Steel deck roll forming machines are essential equipment for manufacturing corrugated steel decking for buildings and infrastructure. This comprehensive guide provides detailed information on all aspects of steel deck roll forming machines from types, technical specifications, applications, installation, operation and maintenance to supplier selection and pricing.
Overview of Steel Deck Roll Forming Machines
Steel deck roll forming machine is equipment that creates corrugated steel decking sheets by bending and rolling steel coil continuously into the desired ribbed profile. Steel decking provides sturdy support for concrete floors in buildings and infrastructure.
Roll forming machines transform flat steel coil stock into finished decking panels by passing the sheet longitudinally through consecutive rolling stations. Each rolling station progressively forms the sheet to the specified profile through a series of rollers.
Steel deck roll forming lines produce decking much faster, efficiently and accurately compared to traditional press braking or bending methods. Automated machines ensure consistent quality and reduce labor requirements.
Key Facts About Steel Deck Roll Forming Equipment:
- Produces corrugated steel decking from coil stock
- Uses roll forming technique to bend sheets into ribbed deck panels
- Output is continuous lengths of finished decking
- Automated for high speeds and precision forming
- Flexible equipment to make different deck profiles
- Requires less space than press braking or bending
- Lower operational costs than other decking fabrication
Types of Steel Deck Roll Forming Machines
There are two main types of steel deck roll forming machines:
Fixed Length Roll Formers
These simpler machines produce set lengths of steel decking like 2 feet or 4 feet long sheets.
- Preferred for lower capacity production
- Use a cutting device to cut each sheet to fixed size
- Changeover to new lengths takes time
- Starts and stops for each sheet reduce output speed
Continuous Roll Forming Lines
Continuous roll formers produce decking in longer undeformed lengths from the input coil.
- Higher output capacities at faster line speeds
- No stopping except for coil changes so smoother operation
- Length is set by customer during installation
- Common configurations up to 150 feet lengths
- Cut-off device shears finished sheets to required size
- Quicker changeover between different deck profiles
Typical Decking Profiles Formed on Roll Forming Machines
- Narrow ribbed sheets (1.5 inches tall ribs)
- Intermediate ribbed sheets (3 inches tall ribs)
- Wide ribbed sheets (6 inches tall ribs)
- Cellular or fluted decking
- Sinusoidal, trapezoidal and curved profiles
- Self-mating and interlocking decking
- Acoustical and composite floor decking
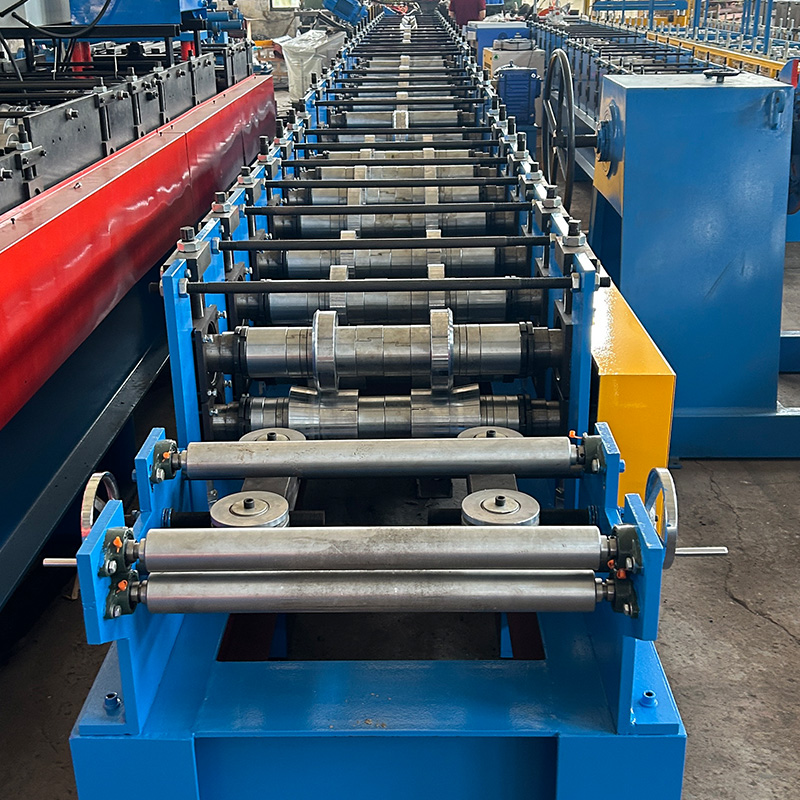
Roll Forming Process for Steel Deck Panels
The roll forming process bends steel coil into deck sheeting through consecutive stages:
Uncoiling – Coil stock is loaded onto a de-coiler which unrolls sheet into the line. Brake tensioning controls uncoiling.
