Automation has been a game-changer in the manufacturing industry, transforming the way companies produce goods and increasing their overall efficiency. One area where automation has had a significant impact is in the width corrugated sheet roll forming machine industry. By automating their production processes, manufacturers of width corrugated sheet profiles can streamline their operations, increase their output, and reduce labor costs. In this post, we’ll explore the advantages of automating your width corrugated sheet roll forming machine, the different types of automation available, the implementation process.
What is Automation of width corrugated sheet roll forming machine?
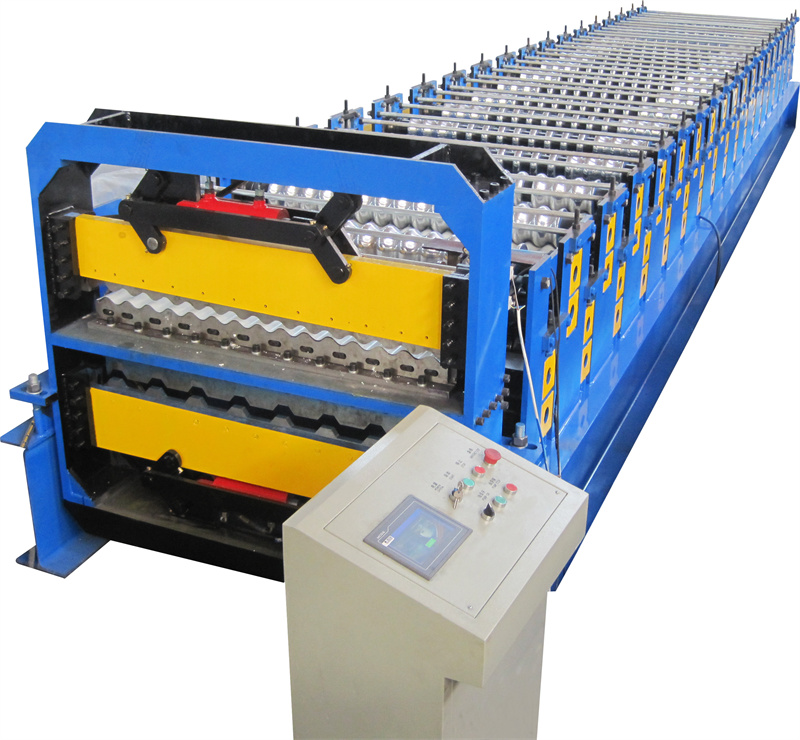
Automation refers to the use of advanced technology to perform tasks that were previously carried out by humans. In the context of width corrugated sheet roll forming machines, automation involves the use of computer-controlled systems to perform tasks such as feeding raw materials, guiding the sheet through the rollers, cutting the finished product, and more.
Automation in width corrugated sheet roll forming machines typically involves the use of sensors, programmable logic controllers (PLCs), and other advanced technologies that allow for precise control of the production process. These technologies can help to improve the accuracy and consistency of the final product, as well as increase the speed and efficiency of the production process.
For example, an automated feeding system can be programmed to precisely measure and feed raw materials into the machine, ensuring that the material is properly aligned and fed at the correct rate. Automated cutting systems can be programmed to cut the finished product to precise specifications, reducing waste and improving accuracy. Overall, automation in width corrugated sheet roll forming machines helps to streamline the production process and reduce the need for human intervention, resulting in greater efficiency and productivity.
Benefits of automating width corrugated sheet roll forming machine
-
Electrical Cabinet Frame Roll Forming Machine
-
Din Rail Roll Forming Machine
-
Cable Ladder Roll Forming Machine
-
PV Mounting Bracket C Shape Profile Roll Forming Machine
-
Cable Tray Roll Forming Machine
-
PV Mounting Bracket Roll Forming Machine (HAT / Omega Profile)
-
PV Mounting Bracket Z Shape Profile Roll Forming Machine
-
Solar mounting strut channel roll forming machine
-
Strut Channel Roll Forming Machine
There are several benefits to automating your width corrugated sheet roll forming machine. Here are some of the key advantages:
- Increased Productivity: Automation can significantly increase the speed and output of your production process. With automation, machines can run 24/7, producing more corrugated sheet profiles in a shorter amount of time. This results in greater productivity and increased revenue.
