Metal roofing tile roll forming machines are equipment used to produce metal roofing tiles and panels through continuous bending and forming of coil material. These versatile machines allow fast, high-volume production of roofing components with custom profiles.
This comprehensive guide covers all aspects of metal roofing tile roll formers from working principles and main components to models, specifications, applications and more.
Overview of Metal Roofing Tile Roll Forming Machines
What are Metal Roofing Tile Roll Forming Machines?
Metal roofing tile roll forming machines take flat metal coil stock and progressively form it into various roofing tile profiles through a series of roller dies and bending stages.
The continuous operation allows roofing components like panels, shingles and tiles to be mass-produced rapidly compared to manual fabrication.
Key Features and Working Principle
- High speed continuous roll forming of metal coil into roofing tile profiles
- Flexible production with quick roll set changeovers
- Rollers and guides progressively shape flat strip into ribbed/corrugated profiles
- Automated cutting after forming tiles of fixed length
- Decoilers hold metal coil stock and feed strip through infeed guides
- Forming roll stands with roller dies make repeated bends and forms
- Adjustable for width, thickness, materials of coil stock
- PLC based controls for automatic operation and monitoring
Main Components and Systems
Metal roof tile roll forming machines include the major components outlined below:
- Coil Holding System: Decoiler or uncoiler holds metal coil stock and allows controlled feeding of strip through guides into first forming stand. Turntable type decoilers provide continuous feed without downtime.
- Feeding and Guiding: Feed rollers grip and pull metal strip through guides maintaining proper alignment entering forming section.
- Forming Stands: Multiple stands with roller dies make progressive bends and profiles to coil strip transforming it into roofing tiles or panels.
- Cutting Unit: Automated cut-off knives slice formed metal sheets into fixed tile/panel lengths for collection
- Conveying and Stacker: Formed and cut sheets conveyed to exit stacker for organized collection
- Controls: PLC based controls allow adjustable parameters and automated roll forming operation
- Frame and Housing: Rigid structural frame houses components with safety covers and guards
Roll Forming Process Overview
The basic working principle involves coil stock being unwound, straightened, and fed into the forming section. The strip passes through consecutive stands where precision roller dies make incremental bends. The cumulative effect of multiple bends transforms the flat strip into desired roofing tile profiles. The formed sheets are then cut into fixed lengths and stacked at the exit.
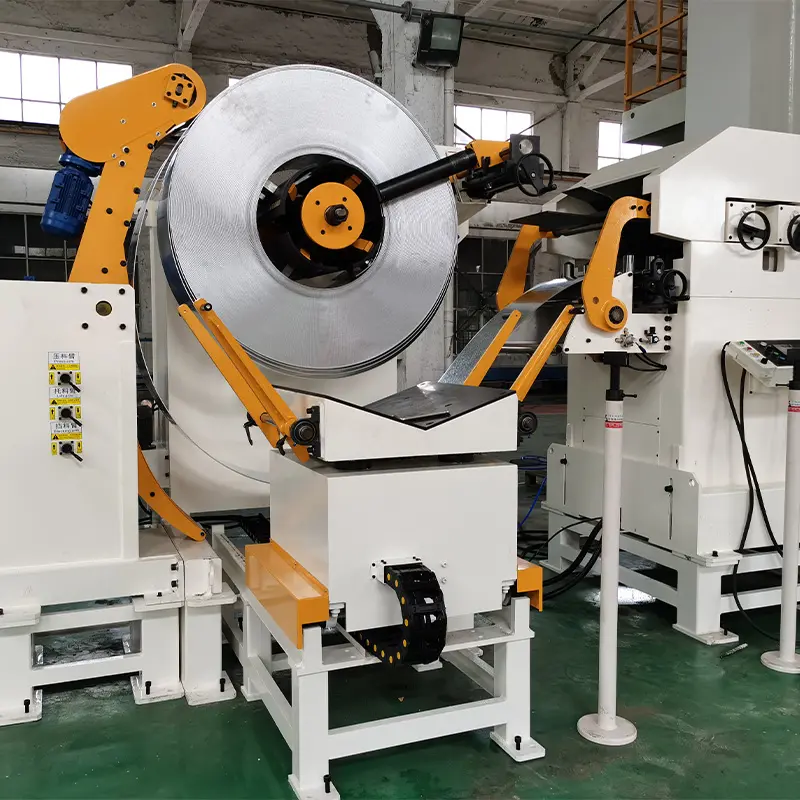
Types of Metal Roof Tile Roll Forming Machines
Metal roof tile roll formers can be categorized based on production scale, forming method and profile shapes:
Types by Production Scale
- Light-duty: Lower capacity machines for small scale production
- Medium-duty: Balanced performance for typical metal roofing needs
- Heavy-duty: High capacity formers for large volume requirements
Type | Coil Width | Sheet Thickness | Speed Range |
---|---|---|---|
Light-duty | Up to 1000 mm | 0.3 – 0.8 mm | 10 – 20 m/min |
Medium-duty | Up to 1250 mm | 0.4 – 1 mm | 15 – 40 m/min |
Heavy-duty | Above 1250 mm | 0.5 – 1.2 mm | 25 – 80 m/min |
Types by Forming Method
- Roll Former: Roller dies bend metal strip into roofing profiles
- Press Brake: Machined dies stamp roofing components in single action
- Panel Roll Former: Produces larger metal roofing panels
Machine | Method | Typical Products |
---|---|---|
Roll former | Roll forming | Roofing shingles, tiles |
Press brake | Press forming | Individual roofing sheets |
Panel roll former | Roll forming | Large roofing panels |
Types by Profile Shape
