Glazed tile roll forming machines are specialized equipment used to produce glazed ceramic tiles in a continuous automated process. This equipment revolutionized tile manufacturing, enabling mass production of tiles with consistent quality and high output volumes.
This guide provides a detailed overview of glazed tile roll forming machines, their working, types, parts, specifications, applications, advantages and more.
How Glazed Tile Roll Forming Machines Work
Glazed tile roll forming machines create glazed ceramic tiles through an automated and continuous production process. Here are the key steps:
Raw Material Preparation
The raw materials – clay, feldspar, kaolin, quartz etc. are blended as per the tile composition requirements and ground to fine powder. Water is added to obtain a homogeneous ceramic slurry.
Pressing
The ceramic slurry is fed into the roll forming machine where it is extruded between an upper and lower roller die continuously as a flat strip. The die surface impressions shape and cut the strip into individual tile blanks.
Drying
The freshly formed wet tile strips are conveyed through dryers at 150-200°C to remove moisture evenly.
Glazing
The dried tiles move to glazing where a coat of glaze slurry is applied on the top surface. The glaze provides the glossy impervious decorative finish after firing.
Firing
Tiles pass through the kiln at temperatures of 1000-1200°C to permanently harden the body and fuse the glaze layer.
Sorting and Packing
Finally, the fired tiles are sorted, inspected for defects and packed for dispatch or storage.
This continuous sequence enables high volumes of tiles to be manufactured at fast production rates.
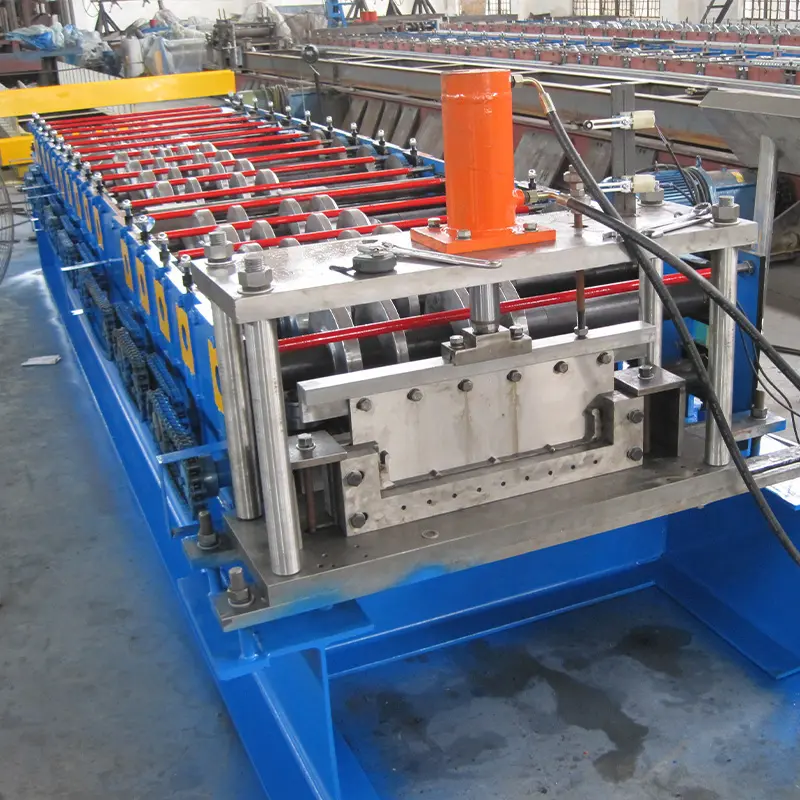
Types of Glazed Tile Roll Forming Machines
Glazed tile roll forming machines can be categorized based on design and capabilities:
Type | Description |
---|---|
Single-layer | Produces tiles of one uniform thickness, typically 6-10mm |
Double-layer | Can produce two layers simultaneously with different thicknesses |
Multi-color | Capable of applying more than one colored glaze to create decorative effects |
Pressing + Glazing | Integrated design that directly glazes the wet tile strip after pressing |
Specialized variants like mesh-mounted tile presses are also available for making thin tiles down to 3mm thickness.