- Reduced Labor Costs: By automating your production process, you can reduce your labor costs by minimizing the number of workers required to operate the machine. This can help to lower your overhead costs and increase your profitability.
- Improved Accuracy and Consistency: Automation allows for greater precision and consistency in the production process, resulting in fewer errors and defects in the final product. This leads to higher-quality corrugated sheet profiles that meet the exact specifications of your customers.
- Reduced Waste: With automated systems, raw materials can be used more efficiently, reducing waste and increasing the overall yield of the production process. This can result in cost savings and a more sustainable manufacturing process.
- Increased Safety: Automation can help to improve safety in the workplace by minimizing the need for human intervention in potentially hazardous processes. This can help to reduce the risk of workplace injuries and create a safer working environment for employees.
In summary, automating your width corrugated sheet roll forming machine can lead to increased productivity, reduced labor costs, improved accuracy and consistency in the final product, reduced waste, and increased safety in the workplace. These benefits can help to improve your bottom line and position your business for long-term success.
Types of Automation that can be applied to width corrugated sheet roll forming machines
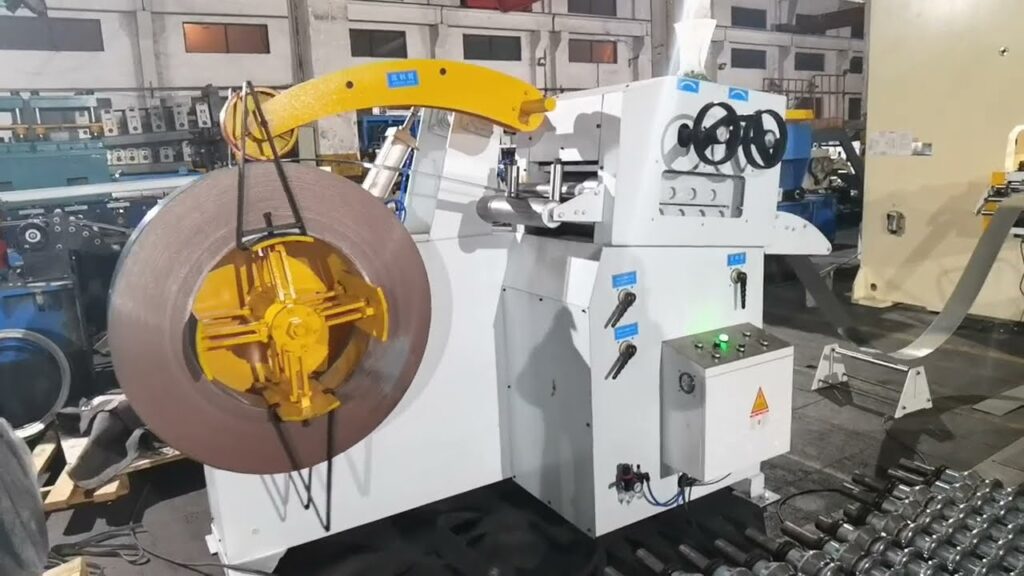
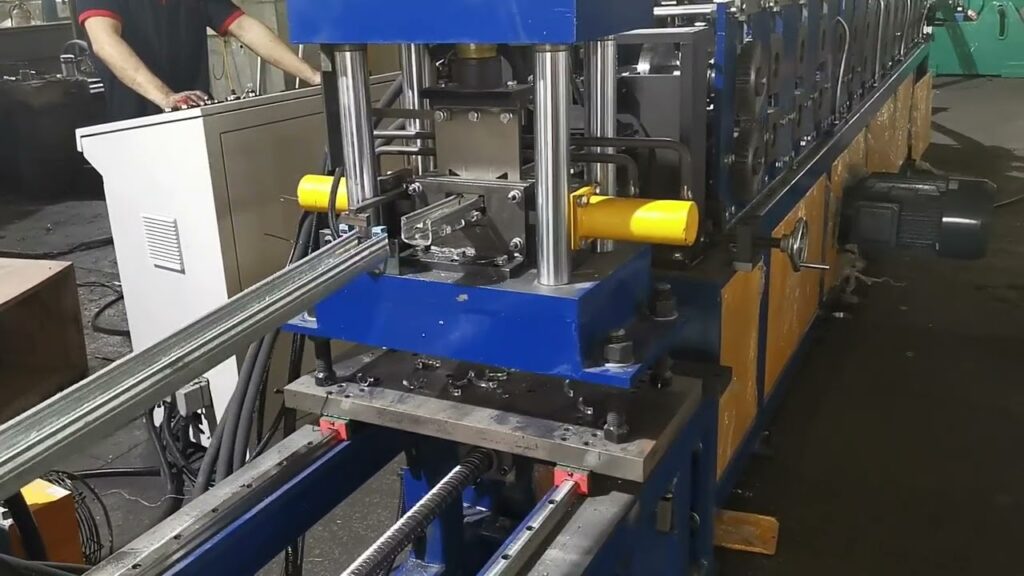
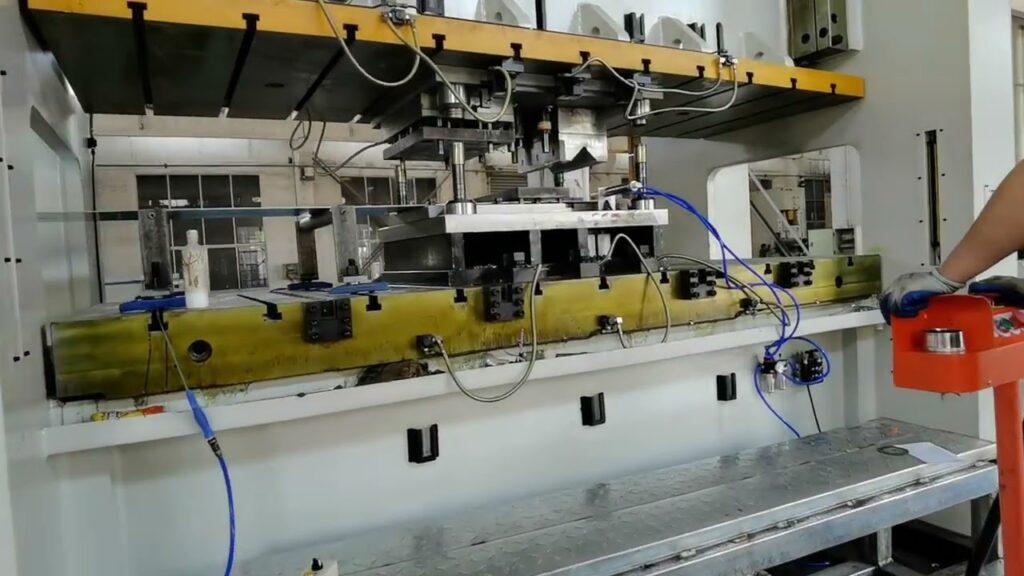
There are two main types of automation that can be applied to width corrugated sheet roll forming machines: semi-automated and fully-automated systems. Here’s a breakdown of each type and their features and benefits:
