Rolling shutters are collapsible doors, gates or windows containing horizontal slats made of metal or plastic that roll up and down by sliding along tracks to open and close. Dedicated roll forming equipment is used to rapidly produce the curved shutter slat profiles in high volumes at low costs.
This comprehensive guide provides in-depth details on rolling shutter door slats roll forming machines including:
Overview of rolling shutter door slats roll forming machine
Roll forming shutter slats involves gradually bending sheets or coils of aluminum, steel, vinyl etc. into a curved shape using a series of roller dies for enclosure and security applications.
Key benefits of roll formed shutter profiles:
- High production rates and low costs
- Flexibility for custom shapes and dimensions
- Consistent quality across long lengths
Roll forming lines can be customized to produce various shutter slat geometries and configurations optimally.
Table 1: Shutter Roll Former Machine Types
Equipment | Description |
---|---|
Standard Roll Formers | Basic machines for standard slat profiles |
C and U Bending Machines | Specialized equipment for pronounced bends |
Multi-Profile Lines | Quick changeover between multiple shapes |
Automated Lines | Integrated material handling and controls |
Custom Roll Formers | Tailored to produce special slat geometries |
Now that we’ve covered the basics, let’s understand how shutter slat roll forming machines work.
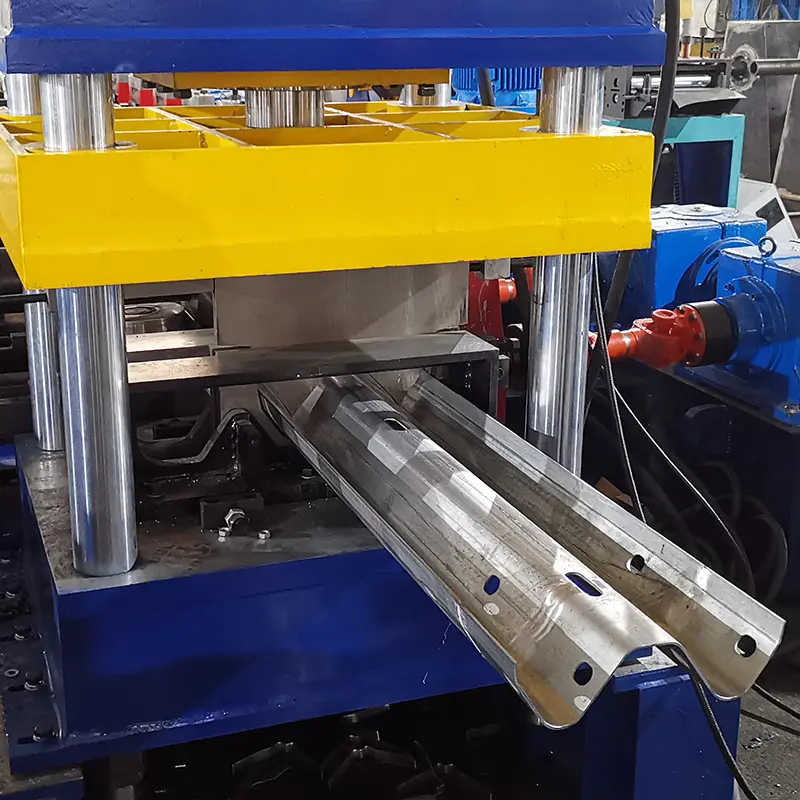
rolling shutter door slats roll forming machine Working Principle
The roll forming process involves:
Steps:
- Feeding metal coil through straightening rolls
- Forming slat profile using contoured roller dies
- Calibrating shape by subsequent stands
- Cutting slats to specified length
- Counting and Stacking finished pieces
Core Components:
Part | Role |
---|---|
Decoiler | Feeds input coil |
Straightener | Removes coil curvature |
Roll Housing | Mounts contour roller dies |
Rotary Shear | Trims slats to length |
Delivery Table | Stacks output |
Gradual bending by the dies enables producing continuous lengths of shutter slats rapidly without defects.
Now that we’ve reviewed the process fundamentals, let’s examine the key design factors for building shutter slat roll formers.
Shutter Slat Roll Former Design Considerations
To create equipment that produces quality shutter slats matching requirements, parameters considered during design include:
Table 2: Shutter Slat Roll Former Design Factors
Aspect | Details |
---|---|
Material | Steel, aluminum grades – gauge, width |
Slat Profile | Shape, bend radius, ribbing |
Forming Speed | Optimized for strain rates, thickness |
Die Contours | Precision machining for profile dimensions |
Added Features | Embossing, notching, drilling |
Line Automation | Material handling, control system |
The designer has to balance these interdependent parameters to build effective and efficient shutter slat roll forming equipment.