- Standing Seam: Long panels with vertical ribs, no exposed fasteners
- Batten Roll: Formed battens (caps) over roofing panels
- Corrugated: iconic waved/corrugated sheet profiles
- Shake Tile: Resembles look of shingles or shake roofing
- Metal Slate: Mimics traditional slate roofing tiles
- Custom: Unique profiles for decorative roofs
Profile Shape | Description | Example Products |
---|---|---|
Standing seam | Long panels, vertical ribs | Snap-lock panels, concealed fastener roofs |
Batten roll | Capped sheets with raised batten | Metal roof with battens, flat pan formed sheets |
Corrugated | Waved/corrugated sheets | Standard corrugated roofing, barn style |
Shake tile | Formed sheets resembling shingles | Interlocking shake pattern tiles |
Metal slate | Sheet metal in slate tile shapes | Faux slate roof system |
Custom | Unique/decorative profiles | Rolled Spanish clay tiles, fish-scale pattern |
Main Specifications
The key specifications of a metal roof tile roll forming machine include:
Parameter | Typical Range |
---|---|
Coil Width Capacity | 1000 – 1250 mm |
Metal Thickness | 0.3 – 1.2 mm |
Sheet Width | 500 – 1000 mm |
Profile Height | 10 – 75 mm |
Forming Speed | 10 – 80 m/min |
Main Drive Power | 5.5 – 37 kW |
Roller Diameter | 100 – 140 mm |
Number of Stands | 5 – 24 |
Machine Dimensions | 6000 x 1200 x 1700 mm |
Machine Weight | 2000 – 10000 kg |
- Capable of processing carbon steel, stainless steel, aluminum and other metal coils
- Quick roll set changeover and profile adjustments
- Accepts hot-dip galvanized, pre-painted and finished coils
- CNC controls for easy parameter settings
Typical Applications and Uses
Metal roofing tile roll forming machines have broad applications across industries:
Industry | Typical Applications |
---|---|
Construction | Roofing sheets, wall cladding, roof drainage, flashing |
Infrastructure | Large warehouses, industrial sheds, shelters |
Architecture | Decorative roofing accents, facades |
Automotive | Trailers, vehicle bodies, RV exterior |
Agriculture | Barns, stables, shelters, storage |
Common uses and processed products include:
- Metal roofing shingles, tiles, shakes
- Standing seam roofing systems
- Corrugated and ribbed roofing sheets
- Wall and facade cladding profiles
- Sheet metal roof drainage components
- Flashing, drips, trim pieces
- Agricultural building roofing and siding
- Trailer and vehicle body panels
Design and Engineering Standards
Metal roofing tile roll forming lines are designed and built to relevant standards:
Component | Standards |
---|---|
Roll Forming | EN 10149, ASTM A568, ASTM A1011 |
Sheet Metal | EN 10143, EN 10346 |
Machine Design | ISO 12100, ANSI B11 |
Electrical | IEC 60204, NFPA 79 |
Automation | IEC 61131, PLCopen |
Fasteners | AS 3566, FM 4471 |
Coatings | ASTM A755, ASTM A792 |
Safety | OSHA, CE directives |
- Materials used follow specifications such as yield strength, corrosion resistance and coatings
- Quality management per ISO 9001 during manufacturing
- Safety integrated into design, guards, controls per guidelines
- Standards ensure long service life and safe operation
Roll Former Manufacturers and Suppliers
There are many equipment manufacturers offering metal roofing tile roll formers:
Company | Location | Product Models |
---|---|---|
Metform | Turkey | IMP tile formers, Symphony corrugated lines |
DIMECO | China | Heavy duty roofing roll formers |
efficacy | Taiwan | Roofing panel and rainware machines |
Formtek | USA | Maxima roofing sheet roll former |
China Henan | China | EP series ceiling tile machines |
Kingsland | Malaysia | Wide sheet roof panel machines |
- Large international companies with global reach and exports
- Regional and domestic manufacturers in metal working markets
- Factory direct sales from manufacturers
- Machines marketed through machinery dealers and distributors
Pricing depends on specifications, capacity, customization and other factors. As a rough estimate, costs range from $30,000 to $150,000 per roll forming line.
