Ceiling T grid roll forming machines are used to produce T grid profiles for suspended ceiling systems. They form metal coil into the characteristic T shape through a series of progressive roll forming stations. Ceiling grids provide an exposed structure to support ceiling tiles or panels in commercial and residential buildings.
This comprehensive guide will cover all aspects of ceiling T grid roll forming machines including:
Overview of Ceiling T Grid Roll Forming Machine
A ceiling T grid roll forming machine takes flat metal coil as input and processes it through a series of roller dies to continuously form the strip into the final T shaped profile. The formed T grids are used as support systems for modular dropped ceilings.
The grid layout creates a frame to support ceiling tiles and provides access to the plenum space above the ceiling for electrical, plumbing and HVAC systems. T grid profiles provide an exposed and aesthetically pleasing ceiling with easy access to the space above.
Main Components
- Uncoiler
- Feeder
- Roll forming stations
- Hydraulic system
- Cutoff device
- Finishing stations
Working Principle
The uncoiler holds the coil of flat sheet metal that is fed into the roll former. The feeder has punching and notching units to create holes or slots in the strip before forming. In the roll forming section, the strip goes through a series of progressive dies and bending rolls that gradually shape it into the T profile with the web and flange. Hydraulic cylinders precisely control the rolls for accurate forming. After rolling, the cutoff device shears the formed grid to the desired length. Additional operations like punching, notching, branding and hardware insertion can then be done at finishing stations.
Key Features
- High productivity and yield
- Flexibility to make different T grid sizes
- Precision roll forming process
- Material savings compared to extrusion
- Low maintenance and operation costs
- Automated line with safety features
Main Applications
Ceiling T grid roll forming systems are ideal for:
- Offices, retail spaces, hospitals
- Residential and commercial buildings
- Airports, hotels, institutions
- Both new construction and renovation projects
Suitable Materials
- Low carbon steel
- Galvanized steel
- Prepainted steel
- Stainless steel
- Aluminum
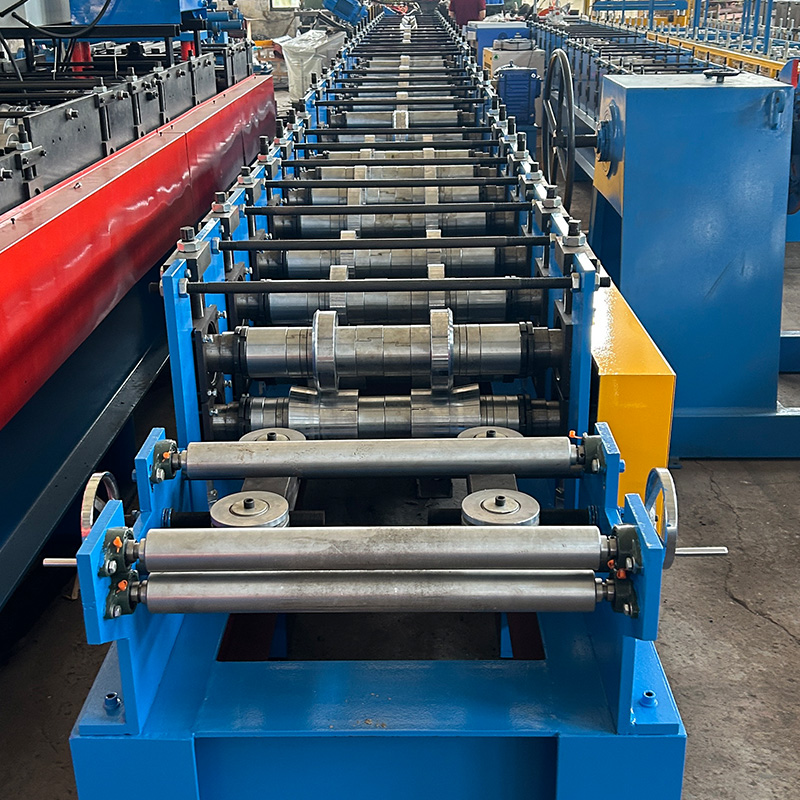
Product Classification
Ceiling T grid roll forming machines can be classified based on:
Automation Level
- Manual – Rolling process is manual, material handling automated
- Semi-automatic – Manual feeding but auto rolling and cutoff
- Fully automatic – Automatic material flow and roll forming
Production Speed
- Low speed – Up to 20 m/min
- Medium speed – 20-40 m/min
- High speed – Over 40 m/min
Roller Type
- Pyramid – Common for high output rates
- S Driven – Compact and precise for small batches
Number of Forming Stations
- 10-12 – Suitable for basic profiles
- 16-20 – For complex/heavy duty T grids
Customization
- Standard – Fixed dimensions and specifications
- Customized – Configurable forming, sizes and accessories
Main Components of T Grid Roll Forming Line
The main sub-systems and components include:
Component | Function |
---|---|
Coil Payoff Reel & Stock Straightener | Holds coil, feeds strip, levels coil |
Servo Feeder System | Feeds strip at constant speed |
Punching Unit | Punch holes for cross tees |
Forming Stations | Progressively form web and flange |
Hydraulic System | Control roller adjustment |
Automatic Cutoff | Cuts profile to length |
Hardware Insertion | Inserts cross tee clips |
Stacker | Collects finished grids |
Technical Specifications
T grid roll forming machine technical specifications vary based on production requirements:
Parameters | Typical Range |
---|---|
Roller Type | Pyramid or S-Driven |
Forming Stations | 10 – 25 |
Roller Material | 45# High Carbon Steel |
Roller Hardness | HRc50-HRc58 |
Maximum Coil Width | 1200 – 1400 mm |
Minimum Coil ID | 508 mm |
Thickness Capacity | 0.3 – 1 mm |
Speed | 10 – 45 m/min |
Power Supply | 220V/380V, 3 Phase, 50/60Hz |
Line Length | 15 – 30 m |
Line Height | 3.5 – 4 m |
Structural Design
The frame and layout employs:
- Welded steel base frames
- Gantry structure for rigidity
- Hydraulic power pack
- Ergonomic design for operation
- Modular stations for flexibility
Minimum door height is 4m. The length depends on production speed and forming stations required.