Now that we have seen the design process, let’s explore materials used and profile options that can be formed for shutters.
Shutter Slat Materials for Roll Forming Lines
Common metal coil materials fed into these machines include:
Table 3: Shutter Slat Raw Materials
Material | Features | Thickness Range |
---|---|---|
Aluminum | Lightweight, strong | 0.3 – 1 mm |
Galvanized Steel | Corrosion-resistant coating | 0.4 – 1 mm |
Stainless Steel | Robust weatherproof finish | 0.5 – 1.25 mm |
Vinyl (PVC) | Low cost, easy forming | 0.10 – 0.20 inches |
Material choice depends on:
- Strength needed by the application
- Corrosion resistance requirements
- Budget constraints
Now let’s look at profile options:
Table 4: Typical Shutter Slat Profiles
Profile | Description | Typical Uses |
---|---|---|
C Shaped | Pronounced concave bend | Storm protection shutters |
Z Shaped | Sharp angled ribs | Counter shutters, enclosures |
Interlocking | Offset bends fit together | Garage, warehouse doors |
Insulated | Foam filled hollow slats | Temperature controlled rooms |
More contours and ribs add strength. Insulated profiles improve noise, heat transfer performance.
After seeing the materials and profiles related to shutter slats, let’s move on to examining OEM roll former manufacturers – key selection criteria and price range.
-
Vineyard Post Roll Forming Machine
-
Auto Size Changeable Sigma Purlin Roll Forming Machine
-
PV Mounting Bracket C Shape Profile Roll Forming Machine
-
C Z Purlin Channel Cold Roll Forming Machine Full Auto Galvanized Steel Profile
-
Steel Coil Cut To Length Line Machine
-
Steel Coil Cut To Length Line Machine
-
Steel Coil Cut To Length Line Machine
-
PV Mounting Bracket Roll Forming Machine (HAT / Omega Profile)
-
PV Mounting Bracket Z Shape Profile Roll Forming Machine
Choosing Shutter Slat Roll Former Manufacturers
Due to their heavy nature and need for customization, evaluating OEM vendors on multiple aspects helps get high performance roll formers for producing shutter slats.
Table 5: Shutter Slat Roll Former OEM Selection Criteria
Parameter | Details |
---|---|
Technical Expertise | Experience serving enclosure industry clients with domain expertise |
Production Facility | Manual and CNC machinery to fabricate heavy-duty forming lines |
Quality Control | Certifications, testing capabilities for consistent standards compliance |
Customization Skills | Equipped for specialized slat geometries, secondary operations |
Services Offered | Design support, operator training, installation and maintenance |
Delivery & Reliability | Proven ability to execute customized projects on schedule |
Pricing | Quality equipment balancing performance and budget |
Industry references and site visits to existing installations build confidence regarding vendor capabilities.
Price range:
- Manual Roll Former – $40,000 to $100,000
- Automated Line – $100,000 to $200,000
- Custom Roll Former – $200,000+
Exact pricing depends on size, production rates and level of automation needed.
Now that we have guidance on selecting OEM partners, let’s examine the pros and cons of buying versus outsourcing slat production.
Buy Versus Outsource Considerations for Shutter Slats
Purchasing own equipment offers control but has significant tradeoffs to weigh against using external roll forming services:
Table 6: Own Machines vs. Outsourcing for Shutter Slats
Consideration | Implications |
---|---|
High Initial Capital | Large cash outlay, long payback period |
Material and Labor Savings | Lower per unit production costs at high volumes |
Quality Control | Full oversight over entire process |
Changeovers | Downtime for adjustments disrupts production scheduling |
Operating Overheads | Skilled labor, maintenance expenses |
Flexibility | Faster design iterations, improve shutters over time |
Manufacturers should assess projected production needs, cost economics, available factory space and team capabilities before deciding between bringing slat roll forming in-house or outsourcing.
Trying out initial batches from tolling services helps validate demand before equipment purchase.
Now that we’ve weighed roll former ownership costs, let’s examine operational factors like installation, operation and maintenance.
Shutter Slat Roll Former Installation, Operation and Maintenance
Getting shutter slat roll formers running efficiently once delivered requires:
Table 7: Shutter Slat Roll Former Installation & Operation
Activity | Details |
---|---|
Site Preparation | Level foundations, electrical connections, material flow zones |
Machine Assembly | Bolt stands, connect power and controls per drawings |
Commissioning | Calibrate sensors, test emergency stops, debug circuits |
Trial Runs | Validate output rates, quality metrics using test materials |
Operator Training | Review control software, setup procedures, safety |
Ongoing Operation | Monitor line status, assist part ejection, packaging |
Following recommended procedures and preventative maintenance helps maximize production uptime.