Installation, Operation and Maintenance
Proper installation, usage and care is key to utilizing a metal roof tile roll former effectively:
Stage | Activities |
---|---|
Installation | – Floor mounting, anchoring<br>- Power, utilities setup<br>- Calibration, test runs |
Operation | – Material coil loading<br>- Parameter adjustment<br>- Roll set changeover |
Maintenance | – Inspections, lubrication <br>- Component servicing<br>- Wear/damage monitoring |
- Install machines on flat and level surface
- Setup appropriate utilities – electrical, pneumatic, hydraulic
- Trial runs to verify performance after installation
- Control feed rates, profiles, speeds for process stability
- Schedule preventive maintenance during production breaks
- Replace consumables like seals, belts and lubricants
Proper installation, operation and maintenance ensures maximum production uptime and roofing quality.
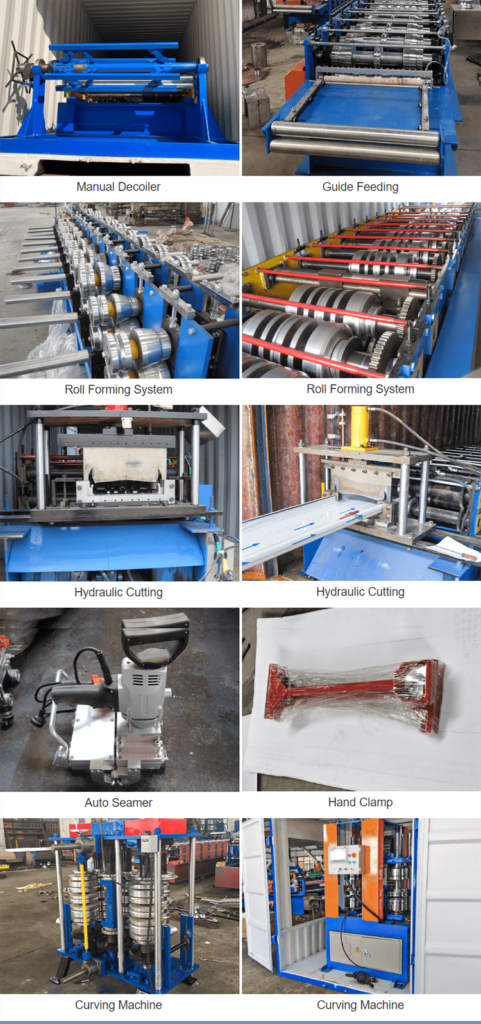
How to Choose the Right Metal Roof Tile Roll Former
Here are key factors to consider when selecting a metal roof tile roll forming system:
Criteria | Description |
---|---|
Capacity | Match production volume needs |
Coil Width | Suitable for required sheet widths |
Metal Thickness | Accepts desired material thickness |
Profile Range | Forms needed roofing profiles |
Speed | Adequate output rate |
Adjustability | Allows changes in parameters |
Controls | Automated operation capability |
Frame Rigidity | Withstands high forming forces |
Service Support | Installation help, maintenance access |
Budget | Overall costs and value |
- Analyze business’ production requirements and growth
- Shortlist models from reputable manufacturers that fulfill needs
- Select robust and flexible machine that meets quality standards
- Ensure adequate after-sales support from supplier
- Compare pricing and total cost of ownership from alternatives
Choosing the right specification and capacity roll former results in better ROI and productivity.