Main Parts and Components
Glazed tile roll forming machines comprise multiple sections for the various production steps. The key parts and their functions are:
Part | Description |
---|---|
Mixing unit | Blends the ceramic raw materials into homogeneous slurry |
Rollers | Extract the slurry and press it into the die shape to form the tiles |
Die | Contains impressions that shape the tile body and surface |
Belt conveyors | Transport the tile strips between processes |
Dryers | Remove moisture from the formed tiles before glazing |
Glazing unit | Applies a coating of glaze slurry on the tile surface |
Kiln | Hardens and fires the tiles at high temperature |
Sorting unit | Checks tiles for defects and sorts by size/type |
Packing system | Packs sorted tiles into boxes for storage or transport |
Control system | Automates and monitors the machine parameters |
Auxiliary units like tile edge cutting and surface polishing can also be integrated.
Specifications and Design Parameters
Glazed tile roll forming machines are designed and built to customer requirements based on production needs. Here are some key specifications and design considerations:
Parameter | Details |
---|---|
Production capacity | 10,000 – 40,000 tiles/hour or more |
Tile sizes | Standard 200x200mm to 1000x1000mm; Custom sizes possible |
Tile thickness | Single layer: 6-12mm Double layer: 4-8mm + 8-12mm |
Roller size | Diameter up to 1200mm; Width 1000-2500mm or more |
Roller pressure | Up to 300 tons by hydraulic cylinders |
Dryer length | 8-12m multi-zone dryers |
Kiln size | Length 25-100m; Capacity 10-100 ton/day |
Conveyor belts | Heat, abrasion and corrosion resistant |
Machine width | 5-8m typical |
Machine length | 15m for basic; Up to 150m for integrated line |
Control system | PLC based; HMI touchscreen; SCADA |
Electrical load | 50-750 kW connected load |
The machine configuration and capabilities can be customized as per the end product mix and plant requirements.
Applications and Tile Types Produced
Glazed tile roll forming machines are extremely versatile. They can produce all varieties of ceramic wall and floor tiles:
Application | Tile Types |
---|---|
Wall Tiles | Glossy, matte finish, digital printed, rustic, textured surfaces |
Floor Tiles | Rustic, matt finish, exterior, abrasion resistant |
Border Tiles | Decorative borders, accents, moldings |
Granite-look | Tiles that simulate natural stone and granites |
Double layer presses can make both thinner and thicker tiles for walls and floors respectively.
Benefits and Advantages
Glazed tile roll forming machine offer significant benefits over traditional processes:
Parameter | Benefit |
---|---|
Fully automated | Less manual labor, consistent quality |
High production rates | Up to 40,000 tiles/hour. Lower costs |
Continuous operation | Higher output and productivity |
Flexible production | Multiple sizes and types possible |
Lower maintenance | Compared to hydraulic or ram presses |
Compact size | Smaller footprint than conventional processes |
Lower energy use | Efficient dryers and kilns available |
These advantages have made roll forming the dominant manufacturing process for high volume tile production lines.
Suppliers and Pricing
There are many equipment manufacturers across China, Europe and India that supply glazed tile roll forming machines. Here are some indicative price ranges:
Machine Output | Price Range |
---|---|
10,000 tiles/hour | $200,000 to $300,000 |
20,000 tiles/hour | $500,000 to $800,000 |
40,000 tiles/hour | $1 million to $1.5 million |
Prices vary based on the level of automation, customization and optional accessories chosen. Second hand and refurbished machines are also available at 30-40% lower cost.
