A standing seam roof sheet roll forming machine continuously cold forms metal coil strip into interlocking roofing panels with raised vertical seams used widely in architectural and industrial building construction.
Overview of Standing Seam Roof Sheet Roll Forming Machines
Standing seam roll formers produce straight or curved roofing panels from thin metal coils for structures needing weather-tight installations.
Key characteristics:
- Cold forms coils into various roof panel profiles
- Raised vertical interlocks for sealing
- Adjustable curving and hemming
- Easy size and profile changeovers
- Used for metal roof panel production
- Higher volumes than fabrication
Types of Standing Seam Roof Sheet Roll Formers
Machine Type | Description |
---|---|
Straight roof sheet roll former | Flat roofing panels |
Curved roof sheet roll former | Arched building profiles |
Double lock roof sheet roll former | For wind uplift resistance |
Custom roof sheet roll former | Special profiles |
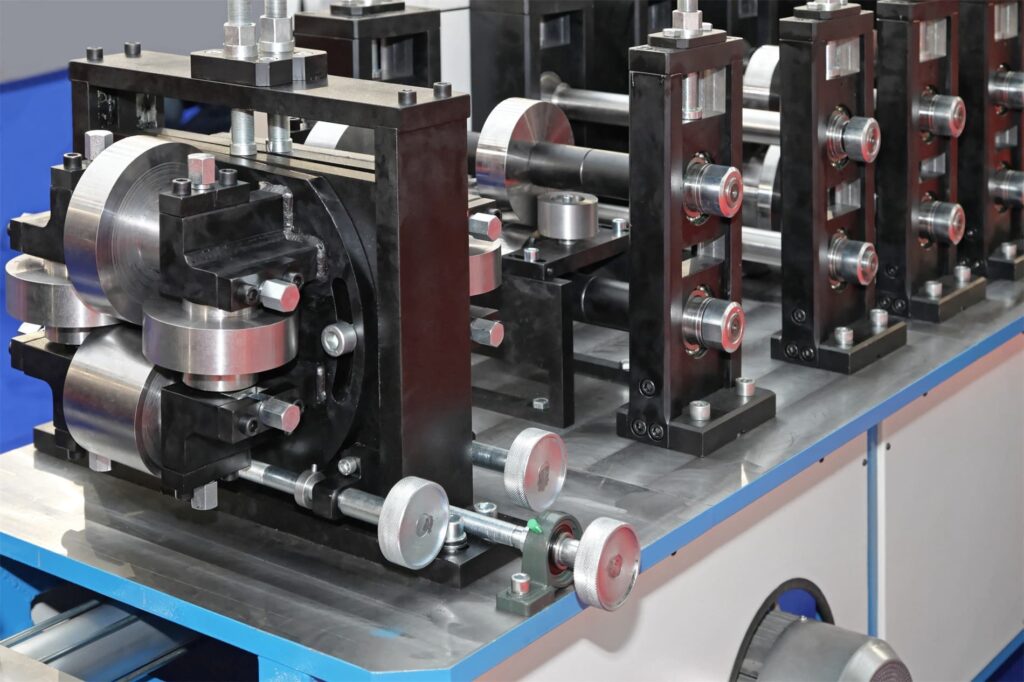
Working Principle of Standing Seam Roof Sheet Roll Forming
Operational process overview:
- Coil strip pre-treated for optimal forming
- Infeed guides align strip into roll former
- Progressive stations gradually shape strip
- Top and bottom rolls perform bending
- Hemming rolls seal panel edges
- Cutoff knife slices formed sheets
- Formed sheets bundle stacked
- PLC control coordinates production
Continuous automated process.
Features of Standing Seam Roof Sheet Roll Forming Machines
Feature | Details |
---|---|
Forming stations | 10-20 stands for optimal shaping |
Rolls | Hardened or adamite coated |
Decoiler | 5 ton capacity handles large coils |
Material feed | Servo motor with precision control |
Hemming | Rolls seam both edges |
Curving | Adjustable for contour roofs |
Cutting | Rotary flying knife for square cutting |
Materials for Standing Seam Roof Sheet Roll Forming
Common sheet metals:
- Aluzinc steel – corrosion resistant surface
- Galvanized steel – low cost corrosion protection
- Aluminum – light weight material
- Copper – traditional metal roof aesthetic
- Stainless steel – ultimate weather resistance
- Color coated steel – prefinished options
Roof Panel Profile Options
Typical roofing profiles produced:
- Corrugated panel – sinusoidal waves
- 5V Crimp panel – Angular rib look
- Standing seam – Vertical interlocks
- Shingle panel emulation – Architectural style
- Trapezoid panel – Structural shape
- Custom profiles – Special architectural
Quick Change Tooling for Roof Panel Roll Formers
Designed for rapid die changeovers:
- Two-piece split die sets
- Hydraulic wedge locks with color codes
- Preset length adjustment slots
- Assist cylinders for roll changes
- Minimal re-calibration needed
- Reduces changeover downtime
Additional Processing Options
Integrated secondary capabilities:
- Hemming both sides
- Longitudinal embossing
- Logo stamping
- Hole punching
- Corner notching
- Special edge bending
- Component robotic welding
- Powder coating
Global Manufacturers of Standing Seam Roof Sheet Machines
Manufacturer | Location |
---|---|
AMS Korea | South Korea |
Furmac | China |
Gasparini | Italy |
Metform | Turkey |
RollXChanging | Thailand |
Reputable suppliers with international experience.
