When it comes to modern infrastructure and industrial wiring systems, cable trays are an essential component. They provide robust support and organization for electrical wiring, ensuring safety, efficiency, and accessibility. But have you ever wondered how these trays are manufactured with such precision and speed? Enter the Cable Tray Roll Forming Machine—a high-tech solution designed to produce cable trays at scale while ensuring consistent quality.
In this comprehensive guide, we’ll explore everything you need to know about Cable Tray Roll Forming Machines in 2025. We’ll cover their applications, types, prices, features, and advanced automation trends, as well as provide troubleshooting tips. Plus, you’ll learn why Wuxi Sunway Machinery is the go-to manufacturer for roll-forming technology.
What is a Cable Tray Roll Forming Machine?
A Cable Tray Roll Forming Machine is a specialized piece of industrial equipment designed to manufacture cable trays from flat metal coils. The roll-forming process involves feeding the material through a series of rollers that gradually shape it into the desired tray profile.
These machines are indispensable for industries that rely on cable management systems, including construction, power generation, telecommunications, and IT infrastructure. With the growing demand for efficient cable organization solutions, cable tray roll-forming machines have become a critical investment for manufacturers worldwide.
Applications of Cable Tray Roll Forming Machines
Cable trays play a vital role in various industries, and the versatility of roll-forming machines ensures they can meet diverse application needs. Let’s explore where these machines make the biggest impact:
1. Electrical Infrastructure
Cable trays are a cornerstone of electrical wiring systems in industrial and commercial buildings. They support power cables, communication wires, and control wiring, ensuring they’re organized and protected.
2. Data Centers
In data centers, cable trays manage the complex network of cables required for servers, storage systems, and routers. They prevent overheating and make cable maintenance more accessible.
3. Renewable Energy
Solar and wind power plants rely on cable trays to protect and organize electrical wiring exposed to harsh environmental conditions.
4. Industrial Plants
Manufacturing facilities use cable trays to route wiring safely through areas with high temperatures, vibrations, or corrosive substances.
5. Construction Projects
From skyscrapers to shopping malls, cable trays are essential for maintaining compliance with electrical safety codes and ensuring efficient cable management.
Types of Cable Tray Roll Forming Machines
The type of cable tray you need to produce will determine the machine you should invest in. Here’s a breakdown of the main types of Cable Tray Roll Forming Machines:
1. Perforated Cable Tray Roll Forming Machines
These machines produce perforated trays, which feature holes for ventilation. They are ideal for environments where heat dissipation is critical.
2. Ladder Cable Tray Roll Forming Machines
Designed for ladder-style trays, these machines create profiles with rungs that provide maximum strength and minimal weight. Ladder trays are popular in high-capacity installations.
3. Solid-Bottom Cable Tray Roll Forming Machines
Solid-bottom trays offer complete protection for cables in dusty, dirty, or wet environments, and the machines that produce them ensure a seamless design.
4. Multi-Profile Cable Tray Roll Forming Machines
For manufacturers serving diverse markets, these machines can produce multiple tray styles (perforated, ladder, and solid-bottom) with quick tooling changes.
Comparison Table: Types of Cable Tray Roll Forming Machines
Machine Type | Primary Use | Tray Styles Produced | Production Speed | Price Range (USD) |
---|---|---|---|---|
Perforated Machines | Ventilated cable trays | Perforated Trays | 10–20 meters/min | $60,000–$100,000 |