Some leading glazed tile roll forming machine manufacturers include:
- KEDA (China)
- SACMI (Italy)
- Eirich (Germany)
- SITI B&T Group (Italy)
- Tosilab (Spain)
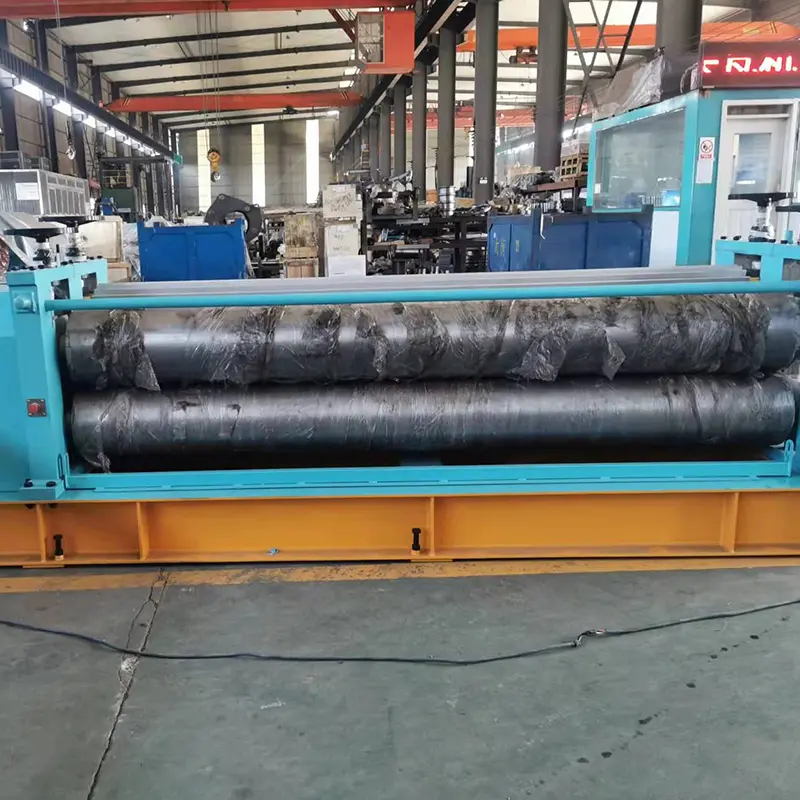
How to Choose a Reliable Manufacturer?
Here are tips on selecting a good glazed tile roll forming machine supplier:
Parameter | Recommendation |
---|---|
Technology | Look for suppliers with in-house R&D for latest designs |
Experience | More experienced companies offer better support |
Production facilities | Visit their factory to assess production capability |
Tile trials | Ask for test samples of tiles made by their machine |
Customization | See if they offer customized solutions for your needs |
After-sales service | Check response time, service network etc. |
Clientele | Established suppliers have reputed tile maker clients |
Cost | Get quotes from multiple vendors for best price |
Choose a technologically capable manufacturer who can deliver high performance, durable machines with good after-sales support.
Installation and Commissioning
Installing a glazed tile roll forming machine requires careful planning and preparation:
- Adequate space is needed for the entire production line and material movement.
- Strong foundations are required to hold the machines weighing hundreds of tons.
- Electrical, water and drainage connections must be provided.
- The machine is assembled in sections which need proper alignment.
- Mechanical and electrical installation is followed by trial runs and testing.
- Raw materials processing units must be operational before starting the tile pressing.
- Staff training for operation and maintenance is essential.
With systematic installation and testing, the machine can be commissioned smoothly. Manufacturers provide engineers to supervise the process.
Operation and Maintenance
To achieve optimal performance from glazed tile roll forming machines:
- Follow the manufacturer’s instructions for operation and safety.
- Keep the dies, rollers and other parts clean to avoid tile defects.
- Use heat resistant belt lubricants to minimize wear.
- Inspect rollers, bearings, belts and hydraulics regularly.
- Monitor process parameters like pressure, speed, temperature.
- Schedule preventive maintenance during plant shutdowns.
- Replace worn out spares like seals, belts, rollers periodically.
Proper operation and maintenance minimizes downtime and maximizes production.
Advantages of Glazed Tile Roll Forming Machines
Glazed tile roll forming machines offer the following key advantages compared to traditional tile making processes:
- Fully automated – Requires less manual labor leading to consistent product quality and minimal human errors.
- High productivity – Capable of outputs up to 40,000 tiles per hour through continuous operation, reducing manufacturing costs.
- Flexibility – Able to make wide range of tile sizes and designs with quick die changeovers. Enables diversified product portfolio.
- Compact size – Footprint is 50-70% smaller compared to conventional tile making methods, saving space.
- Energy efficiency – Advanced dryers and kilns available that optimize heat usage and minimize power consumption.
- Lower maintenance – Simpler system with less moving parts than hydraulic presses. Easier to maintain with infrequent downtimes.
