Cold roll forming machines shape metal coils into customized profiles through an incremental, continuous bending process using a series of rollers. oem cold roll forming machine offer customized design and manufacturing of such equipment tailored to a company’s specific production needs. This comprehensive guide covers everything related to OEM cold roll formers.
Overview of OEM Cold Roll Forming Machines
OEM cold roll forming machines, also known as OEM roll formers or roll forming lines, are an ideal equipment choice for high-volume production of metal parts with repetitive cross-sections. Key benefits include:
- Customized to exact specifications required by the buyer
- Integrated with other manufacturing processes onsite
- Lower upfront capital investment compared to off-the-shelf solutions
- Optimized for efficiency and maximum output
OEM roll forming technology transforms flat metal stock into angled, curved, or other custom shapes by progressively bending the material through consecutive roller stations on a continuous production line.
Common application areas include:
- Roofing, siding, panelling, drainage systems
- Rack, shelving, enclosure, and door frame components
- Automotive, HVAC, and appliance parts
- Scaffolding, solar panel mounts, highway products
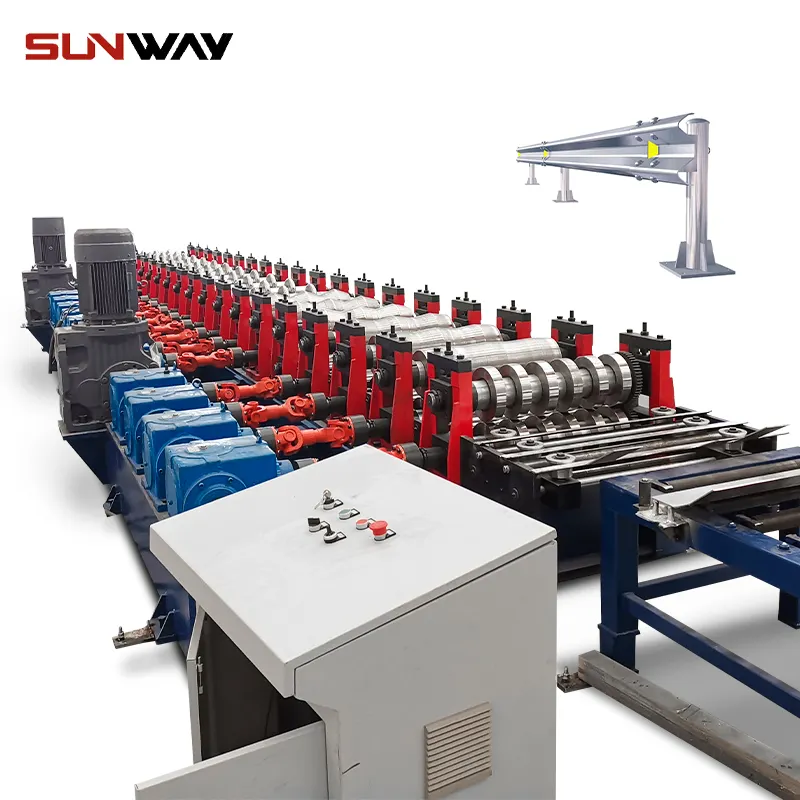
How oem cold roll forming machine Works
The OEM cold roll forming process involves:
Material Feeding
- Coiled metal stock loaded onto a de-coiler
- Fed through a straightener to correct flatness/alignment
- Enters forming section
Forming
- Sheet passes through series of roller stations
- Rollers apply pressure to bend metal incrementally
- Desired profile achieved gradually over multiple roller passes
Cut-Off & Customization
- Formed profile cut to length by rotating shear
- Holes punched, hardware inserted, ends trimmed etc.
- Finished parts extracted by catch table or conveyors
Table 1: OEM Cold Roll Forming Machine Modules
Module | Function |
---|---|
De-coiler | Unwind metal coil stock |
Straightener | Align/flatten material |
Roll Forming Stations | Gradually shape profile |
Punching Unit | Pierce holes if needed |
Shearing | Cut metal to length |
Hardware Insertion | Add fittings if required |
Extractor | Remove finished pieces |
Types of oem cold roll forming machine Equipment
OEM roll formers are customized during design to meet required part geometries, production volumes, and line integration needs. Major types include:
Table 2: Common OEM Cold Roll Former Types
Type | Description |
---|---|
Start & Stop Lines | Batch production with lower output |
Continuous Lines | High-volume, maximum efficiency |
Compact Lines | Space savings for smaller parts |
Turret Attachment | Roll + bend metal on same machine |
Portable Units | Mobile roll forming ability |
All-Electric Lines | Cleaner, eco-friendly forming |
Application-Based Configurations
OEM roll formers can also be categorized based on end-product application area:
- Construction Roll Formers: Roofing, siding, drainage, structural parts
- Solar Roll Formers: Mounting rails, support channels
- HVAC Roll Formers: Duct components, ventilation products
- Agricultural Roll Formers: Silo panels, building framing, drainage
- Automotive Roll Formers: Body panels, structural reinforcements
Component shaping in each vertical requires specific design considerations addressed through the custom OEM equipment.