Ladder Machines | High-strength cable trays | Ladder Trays | 15–25 meters/min | $70,000–$120,000 |
Solid-Bottom Machines | Dust/moisture-proof cable trays | Solid-Bottom Trays | 10–20 meters/min | $60,000–$110,000 |
Multi-Profile Machines | Flexible, multi-style production | Multiple Tray Styles | 10–25 meters/min | $100,000–$200,000+ |
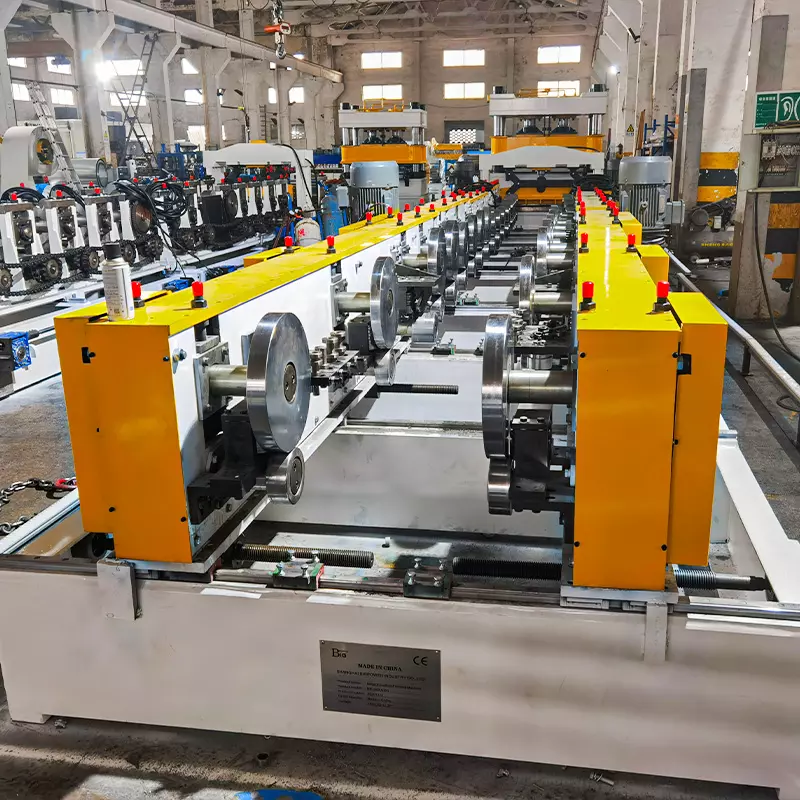
Key Features of Cable Tray Roll Forming Machines
When selecting a Cable Tray Roll Forming Machine, it’s essential to focus on features that maximize productivity, precision, and flexibility. Here are some must-have features:
1. High-Precision Rollers
The rollers are the heart of the machine. High-strength, chrome-plated steel rollers ensure consistent shaping and long-term durability.
2. Integrated Punching System
For perforated trays, integrated hydraulic or servo punching systems ensure precise ventilation holes.
3. PLC Control System
A Programmable Logic Controller (PLC) system automates machine settings, making it easy to adjust tray dimensions, hole patterns, and production speeds.
4. Quick Tool Change Mechanism
For multi-profile machines, quick-change tooling minimizes downtime when switching between tray designs.
5. Noise Reduction
Modern machines feature noise-dampening systems, making them suitable for factory environments where sound levels need to be controlled.
6. Material Compatibility
Ensure the machine can handle the materials you need, such as:
- Galvanized steel (corrosion-resistant)
- Stainless steel (high durability)
- Aluminum (lightweight applications)
Pricing of Cable Tray Roll Forming Machines
The cost of a Cable Tray Roll Forming Machine depends on its features, automation level, and production capacity. Here’s a general pricing guide:
Price Ranges
- Perforated Cable Tray Machines: $60,000–$100,000
- Ladder Cable Tray Machines: $70,000–$120,000
- Solid-Bottom Cable Tray Machines: $60,000–$110,000
- Multi-Profile Machines: $100,000–$200,000+
Automation Trends in Cable Tray Roll Forming Machines
Automation is reshaping the manufacturing industry, and cable tray roll-forming machines are no exception. Here are the latest trends:
1. IoT Integration
IoT-enabled machines allow you to monitor production metrics remotely, receive alerts about potential issues, and optimize workflows in real time.
2. Predictive Maintenance
AI-powered systems analyze machine data to predict when components like rollers or punches may fail, enabling proactive maintenance.
3. Fully Automated Production Lines
Advanced machines handle every step of the process, from material feeding to cutting and stacking, reducing labor costs and boosting efficiency.
FAQs About Cable Tray Roll Forming Machines
Let’s address some of the most frequently asked questions:
Question | Answer |
---|---|
Can these machines produce custom tray profiles? | Yes, multi-profile machines can be customized to produce unique tray designs. |
What’s the average production speed? | Production speeds range from 10–25 meters per minute, depending on the machine type. |
What materials can be processed? | Most machines handle galvanized steel, stainless steel, and aluminum within specified thicknesses. |
Do these machines require skilled operators? | No, advanced PLC systems make these machines user-friendly, requiring minimal operator training. |
What’s the lifespan of these machines? | With proper maintenance, these machines can last 10–15 years or more. |
Advanced Automation in Cable Tray Roll Forming Machines
The manufacturing world is evolving rapidly, and automation is leading the charge. Today’s Cable Tray Roll Forming Machines are smarter, faster, and more efficient than ever before. Here’s how advanced automation is shaping the industry in 2025:
1. IoT Integration for Smart Manufacturing
Imagine being able to monitor your machine’s performance from your smartphone or laptop. With IoT (Internet of Things) integration, cable tray machines now enable:
- Real-Time Monitoring: Track production rates, material usage, and system health remotely.
