Overview
An OEM metal roll forming machine is a versatile industrial equipment system used to efficiently mass produce long lengths of precision custom metal parts and profiles for original equipment manufacturers.
The continuous roll forming process shapes metal coil feedstock into various rails, frames, enclosures and structural components using a series of rotating roller dies.
This guide provides a comprehensive overview of OEM roll former technology, including:
- Machine types and components
- How the roll forming process works
- Design considerations
- End use applications
- Material and specification standards
- Cost analysis
- Comparisons with other metal fabrication methods
Gaining insight into OEM metal roll former capabilities assists manufacturers evaluating optimized production solutions for metal components used in specialized equipment and products.
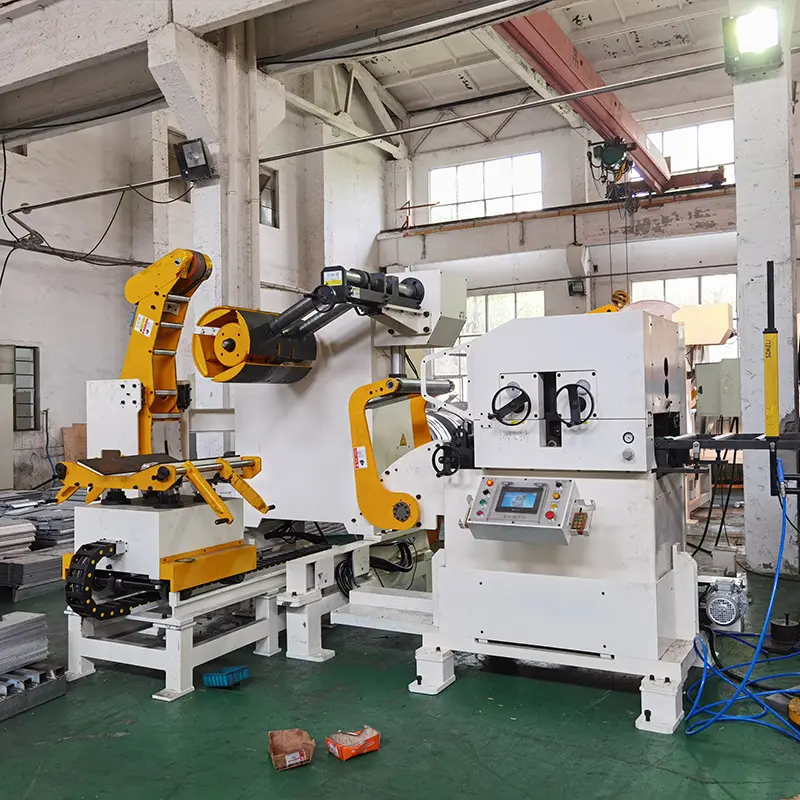
Types of OEM Metal Roll Forming Machines
There are two primary machine configurations for high volume OEM parts production:
Fixed Head Roll Formers
- Typically 10-16 forming stations
- Common base profiles
- Lower tooling cost
- Repeat jobs
Quick Change Roll Formers
- Individual stations per head
- Flexible tooling for profile variations
- Higher output variety
- Frequent form changes
Main Components of a Metal Roll Former
A typical OEM metal roll forming system integrates these main sections:
Coil Payoff Reel
- Holds raw coil at unwind station
- Feeds strip through process
Entry Guides
- Align and straighten strip
- Optimize material feed
Accumulator/Bridle
- Creates back tension zone
- Smooths flow variations
Forming Stations
- Progressive die rollers shape material
- Number & type determine profile
Cutter
- Shears finished parts to length
- Pneumatic, servo electric
Exit Conveyor
- Transfers finished product
- Links to secondary operations
Automation Controls
- HMI and PLC hardware
- Touchscreen programming
- Data feedback
How Metal Roll Forming Machines Work
The OEM roll forming process shapes metal coil feedstock into rails, frames and custom profiles by bending and forming the strip material incrementally as it passes through a series of roller die stations:
- Powered coil payoff reel feeds raw coiled strip into initial machine guides
- Entry guides align strip and feed into first roller station
- At each station, machined rollers make precision bends and forms
- Strip exits slightly more formed moving to subsequent stations
- Finished custom profile emerges at end of forming line
- Profile cutoff to length by pneumatic or servo shear
- Formed parts conveyed for additional fabrication
The number of roller die stations determines possible shape complexity. Quick changeovers accommodate low to high mix production.
