Door frames and jambs serve critical structural and aesthetic purposes in residential or commercial buildings. Straight door frame roll forming equipment efficiently mass produces these components with integrated hardware slots and precision dimensions.
This guide provides a comprehensive overview of straight door frame roll forming machine, including:
Working Principles
Explanation of the automated roll forming methodology shaping flat strips into door frame profiles.
Equipment Types
The classifications and specifications defining door jamb roll former models.
Production Process
Step-by-step specifics on the complete manufacturing sequence to create finished door frame pieces.
Materials and Customization
Suitable metals and material gauges for roll formed door jambs plus customization options.
Suppliers and Pricing
Leading global straight door frame roll former manufacturers and price considerations.
Installation, Operation and Maintenance
Guidelines on setting up, running and sustaining optimal uptime on roll formers.
Choosing Manufacturers
Key factors in vetting and selecting reputable straight door frame roll former suppliers.
Comparative Analysis
Contrasting automated roll forming against cut-weld-assemble and manual bending fabrication.
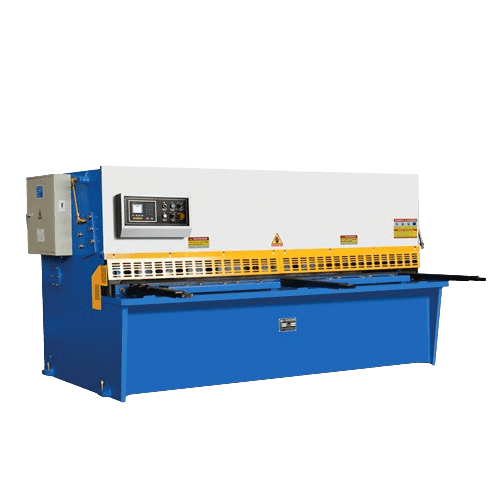
straight door frame roll forming machine Working Principle
The working principle involves rotary bending and sequential shaping of metal coil strips through consecutive roller dies to gradually form a door frame cross-section.
Key aspects include:
- Cold forming avoids heating/welding distortions
- Automated process ensures high outputs
- Specialized tooling packages for profile features
- Integrated hardware punching, notching, hole adding
- Precision calibration and straightening
These capabilities enable efficient mass production of dimensional and functional ready-to-install door frames.
Equipment Types
Straight door jamb roll former classifications include:
Table 1. Major Equipment Specifications
Type | Width | Thickness | Speed | Stations |
---|---|---|---|---|
Light | <800mm | 0.5-0.8mm | 10m/min | 6 |
Medium | 800-1500mm | 0.8-1.2mm | 12m/min | 8 |
Heavy | >1500mm | 1.0-1.5mm | 15m/min | 10+ |
Common line items:
- Decoiler and feeder system
- Forming stations with quick change tooling
- Punching/hardware insertion presses
- Welding for seam locks or reinforced frames
- Cutoff shear for batched lengths
- Exit conveyors and bundling
Production Process
The automated roll forming production sequence comprises:
- Metal coil loaded on powered decoiler
- Strip fed through feed guides into start of line
- Sequential forming stations shape profile
- Hardware notching/punching insertion
- Corner welding for strength
- Flying cutoff shears cut to length
- Exit conveyor stacks finished frames
The process allows high volume precision part making with minimal manual labor between steps. Operators simply maintain equipment settings and offload finished door jambs.
-
Highway Guardrail End Terminal Forming Machine
-
Highway U/C Post Roll Forming Machine
-
2 Waves Highway Guardrail Roll Forming Machine
-
3 Waves Highway Guardrail Roll Forming Machine
-
Two waves highway guardrail machine
-
Three waves highway guardrail machine
-
Steel Coil Cut To Length Line Machine
-
Steel Coil Cut To Length Line Machine
-
Steel Coil Cut To Length Line Machine
Materials and Customization
Metals suited for door frame roll forming include:
- Cold rolled steel – corrosion resistant
- Hot dipped galvanized steel – durable hot-dip zinc layer
- Stainless steels like 304 or 316 – premium weather/chemical resistance
- Prepainted steel with polyester or acrylic coating – customized colors
Custom features possible:
- Knockdown vs welded right-angle corners
- Single or double rabbet design
- Hardware notching patterns
- Holes for securing to studs
- Match frame widths and depths to walls
- Decorative profile elements
This flexibility suits cost-efficient construction for homes, hospitals, warehouses and more with various opening size needs, hardware compatibility requirements, and aesthetic standards.
straight door frame roll forming machine Suppliers
There are over 70 major international straight steel door frame roll former equipment manufacturers globally. A sample includes:
Table 2. Noteworthy Straight Door Frame Roll Former Suppliers
Company | Location | Base Pricing |
---|---|---|
AH Machinery | China | $4,500 – $38,000 |
Eagle Bending Machines | USA | $14,500 – $197,000 |
EWMenn | Germany | $92,000 – $480,000 |
Formtek | India | $13,500 – $120,000 |
Metform | Turkey | $18,500 – $205,000 |
Pricing factors include:
- Maximum strip width
- Automation features
- Construction materials
- Brand reputation
- Support/maintenance services
- Specialized tooling
Budget Chinese models offer basic functionality while premium European suppliers provide heavy production output but with higher equipment costs.