- Automated Alerts: Receive instant notifications about issues like material jams, misaligned rollers, or maintenance needs.
- Data Analytics: Use cloud-based storage to analyze production trends and optimize efficiency.
IoT integration not only reduces downtime but also allows manufacturers to make data-driven decisions for better productivity.
2. Fully Automated Production Lines
Modern Cable Tray Roll Forming Machines can handle the entire production process autonomously:
- Material Feeding: Automated coil feeding ensures consistent material flow.
- Punching and Forming: Servo-driven systems ensure precision in perforation and shaping.
- Cutting and Stacking: Advanced cutting mechanisms deliver clean edges, while stacking systems neatly arrange finished trays.
By eliminating manual intervention, fully automated systems minimize errors, improve safety, and maximize output.
3. Adaptive Profile Switching
For manufacturers that produce multiple types of cable trays, adaptive profile-switching systems are a game-changer:
- Quick Changes: Switch between perforated, ladder, and solid-bottom tray designs in minutes.
- PLC-Controlled Adjustments: Make profile changes directly from the machine’s touchscreen interface.
- Reduced Downtime: Enhanced flexibility means you can meet diverse customer demands without significant delays.
4. Predictive Maintenance with AI
Gone are the days of waiting for a machine failure to schedule repairs. Predictive maintenance tools use AI-powered sensors to:
- Detect wear and tear on rollers, punches, and cutters.
- Predict potential failures before they occur.
- Schedule maintenance proactively, reducing downtime and extending machine life.
Predictive maintenance tools can save manufacturers thousands of dollars annually in repair costs and lost productivity.
5. Energy-Efficient Servo Motors
Energy efficiency isn’t just good for the planet—it’s good for your bottom line. Servo motors are now standard in high-end machines, providing:
- Precision: Consistent forming and cutting accuracy.
- Speed: High throughput rates without compromising quality.
- Energy Savings: Reduced power consumption compared to traditional hydraulic systems.
At Wuxi Sunway Machinery, we’ve integrated these advanced automation features into our machines, ensuring that our clients are equipped to stay ahead in a competitive market.
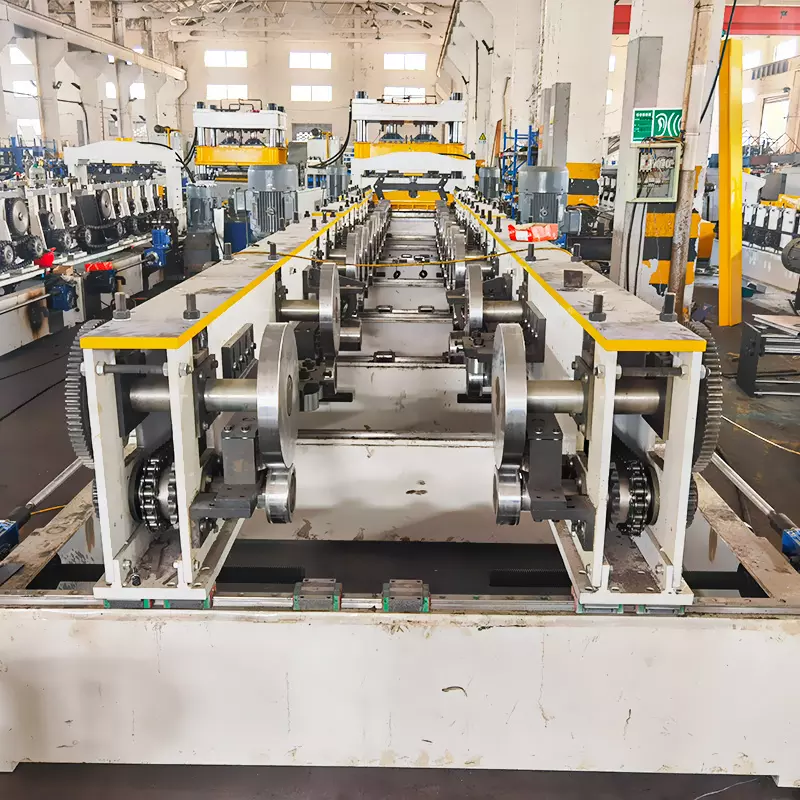
Troubleshooting Common Issues in Cable Tray Roll Forming Machines
Even with high-tech equipment, occasional hiccups are inevitable. Here’s a guide to identifying and resolving common issues in Cable Tray Roll Forming Machines:
1. Uneven Tray Profiles
- Cause: Misaligned rollers or inconsistent material feeding.
