Overview of Roll Forming Systems
Roll forming systems are an essential part of modern manufacturing, particularly in the production of metal components. These systems transform metal sheets into specific shapes by passing them through a series of rollers. The process is continuous and highly efficient, producing consistent and precise results. From automotive parts to construction materials, roll forming is a versatile and vital technology.
What Are Roll Forming Systems?
Roll forming is a type of metal forming process that involves feeding a long strip of sheet metal (usually coiled steel) through a series of rollers. Each roller set performs incremental parts of the bend until the desired cross-section profile is obtained. This process is ideal for producing large volumes of consistent products, making it a preferred choice for many industries.
Why Use Roll Forming Systems?
Roll forming systems offer numerous advantages over other metal forming processes:
- Efficiency: Continuous operation allows for high-speed production.
- Consistency: Ensures uniformity across all produced parts.
- Cost-Effectiveness: Reduces material waste and labor costs.
- Flexibility: Capable of producing complex shapes with high precision.
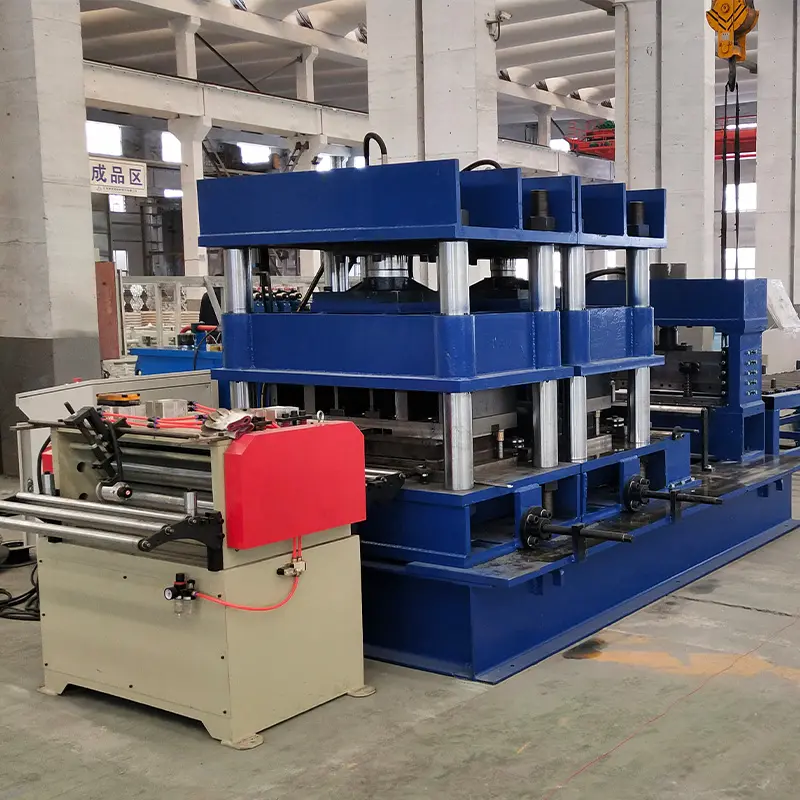
Types of Roll Forming Systems
Different types of roll forming systems are available, each suited to specific applications and materials. Here’s a look at some common types:
Type of Roll Forming System | Description |
---|---|
Single-Stage Roll Forming | Basic form where the entire process is completed in one stage. Ideal for simple shapes. |
Multi-Stage Roll Forming | Involves multiple stages of forming, suitable for complex profiles. |
Adjustable Roll Forming | Allows for adjustments to accommodate different profiles and materials. |
Inline Roll Forming | Integrates additional processes such as punching and notching within the roll forming line. |
Duplex Roll Forming | Two independent forming sections for increased flexibility and efficiency. |
Working Process of Roll Forming Systems
The roll forming process is systematic and involves several stages. Here’s a detailed look at each step:
- Material Feeding: The metal coil is fed into the machine.
- Leveling: The material is straightened to remove any initial curvature.
- Forming: The material passes through a series of roller stations, each progressively shaping it.
- Cutting: The formed metal is cut to the desired length.
- Finishing: Any additional processes such as punching, notching, or embossing are performed.