Working Principle of oem cold roll forming machine
The fundamental working concept behind any cold roll forming system involves passing flat sheet metal strip stock through consecutive roller stations to induce incremental bending until the desired profile is gradually formed across the length of the material.
Table 3: Central Principles of Cold Roll Forming Process
Principle | Explanation |
---|---|
Incremental Bending | Many small bends distributed over several roller passes shape profile |
Continuous Processing | Coil continuously fed through rollers at constant speed |
Cold Working | Room temperature forming preserves material properties |
Compressive Force | Rollers apply localized pressure to bend sheet |
Progressive Shaping | Final form achieved gradually through roller sequence |
Understanding these core mechanics of bend formation helps appreciate how OEM roll formers can create customized geometries.
Key Process Parameters
Additionally, knowledge of certain key process parameters is important for designing effective OEM cold roll forming lines:
- Thickness and Grade of Metal – Determines force required for forming
- Width of Coil Stock – Affects number of forming heads/stations needed
- Inside Bend Radius – Impacts roller dimensions and layout
- Bending Angle – Sequential bending add up to shape profile
- Number of Passes – More passes allow greater control over incremental shaping
By factoring these specifications into equipment concept development, OEM roll former performance can be maximized.
-
Auto Changeable C Z Purline Machine
-
Auto Size Changeable C Z Purlin Roll Forming Machine
-
Electrical Cabinet Frame Roll Forming Machine
-
Din Rail Roll Forming Machine
-
CZ Purlin Roll forming machine
-
Cable Ladder Roll Forming Machine
-
PV Mounting Bracket C Shape Profile Roll Forming Machine
-
Cable Tray Roll Forming Machine
-
C Z Purlin Channel Cold Roll Forming Machine Full Auto Galvanized Steel Profile
Roll Forming Machine Design & Engineering
Creating optimized OEM cold roll forming machines for a company’s production environment requires extensive design engineering customized to their specific component requirements and layout constraints.
Table 4: OEM Roll Former Design Considerations
Design Aspect | Details |
---|---|
Forming Roller Stations | Layout, type, number, and size |
Material Feed System | Decoiler, straightener, and guides |
Profile Cutoff | Rotary or guillotine shear style, automation |
Conveyor/Extraction | Inline or exit conveyors, part removal method |
Controller & Drives | PLC programming, servo/VFD motors, HMI |
Safety Guarding | Mesh, plexiglass, or steel construction |
Structural Frame | Profile, rigidity, and vibration resistance |
Line Integration | Smooth connections to upstream/downstream processes |
Proper design is key for:
- Achieving required part geometries
- Maximizing production speeds and uptime
- Accommodating available floor space
- Simplifying maintenance/changeovers
- Allowing future flexibility
Partnering early with an experienced OEM roll former builder allows leveraging their engineering expertise to get these parameters right.
Key Considerations for Choosing an OEM Cold Roll Forming Machine Supplier
Selecting the right OEM cold roll forming machine partner is critical because the equipment directly impacts manufacturing capabilities, output, and operations.
Table 5: How to Choose OEM Roll Former Supplier
Evaluation Criteria | Significance |
---|---|
Design Engineering Skills | Ability to supply optimal custom solution |
Build Quality & Structural Rigidity | Maximizes accuracy and product consistency |
Production Speed | Determines component output rate |
Quick Changeover Design | Minimizes downtime for size/profile adjustments |
Precision & Repeatability | Vital for maintaining tight tolerances |
Experience & Technical Know-How | Needed for complexity of process engineering |
Responsiveness | Speed of design iterations and quote turnaround |
Budget Constraints | Balance performance with acceptable price point |
Additional considerations when comparing OEM roll former manufacturers include:
- Years in business and number of machines supplied
- Staff engineering competencies
- Understanding exact production requirements
- Line integration experience if needed
- Overall perceived reputation and customer service philosophy
Getting multiple quotes allows comparing technical proposals and cost tradeoffs. Site visits to existing installations are highly recommended as well.
Pros and Cons of OEM Cold Roll Forming Technology
Cold roll forming using OEM equipment offers numerous benefits but also has some limitations to factor in depending on product needs.
Table 6: Advantages and Disadvantages of OEM Cold Roll Formers
Advantages | Disadvantages |
---|---|
Continuous production at fast speeds | Significant upfront capital investment |
Consistent, repetitive output quality | Inflexible once built, changes require rework |
High material yield from coil inputs | Limited forming complexity based on bend radius |
Low tooling costs after initial build | Not ideal for low or extremely high production volumes |
Simplified operating skill requirements | Line integration may require upstream/downstream processes |
Small equipment footprint space | Significant lead time for designing and building machines |
Energy efficiency benefits | Limited ability to shape high strength materials |
No heating or chemistry use |
Understanding this profile of strengths versus limitations helps determine when investing in OEM cold roll formers is strategically justified.
