Overview of Double Stage Roll Forming Machines
Double stage roll forming machines are industrial equipment used to bend and form metal sheets into customized profiles and shapes. They utilize two sets of rolls arranged in a staggered inline configuration to incrementally bend the sheet in two stages, allowing more complex and accurate forms to be created.
Key features of double stage roll forming machines:
Feature | Description |
---|---|
Two roll forming stages | Contains two sets of roller die stations arranged consecutively to bend the sheet in two steps |
Advanced profiling | Complex shapes and profiles can be formed due to two-stage incremental bending |
Accuracy | Precise calibration between the upper and lower rollers ensures high forming accuracy |
Flexibility | Quick roll change systems allow fast profile changeovers |
Efficiency | Automated inline process improves output and reduces labor |
Cost-effective | Lower tooling costs compared to other bending methods |
Types of Double Stage Roll Forming Machines
There are two main types of double stage roll forming machines:
Horizontal Two-Stage Roll Formers
- Sheet is fed horizontally through two inline roller stations
- Compact footprint, flexible layouts
- Lower forming power requirements
- Suitable for short to medium length profiles
Vertical Two-Stage Roll Formers
- Sheet is fed vertically through upper and lower roller beds
- Larger footprint, higher forming forces
- Handles longer profiles and sheets
- Increased forming accuracy for complex shapes
Main Components
Double stage roll forming machines consist of:
- Uncoiler: Feeds metal coil stock into the roll line
- Straightener: Removes coil curvature and aligns the sheet
- First stage roller dies: Initial incremental bending of sheet
- Second stage roller dies: Finish bending sheet to final profile
- Servo motor drives: Provide synchronized motion control
- Punching units: Optional perforating, cutting, punching
- Exit tables: Supports formed profile and straightens
- Controller: Controls the sequential motion and die actuation
Design and Functional Standards
Double stage roll formers are designed to standards including:
- ISO 9001 – Quality management
- CE safety certification
- ISO 12100 – Safety of machinery
- Electromagnetic compatibility standards
Machines are built for heavy duty industrial operation with features including:
- Steel welded framework construction
- Hardened rollers and dies
- Sealed lubricated bearings
- Overload protection sensors
- Guards meeting safety codes
Precision components ensure forming accuracy:
- Roller parallelism ±0.02mm
- Roller surface finish 1.6μm
- High gearbox stability <2 arcmin
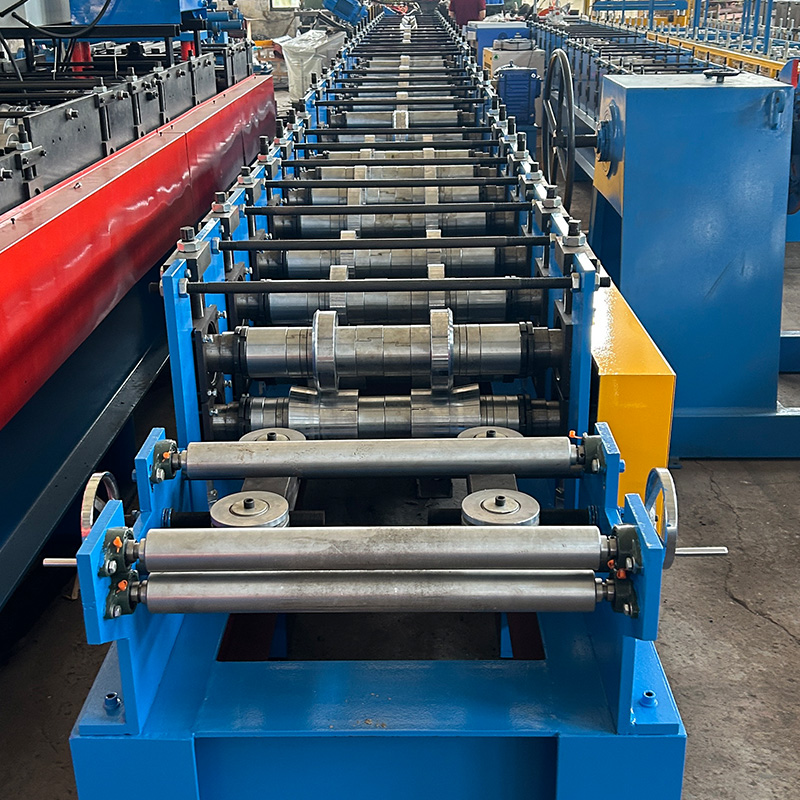
Applications of Double Stage Roll Forming
Double stage roll formers are ideal for producing:
Profile applications | Industry usage |
---|---|
Metal roofing panels | Construction, infrastructure |
Wall cladding | Construction, architecture |
Structural frames | Construction, automotive |
Rack and shelf | Warehousing, retail |
Highway guardrails | Transportation infrastructure |
Door frames | Construction, infrastructure |
Solar panel frames | Renewable energy |
Benefits of using double stage roll forming:
- Complex channel, box and frame geometries
- Increased dimensional accuracy
- Higher production speeds
- Reduced tooling costs
