A metal curving unistrut roll forming machine is an industrial equipment used to continuously bend and form metal coil strips into customized channel beam profiles with curved shapes. Unistrut, also known as channel strut, is a hot-rolled, mill finish plain channel used in construction for its versatile structural support capabilities.
Roll forming utilizes a series of consecutive roller dies to gradually shape sheet metal coil into structural profiles with high dimensional accuracy and consistency at a rapid production rate. Metal curving unistrut roll forming machines allow manufacturers to create lightweight, high strength curved metal support channels on demand as per application requirements.
Metal Curving Unistrut Roll Forming Machine Types
Machine Type | Description |
---|---|
C Profile | Forms standardized C-channel sections with radiused returns |
U Profile | Forms industry standard U-channel sections with tighter radii |
Custom Profile | Creates non-standard channel profiles as per custom design |
Variable Section | Roll forms channels with varying widths and depths |
Curved Profile | Imparts continuous curvature along the channel length |
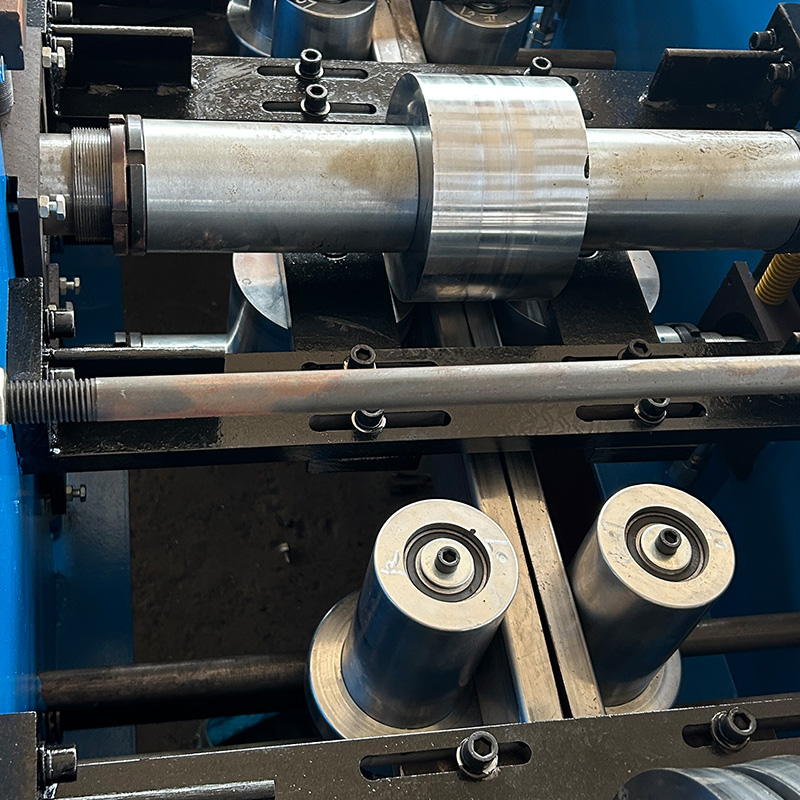
Working Principle of Metal Curving Unistrut Roll Forming
The working principle involves unwinding metal coil strip, feeding into a series of roller dies to gradually bend the strip, finally cutting into desired lengths:
- Coiled steel sheet is loaded onto a decoiler which straightens and feeds the strip through the infeed guides
- The strip passes through a series of roller dies each with custom profile engraved. Dies shape the strip incrementally.
