Corrugated sheets are everywhere, from roofing and siding to fencing and even decorative designs. These wavy sheets of metal or plastic are not just aesthetically pleasing but are also incredibly functional, offering durability, flexibility, and excellent structural integrity. But how are these iconic corrugated patterns created at scale? Enter the Corrugated Roll Forming Machine—a game-changer in the manufacturing world.
In this guide, we’ll explore everything you need to know about Corrugated Roll Forming Machines, from their applications and types to pricing, workflow, and why Wuxi Sunway Machinery is the go-to expert for these machines in 2025. Whether you’re in the construction industry, manufacturing, or are just curious about this versatile machine, this guide has you covered.
Overview of Corrugated Roll Forming Machines
A Corrugated Roll Forming Machine is a specialized piece of industrial equipment designed to create corrugated patterns on metal sheets. The process involves feeding flat metal coils into the machine, where a series of rollers progressively bend the material into wavy, corrugated shapes.
These machines are widely used to manufacture corrugated roofing sheets, wall cladding, and fencing panels. The roll-forming process ensures that the sheets are uniform, durable, and ready to withstand harsh weather conditions. Corrugated sheets are typically made from galvanized steel, color-coated steel, or aluminum, making them ideal for both functional and aesthetic applications.
With increasing construction demands worldwide, Corrugated Roll Forming Machines are essential for manufacturers looking to produce high-quality sheets at scale.
Applications of Corrugated Roll Forming Machines
Corrugated sheets are highly versatile and are used in a variety of industries. Here’s where Corrugated Roll Forming Machines make an impact:
1. Roofing
Corrugated sheets are a popular choice for roofing due to their durability, lightweight nature, and ability to withstand extreme weather conditions. They are used in residential, commercial, and industrial buildings.
2. Wall Cladding
In modern architecture, corrugated sheets are often used as wall cladding to create a sleek, industrial look while providing excellent insulation and protection.
3. Fencing
Corrugated sheets are also used for fencing, offering a sturdy and cost-effective solution for securing properties and construction sites.
4. Agricultural Storage
From barns to silos, corrugated sheets are widely used in agricultural buildings to store crops and equipment, thanks to their rust resistance and strength.
5. Decorative Applications
Corrugated sheets are increasingly being used in interior design and artistic installations, adding a unique, textured aesthetic to surfaces.
By investing in a Corrugated Roll Forming Machine, manufacturers can cater to these diverse applications and tap into growing market opportunities.
Types of Corrugated Roll Forming Machines
Not all corrugated sheets are the same, and neither are the machines that produce them. Here are the main types of Corrugated Roll Forming Machines to consider:
1. Single-Layer Corrugated Roll Forming Machines
These machines are designed to produce one type of corrugated sheet profile, such as a standard wave or trapezoidal pattern. They are ideal for manufacturers focused on a specific product line.
2. Double-Layer Roll Forming Machines
Double-layer machines can produce two different profiles, offering flexibility for manufacturers serving multiple markets. The layers can be switched quickly, saving time and increasing efficiency.
3. High-Speed Corrugated Roll Forming Machines
For large-scale production, high-speed machines are the go-to option. They offer higher production speeds while maintaining precision and quality.
4. Custom Roll Forming Machines
If you’re producing unique corrugated patterns or working with specialized materials, custom machines can be designed to meet your exact specifications.
Comparison Table: Types of Corrugated Roll Forming Machines
Machine Type | Primary Use | Profiles Produced | Average Speed | Price Range (USD) |
---|---|---|---|---|
Single-Layer Machines | Single-profile production | 1 Profile | 10–20 meters/min | $30,000–$60,000 |
Double-Layer Machines | Dual-profile production | 2 Profiles | 10–15 meters/min | $50,000–$80,000 |
High-Speed Machines | Large-scale production | 1 Profile | 20–40 meters/min | $70,000–$120,000+ |
Custom Machines | Unique or specialized profiles | Variable | Variable | Based on design specs |
Key Features of Corrugated Roll Forming Machines
When choosing a Corrugated Roll Forming Machine, it’s essential to understand the features that set high-quality machines apart. Here’s what to look for:
1. High-Precision Rollers
The rollers are the heart of the machine. High-strength steel rollers with chrome plating ensure precision and durability, producing consistent corrugated patterns.