Feeding – Feed rollers grip the sheet and pull it through the equipment at a constant speed.
Leveling – Levelers remove any coil curvature and flatten the sheet before roll forming.
Pre-punching – Optional punches create holes for fasteners, utilities etc.
Roll forming – The sheet progresses through groups of rollers which bend it incrementally into the ribbed decking profile.
Calibration – Final rollers calibrate rib dimensions to exact tolerance.
Cut-off – A flying shear or saw cuts sheets to specified length offline or severs individual sheets in fixed length lines.
Stacking – Conveyors arrange finished decking sheets for downstream processes.
Roll Forming Rollers for Steel Decking
The key part of a steel deck roll former are the rolling dies. Different combinations of rolling dies produce the various decking profiles. The main roller types are:
- Forming rollers – Progressively bend sheet into corrugated rib shape.
- Calibration rollers – Get exact rib height, width and angle.
- Idler rollers – Provide support between forming stations.
- Slotting rollers – Punch dimple slots in valley of deck for composite action.
- Crimping rollers – Crimp ribs for interlocking ends on certain deck.
The longitudinal rolling dies are mounted inline on shafts in each station frame. Stations can be added or removed to vary complexity of profile. Rollers are machined to precision tolerances and made from ultra-hard materials like carbide for longevity.
Main Components of Steel Deck Roll Forming Machines
Complete roll forming lines comprise a series of components for handling and shaping the steel:
Input Material System
- De-coiler – Holds steel coil and unrolls sheet into the line. Includes an unwind motor and coil tensioning.
- Feeder – Grips sheet and feeds into first station. Consists of feed rolls and servo motor.
- Leveler – Flattens sheet before roll forming. Can be 3-roller, 5-roller or 7-roller leveler.
- Sheet guide – Guides flat sheet towards the roll former. Uses adjustable edge guides.
Roll Forming System
- Roll forming stations – Each station has a stand, roll shafts, bearings, rolls and drive. Number of stations varies by profile complexity.
- Forming rolls – Special rolls that shape the ribs and valleys in each station.
- Calibration rolls – Finalize rib dimensions after forming rolls.
- Crimping and slotting rolls – Additional operations like crimping or slot punching if required.
- Roll shafts – Hardened steel shafts that support the rolls.
- Roll bearings – Heavy duty bearings like plummer blocks suit the loads.
- Roll drives – Electric motors drive each station screw or belt drives provide power.
- Roll change trolleys – Special trolleys to assist exchange of rollers.
Output Material System
- Runout table – Extends finished deck sheets for downstream processes.
- Cut-off device – Flying shear or saw cuts sheets to length.
- Stacker – Collects cut sheets and stacks them off the line.
Control System
- PLC control – Controls line speed, feedback signals, monitors sensors.
- HMI touchscreen – Operator interface to control, start/stop and monitor line.
- Servo drives – Closed loop control of motors and precision speed.
- Sensors – Proximity sensors to detect material position and speed.
- Safety features – E-stops, guarding, safety gates for operator protection.