Benefits of Semi-Automated Systems:
- Reduced labor costs
- Increased productivity and efficiency
- Improved accuracy and consistency
- Reduced waste
- Greater flexibility and customization
- Fully-Automated Systems: Fully-automated systems rely on advanced technology to perform all tasks in the production process. These systems are designed to run 24/7 with minimal human intervention, resulting in high levels of productivity and efficiency. Fully-automated systems are a good choice for manufacturers who want to maximize productivity, reduce labor costs, and improve the consistency and accuracy of their final product.
Benefits of Fully-Automated Systems:
- Maximized productivity and efficiency
- Reduced labor costs
- Improved accuracy and consistency
- Reduced waste
- Greater safety in the workplace
In summary, both semi-automated and fully-automated systems offer significant benefits for manufacturers of width corrugated sheet roll forming machines. Semi-automated systems provide a balance between automation and human labor, while fully-automated systems maximize efficiency and productivity. Choosing the right type of automation for your business will depend on your specific needs and goals.
Implementation for automating width corrugated sheet roll forming machine
Implementing automation in your width corrugated sheet roll forming machine involves several steps, including:
- Identify Your Goals: Start by defining your goals for automation. What tasks do you want to automate? What are your expected outcomes? This will help you determine the type of automation you need and the level of investment required.
