Understanding Z Purlins
Z Purlin Roll Forming Machine are typically manufactured from galvanized steel, ensuring resistance to corrosion and harsh weather conditions. Their lightweight nature makes them easy to handle and install, while their Z-shape offers superior strength compared to flat sheets of the same material.
Z purlins are the unsung heroes of construction, providing crucial support for roofs and walls. Here’s a closer look at their unique properties:
1. Z-Shaped Strength: Imagine a flat sheet of metal – it’s strong, but prone to bending under pressure. Now, fold that sheet into a Z-shape. Suddenly, it gains torsional rigidity, resisting twisting and bending much more effectively. This ingenious design allows Z purlins to be lightweight yet exceptionally strong.
2. Lightweight Champions: Compared to traditional support beams, Z purlins are significantly lighter. This translates to several advantages:
- Easier and faster installation: Lifting and maneuvering them requires less manpower and equipment, reducing construction time and costs.
- Reduced structural load: Lighter roof supports translate to less weight on the building’s foundation, potentially allowing for more efficient designs.
3. Galvanized Guardians: Z purlins are typically clad in a galvanized coating, acting as a shield against corrosion. This makes them ideal for a variety of environments, including those prone to rain, snow, or coastal elements.
4. Versatile Applications: Z purlins aren’t limited to just roofs. They can be used for walls, canopies, carports, and other structures. Their adaptability makes them a valuable tool for various construction projects.
5. End-Lapping Advantage: Unlike some purlins, Z purlins offer the benefit of end-lapping. This means individual sections can be easily overlapped and connected, allowing for longer spans and greater structural integrity.
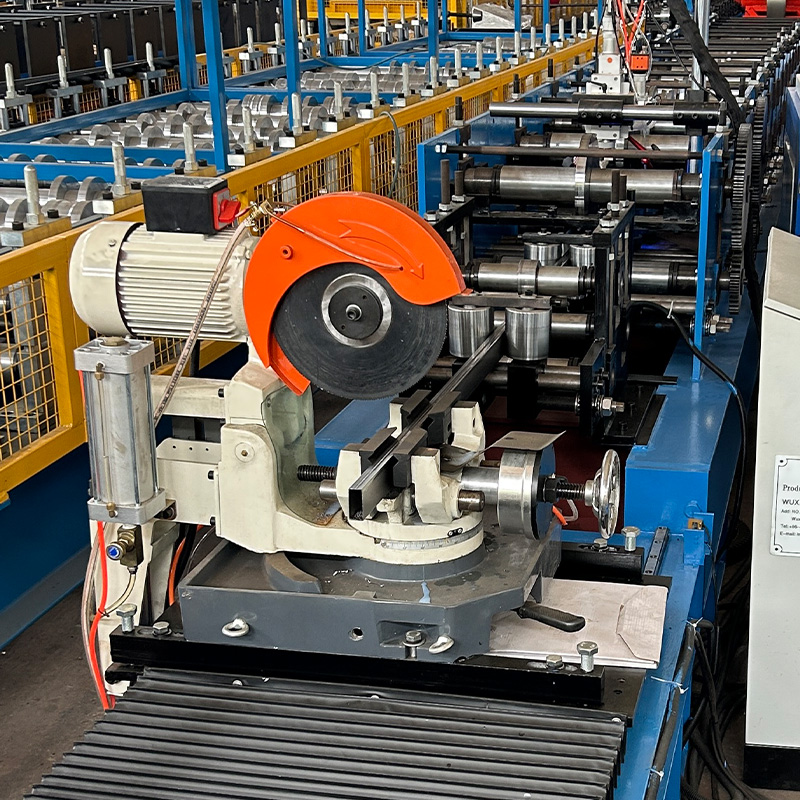
Z Purlin Roll Forming Machine Working Process
The Z purlin roll forming process can be compared to a well-orchestrated ballet, each step crucial in transforming a metal coil into a strong structural component. Let’s delve deeper into the individual acts of this fascinating transformation:
Act 1: Uncoiling – The Grand Entrance
The process begins with the metal coil, resembling a tightly wound roll of silver ribbon. This coil is loaded onto the machine, where powered unwind stands equipped with rollers gently guide and unwind the metal. Brakes strategically placed throughout the system ensure controlled uncoiling, preventing unwanted tension or slack.
Act 2: Feeding – Shaping the Canvas
The unwound metal strip, now a long, flat sheet, enters the feeding stage. Here, it encounters a series of rolling dies, each pair strategically designed to progressively bend the metal. Imagine skilled hands gently folding the sheet, one stage at a time, ensuring there are no unwanted wrinkles or imperfections.