Advanced Configurations
Additional capabilities can be added:
- Decoiling System – For smooth coil holding and feeding
- Pre-punching – For punching holes before forming
- Automated Stacker – For automatic profile stacking
- Programmable Logic Controller – For precision control
- Flying Cutoff – High speed cutoff system
- Servo Motor Drives – For accurate speed control
- Vision Inspection System – For quality checking
- Data Logging – For production data collection
Range of T Grid Profiles Produced
Standard top tee profiles that can be produced include:
Profile | Dimensions (mm) |
---|---|
15/16″ | 38.1 x 31.8 x 1.27 |
1-1/2″ | 38.1 x 38.1 x 0.457 |
9/16″ | 15.9 x 31.8 x 0.71 |
24mm | 24 x 38 x 0.5 |
600mm | 600 x 38 x 0.7 |
Custom profiles in different sizes, gauges and materials can also be produced by changing the roller dies and machine programming.
Choosing Supplier for T Grid Roll Forming Machine
Key factors in selecting ceiling T grid roll forming machine manufacturer:
Parameters | Considerations |
---|---|
Experience | Number of years in business, projects delivered |
Production Facilities | Factory size, production capacity |
Technical Capability | R&D, design expertise |
Customization | Ability to develop new profiles |
Quality Control | Certifications, quality procedures |
Service Support | Installation, training, maintenance |
References | Client testimonials, site visits |
Pricing | Price vs quality and features |
Reputable manufacturers with strong technical expertise and service support are recommended for machine quality and performance.
Purchase Cost Considerations
Component | Price Range |
---|---|
Manual Line | $5000 to $8000 |
Automatic Line | $8000 to $15000 |
Additional stations | $500 to $1000 per station |
Advanced options | $2000 upwards per item |
Total For Basic Line | $8000 to $12000 |
Total For Fully Automatic Line | $15000 to $30000 |
Cost depends on production speed, line automation, and special features. Additional costs include shipping, installation and training.
Operation and Maintenance
Activity | Details |
---|---|
Material Loading | Use slings to mount coils on payoff reel, manually or with crane |
Line Startup | Turn on hydraulic powerpack, control system, set speed |
Roll Change | Replace rollers after prolonged use using hand tools |
Lubrication | Apply grease to bearings through lines daily |
Cleaning | Remove metal debris buildup on rolls periodically |
Preventive Maintenance | Check roll alignment, hydraulics weekly |
Safety Checks | Ensure safeguards like light curtains are working |
Training | Train workers on proper machine operation, safety |
The hydraulic components require regular maintenance for flawless forming and durability. Workers must be trained on proper line procedures.