Pricing Considerations for Standing Seam Roof Sheet Roll Lines
Production Class | Price Range |
---|---|
Light-duty | $55,000 – $95,000 |
Medium-duty | $85,000 – $145,000 |
Heavy-duty | $120,000 – $230,000 |
Costs vary based on speed, automation, material needs, and integrated features. Significant differences can exist between regions.
-
Highway Guardrail End Terminal Forming Machine
-
Highway U/C Post Roll Forming Machine
-
2 Waves Highway Guardrail Roll Forming Machine
-
3 Waves Highway Guardrail Roll Forming Machine
-
Two waves highway guardrail machine
-
Three waves highway guardrail machine
-
Steel Coil Cut To Length Line Machine
-
Steel Coil Cut To Length Line Machine
-
Steel Coil Cut To Length Line Machine
Installation and Operation of Standing Seam Roof Sheet Machines
Proper installation helps ensure production quality and uptime. Thorough operator training needed on procedures.
Installation Recommendations
- Fixed, rigid, leveled mounting
- Adequate vibration damping
- Sufficient power supply wiring
- Pneumatic lines with moisture separators
- material decoiler capacity
- Safety guarding around hazards
- Lighting for visual inspection
Operational Procedures
- Review safety procedures
- Ensure area clear of obstructions
- Engage main electrical disconnect
- Energize hydraulic power units
- Set line speed and curving degree
- Thread coil material through machine
- Initiate controlled startup sequence
- Monitor forming quality continuously
- Conduct regular die inspections
- Log production output
Follow manufacturer’s instructions precisely.
Maintenance of Standing Seam Roof Sheet Roll Lines
- Schedule periodic maintenance downs
- Lubricate bearings every 40 hours
- Inspect pneumatic elements
- Verify hydraulic fluid cleanliness
- Check chains, sprockets, belts
- Touch up paint deterioration
- Keep inventory of common spare parts
Extends equipment lifetime and prevents premature failures.
Purchasing Selection Factors for Standing Seam Roof Sheet Machines
Key considerations when investing in new roll forming production lines.
Evaluating Roll Former Manufacturers
Factor | Description |
---|---|
Experience | Years in business, number of lines installed |
Testing | Validation data for machines |
Materials | Range of metals successfully processed |
Engineering | Design skills and analysis expertise |
Support | Installation help offered |
Training | Operator training provided |
Questions to Ask Potential Suppliers
- What international standards do your machines meet?
- Will you share baseline production data?
- How customized is your tooling design agility?
- What level of support is included?
- Can we see virtual demonstrations?
- Where are key bought-in components sourced?
- Can enhancements be added later?
Benefits and Challenges of Standing Seam Roof Sheet Roll Forming
Advantages
- High production efficiency
- Consistent quality panels
- Volume efficiencies
- Lower operational labor
- Small equipment footprint
- Flexibility for product changes
- Integrated secondary processing
Disadvantages
- Higher initial investment capital
- Potential roll damage risks
- Skilled PLC programming needed
- Coil inventory racking required
- Limited extremely heavy gauge capabilities
- Perceived simpler fabrication methods
When requirements fit process capabilities, roll forming provides speeds and economies exceeding traditional standing seam roof panel fabrication approaches.