2. Material Compatibility
Your machine should be capable of processing a variety of materials, including galvanized steel, aluminum, and pre-painted color-coated sheets.
3. PLC Control System
A Programmable Logic Controller (PLC) system allows for automation and easy adjustments, ensuring accuracy and reducing operator error.
4. Hydraulic Cutting Systems
Hydraulic cutters provide clean, burr-free cuts, ensuring that the finished sheets meet exact length specifications.
5. Quick Changeover
For double-layer or multi-profile machines, quick-change mechanisms reduce downtime when switching between profiles.
6. Noise Reduction
Modern machines are designed with noise-reducing features, creating a quieter working environment.
Machines from Wuxi Sunway Machinery combine these features with robust construction and cutting-edge technology, ensuring top-tier performance.
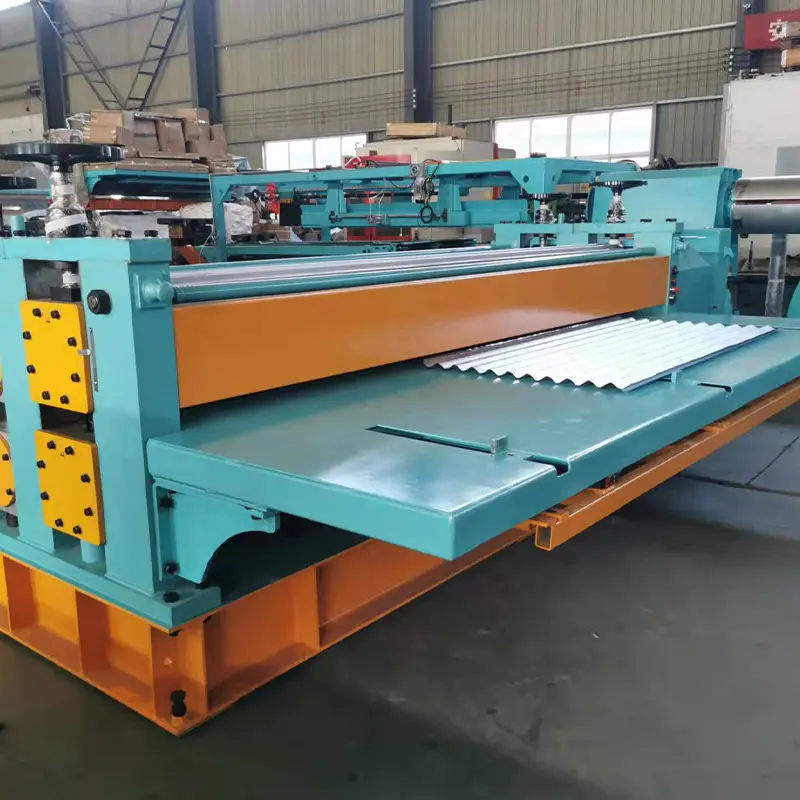
Specifications of Corrugated Roll Forming Machines
Understanding the technical specifications of a machine can help you make the right investment. Here are the standard specs to expect:
Specification | Details |
---|---|
Material Thickness | 0.3mm–1.2mm |
Material Type | Galvanized steel, aluminum, pre-painted steel |
Forming Speed | 10–40 meters per minute |
Roller Material | High-strength steel with chrome plating |
Cutting System | Hydraulic or servo cutting for precision |
Control System | PLC with HMI (Human-Machine Interface) |
Power Supply | Typically 380V/50Hz (customizable for regional standards) |
Production Capacity | 5,000–10,000 square meters per day |
Pricing of Corrugated Roll Forming Machines
The cost of a Corrugated Roll Forming Machine depends on several factors, including its features, production capacity, and level of automation. Here’s an overview:
Price Ranges
- Single-Layer Machines: $30,000–$60,000
- Double-Layer Machines: $50,000–$80,000
- High-Speed Machines: $70,000–$120,000+
- Custom Machines: Pricing varies based on design and capabilities.