- Pinch rollers grip and transport the strip through the consecutive dies at a set speed
- Profiled strip moves through the post-cutting section with specific punch and die to shear cut as per length
- Formed channels with curved profile are moved out on the exit conveyor/rollers
- Advanced machines allow online drilling and other secondary processing
Key Aspects of Metal Curving Unistrut Roll Forming Process
Parameter | Details |
---|---|
Material Feeding | Decoiler capacity, strip width, thickness, compatibility with metal grade |
Profile Forming | Number of roller stations, profile dimensional accuracy, surface finish |
Profile Design | Channel dimensions, radii, holes, curvature ability |
Cutting | Shearing length accuracy, blade sharpness, scrap handling |
Customization | Profile variability, secondary processing, production batch size |
Suppliers of Metal Curving Unistrut Roll Forming Machines
Supplier | Location | Price Range |
---|---|---|
ECeRoll | Italy | $150,000 to $650,000 |
Formtek | USA | $200,000 to $900,000 |
SDMC | China | $120,000 to $500,000 |
DAGH | India | $100,000 to $400,000 |
-
Highway Guardrail End Terminal Forming Machine
-
Highway U/C Post Roll Forming Machine
-
2 Waves Highway Guardrail Roll Forming Machine
-
3 Waves Highway Guardrail Roll Forming Machine
-
Two waves highway guardrail machine
-
Three waves highway guardrail machine
-
Steel Coil Cut To Length Line Machine
-
Steel Coil Cut To Length Line Machine
-
Steel Coil Cut To Length Line Machine
Installation, Operation and Maintenance
Activity | Description |
---|---|
Installation | Leveling, alignment, trial runs without load, electricals by supplier engineers |
Operation | Parameter settings,decoiler loading, profile quality checks, safety procedures |
Maintenance | Schedule lubrication, inspect wear items, blade sharpening every 6 months |
How to Choose a Reliable Metal Curving Roll Forming Machine Supplier
Consideration | Details |
---|---|
Experience | Years in business, number of machines supplied |
Clientele | Reputed customer brands already supplied to |
Customization | Range of profile variability offered |
Quality | Certifications like ISO 9001, consistency of output |
Service Support | Responsiveness for technical queries, spare part availability |
Budget | Total cost aligning with production objectives |
Pros and Cons of Metal Curving Unistrut Roll Forming Machines
Advantages
- High production rate up to 80 m/min
- Consistent and accurate channel dimensions
- Imparts robust structural curve shape
- Reduced labor cost compared to other bending methods
- Allows custom channel profile design flexibility
- Automated mass production improves efficiency
Limitations
- High initial capital investment requirement
- Regular maintenance requirement for quality output
- Limited thickness and width capacity per machine
- Secondary operations may still be required
Application Areas for Curved Metal Unistrut Channels
Sector | Application Example |
---|---|
Construction | Decorative roofing structures, curved handrails |
Infrastructure | Unique highway crash barriers, flyover supports |
Architecture | Sculptural building facades, amphitheater framing |
Automotive | Custom truck/bus chassis, curved conveyor framing |
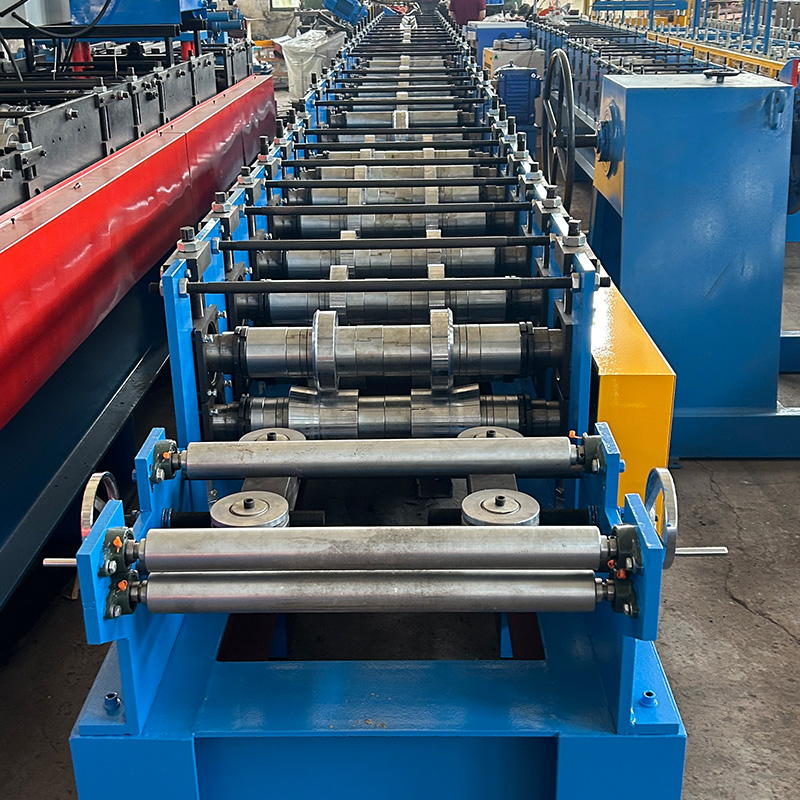
Frequently Asked Questions
Q: What sheet metal thickness can be roll formed into curved unistrut?
A: Standard machines handle metal thickness from 0.5 mm to 3 mm for curved channels. Heavy duty machines available for 5 mm thickness capacity.
Q: What is the ideal unistrut size for curved profile?
A: 50 mm x 30 mm, 80 mm x 40 mm, 100 mm x 50 mm are common rolled channel sizes for curved structural sections. Custom sizes possible.
Q: What degree of curvature can be achieved in roll formed channels?
A: Up to 120 degree continuous curvature along 10 m length is possible. Maximum bend radius ratio ~1 is standard for structural channels.
Q: How to design custom curved unistrut profile and tooling?
A: Share CAD models of desired profile shape with machine manufacturer. Their design team engineers suitable roller dies and tooling.
Q: What factors affect price of these roll forming machines?
A: Type of customized features, production speed, raw material width/gauge capacity, overall stiffening levels and length, secondary processing needs.
Q: How much area is needed to install a curved C channel roll former?
A: Approximately 36 feet x 10 feet for machine (feed to exit conveyors) plus decoiler, shear and space for formed products.