Applications and Uses of Roll Formed Steel Decking
The decking made on steel deck roll forming machines has many applications:
Floor Decking
- Concrete floor slab reinforcement in buildings
- Composite floor deck for integrated concrete topping
- Acoustical decking with perforations for sound absorption
Roof Decking
- Roofing substrate instead of wood or concrete decks
- Composite roof deck filled with insulation
- Acoustical roof deck for soundproofing
Wall Panels
- Interior wall cladding, partitions and mezzanines
- Curtain walls and spandrel panels
- Structural stud walls with sheathing
Other Applications
- Stairs, walkways, catwalks and platforms
- Culverts, tunnels, trenches and drainage
- Trailers, motor homes and mobile shelters
- Scaffolding, shoring and concrete forming
Steel decking provides sturdy support for construction loads while being lightweight for efficiency. The ribbed shape with embossments increase strength while using less steel.
Specifications for Steel Deck Roll Forming Machines
Steel deck roll forming lines are available in different sizes with various specifications:
Specification | Typical Size/Rating |
---|---|
Line speed | 16 – 100 ft/min |
Input sheet width | 24 – 72 inches |
Finished sheet length | 2 – 150 feet |
Steel thickness | 20 – 22 gauge (0.8 – 0.036 inches) |
Steel yield strength | 33 – 80 ksi |
Roll stations | 10 – 26 stations |
Line power | 15 – 50 kW |
Roll changing | Manual or automatic |
Controls | PLC with HMI |
Structural design | Per building codes |
- Machines can be customized for specialized decking requirements.
- Speeds from 16 ft/min for complex long sheets up to 100 ft/min for high volume.
- Widths accommodate 24 inch to 72 inch input coil.
- Common length range is 2 to 20 feet but can be 150 feet.
- Thicker material may need lower speeds to avoid defects.
- Yield strength affects force needed for rolling.
- More stations needed for profiles like celluar deck.
- Power requirement depends on speed, force and automation.
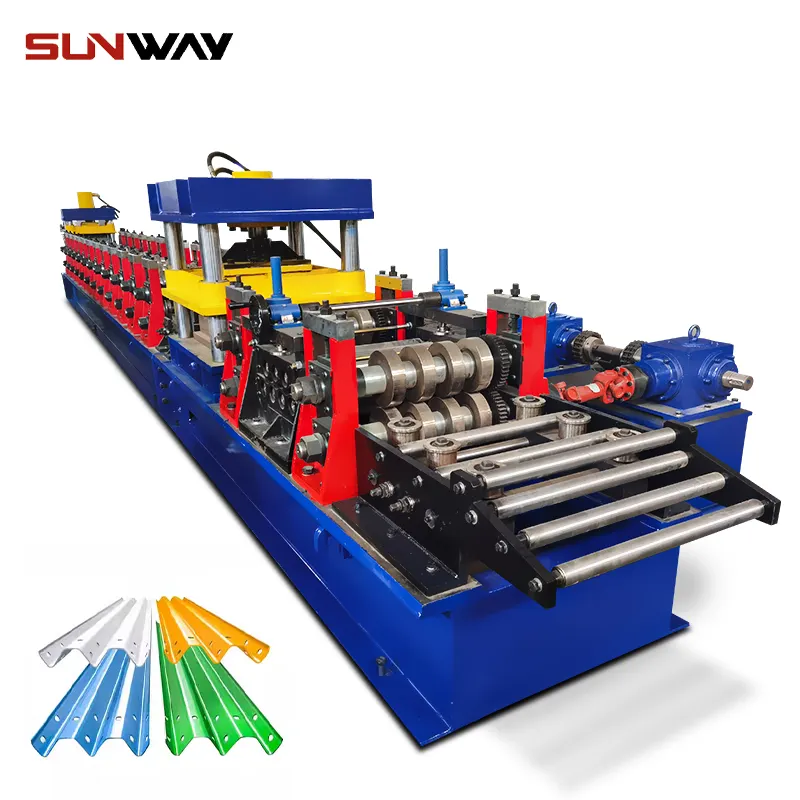
Design Standards for Roll Formed Steel Decking
There are two main industry standards covering roll formed steel decking:
- American Iron and Steel Institute (AISI) – AISI S100-16 North American Specification for the Design of Cold-Formed Steel Structural Members.