- Just-in-time production
Equipment Specifications
Double stage roll forming machines are available in standard and custom configurations:
Specification | Details |
---|---|
Forming length | 1m – 10m standard (custom on request) |
Width capacity | Up to 1650mm (65″) |
Material thickness | 0.3mm – 3mm steel and aluminum |
Roller diameter | ≥150mm hardened steel |
Roller adjustment | ±0.02mm precision |
Forming speed | 10 – 25 m/min standard (customizable) |
Drive motors | servo, geared AC vector or variable frequency |
Machine control | PLC and HMI touchscreen |
Noise level | <80 dB with sound enclosure |
Machine Layout Styles
- Compact layout – Tight footprint conserving space
- Accessible layout – Open access for easy maintenance
- Flexible layout – Modular sections for optional accessories
- Custom layout – Tailored to product requirements
Material Handling Equipment
- Coil loading systems – Power or manual reel loading
- Coil car – Multi-ton coil racks for quick loading
- Decoiler – Pre-straighten and decoil metal coils
- Looping pit – Allows speed differences between stages
- Exit tables – Supports and straightens finished profiles
- Conveyor system – Transports output to next operation
Additional Options
- Punching – Cutouts, louvres, holes, slots
- Embossing – Patterned impressions on surface
- Quality inspection – Gauges for checking thickness, camber
- Stacking – Automatic stacking and counting
- Bending – Post-forming bends and shapes
- Materials – Specialty metals like brass, copper
Installation Requirements
- Rigid level floor to withstand machine forces
- Minimum 4m x 2m space for small units
- 3 phase power supply with 30-50kVA capacity
- Compressed air line (5-7 bar)
- Exhaust systems for fumes
Site Preparation
- Concrete foundation with anchors to secure machine
- Services installation – trenches and conduits
- Lifting gear – cranes, jacks to position machine
- Lighting, access platforms and railings as needed
Operations and Control
Typical Production Sequence
- Load metal coil on uncoiler
- Sheet feeds into leveler and first stage rollers
- Forming at first stage bends sheet incrementally
- Sheet transfers to second stage with looping
- Second stage completes bending to final profile
- Formed stock exits to table or conveyor
- Operator stacks finished pieces
Control Modes
- Manual – Individual motor JOG functions
- Semi-automatic – Auto run with manual prompts
- Fully automatic – Executes entire sequence by program
- Recipe memory – Stores programs for each profile
Operator Interface
- Color touchscreen HMI
- Graphical display with machine animations
- Function buttons for manual control
- Displays machine status, sensors, faults
- Programming interface
Communication Interface
- Industrial Ethernet or fieldbus
- OPC server data exchange
- Remote diagnostics, monitoring and control
- Data logging of production
- Networking to management systems
Maintenance Procedures
Regular maintenance activities:
Task | Schedule |
---|---|
Inspect roll tooling | Daily |
Monitor lubrication levels | Daily |
Clean machine debris | Daily |
Functional testing | Weekly |
Check belt/chain tension | Weekly |
Check hydraulic pressure | Weekly |
Inspect electrical wiring | Monthly |
Backup control programs | Monthly |
Check roll parallelism | 6 months |
Bearing lubrication | 6 months |
Hydraulic fluid change | Annually |