Factors Affecting Price
- Automation Level: Fully automated machines cost more but reduce labor costs in the long run.
- Production Speed: High-speed machines are more expensive but essential for large-scale operations.
- Customization: Machines designed for unique profiles or materials come at a premium.
- Brand Reputation: Trusted manufacturers like Wuxi Sunway Machinery provide durable and reliable machines that deliver excellent ROI.
FAQs About Corrugated Roll Forming Machines
Here are answers to some frequently asked questions:
Question | Answer |
---|---|
Can these machines produce custom profiles? | Yes, custom machines can be designed to create unique corrugated patterns for specialized applications. |
What’s the lifespan of these machines? | With proper maintenance, these machines can last 10–15 years or more. |
What materials can be processed? | Most machines handle galvanized steel, aluminum, and pre-painted color-coated sheets. |
Is operator training provided? | Yes, manufacturers like Wuxi Sunway Machinery offer on-site training and support. |
What’s the average production capacity? | Depending on the model, machines can produce 5,000–10,000 square meters of corrugated sheets per day. |
Automation Trends in Corrugated Roll Forming Machines
The manufacturing industry is rapidly evolving, and Corrugated Roll Forming Machines are no exception. Automation is no longer just an option—it’s a necessity for manufacturers looking to stay competitive in 2025. Here’s how automation is transforming the corrugated sheet production process:
1. IoT Integration
IoT-enabled machines are revolutionizing how manufacturers monitor and control production lines. Imagine receiving real-time updates about your machine’s performance, error alerts, and maintenance schedules—all on your smartphone or computer. This connectivity ensures minimal downtime and optimal efficiency.
2. Fully Automated Systems
From coil feeding to stacking finished sheets, fully automated machines handle every aspect of production. Operators only need to oversee the process, drastically reducing labor costs and increasing output.
3. Servo-Driven Precision
Servo motors are becoming a standard feature in high-end machines, offering unparalleled accuracy in cutting, punching, and forming. With servo-driven systems, you can achieve burr-free cuts and perfectly shaped corrugated patterns.
4. Adaptive Rollers
Modern machines feature adaptive rollers that automatically adjust to different material thicknesses and profile specifications. This eliminates the need for manual recalibration, ensuring seamless production transitions.
5. Real-Time Quality Control
Integrated sensors and cameras monitor the production process in real-time, detecting issues like misalignments or material inconsistencies. This feature minimizes defective sheets and reduces waste.
6. Predictive Maintenance
Thanks to advanced sensors and machine learning, predictive maintenance systems can anticipate when critical components, like rollers or cutting blades, are likely to fail. This proactive approach prevents unexpected breakdowns and extends the machine’s lifespan.
At Wuxi Sunway Machinery, we embrace these automation trends to deliver machines that are not only efficient but also future-ready.