Pros and Cons of Metal Roof Tile Roll Forming Machines
Some key advantages and limitations of metal roofing tile roll forming machines include:
Pros | Cons |
---|---|
Fast production of long sheets | Limited to roll-formed profiles |
Ideal for metal roofing in high volumes | Lower flexibility compared to press brakes |
Consistent quality across large batches | Restricted by maximum coil width capacity |
Interchangeable roll sets for profile changes | Significant initial capital investment |
Compact compared to spot welding lines | Requires skilled adjustment and operation |
Lower costs than alternate fabrication | Complex maintenance with many components |
Main Benefits
- Continuous high speed forming from coils increases output
- Uniform profile and quality along sheet length
- Flexible production with quick roll set changeover
- Compact footprint compared to cut-and-bend methods
Limitations
- Only produces set profiles, limited custom shapes
- Higher maintenance needs than simpler machines
- Significant capital cost for heavy duty production
For most roofing manufacturers, the productivity benefits of roll forming lines outweigh the limitations.
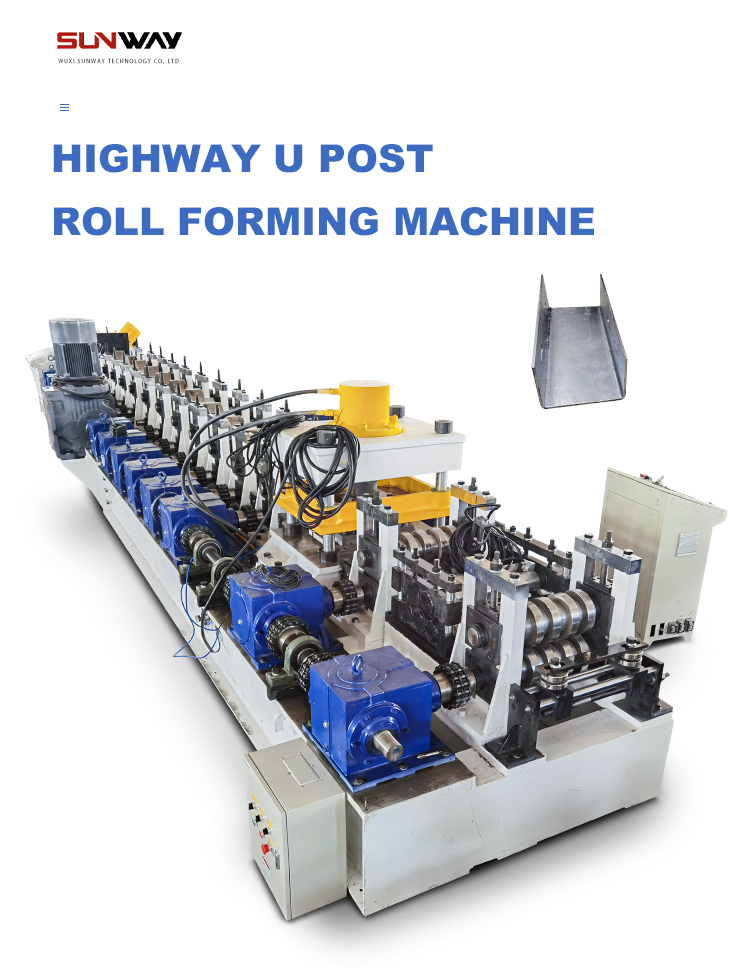
FAQ
Question | Answer |
---|---|
What profiles can be produced? | Common profiles include standing seam, corrugated, shake tile. Custom profiles are also possible. |
What metals can be formed? | Carbon steel, galvanized steel, aluminum and stainless steel coils. |
How to adjust the machine? | Main parameters like profiles, speeds, feeds are set in the PLC controls. Mechanical alignment done with gauges. |
What thickness range is possible? | Standard machines accept 0.3 – 1.2 mm thickness material. |
How long are the formed sheets? | Length determined by cut-off knives from 0.5 – 5 meters. |
What maintenance is required? | Schedule lubrication, inspect/replace wear items, calibrate sensors and monitors. |
This covers the basics of metal roof tile roll forming machine capabilities, features and operation. Contact manufacturers directly for machinery quotations and further details.
Conclusion
Metal roof tile roll forming machines allow fast production of various roofing components like shingles, panels and drainage products. These versatile roll formers transform flat sheet metal coils into complete roofing tiles through a series of bending and shaping rollers.
Key factors in selecting suitable metal roofing roll formers include required capacity, coil width, metal thickness range, roofing profiles, and forming speeds. Leading manufacturers offer machines from compact light-duty to heavy-duty production scales.
Proper installation, controls configuration, operation and preventive maintenance is necessary to achieve high productivity and roofing quality. Roll formed metal roofing provides durability, design flexibility and economical fabrication.