- Solution: Check roller alignment and recalibrate the machine settings. Ensure the material is fed evenly and without tension variations.
2. Material Jamming
- Cause: Improper coil feeding or debris in the machine.
- Solution: Clean all rollers, guides, and feeding mechanisms. Inspect the material coil for defects and ensure proper tensioning.
3. Inconsistent Perforations
- Cause: Worn punching dies or incorrect PLC programming.
- Solution: Replace worn punching dies and reprogram the PLC settings to match the desired hole pattern.
4. Burrs and Rough Edges
- Cause: Dull cutting blades or poorly aligned cutting mechanisms.
- Solution: Sharpen or replace cutting blades. Adjust the cutting mechanism alignment to ensure clean cuts.
5. Machine Downtime
- Cause: Lack of regular maintenance or undetected wear on components.
- Solution: Follow a strict maintenance schedule, including lubrication, cleaning, and inspections. Use predictive maintenance tools if available.
For professional troubleshooting support, reach out to Wuxi Sunway Machinery. Our team of experts is always ready to help.
Environmental Impact of Cable Tray Roll Forming Machines
Sustainability is a growing priority for manufacturers and consumers alike. Modern Cable Tray Roll Forming Machines contribute to eco-friendly production in the following ways:
1. Reduced Material Waste
The roll-forming process is highly efficient, utilizing nearly 100% of the raw material. Any scrap generated is minimal and can be recycled.
2. Energy Efficiency
Servo-driven systems and optimized hydraulic mechanisms reduce energy consumption, making these machines more eco-friendly than their predecessors.
3. Recyclable Materials
Cable trays are typically made from galvanized steel, aluminum, or stainless steel—all of which are fully recyclable. This ensures that end-of-life trays don’t contribute to landfill waste.
4. Long-Lasting Products
Cable trays produced by modern roll-forming machines are durable and corrosion-resistant, reducing the need for frequent replacements and lowering the overall environmental impact.
By choosing energy-efficient machinery, manufacturers can reduce their carbon footprint and align with global sustainability goals. At Wuxi Sunway Machinery, we prioritize sustainability in our designs.
FAQs About Cable Tray Roll Forming Machines
Still have questions? Let’s address some of the most frequently asked questions about Cable Tray Roll Forming Machines:
Question | Answer |
---|---|
What is the typical production speed? | Most machines can produce 10–25 meters of cable tray per minute, depending on the tray type and material. |
Can one machine produce multiple tray styles? | Yes, multi-profile machines can produce perforated, ladder, and solid-bottom trays with quick tooling changes. |
What materials can these machines process? | Common materials include galvanized steel, stainless steel, and aluminum, with thicknesses ranging from 0.8mm to 2.5mm. |
How long does it take to switch profiles? | With automated profile switching, changes can be made in just a few minutes. Manual changes may take longer. |
Do these machines require skilled operators? | No, advanced PLC systems make these machines user-friendly and require minimal operator training. |
What is the average lifespan of these machines? | With proper maintenance, these machines can last 10–15 years or more, offering excellent ROI. |
Are financing options available? | Yes, manufacturers like Wuxi Sunway Machinery offer flexible financing plans. |
Why Choose Wuxi Sunway Machinery for Cable Tray Roll Forming Machines?
When it comes to roll-forming technology, Wuxi Sunway Machinery is a global leader. Here’s why manufacturers worldwide trust us:
- Unmatched Expertise: Decades of experience in designing and manufacturing roll-forming machines for diverse applications.
- Custom Solutions: Machines tailored to your specific production needs, whether for standard or unique profiles.
- Global Reputation: With clients in Asia, Europe, Africa, and beyond, we’re a trusted partner across industries.
- Innovation: We integrate cutting-edge technologies like IoT, servo-driven systems, and predictive maintenance into our designs.
- Comprehensive Support: From installation to maintenance and spare parts, we’re with you every step of the way.
Conclusion: Is a Cable Tray Roll Forming Machine the Right Investment for You?
If you’re in the electrical, construction, or renewable energy sectors, investing in a Cable Tray Roll Forming Machine is a game-changing decision. These machines offer unmatched efficiency, scalability, and precision, enabling you to meet the growing demand for cable trays across industries.
For a reliable partner in roll-forming technology, choose Wuxi Sunway Machinery. With our innovative designs, global expertise, and commitment to customer satisfaction, we’re here to help you elevate your manufacturing game. Ready to transform your production line? Let’s roll into a brighter, more profitable future—together!