In the world of metal forming, heavy duty roll forming machines stand out as essential equipment for manufacturing high-precision metal components. These machines transform metal sheets into desired shapes through a continuous bending operation. This guide dives deep into the intricacies of heavy duty roll forming machines, providing you with an in-depth understanding of their workings, types, components, and much more.
Overview of Heavy Duty Roll Forming Machines
Heavy duty roll forming machines are advanced equipment designed for shaping long strips of metal into various profiles and cross-sections. These machines are integral to industries such as construction, automotive, and manufacturing, offering efficiency, precision, and versatility. Let’s explore the fundamental aspects of these machines.
Key Details
- Purpose: To form metal sheets into continuous shapes or profiles.
- Materials: Typically works with steel, aluminum, and other durable metals.
- Industries: Construction, automotive, manufacturing, and more.
- Advantages: High efficiency, precision, and customizability.
Understanding the various aspects of heavy duty roll forming machines is crucial for selecting the right model for your needs. Here, we’ll cover the different types, the working process, key components, and much more.
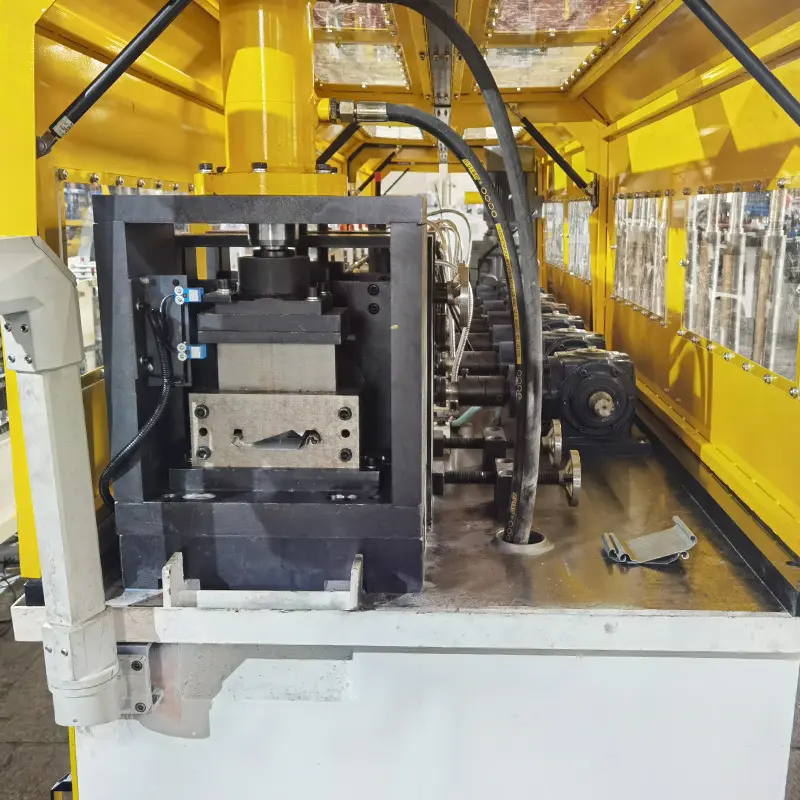
Types of Heavy Duty Roll Forming Machines
There are several types of heavy duty roll forming machines, each designed for specific applications and materials. The table below outlines some of the most common types and their characteristics.
Type | Description |
---|---|
Single-Side Roll Forming | Ideal for simpler profiles with uniform cross-sections on one side. |
Double-Side Roll Forming | Allows for more complex profiles with different cross-sections on either side. |
Flying Die Roll Forming | Features a cutting die that moves along with the workpiece, ensuring continuous operation without stops. |
Fixed-Die Roll Forming | Utilizes a stationary die, suitable for simpler and repetitive profiles. |
High-Precision Roll Forming | Offers exceptional accuracy for intricate and high-tolerance profiles. |
Compact Roll Forming | Space-saving design, suitable for smaller workshops or limited space environments. |
Heavy-Duty Industrial | Built for robust and large-scale industrial applications, handling thick and wide metal sheets. |
Portable Roll Forming | Designed for on-site work, providing flexibility and mobility. |
Automated Roll Forming | Integrates advanced automation for improved efficiency and reduced manual intervention. |
Custom Roll Forming | Tailored to specific production needs and custom profiles. |
Working Process of High-Speed Roll Forming Machines
The working process of high-speed roll forming machines is a blend of precision and efficiency. Here’s a step-by-step breakdown:
- Material Feeding: The metal strip is fed into the machine.
- Roll Forming Stages: The strip passes through a series of roller dies that gradually shape it into the desired profile.
- Cutting Process: The formed profile is cut to the required length by an integrated cutting system.
- Collection: The finished products are collected and prepared for further processing or shipment.
This continuous process ensures high-speed production with minimal downtime, making it ideal for large-scale manufacturing.
Key Components and Their Functions
Heavy duty roll forming machines comprise several key components, each playing a vital role in the operation. The table below details these components and their functions.