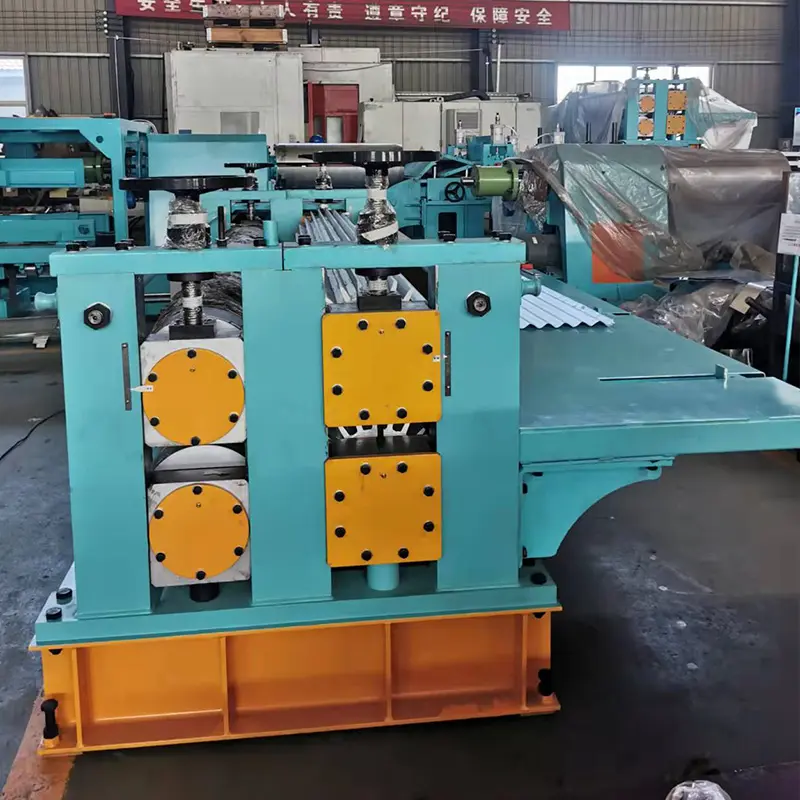
Workflow Optimization for Corrugated Sheet Production
An optimized workflow is the backbone of an efficient production line. Whether you’re producing roofing sheets or wall cladding, aligning your machine’s capabilities with a streamlined workflow can significantly boost productivity and quality. Here’s a step-by-step guide to optimizing your production process:
Step 1: Material Preparation
- Raw Material Selection: Choose high-quality galvanized steel, aluminum, or pre-painted coils with the required thickness (typically 0.3mm–1.2mm).
- Storage Conditions: Store coils in a dry, clean environment to prevent corrosion or contamination.
- Decoiling: Use an automatic or hydraulic decoiler to feed the material into the machine. This minimizes manual intervention and speeds up the process.
Step 2: Feeding and Alignment
- Precision Feeders: Ensure the material is perfectly aligned as it enters the rollers. Advanced feeders with tension control prevent slippage or wrinkling.
- Edge Sensors: Modern machines use sensors to detect and correct alignment issues in real time.
Step 3: Roll Forming
- Progressive Shaping: The metal sheet passes through multiple roller stations, each shaping it further into the desired corrugated profile. This ensures consistency and dimensional accuracy.
- Roller Maintenance: Regularly clean and inspect the rollers to maintain precision and prevent wear-related defects.
Step 4: Cutting
- Hydraulic Cutting: Integrated cutting systems trim the sheet to the desired length. Hydraulic or servo-driven cutters ensure clean, burr-free edges.
- Length Adjustments: Use the PLC system to easily adjust cutting lengths based on order specifications.
Step 5: Stacking and Packaging
- Automated Stacking: Finished sheets are automatically stacked for easy handling and transport.
- Protective Packaging: Wrap sheets in moisture-resistant materials to protect against rust during shipping or storage.
Real-Time Monitoring
Machines equipped with HMI (Human-Machine Interface) panels allow operators to monitor production metrics, adjust settings, and troubleshoot errors in real-time.
By following these steps, manufacturers can maximize the efficiency of their production lines and deliver high-quality corrugated sheets at scale.
Troubleshooting Common Issues in Corrugated Roll Forming Machines
Even the most advanced machines can encounter technical issues. Here’s a troubleshooting guide for some common problems:
1. Material Slippage
- Cause: Improper tension settings or misaligned feeding rollers.
- Solution: Adjust the tension settings and ensure the feeding rollers are properly aligned. Clean any debris from the rollers or feeding path.