Key Components and Their Functions
Understanding the components of roll forming systems is essential for effective operation and maintenance. Here’s a breakdown of the key parts:
Component | Function |
---|---|
Uncoiler | Feeds the metal coil into the roll forming machine. |
Roll Stands | Support and house the rollers that shape the metal. |
Rollers | Incrementally bend the metal into the desired profile. |
Cutting Mechanism | Cuts the formed metal to the required length. |
Control System | Manages the operation of the machine, ensuring precision and efficiency. |
-
Highway Guardrail End Terminal Forming Machine
-
Highway U/C Post Roll Forming Machine
-
2 Waves Highway Guardrail Roll Forming Machine
-
3 Waves Highway Guardrail Roll Forming Machine
-
Vineyard Post Roll Forming Machine
-
Auto Size Changeable Sigma Purlin Roll Forming Machine
-
Auto Size Changeable C Z Purlin Roll Forming Machine
-
Auto Size Changeable Z Purlin Roll Forming Machine
-
Auto Size Changeable C U Purlin Roll Forming Machine
Machine Speed and Efficiency
Speed and efficiency are critical in roll forming operations. Here’s a table detailing typical machine speeds and efficiencies:
Machine Type | Speed (m/min) | Efficiency (%) |
---|---|---|
Basic Roll Forming | 30-60 | 85-90 |
High-Speed Roll Forming | 60-120 | 90-95 |
Precision Roll Forming | 10-30 | 80-85 |
Customized Mechanical Parameters
Different applications require different mechanical parameters. Here’s a table showing some customizable parameters:
Parameter | Range |
---|---|
Material Thickness | 0.2-6.0 mm |
Profile Width | 20-600 mm |
Roller Diameter | 50-400 mm |
Number of Roll Stands | 4-30 |
Applications of Roll Forming Systems
Roll forming systems have a wide range of applications across various industries:
Application | Description |
---|---|
Automotive | Producing parts like bumpers and chassis. |
Construction | Making roofing, wall panels, and gutters. |
Appliance Manufacturing | Forming parts for refrigerators, ovens, etc. |
Storage Solutions | Creating shelving units and racks. |
Energy Sector | Manufacturing parts for solar panels and wind turbines. |
Installation, Operation, and Maintenance
Proper installation, operation, and maintenance are vital for the optimal performance of roll forming systems:
Aspect | Description |
---|---|
Installation | Ensure a stable foundation and accurate alignment of components. |
Operation | Regularly monitor and adjust machine settings for consistent output. |
Maintenance | Perform routine inspections and replace worn-out parts to prevent downtime. |
Suppliers and Price Range Details
Choosing the right supplier is crucial for acquiring a reliable roll forming system. Here’s a list of some prominent suppliers and their price ranges:
Supplier | Price Range |
---|---|
ABC Roll Forming | $50,000 – $150,000 |
XYZ Machinery | $60,000 – $200,000 |
FormTech Inc. | $55,000 – $180,000 |
RollSys Solutions | $65,000 – $220,000 |
How to Choose a Supplier
Selecting a supplier involves several considerations. Here’s a guide to help you make an informed decision:
Criterion | Considerations |
---|---|
Reputation | Look for reviews and testimonials. |
Experience | Prefer suppliers with a proven track record in the industry. |
Customization Options | Ensure they offer customizable solutions to meet your specific needs. |
Support and Service | Check if they provide comprehensive after-sales support. |
Price | Compare prices but also consider the quality and features offered. |
Comparing Pros and Cons
Different roll forming systems have their advantages and limitations. Here’s a comparative look:
System Type | Advantages | Limitations |
---|---|---|
Single-Stage | Simple setup, lower cost | Limited to simple profiles |
Multi-Stage | Handles complex shapes | Higher initial investment |
Adjustable | Versatile, adaptable | Requires more adjustments |
Inline | Integrates additional processes | More complex setup |
Duplex | High flexibility, efficiency | Higher cost and space requirements |
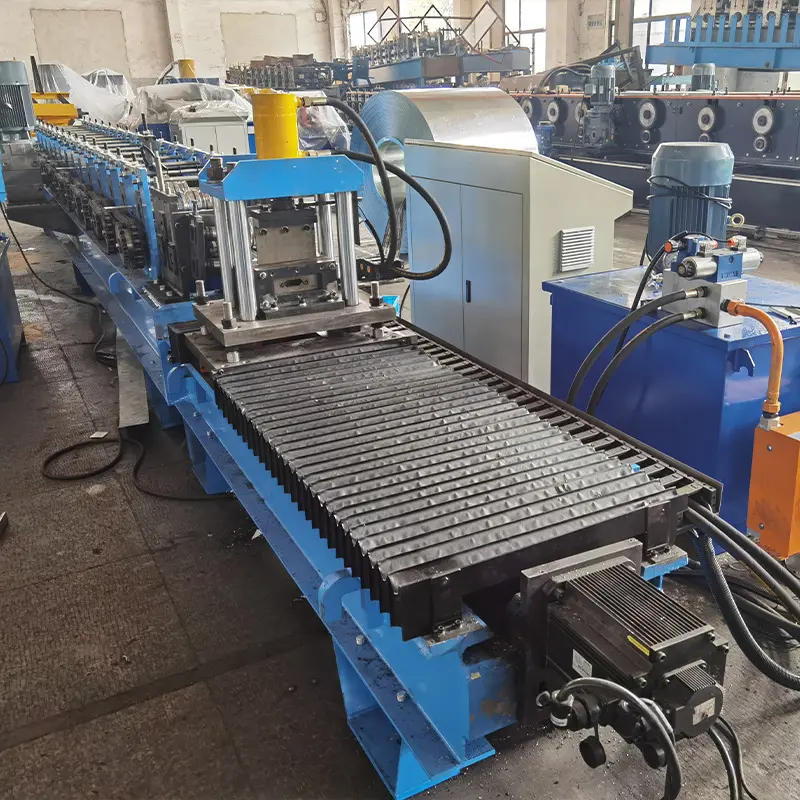
FAQ
Here are some frequently asked questions about roll forming systems, along with their answers:
Question | Answer |
---|---|
What materials can be roll formed? | Metals like steel, aluminum, and copper are commonly used. |
How does roll forming compare to stamping? | Roll forming is continuous and better for long lengths; stamping is ideal for intricate shapes. |
What are the common defects in roll forming? | Bowing, camber, and twist are common defects that can be controlled with proper setup. |
Can roll forming systems be automated? | Yes, modern systems often include automation for improved efficiency. |
What is the typical lifespan of a roll forming machine? | With proper maintenance, these machines can last several decades. |
Conclusion
Roll forming systems are indispensable in various manufacturing sectors due to their efficiency, consistency, and flexibility. By understanding the types, working processes, key components, and other crucial aspects, businesses can optimize their use and achieve superior results. Whether you’re in automotive, construction, or another industry, roll forming systems offer a reliable solution for your metal forming needs.