Calibrate sensors | Annually |
Maintenance Safety
- Follow manufacturer lockout procedures before maintenance
- Allow components to cool before servicing
- Use appropriate lifts for heavy parts
- Ensure pneumatic pressure is exhausted
- Employ proper tools to avoid damage
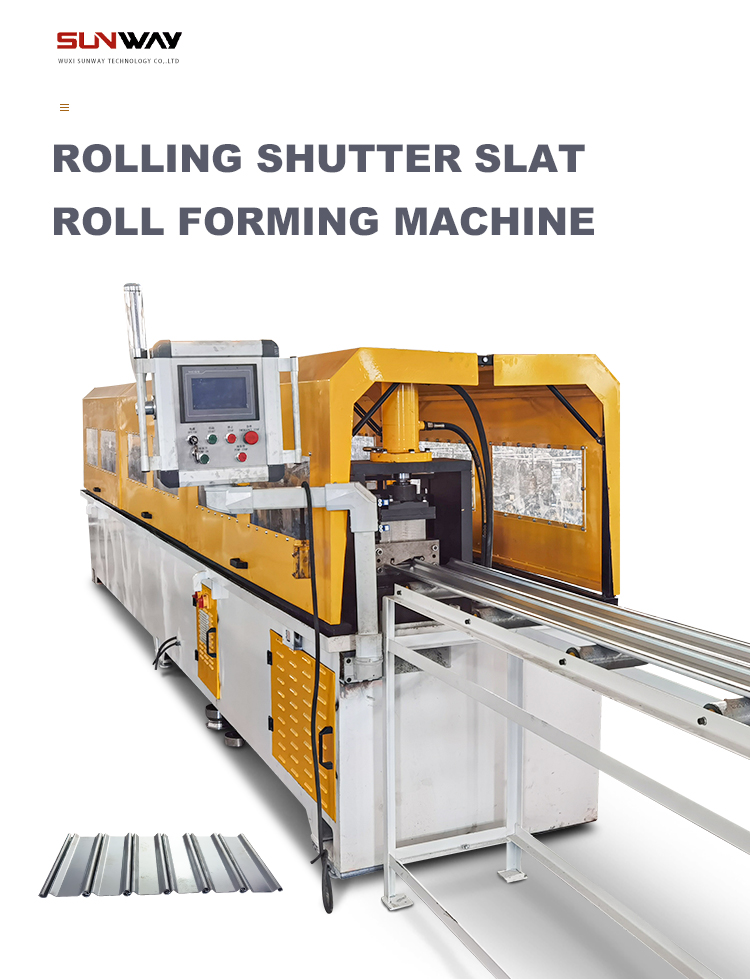
Roll Tooling Design and Management
- Roll tooling consists of top and bottom contoured dies
- Carbide inserts provide long service life
- Progressive dies bend profile in stages
- Quick change systems for fast die changeovers
- Tooling inventory stored on racks
- RFID tags for tool identification
- Specialized tools for difficult alloys
Roll Design
- 3D CAD modeling and simulation
- Iterative design approach
- FEA analysis for stress levels
- Validation through sample production
Tool Management System
- Organized storage with identification
- Computerized records of tools
- Retrieval for production
- Resharpening and refurbishment
- Monitoring of tool life cycles
Buying Considerations for Double Stage Roll Forming Machines
Purchasing double stage roll forming machines requires consideration of:
Purchase Factors | Details |
---|---|
Production needs | Profile types, volumes, sheet sizes |
Product precision and speed | Tolerances, surface finish, throughput |
Operation costs | Labor, maintenance, tooling factors |
Production flexibility | Fast changeovers, growth potential |
Available space | Machine footprint limitations |
Control requirements | Level of automation, data interface |
Safety standards | Guarding, electromagnetic compliance |
Vendor reputation | Experience, installations, service |
Pricing | Purchase, shipping, import duties |
Warranties | Coverage periods, limitations |
Requesting Quotes
- Prepare RFQ with product specifications required
- Compare machine configurations and layout options
- Review options for material handling and automation
- Consider services – training, installation, spare parts
- Evaluate vendors on expertise, quality, support capabilities
Key Suppliers
Some leading double stage roll forming machine manufacturers include:
- Mazzella Companies
- Formtek
- Samco Machinery
- Bradbury Group
- Dimeco
- Metform International
- Form Process Engineering
- Jouanel Industrie
Pricing varies widely based on configurations but typical range is $100,000 to $500,000.
Comparing Single and Double Stage Roll Forming Machines
Machine | Advantages | Disadvantages |
---|---|---|
Single Stage | Lower cost equipment Simpler layout Short to mid profiles | Limited profiling ability Lower accuracy |
Double Stage | ex shapes High precision Long part lengths | Slower production rate Higher machine cost Larger footprint |
Double stage rollers have extended capabilities for difficult profiles but have higher capital and operating costs. Single stage machines are advantageous for simpler, shorter products.
Roll Forming Versus Press Brake Bending
Bending Method | Pros | Cons |
---|---|---|
Roll forming | Continuous production Labor efficiency Consistent quality Low tooling cost | Only linear profiles Lengthy machine Fixed initial investment |
Press braking | Short production runs End forming flexibility 3D part geometries | Batch operation High tooling cost Operator skill required |
Roll formed parts excel in long production runs but press brakes allow short batch flexibility.