- Steel Deck Institute (SDI) – SDI Publication No. 30 Design Manual for Composite Decks, Form Decks, Roof Decks.
The AISI standard has detailed provisions for cold forming loads, stresses and strains. This ensures the decking has adequate strength and rigidity.
The SDI standard gives guidance on decking profiles, material specs, testing methods, design spans, and installation. Manufacturers produce decking according to SDI profiles.
Both standards include factors of safety, testing validation, quality conformance and design optimization. The standards are periodically updated to reflect latest industry practices and research.
Installation of Roll Formed Steel Decking
Proper installation of finished steel decking ensures its strength and performance:
- Place decking on supporting steel framework. Endlaps over supports.
- Use self-drilling fasteners like screws to attach to structure.
- Position with correct side and rib orientation.
- Maintain minimum bearing lengths on supports.
- Install supplemental deck reinforcement at openings.
- Locate endlaps away from high stress areas.
- Seal sidelaps with tape, sealant or button punching.
- Install safety netting, edge protection and maintenance access.
- Ensure electrical continuity if required.
- Touch up paint damage during installation.
Reference the SDI manual for detailed decking attachment techniques. Proper site storage, safety and handling prevents damage.
Operation of Steel Deck Roll Forming Machines
Running a steel deck roll forming line involves these key steps:
1. Safety checks – Ensure proper guarding, E-stops, gates and no slip hazards.
2. Inspection – Check rollers, bearings, guides, sensors before startup.
3. Line setup – Stage correct coils, decks, rolls, sheer etc.
4. Speeds – Set the run speed at the HMI and test run.
5. Trial run – Run a test sheet through the entire line and check quality.
6. Start production – Feed the coil end into the machine to start the process.
7. Monitoring – Monitor line operation and inspect decking quality periodically.
8. Sheet change – When coil is done, stop the line before feeding the next coil.
9. Maintenance – Perform cleaning, lubrication, adjustments during breaks.
10. Safety procedures – Follow all operational and safety procedures.
Proper operator training is key to safely running production and preventing problems. Develop detailed standard operating procedures.
Maintenance of Steel Deck Roll Forming Equipment
Preventative maintenance protects roll tooling and ensures high uptime:
- Daily cleanup – Remove metal chips, oil and debris on rolls and guides.
- Lubrication – Apply right lubricant on bearings, gears and friction surfaces.
- Fastener check – Ensure tightness on roll shafts, guards and drives.
- Bearing check – Inspect for noise, heating and runout.
- Roll inspection – Check for wear, scores or geometry damage.
- Realign – Realign shafts, rolls and guides if deviations are detected.
- Sensor calibration – Recalibrate proximity and access sensors periodically.
Schedule periodic major maintenance during plant shutdowns:
- Roller change – Change worn rollers to avoid damage. Keep spares.
- Leveler service – Inspect and service leveling rollers as required.
- Drive service – Check belts, motors, gearboxes, chains and shafts.
- Overhaul – Complete overhaul of linear guides, cylinders, valves etc.
Troubleshooting Steel Deck Roll Forming Lines
Some common roll forming problems and remedies include:
Defect | Possible Causes | Corrective Actions |
---|---|---|
Incorrect profile | Worn/damaged rolls | Replace affected rolls |
Misaligned rolls | Realign roll shafts and guides | |
Buckled sheet | Sheet feeding issue | Adjust feed rolls and guides |
Sheet stackup | Clean rollers and guides | |
Forming stress | Reduce roll forming force | |
Wavy sheet | Bad coil stock | Improve stock quality control |
Leveler problem | Inspect, adjust or service leveler | |
Roll marking | Reduce roll pressure, lubricate | |
Scrap pieces | Cut-off timing off | Re-calibrate shear on HMI |
Feed length off | Correct line speed and feed length |
Use sensors along the line to identify sources of defects and make adjustments promptly.