Installation, Operation, Maintenance
To install:
- Offload components with crane/forklift
- Bolt reinfoced frame to level concrete
- Wire power, pneumatic and lubrication
- Align decoiler, loop feeder, stations
- Insert tooling per design
For operation:
- HMI and PLC automates process
- Input parameters – width, thickness, lengths
- Monitor strip flow, finish part quality
Maintenance best practices:
- Inspect/replace forming rollers
- Confirm belt tensions
- Top up hydraulic fluid
- Clear metal fines
- Test emergency stop buttons
- Audit safety guards
Proactive preventative maintenance protects operational uptime on door frame lines.
Choosing Manufacturers
Crucial factors when selecting reputable straight door frame roll former suppliers:
Table 3. Key Vetting Considerations for Manufacturers
Factor | Description |
---|---|
Production Expertise | Extensive roll forming process knowledge for quality door frames |
Customization Range | Broad hardware insertion and profile variation capabilities |
Construction Quality | Use of premium components for longevity and precision |
Responsiveness | Rapid design feedback and troubleshooting response |
Overall Value | Balance of line output, reliability and pricing |
No single manufacturer leads all considerations – end users should rank factors appropriately for their specific production needs and building specifications during door frame roll former selection.
Comparative Analysis
Versus other fabrication platforms, powered roll forming provides:
Table 4. Relative Pros and Cons
Metric | Roll Forming | Manual Bending | Cut-Weld-Fab |
---|---|---|---|
Setup Time | Medium | Fast | Slow |
Operating Costs | Lower material/energy use | High labor | Higher energy |
Build Consistency | Optimized software control | Worker variability | Prone to distortions |
Throughput Speed | High continuous volumes | Very slow pace | Batch processing |
Size Capabilities | 1.5m+ widths possible | ~1m max typical | 1.5m max |
Hardware Integration | Inline automation available | Manual insertion only | Secondary op |
Precision | Excellent, software-corrected | Approximate finished form | Variable |
Changeovers | Tooling pack swaps | Immediate | Reconfigure tools |
In summary, automated roll forming produces superior door frame components over manual or cut-weld-assemble fabricating – both in productivity, consistency, and hardware integration.
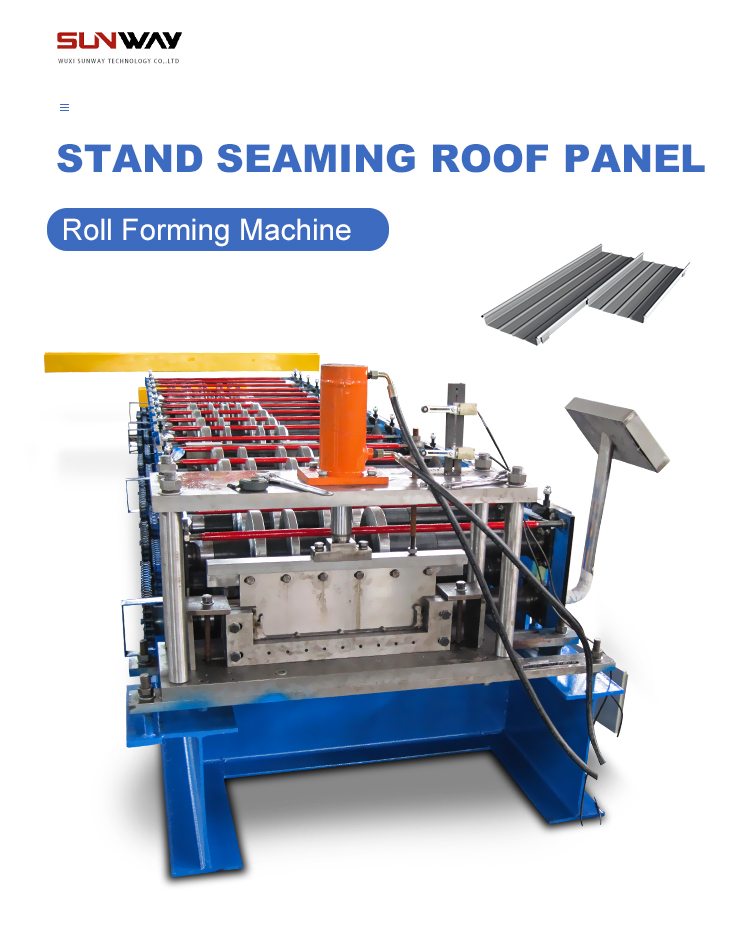
Frequently Asked Questions
Q: What types of door frames can roll forming lines produce?
A: Common models include single/double rabbet, knocked down, welded, profiles from wood door frames to heavy duty industrial.
Q: Can decorative patterns be added to roll formed door jambs?
A: Yes, aesthetic elements like embosses, textures and wood grain effects can be incorporated into profile tooling along with protective coatings.
Q: What is the typical production rate for door frame lines?
A: Output speeds vary based on width and thickness but approx. 10-20 finished door frames per minute is standard. Larger profile capacities hit 30+ per minute rates.
Q: How long does forming tooling last on door frame roll lines?
A: At 2 shift production volumes, tooling sees maintenance every ~3-4 months. Roller lifespan averages 100,000 feed meter cycles before needing replacement.
Q: Can door frame ends be notched before rolling?
A: Yes, rotary power notchers allow hardware voids and other edge features to be added even before the actual roll forming stations.
Q: Are knockdown roll formed door jambs as strong as welded?
A: Welded corners provide 30-40% higher frame strength but mechanical joints suffice for typical installations. Knockdown allows easier transport.