-
Highway Guardrail End Terminal Forming Machine
-
Highway U/C Post Roll Forming Machine
-
2 Waves Highway Guardrail Roll Forming Machine
-
3 Waves Highway Guardrail Roll Forming Machine
-
Two waves highway guardrail machine
-
Three waves highway guardrail machine
-
Steel Coil Cut To Length Line Machine
-
Steel Coil Cut To Length Line Machine
-
Steel Coil Cut To Length Line Machine
Key Design Factors for OEM Roll Forming
Equipment specifiers evaluate numerous characteristics when selecting OEM metal roll formers:
Product Type
- Metal structural framing
- Equipment enclosures
- Machine bases and supports
Material
- Mild steel
- Stainless steel
- Aluminum
- Other alloys
Thickness
- 20 gauge to 1/4”
- 0.6 mm to 6 mm
Profile
- C & U channels
- Complex rails and frames
- Hollow box sections
Length
- Up to 30′ possible
- Exit tables for support
Speed
- 10 to 100+ feet/min
- Low vs high cycle times
Changeover
- Quick change tooling
- Repeatable accuracy
Automation
- Level required
- Data feedback
Floor Space
- Line length
- Layout constraints
Standards for OEM Roll Formed Metals
While having fewer universal specifications, these guidelines apply to certain OEM components:
Standard | Description |
---|---|
ASTM A792 | Steel sheet UV performance |
ASTM A1008 | Low carbon steel sheet grades |
EN 10346 | Continuously hot dipped coatings |
IATF 16949 | Automotive quality management |
Typical Applications for Roll Formed Metals
Common end uses for roll formed metals in original equipment include:
Electrical Equipment
- Motor and transformer frames
- Switchgear housings
- Generator enclosures
Machinery Structures
- Machine bases
- Robotic arm supports
- Conveyor frames
Commercial Appliances
- Refrigerator liners
- Range and oven cavities
- Washer and dryer drums
HVAC Components
- Furnace and AC housing
- Heat exchangers
- Ducting frames
Furniture
- Desk and cabinet frames
- Shelving posts and rails
- Table bases
White Goods
- Dishwasher tubs
- Clothes dryer cylinders
- Range oven cavity frames
Specifications
Metric | Typical Range |
---|---|
Thickness | 0.5 mm – 3 mm |
Width | 10 mm – 300 mm |
Height | 10 mm – 150 mm |
Length | 50 mm – 20,000 mm |
Holes | 1 mm – 20 mm dia |
Loads | 50 kg – 3000 kg |
Manufacturers of oem metal roll forming machine
Leading global OEM metal roll former manufacturers include:
Company | Location |
---|---|
Formtek | USA |
Bradbury | USA |
DIMA | Italy |
Shanghai Winsun | China |
BOTOU Xianfa | China |
Pricing
Machine | Average Cost (USD) |
---|---|
Basic Manual Roll Former | $38,000 |
20 Station Servo-Electric | $120,000 |
High Speed Quick Change | $240,000 |
Rolled Part | Typical Cost per Kg (USD) |
---|---|
Mild Steel Channel | $2 |
Stainless C-Rail | $5 |
Aluminum Profile | $10 |
Advantages of OEM Metal Roll Forming
Benefits
- High hourly production rates
- Precision tolerances
- Low operational costs
- Minimal secondary fabricating
- High material utilization
- Lean, continuous-flow process
Limitations
- Substantial initial capital costs
- Mostly long, straight geometries
- Tooling expensive for low volumes
- Can require secondary punching, welding, drilling
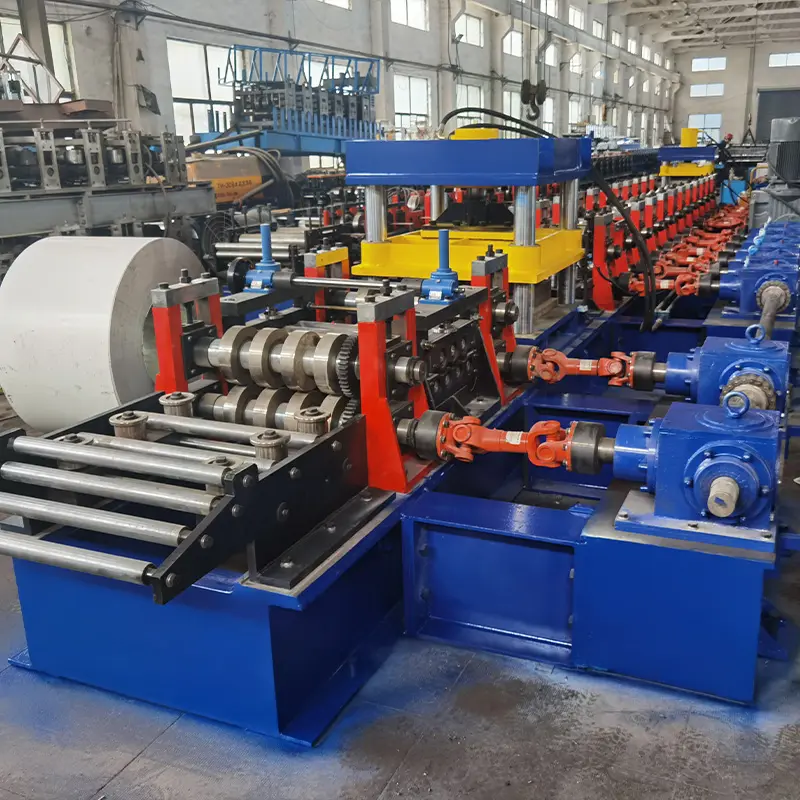
FAQ
What metals work with OEM roll forming?
All ductile metals can use roll forming including low carbon steel, stainless steel, aluminum, copper, and titanium alloys. Hardened materials may require specialized tooling.
What tolerances are possible with OEM roll formed parts?
Roll formed components can reliably achieve profile tolerances between +/- 0.1 mm to +/- 0.25 mm for quality machines depending on the material gauge.
How long can an OEM roll formed metal part be?
Standard maximums with support tables are around 18 meters (60 feet). Custom long bed machines can produce sections over 30 meters (100 feet).
How thick of metal can an OEM roll former handle?
Thicknesses from 0.15 mm (30 gauge) to about 6 mm (1/4 inch) are typical for an average OEM roll former. Beyond that may require custom heavy-duty equipment.