- Customization – Machines can be tailored to customer needs in terms of automation features, line integration, optional accessories etc.
These valuable advantages have made glazed tile roll forming the most popular manufacturing process among leading tile makers worldwide.
Limitations of Glazed Tile Roll Forming Machines
Despite many benefits, glazed tile roll forming machines also have certain limitations:
- High initial capital investment required. Major tile manufacturers prefer to buy, while smaller players prefer conventional machines.
- Design complexity makes manufacturing dependent on availability of high-precision metalworking facilities. Local production in developing markets can be a challenge.
- Limited ability to make specialized tiles like concert, terrazzo or highly textured designs. Alternative processes may be better suited.
- Thickness is restricted to around 6mm for floor tiles and 12mm for wall tiles on a single layer press.
- Not ideal for producing tiles in small batches for custom applications. Conventional or digital printing may be preferred.
- Lack of trained personnel and after-sales support in some regions can hamper adoption.
- Requires significant manual batching and glazing work for certain textured or decorative tiles.
Keeping these limitations in mind, glazed tile roll forming remains the premier solution for medium to high volume tile manufacturing for regular formats and designs.
Glazed Tile Roll Forming Vs Wet Powder Compaction
Glazed tile roll forming and wet powder compaction are two competitive automated technologies for ceramic tile production. How do they compare?
Parameter | Glazed Tile Roll Forming | Wet Powder Compaction |
---|---|---|
Pressing method | Extrusion between rollers | Compaction by vibration and pressure |
Production rate | Up to 40,000 tiles/hour | Up to 33,000 tiles/hour |
Thickness range | 4mm to 12mm | 3mm to 12mm |
Size flexibility | Limited for very large or small tiles | Higher flexibility in sizes |
Process complexity | Slightly lower | More complex material preparation |
Investment cost | Lower by 15-20% | Higher |
Running cost | Lower energy usage | Slightly higher energy |
Product consistency | Very high | High |
Type of tiles | All standard formats | Lower suitability for specialized tiles |
Glazed tile roll forming scores in terms of higher throughput, lower cost and flexibility for regular tiles formats. Wet powder compaction offers ability to go thinner and make some special sizes. For most applications, roll forming is preferred, but powder compaction is a good alternative.
Glazed Tile Roll Forming Vs Dry Powder Pressing
Here is a comparison between glazed tile roll forming and conventional dry powder pressing:
Parameter | Glazed Tile Roll Forming | Dry Powder Pressing |
---|---|---|
Process | Automated continuous | Batch type press cycles |
Production rate | Much higher upto 40,000/hour | Lower around 15,000/hour |
Labor | Lower since automated | Higher labor for pressing and handling |
Power usage | More efficient dryers and kilns | Higher power consumption |
Maintenance | Lower with fewer moving parts | Higher on hydraulic components |
Size flexibility | Limited for very large or small tiles | Higher flexibility in sizes |
Product consistency | Extremely high | Moderate, depends on manual supervision |
Cost | Higher capital investment | Lower capital cost |
Running cost | Lower due to higher throughput | Higher due to lower productivity |
Glazed tile roll forming offers superior productivity, efficiency, consistency and capability for mass tile production. Dry powder pressing is suitable for smaller batch volumes or specialized tiles.
Glazed Tile Roll Forming Vs Ram Extrusion
Glazed tile roll forming machines and ram extruders are the most common machine choices for glazed wall tile production.
Parameter | Glazed Tile Roll Forming | Ram Extrusion |
---|---|---|
Pressing method | Rollers | Hydraulic ram |
Production rate | Higher upto 40,000 tiles/hour | Lower around 25,000 tiles/hour |
Tile thickness | 4mm to 12mm | 7mm to 12mm |
Size range | Limited for very large or small tiles | Wider range of tile sizes |
Maintenance | Lower on rollers | Higher on hydraulic components |
Power consumption | More optimized | Higher due to friction losses |
Product consistency | Extremely high | Moderate, depends on supervision |
Automation | Higher degree of automation | Lower automation levels |
Cost | Higher capital cost | Lower capital cost |
Glazed tile roll forming is superior in output, efficiency, automation and product consistency. Ram extrusion tiles lines have lower investment costs but require more supervision.