- Select the Right Technology: Once you’ve identified your goals, you need to select the right technology for your application. This may involve working with a supplier or manufacturer to identify the best automation systems for your specific needs.
- Develop a Plan: Develop a detailed plan for implementing automation in your width corrugated sheet roll forming machine. This plan should include timelines, budgets, and responsibilities for each phase of the implementation process.
Train Your Staff: Automation requires a certain level of expertise to operate, so make sure your staff is properly trained on the new systems and technologies.
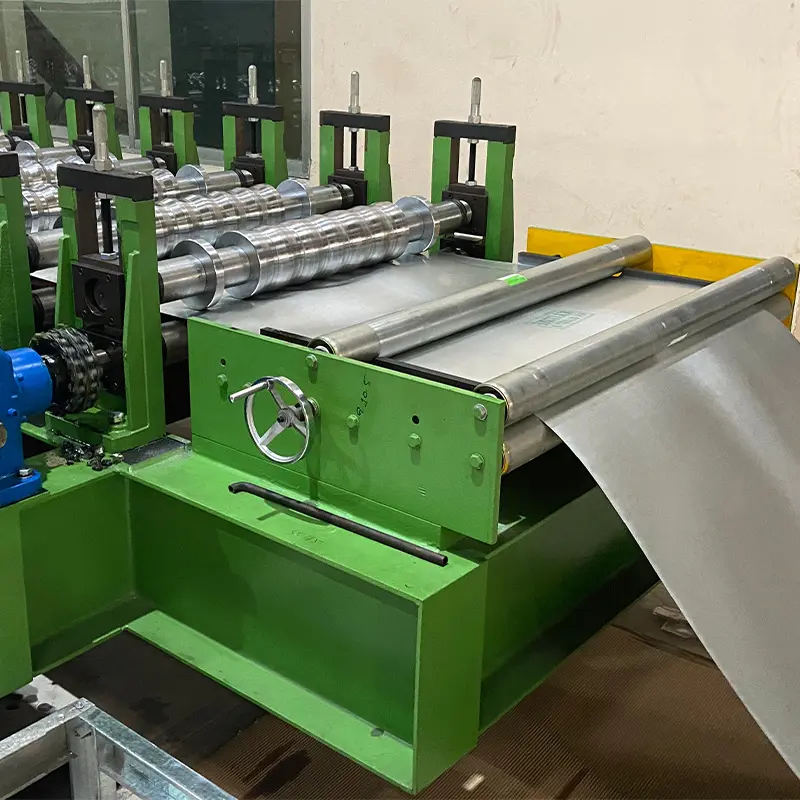


- Test and Monitor: Before fully implementing automation in your production process, conduct tests and monitor the results to ensure that the new systems are working properly and delivering the expected outcomes.
- While implementing automation in your width corrugated sheet roll forming machine can offer significant benefits, there are also potential challenges to consider, such as:
- High Upfront Costs: Automation systems can be expensive to purchase and implement, requiring a significant upfront investment.
- Technological Challenges: Implementing new technology can be challenging, and there may be a learning curve for your staff.
- Maintenance and Repair: Automation systems require regular maintenance and repairs, which can add to the overall cost of implementation.
To determine if automation is a worthwhile investment for your business, it’s important to conduct a cost-benefit analysis. This analysis should take into account the potential costs and savings associated with automation, as well as the expected return on investment over time. By weighing the benefits and costs, you can make an informed decision about whether automation is the right choice for your business.
In conclusion, automation technology has significantly transformed the width corrugated sheet roll forming machine industry. By automating the production process, manufacturers can achieve greater productivity, increased efficiency, improved accuracy and consistency, and reduced labor costs. Semi-automated and fully-automated systems offer unique advantages and benefits, and manufacturers must choose the appropriate type based on their specific needs and goals. The implementation process for automation involves several steps, including identifying goals, selecting technology, developing a plan, training staff, and testing and monitoring. While automation can be costly, conducting a cost-benefit analysis can help manufacturers determine the long-term ROI and make informed decisions about implementing automation in their businesses.