Major Application Areas for OEM Cold Roll Formed Parts
Custom OEM roll forming machines find widespread adoption serving the production needs of various industries.
Construction:
- Structural framing studs
- Roofing, siding, drainage profiles
- Door, window, shelving components
Automotive:
- Vehicle frame strengthening inserts
- Exterior body panels and trims
- Interior compartment supports
Appliances & HVAC:
- Washer/dryer drums
- Refrigeration units
- Airducts and ventilation parts
Infrastructure:
- Highway safety barriers
- Traffic signage and signals
- Scaffolding and staging
Energy:
- Mounting frames for solar panels
- Wind turbine body panels
- Power transmission poles
The flexibility to create customized cross-sectional geometries efficiently through OEM roll forming allows mass supplying repetitive parts to these diverse sectors.
Conclusion
Investing in tailor-made OEM cold roll forming capabilities brings extensive benefits for producing components with repetitive profiles at high volumes efficiently. Partnering early with specialized OEM equipment builders allows customizing every design aspect for maximum performance. By understanding the incremental bending process fundamentals, opportunities abound for creatively shaping metal across endless applications. With appropriate planning and engineering rigor, OEM roll formed parts can deliver productivity and quality gains across manufacturing.
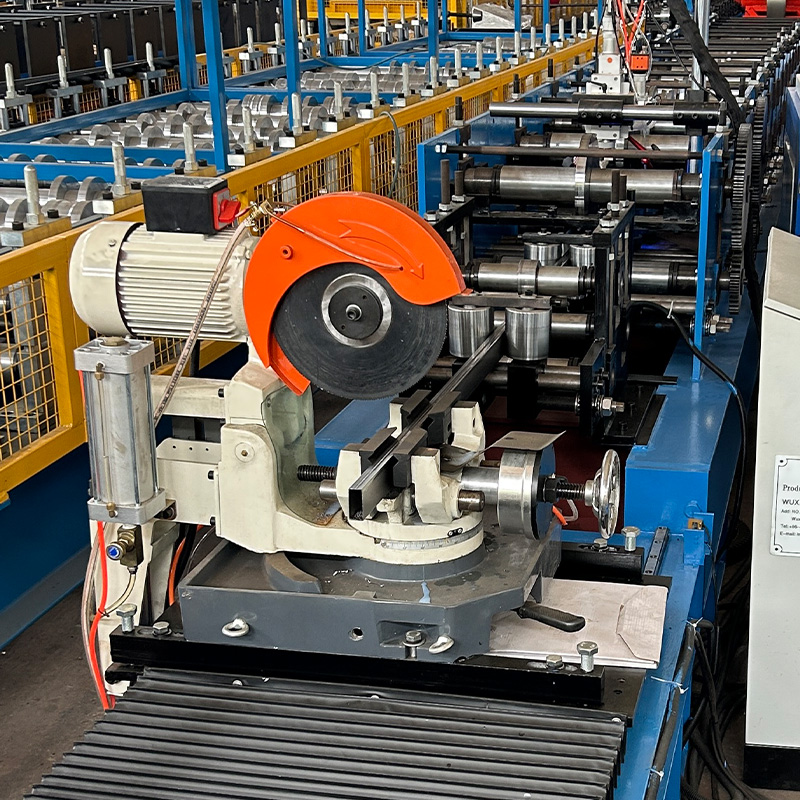
FAQ
Q: What expertise is needed to operate OEM cold roll forming lines?
A: Basic equipment operation is simple enough for quick operator training. Production engineers handle program settings and maintenance. Experienced technical teams are needed on the OEM builder side for proper machine design and development.
Q: Can other metal processing be integrated with cold roll forming machines?
A: Yes, punching, shearing, pressing, hardware insertion, part extraction via robotics, and other secondary processing can be built into complete OEM roll forming system solutions.
Q: What size metal coils can be roll formed?
A: OEM roll former capacities range widely based on design and generally handle coils from a few inches up to 72 inches wide weighing over 50,000 pounds. Many accommodate multiple coil inputs.
Q: How quick are changeovers between different roll formed profiles?
A: Electric powered roll adjustment with positional feedback allows fairly rapid profile changeovers in 15-30 minutes depending on complexity once initial tooling is built.
Q: What factors affect OEM cold roll forming machine pricing?
A: Key determinants of capital cost include overall line length, number of forming heads, material thickness/width capabilities, accuracy requirements, and extent of part customization features.
Q: Can OEM cold roll forming equipment be relocated or resold easily?
A: Changing an entire production line’s location after initial building is generally unfeasible. For resale, customizations to the original buyer’s needs often limit universal appeal requiring heavy modifications.