Act 3: Forming – The Master Sculptors
As the metal progresses through the machine, it reaches the forming stage. This is where the magic truly happens. Here, a series of forming rollers, resembling the skilled hands of a sculptor, further bend the sheet incrementally in multiple steps. With each pass, the metal is meticulously shaped closer to its final Z-shaped destiny.
Act 4: Punching – Precision Piercings
The Z-shaped profile is almost complete, but it needs crucial features for assembly. In the punching stage, specialized punch and die sets come into play. These act like precise cookie cutters, punching out bolt holes at specific locations along the formed purlin. This ensures accurate and efficient fastening during construction.
Act 5: Shearing – The Final Cut
The formed Z purlin, now complete with bolt holes, reaches its final transformation stage— shearing. Here, a powerful shear acts like a sharp pair of scissors, cutting the purlin to the predetermined lengths required for the specific project.
Act 6: Counting – The Grand Finale
As the formed Z purlins gracefully exit the production line, a final step ensures quality control. A set counter automatically tallies the number of purlins produced, guaranteeing accurate inventory and production tracking.
The Z purlin roll forming process, through its well-coordinated stages, efficiently transforms a simple metal coil into a versatile and robust structural component, playing a vital role in the construction of buildings and various structures around us.
-
Vineyard Post Roll Forming Machine
-
Auto Size Changeable Sigma Purlin Roll Forming Machine
-
Auto Size Changeable C Z Purlin Roll Forming Machine
-
Auto Size Changeable Z Purlin Roll Forming Machine
-
Auto Size Changeable C U Purlin Roll Forming Machine
-
C Section Bracing Omega Storage Rack Upright Post Roll Forming Machine
-
Steel Box Plate Making Roll Forming Machine
-
Box Beam Steel Roll Forming Machine For Shelf Column
-
Pallet Racking Step Beam P Beam Roll Forming Machine
Equipment Types
Z purlin roll forming machines, the workhorses of the construction industry, play a crucial role in shaping metal sheets into the Z-shaped profiles that support roofs, walls, and floors. However, with different types of roll forming machines available, choosing the right one for your project is essential. Understanding the various types and their strengths will ensure optimal efficiency and successful execution.
1. Automatic vs. Semi-Automatic Machines:
- Automatic: These machines take an entire roll of metal, feed, form, punch, cut, and count purlins entirely independently. Ideal for high-volume production and consistent results, they minimize human intervention and maximize efficiency.
- Semi-Automatic: These machines require manual loading and unloading of metal sheets. While not as fast as their automated counterparts, they offer greater flexibility for smaller projects or production runs with diverse purlin specifications.
2. Single vs. Double Uncoiler Machines:
- Single Uncoiler: Suitable for handling lighter gauge metals and smaller purlin sizes, these machines utilize a single coil unwinder. They are often used in conjunction with semi-automatic roll forming machines and are cost-effective for specific projects.
- Double Uncoiler: These machines employ two unwinders, allowing for continuous production by automatically switching coils when one runs out. Ideal for high-volume production and thicker gauge materials, they reduce downtime and streamline the process.
3. Customization Options:
Several additional factors can influence your choice of roll forming machine:
- Roll forming speed: Higher speeds lead to increased production capacity but might require specialized operators and material handling systems.
- Maximum purlin size: The machine’s capacity to handle the desired purlin width and thickness is crucial.
- Punching and shearing capabilities: Choose machines with the punching and shearing options required for specific bolt hole configurations and purlin lengths.
Choosing the Right Machine:
Selecting the most suitable Z purlin roll forming machine requires considering your project’s specific needs, production volume, budget, and material specifications. By understanding the different types of machines and their functionalities, you can make an informed decision that ensures efficient, cost-effective, and successful Z purlin production. Remember, the right machine can be the key to delivering high-quality Z purlins for your construction projects.
Type | Description |
---|---|
Manual | Basic machines with manual adjustments for each operation |
Semi-automatic | Automated in parts like feeding or punching but needs manual setup changes |
Fully-automatic | Programmable controls for automatic production after initial setup |
Customized | Tailored to produce purlins of various custom lengths, hole patterns and sizes |
Material Feeding
- Hot dip metal coils: These are large rolls of metal, similar to giant metal ribbons, heated in a zinc bath for corrosion protection.
- Thickness: The coils can be anywhere between 0.4 and 2.0 millimeters thick, offering flexibility for different structural needs.
- Weight capacity: The machine can handle coils weighing up to 8 metric tons, which is equivalent to roughly 17,600 pounds.
- Strip widths: Depending on the type of purlin being produced (normal z purlins in this case), the machine can accommodate metal strips ranging from 700 to 1250 millimeters wide (approximately 27.5 to 49 inches).
