Self lock roofing sheet roll forming machines produce interlocking roof panels with integrated connectors from coil feedstock. This guide reviews self lock roll former configurations, components, customization options, operation guidance and maintenance considerations to inform manufacturers.
self lock roofing sheet roll forming machine Overview
Self lock roof sheet roll formers transform flat coil stock into roofing panels with integrated mechanical seams for simplified installation. Key features:
- High hourly production volumes lower cost per panel
- Flexibility producing varied interlock profile types
- Reduced material waste versus stamping processes
- Continuous automated production 24×7 after coil loading
Reviewing configurations, customization possibilities and maintenance procedures assists manufacturers employing self lock roll formers optimally.
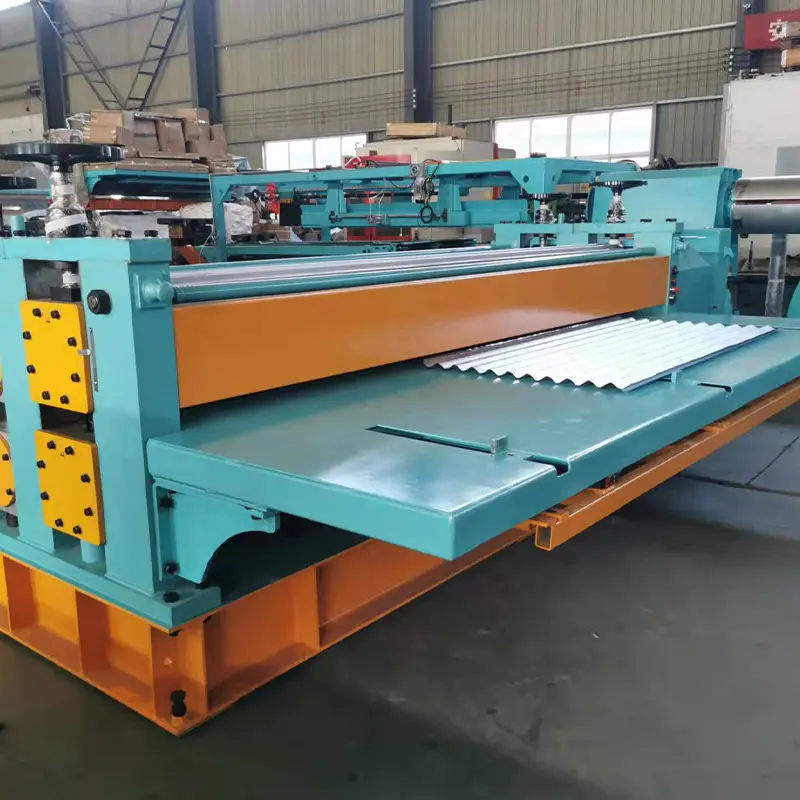
Types of Self Lock Roofing Sheet Roll Formers
Common variants include:
Type | Description |
---|---|
Mechanical Drive | Hydraulic powered stations via mechanical gearboxes |
Servo Electric Drive | AC precision servo motors independently control stations |
Single Layer | For standard smaller interlock profiles |
Double Layer | Complex larger interlocks simultaneous top and bottom forming |
Table 1: Self lock roofing sheet roll former types covering power, configuration and forming considerations
Electric servo controls enable fast set changeovers while mechanical gears provide heavy duty economical forming reliability. Double layer machines boost output for standard self lock commodities.
Roll Forming Process for Self Locking Roof Sheet
A multi-stage roll forming process for interlocking roof panels involves:
Decoiling – Coil stock enters powered decoiler holding tension
Feeding – Feed rolls pull steel through subsequent stations
Pre-forming – Sheet lightly forms into early panel wave shape
Profile Forming – Sequential stands cut then form connector hooks
Lock Forming – Final stands close locks into other side
Cutting – Hydraulic shear slices panels to length
Counting – Automated counters tally sheets
Stacking – Formed panels placed onto exit tables
Synchronizing these steps enables efficient high volume production of self locking roofing.
Key Components of Self Lock Roofing Sheet Roll Formers
Typical engineered sub systems include:
- Decoiler – Holds coil strip feeding line input
- Feed System – Pulls stock into first forming station
- Progressive Forming Dies – Gradually cut then shape interlocks
- Hydraulics System – Powers mechanical gearbox drive
- Control System – Automates line speed and counting
- Cutter – Shears panels to length after profile complete
- Exit Conveyor – Stacks finished panels
Interlinking these modules maximizes automated forming of self locking roof sheeting.
-
Electrical Cabinet Frame Roll Forming Machine
-
Din Rail Roll Forming Machine
-
Cable Ladder Roll Forming Machine
-
PV Mounting Bracket C Shape Profile Roll Forming Machine
-
Cable Tray Roll Forming Machine
-
PV Mounting Bracket Roll Forming Machine (HAT / Omega Profile)
-
PV Mounting Bracket Z Shape Profile Roll Forming Machine
-
Solar mounting strut channel roll forming machine
-
Strut Channel Roll Forming Machine
Customizing Self Lock Roof Sheet Roll Former Lines
While standardized, customization possibilities include:
- Profile Tooling – Special roll sets match customer interlock geometries
- Speed – Servo electric drives for faster cycle times
- Automation – Monitoring, stacking and packaging allows lights out operations
- Decoiler Size – Large coils mean fewer loading interruptions
- Secondary Operations – Custom post-forming fabrication steps like punching
Articulating special engineering goals in procurement requests allows pricing appropriate customization delivering lines matching security interlock roofing business requirements.
