Width corrugated sheet roll forming machines are an essential tool in modern manufacturing, used to produce corrugated sheets of different widths, lengths, and thicknesses for a wide range of applications. These machines can work with various materials, such as steel, aluminum, or copper, and are designed to produce high-quality corrugated sheets at a continuous and high-speed rate. However, with so many different machines available on the market, it can be challenging to know what features to look for when choosing the right one for your business. In this post, we will discuss the top features to look for in a width corrugated sheet roll forming machine, including high-speed production, customization and flexibility, precision and accuracy, durability and reliability. By understanding these features, businesses can make an informed decision and select a machine that meets their specific needs and requirements.
High-speed production of width corrugated sheet roll forming machine
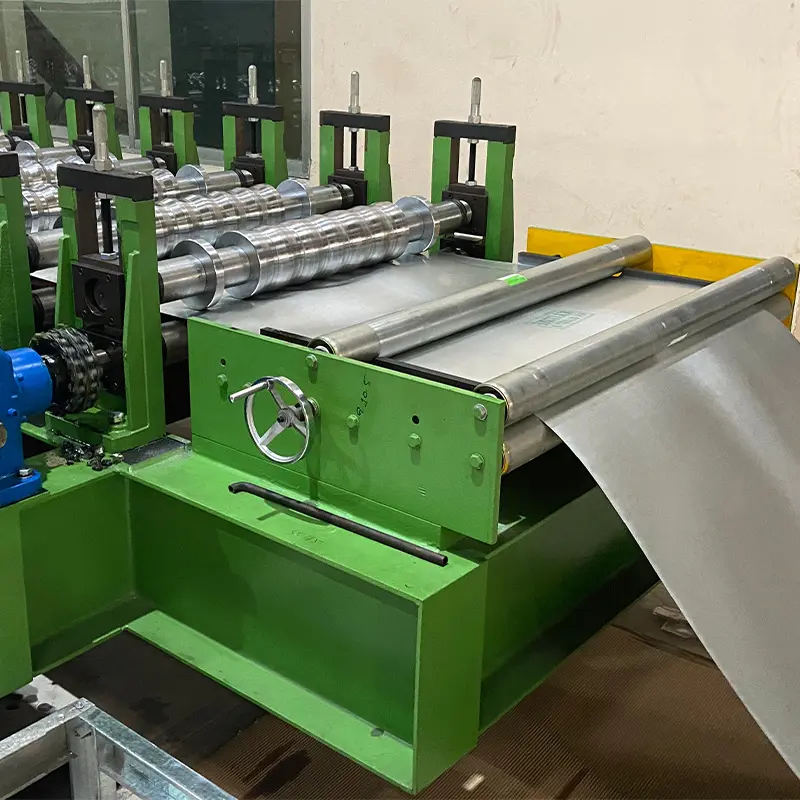
High-speed production is a critical feature to consider when choosing a width corrugated sheet roll forming machine. These machines are designed to produce corrugated sheets at a rapid and continuous rate, enabling businesses to increase their overall production efficiency and output. Here are some key factors to look for when assessing a machine’s high-speed production capabilities:
- Number of forming stations: The number of forming stations on a width corrugated sheet roll forming machine is directly related to its production speed. Machines with a higher number of forming stations can produce corrugated sheets faster than those with fewer stations.
- Tooling changeover time: The time it takes to change the machine’s tooling is a critical factor in its high-speed production capabilities. Machines with fast tooling changeover times can switch between different widths, lengths, and thicknesses of corrugated sheets quickly, minimizing downtime and increasing production efficiency.
- Automated controls: Automated controls that monitor the production process in real-time can also significantly impact a machine’s high-speed production capabilities. Machines with sensors and automated controls can detect any issues or deviations in the material and make the necessary adjustments to ensure a smooth and continuous operation.
- Material feed system: The material feed system is another critical factor in a machine’s high-speed production capabilities. Look for machines with a smooth and continuous material feed system that can deliver the material to the forming stations at a consistent rate, ensuring a constant flow of corrugated sheets.