- Decoiler with automatic feeding system: This is the key player. The decoiler unwinds the metal coil, and the automatic feeding system precisely guides the metal strip into the machine for further processing.
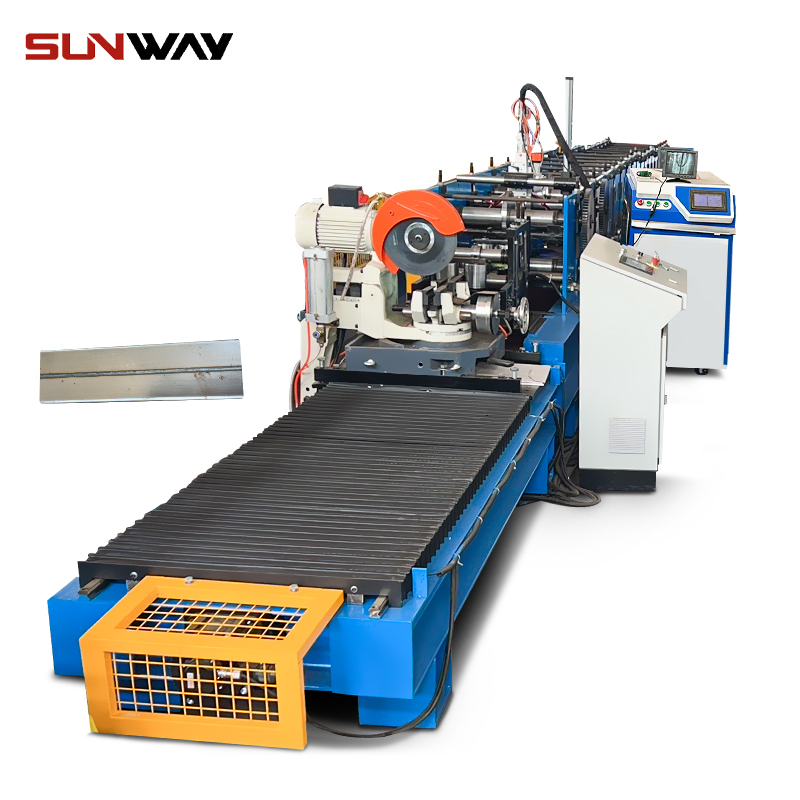
Customization Features
Feature | Details |
---|---|
Profile dimensions | Adjustable forming rolls for custom profile heights and widths |
Hole patterns | Interchangeable precision punch dies for customized hole shapes, spacing |
Length control | Programmable shear for cutting purlins from 2m to 12m long |
Coil width | 700mm to 1250mm strips accommodation |
Packaging | Stackers, strapping as per client requirement |
Suppliers and Price Range
Manufacturer | Location | Price Range |
---|---|---|
ECC Machinery | China | $100,000 – $200,000 |
UNIC Machinery | Taiwan | $150,000 – $300,000 |
Gasparini S.p.A. | Italy | $250,000+ |
Metform | Turkey | $180,000 – $350,000 |
Installation and Operation
Z purlin roll forming machines play a vital role in the construction industry, transforming metal coils into Z-shaped profiles known as purlins. These purlins form the skeletal framework for roofs and walls, providing support for roofing materials, cladding, and other building elements. Installing and operating a Z purlin roll forming machine requires careful planning, technical knowledge, and adherence to safety protocols.
Installation: A Foundation for Success
- Site Preparation: The installation begins with preparing a level and stable foundation for the machine. This ensures smooth operation and prevents vibrations that could affect production quality.
- Offloading and Positioning: Using appropriate lifting equipment, the machine is carefully offloaded and positioned on the prepared foundation. Precise alignment is crucial, often achieved using specialized leveling tools and anchor bolts.
- Electrical and Hydraulic Connections: Qualified electricians and hydraulic technicians connect the machine to the appropriate power supply and hydraulic lines, ensuring they meet the manufacturer’s specifications.
- Roll Set-up: The specific roll set for the desired Z purlin profile is installed. This involves meticulous alignment and adjustment of individual forming rolls to achieve the precise dimensions and profile of the purlin.
- Testing and Calibration: After installation is complete, thorough testing and calibration are conducted to ensure the machine operates smoothly and produces purlins to the required specifications. This involves running trial batches and verifying dimensional accuracy.
Operation: Bringing the Machine to Life
- Coil Loading: The operator loads a metal coil onto the decoiler, the machine component responsible for unwinding the metal strip. Following safety protocols, the operator secures the coil and ensures proper threading of the metal strip through the forming rolls.
- Machine Start-up: After confirming all safety measures are in place, the operator initiates the machine’s operation. The control panel, often featuring a touch screen or buttons, allows for adjustments to production speed, punch and cut-off settings, and other parameters based on the desired purlin specifications.