Regular maintenance activities include:
- Cleaning and lubricating forming dies
- Inspecting bearings, sensors, hydraulics for wear
- Replacing worn components like blades
- Software and firmware upgrades
Now that we’ve covered the production phase, let’s conclude by recapping the main advantages and limitations around shutter slat roll forming equipment.
Pros and Cons of Shutter Slat Roll Forming Machines
Table 8: Shutter Slat Roll Former Advantages and Limitations
Consideration | Details |
---|---|
High Productivity | Hundreds of feet formed per minute |
Short Lead Times | Rapid delivery for rush orders |
Lower Labor Costs | Automated process needs few operators |
Shape Limitations | Gradual bends feasible |
Quality Control | Tight tolerances hard to achieve |
Line Changeover | Downtime for profile adjustments |
Weighing these key factors helps manufacturers make optimal equipment investment and production choices.
I hope this guide covers the shutter slat roll forming machine details needed by metal fabricators, integrators and end-customers exploring producing these essential collapsible door components. Let me know if you need any clarification or have additional questions!
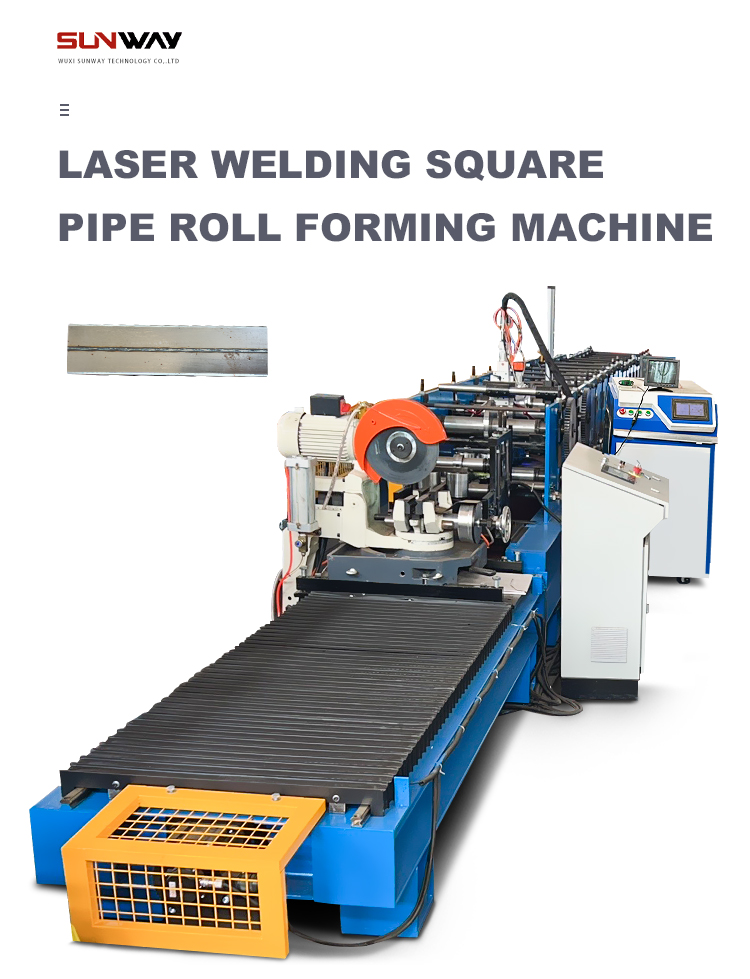
Frequently Asked Questions
Q: What expertise is required to operate shutter slat roll formers?
A: Skilled technicians able to interpret drawings, calibrate sensors, handle coil stock and inspect quality standards compliance are needed to setup and run shutter slat roll forming lines efficiently.
Q: How are the curved shutter slats joined together?
A: Interlocking end clips or separate hinges are used to link each C/Z-shaped slat vertically into a collapsible door assembly that slides within side rails as it rolls up.
Q: What determines shutter durability?
A: Shutter life is affected by material grade selected, slat profile design, coating treatments, lubrication applied and frequency of use. Manual versus motorized opening/closing also impacts wear rates.
Q: Can PVC slats be recycled?
A: While steel and aluminum slats can readily be recycled, PVC typically ends up in landfills. However vinyl recover initiatives aimed at shutter recycling enables reuse opportunities.