Customization and flexibility of width corrugated sheet roll forming machine
-
Vineyard Post Roll Forming Machine
-
Auto Size Changeable Sigma Purlin Roll Forming Machine
-
PV Mounting Bracket C Shape Profile Roll Forming Machine
-
C Z Purlin Channel Cold Roll Forming Machine Full Auto Galvanized Steel Profile
-
PV Mounting Bracket Roll Forming Machine (HAT / Omega Profile)
-
PV Mounting Bracket Z Shape Profile Roll Forming Machine
Customization and flexibility are essential features to look for when choosing a width corrugated sheet roll forming machine. Businesses need to be able to produce corrugated sheets of different widths, lengths, and thicknesses, with customizable profiles and shapes, to meet the specific needs and requirements of their customers. Here are some key factors to consider when assessing a machine’s customization and flexibility capabilities:
- Adjustable rollers and dies: Machines with adjustable rollers and dies offer more flexibility in the manufacturing process, allowing businesses to produce corrugated sheets of different sizes and shapes. These machines can be customized and adjusted to meet the specific needs and requirements of the customer, providing a competitive edge in the market.
- Material compatibility: It’s essential to choose a machine that can work with a wide range of materials, such as steel, aluminum, or copper, to offer maximum flexibility to businesses. This compatibility allows businesses to adapt to changing market demands and offer customized solutions to their customers.
- Multiple profiles and shapes: Machines that can produce multiple profiles and shapes offer more versatility in the manufacturing process, allowing businesses to produce corrugated sheets for various applications and industries. These machines can be customized and adjusted to produce corrugated sheets with different profiles, such as sinusoidal or trapezoidal, and different shapes, such as round or square.
- Computer-controlled operation: Machines with computer-controlled operation can also offer more customization and flexibility in the manufacturing process. These machines can be programmed to produce corrugated sheets of different sizes and shapes, with specific patterns or designs, offering businesses the ability to produce unique and customized products.
Precision and accuracy of width corrugated sheet roll forming machine
Precision and accuracy are critical features to consider when choosing a width corrugated sheet roll forming machine. These machines should be able to produce corrugated sheets with a consistent shape, dimension, and quality throughout the production process. Here are some key factors to consider when assessing a machine’s precision and accuracy capabilities:
- Accurate sensors and controls: Machines with accurate sensors and controls can detect any deviations or defects in the material and make the necessary adjustments to ensure a smooth and consistent operation. These sensors and controls can detect any material irregularities, such as thickness variations, and adjust the machine’s rollers and dies to ensure a consistent corrugated sheet’s shape and dimension.