Limitations and Challenges of Double Stage Roll Forming
Some limitations include:
- Only linear profiles can be produced
- Lengthy equipment requiring large facility
- Initial high cost of investment
- Dedicated to high volume production
- Design and debugging of tooling can be time consuming
- Adjustments needed for thickness and hardness changes
Latest Innovations in Double Stage Roll Forming Technology
- Electromechanical actuation for faster, more accurate die movements
- Servo motor drives for dynamic speed and tension control
- Intelligent assist systems to aid operators
- Quick-change tooling systems
- Inline correction of longitudinal bow and twist
- Advanced safety designs with safeguarding robots
- Internet-connected systems for monitoring and diagnostics
- Vision systems for quality inspection and adaptive control
- Laser-guided cobots for material handling automation
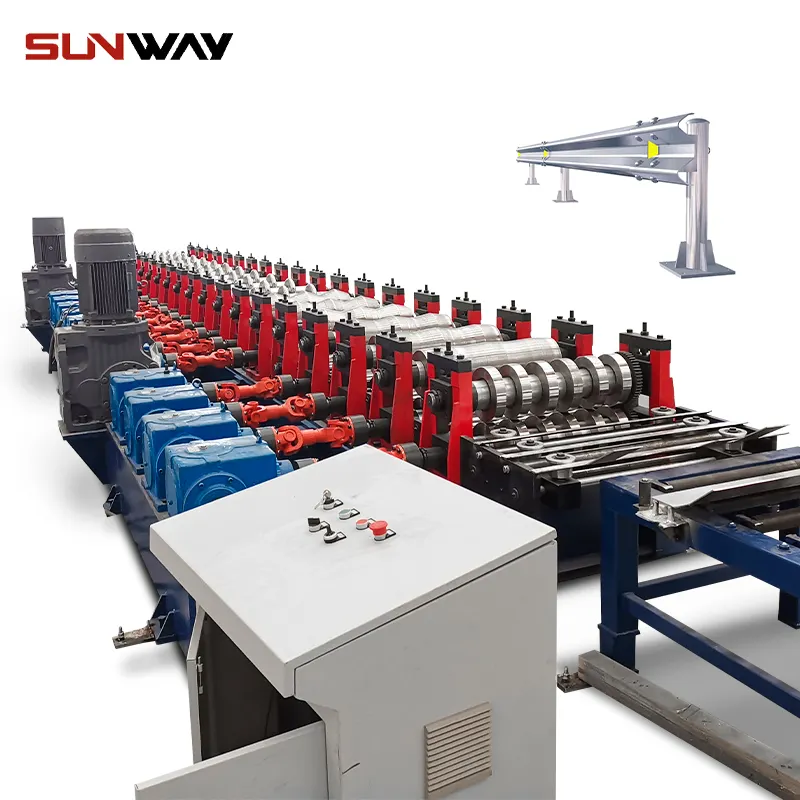
Roll Formed Products and Applications
Roll formed components are ubiquitous across industries including:
Construction: Roofing, siding, purlins, studs, floor joists, wall panels, ducting, drainage
Infrastructure: Guardrails, catwalks, breeze ways, panels, enclosures
Automotive: Frames, bumpers, rails, panels
Appliances: Housings, supports, racks, frames, brackets
Aerospace: Frame stringers, brackets, fittings, clips
Furniture: Legs, rails, enclosures, shelves, racks
Packaging: Rails, dividers, enclosures, pallets
Solar: Mounting racks, collectors, framing
FAQ
What are the advantages of double stage roll forming?
Double stage roll forming enables more complex shapes, higher precision, and improved material properties compared to single stage machines. The two bending stages allow more controlled stress relieving.
What should I consider when designing roll forming tooling?
Tooling design requires high precision modeling and FEA analysis to develop the progressive die stages. Prototype testing validates the tooling performance before final hardening and production use.
How long does a roll forming machine last?
With proper operation and maintenance, the lifespan of a double stage roll forming machine typically exceeds 20 years or more of continual use. Robust construction and mechanical design ensures longevity.
Can a double stage roll former make curved profiles?
No, roll forming only makes linear profiles since bending occurs longitudinally along a straight path. Post-forming equipment can make subsequent transverse bends to the profiles.
How are roll formed products cut to length?
Flywheel punching and cutting units on the exit side automatically shear profiles to length based on a photo sensor. Rotary scribing also pre-scores sheets for manual breakdown.
What safety precautions should be used with roll formers?
Guards, barriers, interlocks, E-stops, and compliance with standards prevents hazards. Lockout before maintenance prevents accidental operation. Proper forklift handling prevents damage or injury.
How do I choose the right supplier for my application?
Consider reputation, experience, design expertise, quality, and services when selecting a double stage roll forming machine vendor. Provide detailed specifications for your production needs.
Conclusion
With their ability to produce complex, elongated profiles with good accuracy, double stage roll forming machines offer an efficient mass production solution for metal fabrication across many industries. Their inline automated process, flexible tooling, and incremental bending engender continuous outputs of formed components spanning up to 10 meters in length for both lightweight and heavy gauge materials. When properly engineered with precision components and robust construction, double stage roll formers provide years of reliable service for forming panel siding, racking, structural framing, metal enclosures, automotive components, and innumerable profiles across diverse applications.