Component | Function |
---|---|
Uncoiler | Feeds the metal strip into the machine. |
Roller Dies | Gradually shape the metal strip into the desired profile. |
Cutting Mechanism | Cuts the formed profile to the required length. |
Control System | Manages the machine’s operations and settings. |
Hydraulic System | Powers the cutting and other auxiliary systems. |
Guiding System | Ensures the metal strip is accurately positioned throughout the forming process. |
Drive System | Powers the rollers and ensures consistent material movement. |
Safety Features | Includes emergency stop buttons, guards, and sensors to protect operators and equipment. |
Cooling System | Prevents overheating of the machine components during prolonged operation. |
Lubrication System | Reduces friction between moving parts, extending the machine’s lifespan. |
-
Highway Guardrail End Terminal Forming Machine
-
Highway U/C Post Roll Forming Machine
-
2 Waves Highway Guardrail Roll Forming Machine
-
3 Waves Highway Guardrail Roll Forming Machine
-
Vineyard Post Roll Forming Machine
-
Auto Size Changeable Sigma Purlin Roll Forming Machine
-
Auto Size Changeable C Z Purlin Roll Forming Machine
-
Auto Size Changeable Z Purlin Roll Forming Machine
-
Auto Size Changeable C U Purlin Roll Forming Machine
Machine Speed and Efficiency
The speed and efficiency of a roll forming machine are critical factors for productivity. The table below highlights typical speed ranges and efficiency metrics for heavy duty roll forming machines.
Machine Type | Speed (meters/minute) | Efficiency (%) |
---|---|---|
Single-Side Roll Forming | 10 – 20 | 85 – 90 |
Double-Side Roll Forming | 15 – 25 | 80 – 85 |
Flying Die Roll Forming | 20 – 30 | 90 – 95 |
Fixed-Die Roll Forming | 10 – 20 | 85 – 90 |
High-Precision Roll Forming | 5 – 15 | 95 – 98 |
Compact Roll Forming | 10 – 20 | 80 – 85 |
Heavy-Duty Industrial | 5 – 15 | 90 – 95 |
Portable Roll Forming | 10 – 20 | 75 – 80 |
Automated Roll Forming | 20 – 35 | 95 – 98 |
Custom Roll Forming | Varies | Varies |
Customized Mechanical Parameters
Customizing mechanical parameters ensures the machine meets specific production requirements. The table below showcases typical customizable parameters.
Parameter | Description |
---|---|
Roller Diameter | Can be adjusted to handle different metal thicknesses and profiles. |
Material Width | The width of the metal strip being processed can be customized. |
Material Thickness | Adjustments to handle various thicknesses from thin sheets to thick plates. |
Number of Rollers | Customizable to match the complexity of the profile. |
Line Speed | Speed adjustments to match production needs. |
Cutting Length | Customizable length settings for the final product. |
Power Requirements | Adjustable to match the available power supply and production demands. |
Automation Level | Customizable automation features for different levels of manual intervention. |
Control System | Tailored control systems for specific operational requirements. |
Safety Features | Enhanced or specific safety features based on the operational environment. |
Applications and Uses
Heavy duty roll forming machines are versatile and find applications in various industries. The table below lists some common applications.
Industry | Application |
---|---|
Construction | Forming roofing sheets, wall panels, and structural components. |
Automotive | Manufacturing car frames, bumpers, and reinforcements. |
Aerospace | Producing lightweight yet strong structural components. |
Electrical | Creating enclosures, cable trays, and conduits. |
Furniture | Forming metal frames and supports. |
Appliances | Producing parts for refrigerators, washing machines, and other appliances. |
Energy | Manufacturing components for wind turbines, solar panels, and pipelines. |
Transportation | Creating parts for trucks, trailers, and rail vehicles. |
Agriculture | Producing equipment parts and storage structures. |
Marine | Forming components for ships and offshore structures. |
Installation, Operation, and Maintenance
Proper installation, operation, and maintenance are crucial for the optimal performance of heavy duty roll forming machines. The table below provides a guide for each aspect.
Aspect | Details |
---|---|
Installation | Ensure a stable foundation, proper alignment, and secure all components. |
Operation | Follow manufacturer guidelines, train operators, and use appropriate safety gear. |
Maintenance | Regularly inspect and lubricate components, replace worn parts, and ensure the hydraulic system is functioning. |
Suppliers and Price Range
Choosing the right supplier and understanding the price range are essential for investment decisions. The table below lists some prominent suppliers and typical price ranges.
Supplier | Price Range (USD) | Description |
---|---|---|
Samco Machinery | $50,000 – $200,000 | Known for high-quality and durable roll forming machines. |
Formtek | $60,000 – $250,000 | Offers a range of customizable and automated roll forming solutions. |
Gasparini Industries | $70,000 – $300,000 | Specializes in high-precision and industrial-grade machines. |
Bradbury Group | $80,000 – $350,000 | Renowned for innovative and high-speed roll forming equipment. |
Dallan | $90,000 – $400,000 | Provides advanced automation and energy-efficient machines. |
How to Choose a Supplier
Selecting the right supplier involves evaluating several factors. The table below outlines key considerations.