How to Select A Steel Deck Roll Forming Machine Supplier
The right supplier ensures a good quality and productive roll forming line. Consider these criteria when choosing:
- Experience in delivering steel decking machines specifically. Avoid generalist roll former builders.
- Engineering expertise in robust roll designs and mill integration.Check designer qualifications.
- Able to build your required deck profiles to execute design and functionality.
- Has supplied similar lines to other steel decking manufacturers preferably.
- Includes proprietary components like roll tooling, levelers and cut-offs designed for steel deck.
- Production capacity to manufacture and test the line thoroughly before shipping.
- Services available for maintenance training, spare parts, upgrades.
- Responsive technical support for troubleshooting issues.
- Complies with CE, UL and OSHA standards. Provides documentation.
- Flexible on modifying machine to special requirements.
- Competitive pricing for performance level offered.
Choose a manufacture partner rather than just an equipment supplier for the long term.
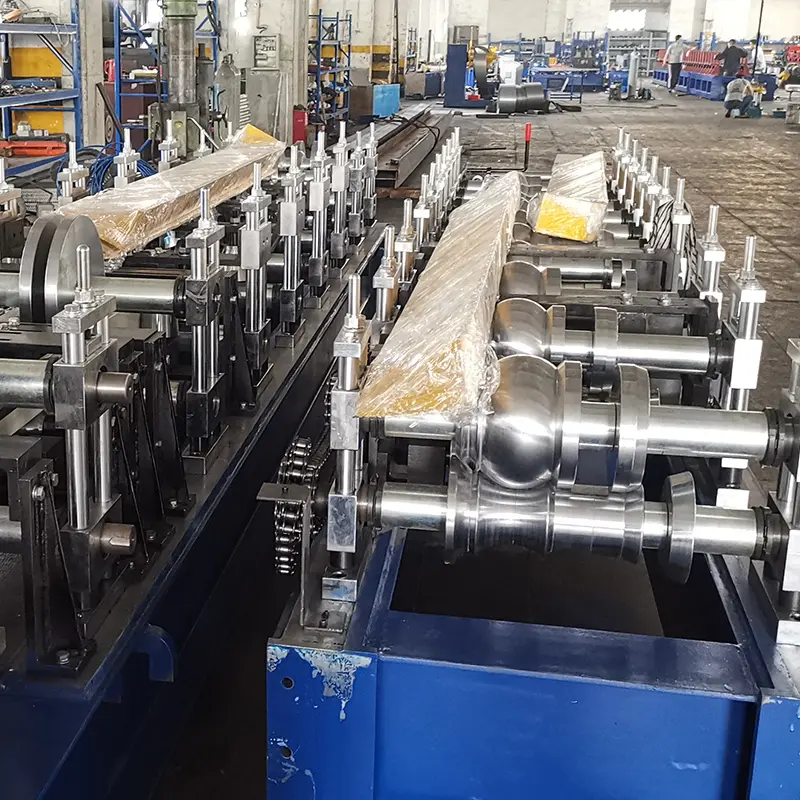
Pricing of Steel Deck Roll Forming Machines
Cost depends on steel deck roll former length, speed, automation level and options:
Machine Rating | Price Range |
---|---|
Prototype/Pilot Line | $60,000 – $150,000 |
Low Production | $150,000 – $500,000 |
Medium Production | $300,000 – $1 Million |
High Production | $500,000 – $5 Million |
- Prototype lines for R&D, short runs and low volume.
- Production from 10,000 sqft/month to above 100,000 sqft/month.
- Speeds from 16 ft/min entry level up to 100 ft/min high speed.
- Fixed length or continuous configurations.
- Automation adds cost but improves productivity.
- Additional options like vision systems, robotics etc further increase price.
- Used and rebuilt equipment costs 50% less approximately.
Get itemized quotes from shortlisted suppliers on your exact requirements for accurate price comparison.
Pros and Cons of Steel Deck Roll Forming
Advantages
- High production rates up to 130 ft/min line speed.
- Consistent quality with automated precision forming.