Conclusion
Glazed tile roll forming machines deliver high productivity, superb quality consistency and design flexibility at optimized costs. The automated process allows tile manufacturers to produce large volumes cost-effectively with minimal manual intervention. Although the initial investment is higher, the advantages of much greater throughput and lower operating expenses make glazed tile roll forming the ideal choice for large scale tile production. Leading tile makers around the world have adopted this technology for their core manufacturing needs. With continual advances and new developments, glazed tile roll forming machines will consolidate their dominance as the premier manufacturing process for the global ceramic tile industry.
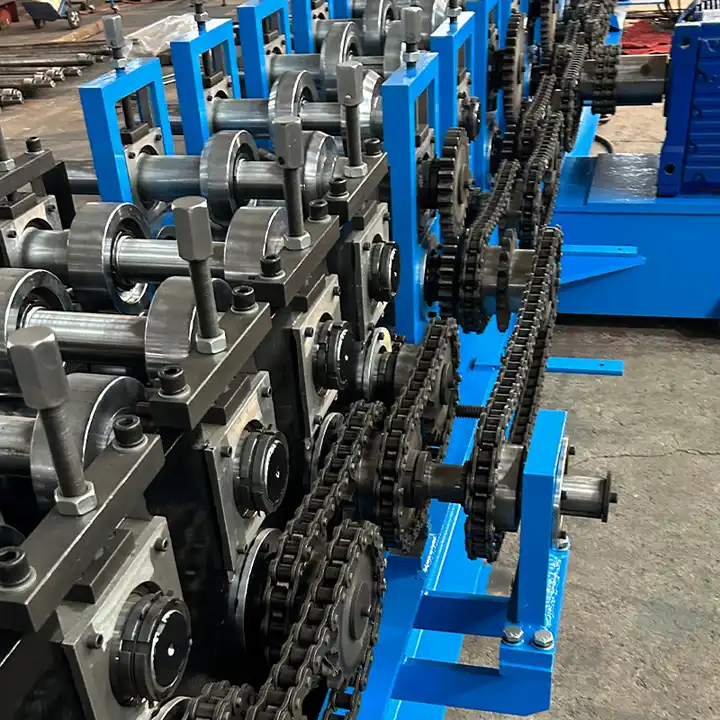
FAQs
Q: What is the typical production capacity of glazed tile roll forming machines?
A: Standard production capacity ranges from 10,000 to 40,000 tiles per hour. Higher custom capacity machines are also available.
Q: What tile sizes can be made on these machines?
A: Common tile dimensions from 200x200mm up to 1000x1000mm can be produced. Custom sizes are also possible.
Q: What types of tiles can be made?
A: All kinds of wall tiles and floor tiles with glossy, matte, textured, rustic, stone-look and other finishes can be manufactured.
Q: How to choose between single layer and double layer tile presses?
A: Single layer is suitable for most tile thicknesses from 6-12mm. Double layer allows combining thinner and thicker tiles on the same machine.
Q: How are different tile colors and patterns achieved?
A: Multi-color glazing, digital printing and customized die shapes enable a range of decorative designs.
Q: How to reduce power consumption in glazed tile roll forming?
A: Using energy-efficient dryers and kilns is key. Heat recovery systems can also minimize energy usage.
Q: What is the service life of these machines?
A: With proper maintenance, the machinery will last over 15-20 years. Key parts like rollers may need replacement over time.
Q: What factors affect the price of glazed tile roll forming machines?
A: Production capacity, automation features, customization, line integration and optional accessories impact the pricing.
Q: How much floor space is needed to install a tile roll forming machine?
A: Approximately 600-1000 sq.m is required for a basic machine with ancillaries. More for integrated lines.
Q: What skills are needed to operate glazed tile roll forming machines?
A: Machine operators need basic technical skills. Process engineers oversee the production quality and parameters.
Q: How is glazed tile roll forming better than powder compaction?
A: It offers higher throughput, lower cost, and greater consistency in product quality for regular tile formats.
Q: What are the limitations of glazed tile roll forming machines?
A: High investment cost, less suitability for specialized tiles, restrictions on tile sizes, and availability of skilled resources.