- Monitoring and Quality Control: During operation, the operator closely monitors the forming process, ensuring the metal strip feeds smoothly and the purlins are produced to the required dimensions and quality. Regular checks for burrs, twists, or other imperfections are crucial.
- Maintenance: Regular maintenance is essential for optimal machine performance and longevity. This includes cleaning the forming rolls, lubricating moving parts, and adhering to the manufacturer’s recommended maintenance schedule.
Maintenance
Task | Frequency | Details |
---|---|---|
Visual inspection | Daily | Check alignments, wear, loose parts |
Sensor calibration | Monthly | Verify lengths, holes as per standards |
Lubrication | Biweekly | Grease bearings and slides |
Blade replacement | As needed | Rotate/replace per 1L km of production |
Machine cleaning | Weekly | Remove metal dust and residue |
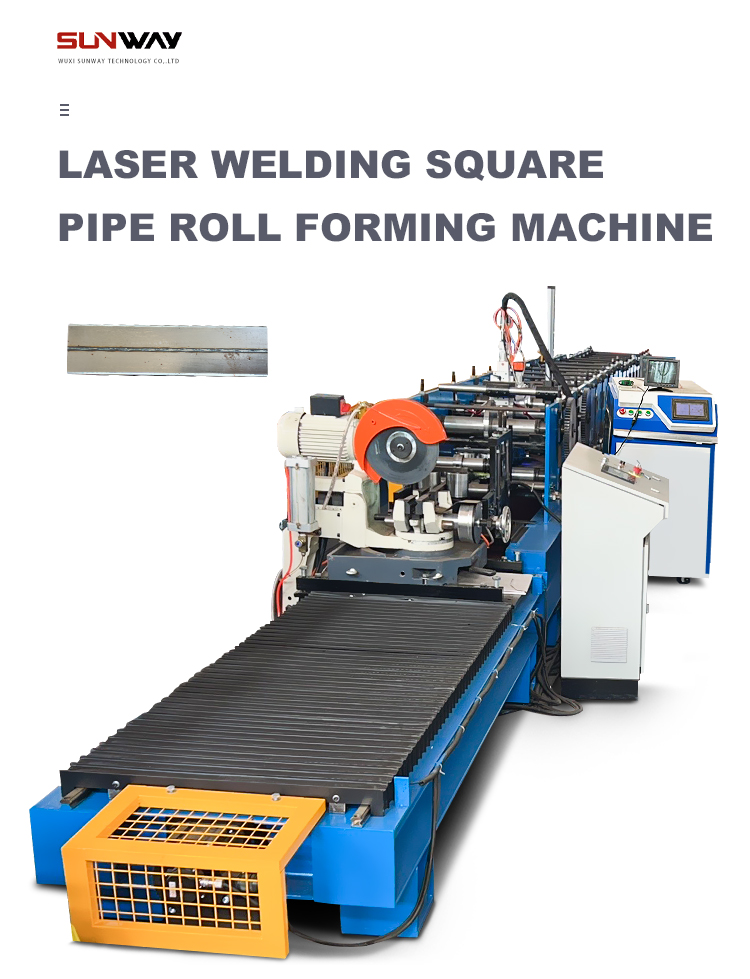
Pros and Cons
Pros | Cons |
---|---|
High production capacity up to 18,000 tons annually | High initial investment cost |
Easy scalability by adding more lines | Regular maintenance for punches and dies is crucial |
Low labor requirement with automation | Limited customization compared to press brakes |
Precision and consistency in forming profiles | Line setup complexity with size changeovers |
Versatility to produce various purlin types | Fixed tooling restricts profile variations |
FAQs
Q: What thickness of coils can be formed in these machines?
A: 0.4mm to 2mm thickness hot dipped galvanized coils are commonly used. Up to 3mm sheets can be formed with heavy duty tooling.
Q: Can the line be switched to make different purlin sizes easily?
A: Some machines offer quick die change designs to alter purlin depths. Major size changes affect line balancing and require modifications.
Q: What is the typical hole size and pitch for purlins?
A: Hole diameter is generally 16-22mm. Lengthwise pitch is mostly 750mm or 1000mm between holes. Pitch and pattern can be varied through customizable tooling.
Q: What factors affect Z purlin roll forming machine prices?
A: Key determinants are speed/output, automation features, precision standards, customization range, coil capacity and tooling quality used. Advanced European equipment sits at the higher end.
Q: Are there protective features for safety purposes?
A: Yes, these machines incorporate safety measures like emergency stops, safety fences, interlocks, overload sensors, and isolation during service and maintenance.