2. Inconsistent Corrugation
- Cause: Worn rollers or incorrect roller calibration.
- Solution: Inspect the rollers for wear and recalibrate the machine as per the manufacturer’s instructions. Replace damaged rollers if necessary.
3. Uneven Cutting
- Cause: Dull cutting blades or misaligned cutting systems.
- Solution: Replace or sharpen the cutting blades. Ensure the cutting system is properly aligned to achieve clean, precise cuts.
4. Machine Downtime
- Cause: Lack of regular maintenance or undetected wear on critical components.
- Solution: Follow a strict maintenance schedule, including lubrication, cleaning, and inspections. Use predictive maintenance features to identify and address issues early.
5. Sheet Wrinkling
- Cause: Material tension issues or incorrect roller settings.
- Solution: Adjust the material tension and check the roller alignment. Ensure the material thickness is within the machine’s processing range.
For expert assistance, contact Wuxi Sunway Machinery, which offers comprehensive support and spare parts for all its machines.
Environmental Benefits of Corrugated Roll Forming Machines
Sustainability is becoming a critical focus for manufacturers worldwide. Corrugated Roll Forming Machines contribute to eco-friendly practices in several ways:
1. Minimal Material Waste
The roll-forming process is highly efficient, using nearly all of the raw material. Scrap material is minimal and often recyclable, reducing overall waste.
2. Energy Efficiency
Modern machines are designed to consume less energy without compromising performance. Features like servo motors and optimized hydraulic systems ensure lower power consumption.
3. Recyclable Materials
Corrugated sheets are typically made from materials like galvanized steel and aluminum, which are 100% recyclable. This aligns with global sustainability goals.
4. Long Product Lifespan
Corrugated sheets are durable and resistant to corrosion, reducing the need for frequent replacements. This extends the lifecycle of the products and minimizes resource consumption.
By investing in energy-efficient machinery, manufacturers can align with environmental standards while also reducing operational costs. At Wuxi Sunway Machinery, we prioritize sustainability in our designs.
FAQs About Corrugated Roll Forming Machines
Here are some more frequently asked questions to help you make an informed decision:
Question | Answer |
---|---|
Can I produce multiple profiles with one machine? | Yes, double-layer or custom machines can produce multiple profiles with quick tooling changes. |
What is the typical maintenance schedule? | Monthly maintenance includes lubrication, cleaning, and inspections. Annual overhauls are recommended. |
What’s the average production speed? | Machines typically produce 10–40 meters of corrugated sheets per minute, depending on the model. |
Do these machines require skilled operators? | Automated machines are user-friendly and require minimal training, which is often provided by the manufacturer. |
Are financing options available? | Yes, manufacturers like Wuxi Sunway Machinery offer flexible payment plans. |
Why Choose Wuxi Sunway Machinery for Corrugated Roll Forming Machines?
When it comes to roll-forming technology, Wuxi Sunway Machinery is the gold standard. Here’s why:
- Proven Expertise: With decades of experience, we specialize in designing roll-forming machines tailored to diverse industries.
- Custom Solutions: Whether you need standard or unique profiles, we offer fully customized machines to meet your requirements.
- Global Trust: Our machines are trusted by manufacturers across Asia, Europe, Africa, and beyond.
- Quality Assurance: Built to international standards, our machines are durable, efficient, and reliable.
- Comprehensive Support: From installation to maintenance and spare parts, we’re with you every step of the way.
Conclusion: Is a Corrugated Roll Forming Machine Worth It?
If you’re in the construction or manufacturing industry, investing in a Corrugated Roll Forming Machine is a smart move. These machines offer unmatched efficiency, precision, and scalability, enabling you to meet the growing demand for corrugated sheets in roofing, cladding, and more.
And when it comes to choosing a partner, Wuxi Sunway Machinery stands out for its innovation, quality, and customer-centric approach. Ready to take your production line to the next level? Let’s roll into a brighter, more profitable future—together!