- Just-in-time low inventory production.
- Flexible equipment produces different profiles fast.
- Compact equipment requires less factory space.
- Safer automated process than press braking.
- Lower operational costs than other methods.
- Easy integration with upstream and downstream processes.
Disadvantages
- Higher initial capital investment than press brakes.
- Require skilled personnel for specialized maintenance.
- Roll consumables last finite time before replacement.
- Profile changes need roll changeover.
- Limited thickness and yield strength ratings.
- Not ideal for low volume or custom work.
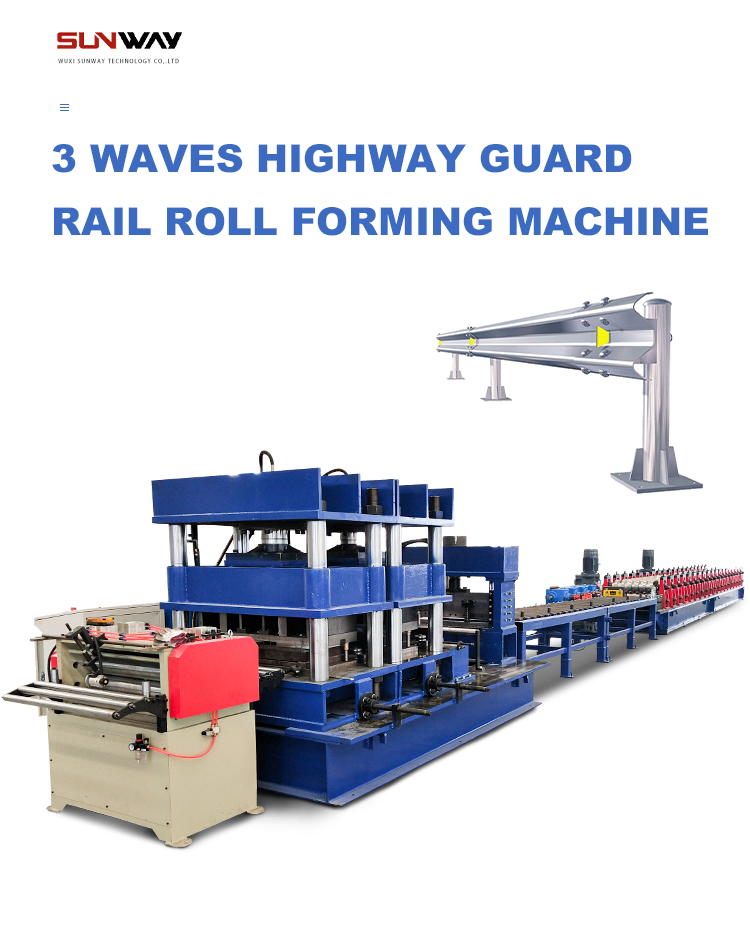
FAQ
What types of steels can be roll formed into decking?
Carbon steels and low alloy steels specified for cold forming like ASTM A1008, A1011, A653, A792 work well. High strength low alloy steels require caution. Stainless steel needs special roll materials.
What thickness range can decking machines accommodate?
Typical thicknesses are 20 to 22 gauge. Can handle 0.028” to 0.075″ range with appropriate roll capacity. Thinner material may require support rolls to avoid buckling.
How long do roll forming rollers last?
Hardened tool steel rolls last 500,000 to 1 million linear feet under proper conditions. Carbide rolls offer 5-10X life but cost 5-6X more. Proper maintenance extends longevity.
What safety measures are required on the line?
Full guarding, emergency stops, safety gates at infeed and outfeed, operator training and lockout procedures. Mandatory for CE and OSHA compliance.
How to improve line efficiency and uptime?
Good preventive maintenance, operator training, keeping extra consumable spares, and utilizing production data to optimize schedules.
What is the typical delivery time for a steel deck roll forming machine?
Lead time ranges from 8 to 16 weeks depending on line specifications. Prototype units can ship faster. Planning 6 months ahead is recommended.