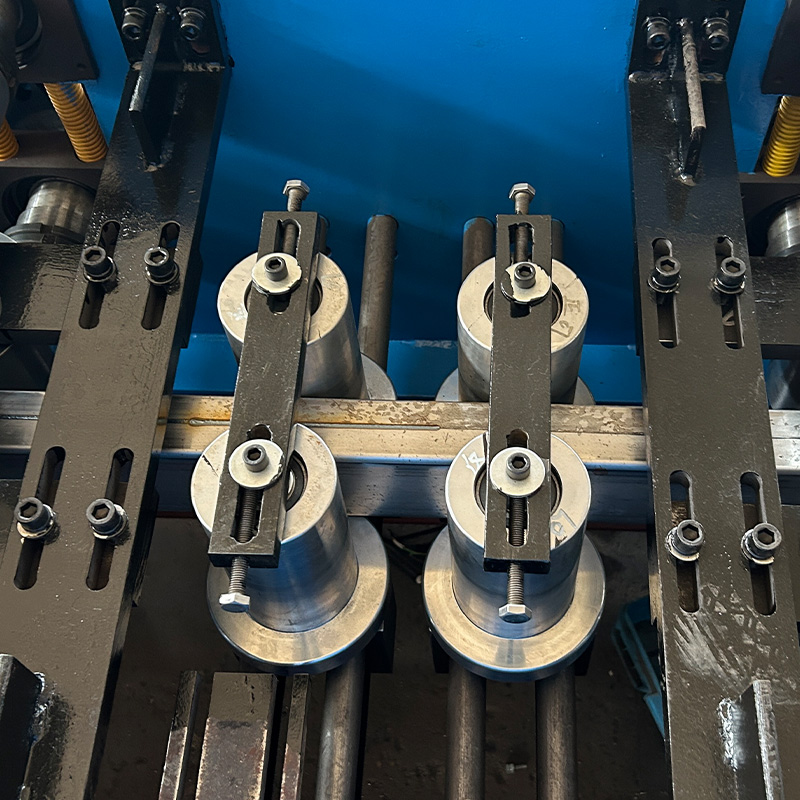
Frequently Asked Questions
What types of slicing can be integrated with roof sheet roll formers?
Rotary flying knife cutting evenly spaces cut sheets for bundle stacking. Abrasive wheels allow mitertrim bevel angle cutting if needed for architectural applications. Band saws also possible.
What factors affect the hem quality during roof sheet roll forming?
Critical parameters influencing hemming include incoming strip flatness quality, edge burr removal effectiveness, forming stand parallelism, edge prepping penetration depth consistency, hem prep geometry, roll surface finish, and tip radius with sufficient offset space.
How many forming passes are typically utilized for common roof sheet profiles?
12-18 stations are typical for standard roofing panels like corrugated, 5V crimp, and standing seam profiles. More complex multi-radius products can demand over 20 stations with pre-piercing, final shaping, and hemming operations.
What key machine safety circuits are vital for roof sheet roll former operation?
Redundant emergency halting, interlocked physical guarding, pinch point sensors tying into actuation power interrupt, preset overload fault limits on drive systems, lockout protocols, and monitoring any hydraulic leaks as highest priorities if detected.
What factors contribute to higher snow and wind load capacity of standing seam roofing?
Load capacity results from sheeting gauge thickness, steel yield rating, panel widths, seam height, clip fastener spacing, and installed seam joint consistency using controlled hardware and meticulous craftsmanship connecting to underlying fixed substructure.
How does panel curving flexibility benefit certain standing seam roof architectural designs?
Curving abilities allow tapering panels on domes or barrel buildings to divert the vertical forces into primarily axial compression more efficiently down into ring beam systems rather than necessitating extensive diagonal bracing with flat sheeting.
What special storage precautions should be taken with prepainted coil inventory?
Interior climate controlled storage helps prevent excessive humidity exposure and moisture accumulation between tightly wound prepainted coil layers during storage which risks white rust corrosion detention and staining defects detected only after costly roll forming material conversions discovered at finishing.
Where are variable frequency drives used throughout standing seam roof sheet roll formers?
VFDs provide servo motor coordination for the main line pull speed, cut to length index positioning, and upper and lower roll stations most adjacent to the progressive die steps accomplishing the primary bending with profiles sensitive to velocity fluctuations detrimentally influencing material yielding behavior.
How should technicians safely clear occasional sheet metal jams inside roll formers?
After engaging emergency stops, follow lockout tagout procedures before approaching any jam region while wearing protective gear. Use hands tools only with extreme caution regarding material edges and machine hazards to gently extract strip sections after fully verifying drives motion-free, before management signoff reinitiating any restart sequence ensuring clearances.
What factors make certain architectural metal roofing finishes more prone to oil canning panel distortion? Stiffer harder aluminum and coated steel compositions, seamed panel fixing methods, installation labor variances, extreme color finishes lacking sufficient film flexibility along with substrates lacking proper temper roll leveling control contribute to visible waviness accentuated under critical lighting conditions faced by building owners. Proactive review should mitigate risk.