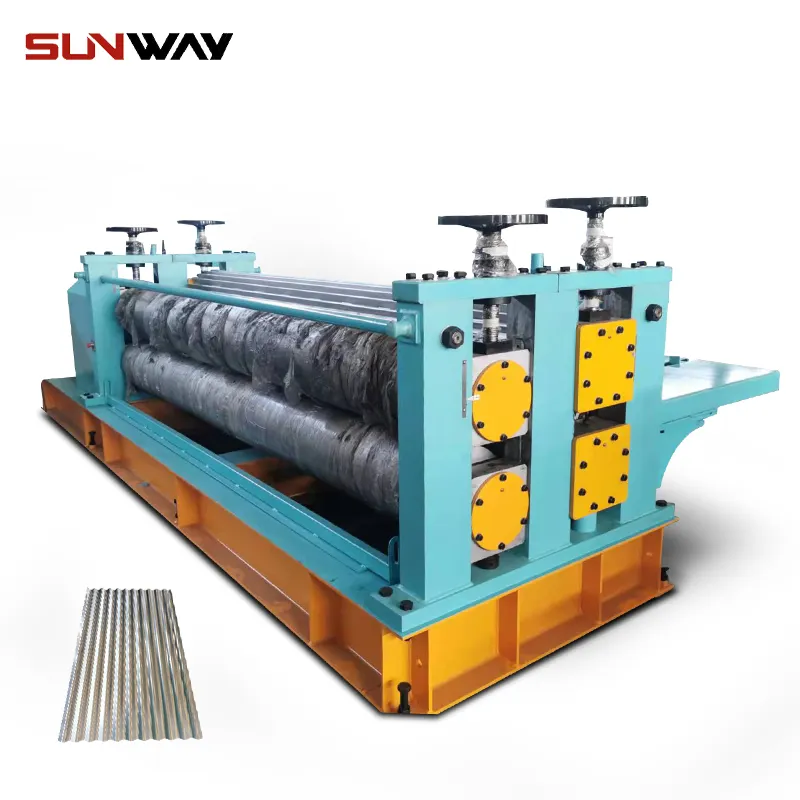
Choosing Between Roll Forming and Extrusion
Method | Roll Forming | Extrusion |
---|---|---|
Working Principle | Rolls gradually form profile | Extrudes profile through die |
Locked Cross-Section | Not guaranteed | Guaranteed by process |
Cycle Time | Slow | Very fast |
Tooling Cost | Lower | Higher |
Material Savings | Higher due to no voids | Lower due to voids |
Strength | Comparable | Comparable |
Product quality | Dimensional accuracy critical | Better tolerances |
Equipment Cost | Lower | Higher capital cost |
Scale of production | Any production volumes | Only very high volumes |
Shape complexity | Limited | High complexity possible |
Operating cost | Lower energy consumption | Higher energy use |
Build rate | Slower | Faster for high volumes |
For most applications, roll forming offers the optimal balance of productivity, quality, and cost-efficiency.
Advantages of Ceiling T Grid Roll Forming
- Cost-effective – Lower equipment and operating costs
- Material savings – No voids unlike extrusion
- Flexibility – Easy changeover between profiles
- Simple operation – Lower skill requirement
- Energy efficient – Lower power consumption
- Lean production – Minimal material waste
- Scalability – Adaptable for different volumes
- Product quality – Good dimensional accuracy
- Productivity – High hourly output rates
Limitations of Ceiling T Grid Roll Forming
- Not suitable for complex asymmetric shapes
- Initial tooling and setup takes time
- Rollers require maintenance
- Limited configuration options
- Periodic roll replacement needed
- Lower strength than extruded T grids
- Limited thickness capacity
- Speed lower than other processes
- Low volume production not economical
- Operator skill needed for coil handling
Proper production planning and machine selection helps minimize these limitations.
FAQ
Q: What materials can be roll formed into T grids?
A: Common materials include low carbon steel, galvanized steel, prefinished steel, stainless steel and aluminum. Special alloys may require custom tooling.
Q: What thickness of coils can be processed?
A: Standard machines accommodate 0.3 – 1 mm thickness. Special units are available for thinner and thicker coils.
Q: How are T grid roll forming machines controlled?
A: They use a PLC for automatic control of all functions. Parameters like speed, cutoff length etc. can be input via the operator interface.
Q: What safety protection is provided?
A: Safety guards, light curtains, emergency stops around moving components prevent accident hazards.
Q: Does the process allow punching of holes for cross tees?
A: Yes, punching units can be integrated before the roll forming section for hole creation.
Q: How are ceiling tiles attached to the T grids?
A: Cross tee connectors are inserted into the holes/slots in the grid to support the ceiling panels.
Q: How to determine the correct machine capacity for production needs?
A: Consider current and future production volumes, T grid sizes, material thickness and budget. The supplier can recommend the ideal configuration.
Q: What is the typical production rate of these machines?
A: Production speed ranges from 10 to 45 meters per minute depending on model. Output is up to 300-400 meters per hour.
Q: How long does it take to change between different T grid profiles?
A: Roll changeover takes approximately 15-20 minutes for an experienced operator to complete.
Q: What is the installation process and requirements for the machine?
A: Machines are shipped pre-assembled in containers. They need a leveled concrete foundation, power supply, compressed air and minimum door height. Installation and commissioning is done by the manufacturer’s technicians.
Q: What is the typical maintenance needed for the machine?
A: Maintenance involves lubricating bearings, cleaning debris from forming stations, replacing worn components and periodic training of operators on procedures.