Selecting Self Lock Roof Sheet Roll Former Manufacturers
When evaluating suppliers, key selection criteria encompasses:
- Specialization – Seek dedicated roll former machine vendors
- Experience – Review company lineage and client installation portfolio
- Design Services – Necessitate engineering support for custom needs
- Quality – Require all steel fabricated construction
- Validation – Look for quality/safety control certifications
- Services – Installation, training and maintenance support options
- Pricing – Compare proposals ensuring adequate feature parity
Thoroughly vetting numerous manufacturers on engineering strengths, safety-focused production and ongoing services availability builds confidence when investing in major factory enhancing automation.
Self Lock Roof Sheet Roll Former Pricing
Budget estimates for complete roll forming line costs span:
- Base Machine – Around $125,000 for basics
- Size customization – For bigger decoilers add $5,000-$15,000
- Servo upgrades – Adds $25,000-$60,000 versus base mechanical drives
- Conveyors/Transfers – $5,000-$15,000 depending on automation
- Install/Transport – Typically runs $15,000-$30,000 using professional technicians
Factor $175,000 to $275,000+ for turnkey lines matching standard versus fully customized order specifications ultimately aligning fabricated productivity to target business volume, flexibility and quality prerequisites demanded daily.
Maintaining Self Lock Roof Sheet Roll Former Operations
To sustain consistent production, recommended routines include:
Daily Cleaning – Clear line debris inhibiting transfers
Scheduled Inspections – Monthly inspect hydraulics, electricals and alignments
Roll Maintenance – Lubricate/resurface roll dies minimizing scratches
Recalibration – Annual servicing checking sensors, actuators and press alignments
Catching component wear early via prescribed maintenance prevents unplanned downtime through replacing parts proactively – a reliability-focused mindset applied sustaining high percent operating availability enabling consistent interlock roof sheeting production 24×7 over decades seamlessly matching variable market demand seen historically the world over.
Comparing Roll Forming to Stamp Presses
Consideration | Roll Forming | Stamping Presses |
---|---|---|
Setup Time | Hours | Days |
Lead Time | Weeks | Months |
Tooling Cost | Tens of thousands | Hundreds of thousands |
Material Utilization | 95%+ | 60% |
Short Run Flexibility | Strong | Limited |
Product Complexity | Simpler profiles | High complexity achievable |
Table 2. Comparing self lock roof sheeting production via roll forming and large stamping press approaches
For producing mixed niche products across varying monthly volumes efficiently, the flexibility of roll forming solutions deserve consideration when evaluating optimal fabrication system investments supporting both current and projected business over likely decades of changing requirements likely to emerge.
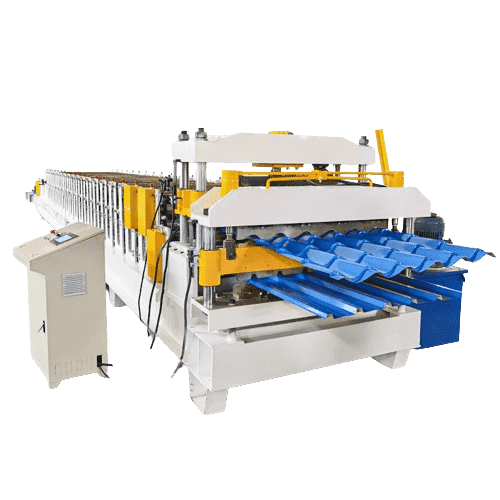
FAQ
Q: What thickness and hardness ranges can lines accommodate?
A: Most handle 0.4 – 1 mm thickness across harness levels to Temper 07/3H notoriously difficult to coin stamp without splitting or cracking as strains localized harden exceeding 85% depending on geometry and penetration ratios determine equipment upgrade requirements balancing tonnage against forming stations properly supporting bends completed. Additional secondary process annealing often minimizes refinement stresses although reducing margins so each specification deserves scrutiny evaluating entire production ecosystem capabilities currently installed.
Q: What causes scratching defects on finished roof panels?
A: Buildup, press roll alignment drift or inadequate external blowoff occasionally requires increased vigilant monitoring and maintenance ensuring pristine surface quality production not impacted short or long term. Address root causes rather than applying temporary containment inspecting why problems manifested initially.
Q: Can a single production line handle multiple interlock profile types?
A: Yes, additional quick change roll sets transformed systems enabling mixed products supporting high product varieties still maintaining profitably – flexibility enabling broader building construction panel catalogs competitively. Modern quick tool change solutions make this possible.
Q: What production speed range capability exists on these roll formers?
A: Mechanical lines typically operate around 20 meters per minute. Integrated servo electric lines can achieve 80+ meters per minute output contingent upon installed power, press tonnage transfer and stock decoiler feed rate capabilities all sized appropriately mapping final throughput targets forecast each year. Carefully validate proposed specifications against realistic volume expectations ensuring honest capacity communications.