Factor | Details |
---|---|
Reputation | Research supplier reputation, customer reviews, and industry standing. |
Quality | Assess the quality of machines, materials used, and precision capabilities. |
Support | Consider after-sales support, training, and availability of spare parts. |
Customization | Look for suppliers offering customizable solutions tailored to your needs. |
Price | Evaluate the price in relation to the features and capabilities of the machine. |
Delivery Time | Check the supplier’s delivery time to ensure it aligns with your project timeline. |
Warranty | Review the warranty terms and coverage for the machines. |
Technical Expertise | Ensure the supplier has the technical expertise to support your specific requirements. |
Pros and Cons: Advantages and Limitations
When considering a heavy duty roll forming machine, it’s essential to weigh the pros and cons. The table below provides a comparative analysis.
Aspect | Advantages | Limitations |
---|---|---|
Efficiency | High production rates and continuous operation. | Initial setup and alignment can be time-consuming. |
Precision | Consistent and accurate profiles. | Requires skilled operators and precise calibration. |
Versatility | Can handle various profiles and materials. | Limited by the specific design and capabilities of the machine. |
Cost | Lower long-term production costs. | High initial investment. |
Automation | Reduced manual intervention and increased safety. | Complex automation systems may require specialized maintenance. |
Durability | Long lifespan with proper maintenance. | Potential downtime during maintenance or part replacement. |
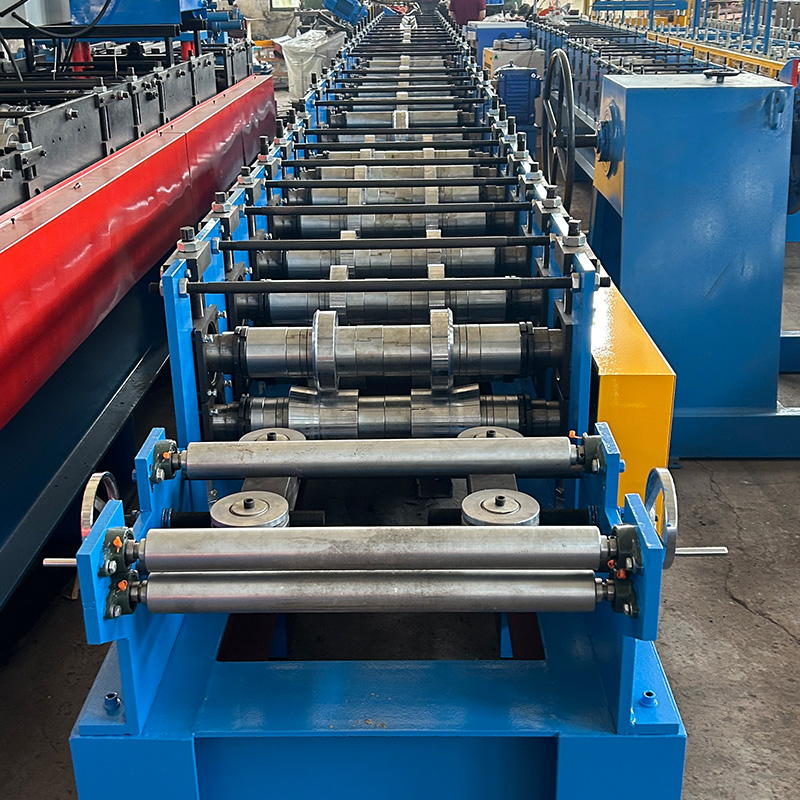
FAQs
To address common queries, here’s an FAQ section with answers to frequently asked questions.
Question | Answer |
---|---|
What materials can be used with roll forming machines? | Typically, steel, aluminum, and other durable metals. |
How do I choose the right roll forming machine? | Consider factors such as material, profile complexity, production volume, and budget. |
What is the typical lifespan of a roll forming machine? | With proper maintenance, these machines can last for decades. |
Can roll forming machines be customized? | Yes, many manufacturers offer customizable options to meet specific production needs. |
What are the safety features of roll forming machines? | Includes emergency stop buttons, guards, sensors, and automated shutdown systems. |
How often should maintenance be performed? | Regular maintenance should be performed as per the manufacturer’s guidelines, typically monthly or quarterly. |
What is the difference between single-side and double-side roll forming machines? | Single-side is for uniform profiles on one side, while double-side handles complex profiles on both sides. |
Is operator training necessary? | Yes, proper training ensures safe and efficient machine operation. |
Conclusion
Heavy duty roll forming machines are indispensable in the metal forming industry, offering unmatched efficiency, precision, and versatility. By understanding the various types, components, working processes, and customization options, you can make an informed decision when investing in these powerful machines. Whether you’re in construction, automotive, or any other industry requiring metal profiles, these machines are a game-changer, boosting productivity and ensuring high-quality output.
Investing in a heavy duty roll forming machine is a significant decision, but with the right information and guidance, you can choose the best machine to meet your production needs and elevate your manufacturing capabilities.