 meter
- Short pieces lose dimensional accuracy
- start up time affects output
- Difficult to roll small segments
- Other methods better for small parts
The roll forming process has limitations when profiling short length components due to startup effects. Press brakes are better for small quantities.
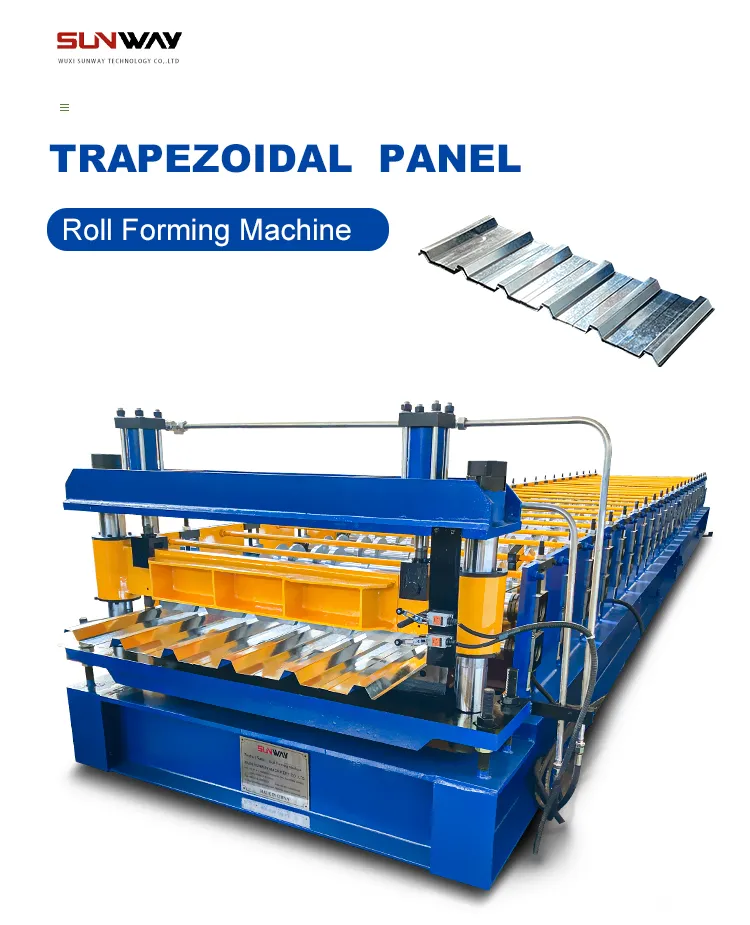
Conclusion
Roll forming machinery offers continuous and precision forming of metal strips into customized longitudinal profiles. This detailed guide has encompassed all the key information regarding configurations, components, specifications, operations and applications of steel roll forming equipment. The advantages of flexibility, speed and accuracy provide superior manufacturing solutions for long length structural framing members. However, the process also has certain limitations when it comes to short lengths, tapered geometries and thin exotic alloys. With appropriate design and selection, roll forming lines provide efficient mass production solutions for metal profile requirements arising across automobile, railways, construction, infrastructure and allied industries.
FAQ
What are the different types of roll forming machines?
The main types are coil lines, modular machines, portable roll formers, custom profile mills, and shape rolling mills for variable sections.
How does the roll forming process work?
It works by continuously feeding metal strips through a series of roller stations that apply progressive bending forces to gradually form the strip into the desired profile shape.
What materials can be roll formed?
It can form all kinds of steel including mild steel, stainless steel, galvanized steel, and aluminum. Special alloys and extrusions are also possible with some restrictions.
What profiles can be produced by roll forming?
Angle sections, channels, roofing sheets, wall panels, rectangular and round tubes, I-beams, rails, racks, door frames etc. Custom profiles are also feasible.
What is the cost of roll forming equipment?
The price range is $5000 to $500,000 depending on output rate, features, automation level and optional secondary processing.
What are the benefits of roll forming?
High speeds, excellent quality and tolerances, flexibility, cost efficiency, material savings, suitability for mass production are the major benefits.
What are the limitations of the roll forming process?
Fixed cross-sections only, high initial tooling cost and time, issues with short lengths, variable sections, and limitation on using very thin and high tensile materials.
How to choose the right roll forming machine?
Consider production volumes, material specifications, profile shape complexity, length of finished parts, available budget, and future expansion plans.
How is roll forming different from extrusion?
In extrusion, the profile is formed by pushing material through a die opening while roll forming gradually bends the strip through a series of roller dies into shape.
How to maintain roll forming equipment?
Follow the operator’s manual for periodic lubrication, inspection and parts replacement. Keep rolls clean, change worn items, log machine settings, adjust alignments as needed.