- Precise alignment: The machine’s alignment is critical in ensuring the precision and accuracy of the corrugated sheets produced. Look for machines with precise alignment mechanisms that can ensure the material is centered and correctly positioned throughout the production process.
- Quality assurance systems: Quality assurance systems can also significantly impact a machine’s precision and accuracy capabilities. Machines with quality assurance systems can detect any defects or inconsistencies in the material and either remove the affected material or make the necessary adjustments to the production process.
- High-quality components: The quality of the machine’s components can also affect its precision and accuracy capabilities. Look for machines with high-quality components, such as bearings, gears, and motors, that can withstand the rigors of the manufacturing process and maintain their precision and accuracy over time.
Durability and reliability of Width corrugated sheet roll forming machine
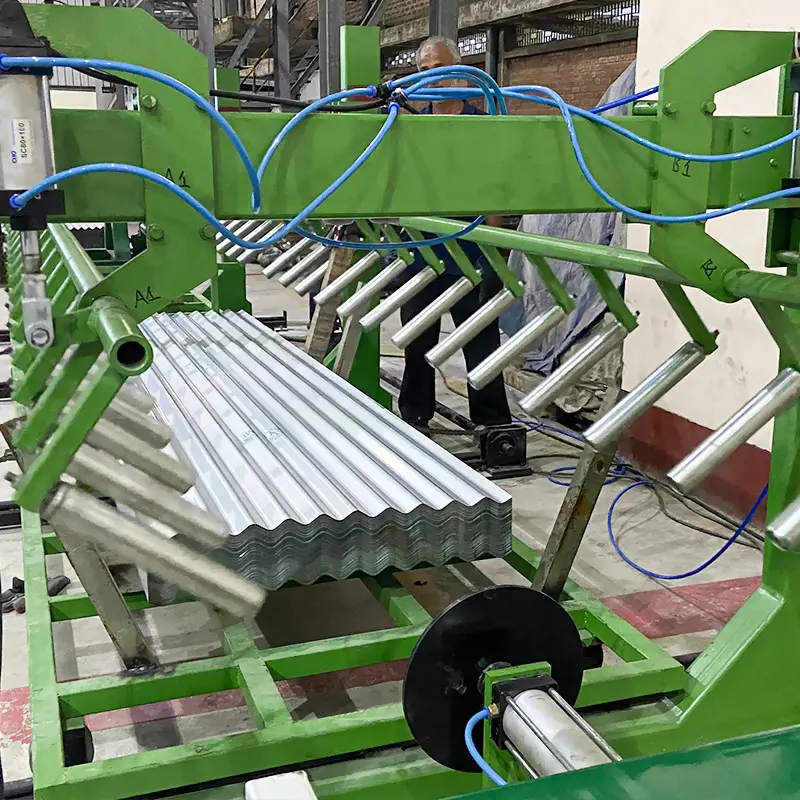

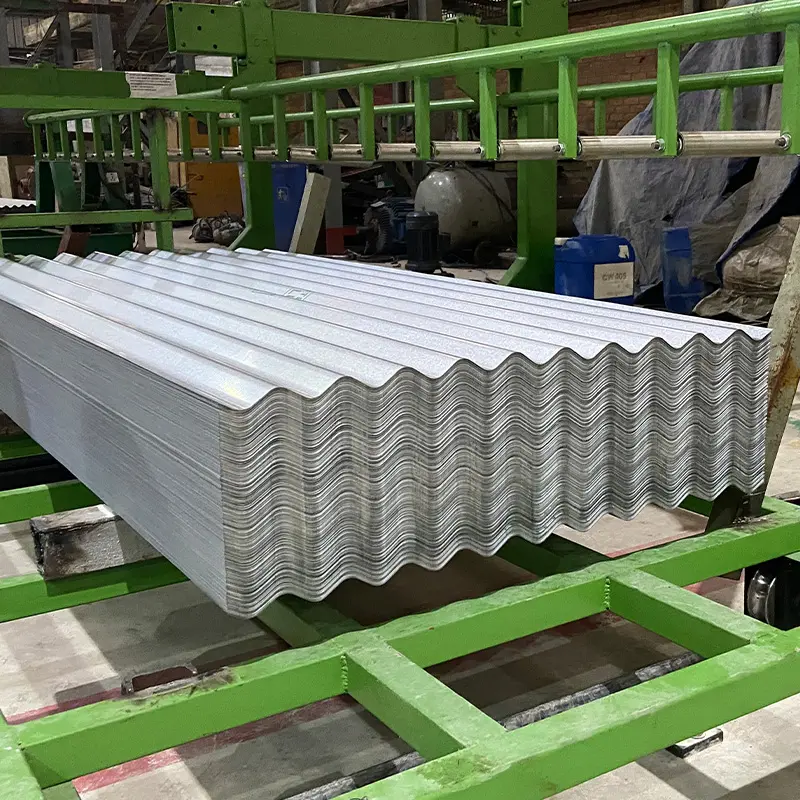
Durability and reliability are crucial features to consider when selecting a width corrugated sheet roll forming machine. These machines are a significant investment for businesses, and it’s essential to choose a machine that can withstand the rigors of the manufacturing process and provide a long-term return on investment. Here are some key factors to consider when assessing a machine’s durability and reliability:
- High-quality materials: The machine’s construction materials are critical in determining its durability and reliability. Look for machines made of high-quality materials, such as steel or aluminum, that can withstand the wear and tear of the manufacturing process.
- Robust components: The quality of the machine’s components is also critical in ensuring its durability and reliability. Look for machines with robust components, such as bearings, gears, and motors, that can handle the stresses and strains of the production process and maintain their performance over time.
- Low maintenance requirements: Machines with a low maintenance requirement can save businesses time and money in the long run. Look for machines with simple and easy-to-maintain components that can be quickly repaired or replaced, minimizing downtime and ensuring a consistent production process.
- High level of uptime: The machine’s uptime is critical in ensuring its reliability and productivity. Look for machines with a high level of uptime, which means they can operate for extended periods without breakdowns or interruptions, reducing production delays and increasing efficiency.
In conclusion, when selecting a width corrugated sheet roll forming machine, it’s essential to consider the features that will best meet the needs and requirements of your business. High-speed production, customization and flexibility, precision and accuracy, durability and reliability, and safety features are all critical features to look for in a quality machine. By choosing a machine with these features, businesses can increase their production efficiency, improve the quality of their products, and ensure a safe and reliable operation. Investing in a width corrugated sheet roll forming machine that meets your business’s specific needs and requirements can provide a long-term return on investment and improve your competitiveness in the market.