Overview
A warehouse shelf upright rack machine is an essential piece of equipment used in the manufacturing and storage of shelving units, racks, and upright frames. These machines employ roll forming technology to produce sturdy, precision-formed components from flat metal coils or sheets. The resulting products are widely utilized in warehouses, distribution centers, retail stores, and various other commercial and industrial settings for storage and organization purposes.
The Roll Forming Process
Roll forming is a continuous bending operation that transforms flat metal strips into desired profiles or shapes. The process involves feeding a flat metal strip through a series of rollers arranged in a specific pattern. Each roller progressively bends and shapes the metal strip until the desired cross-sectional profile is achieved.
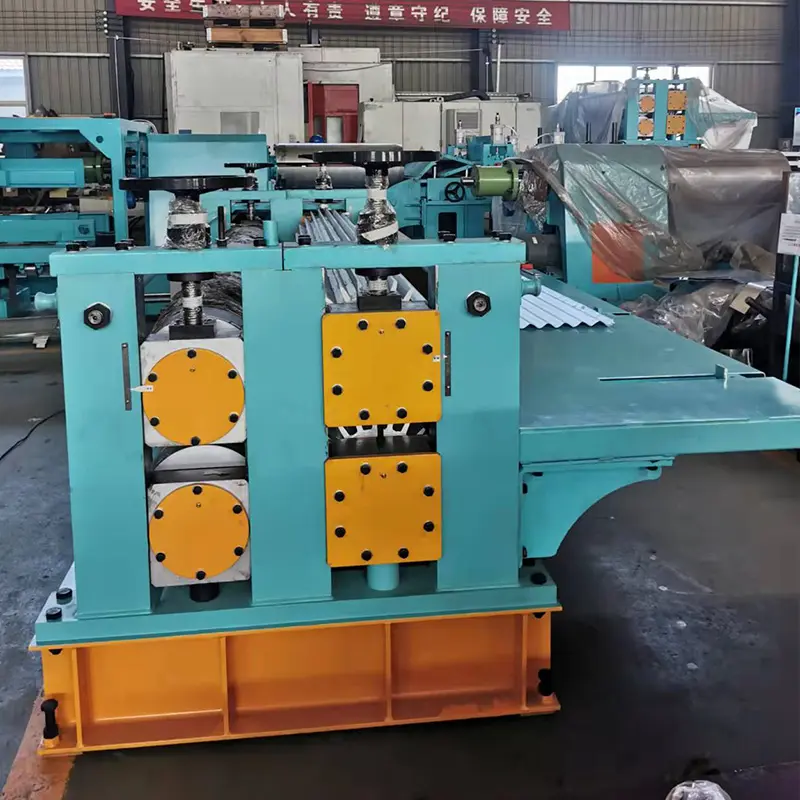
Types of Warehouse Shelf Upright Rack Machines
Machine Type | Description | Typical Materials |
---|---|---|
Light-Duty Machines | Designed for producing lightweight shelving components, suitable for home and small business applications. | Cold-rolled steel, aluminum |
Heavy-Duty Machines | Robust machines capable of forming thick and sturdy upright frames, beams, and load-bearing components for industrial and commercial applications. | Hot-rolled steel, stainless steel |
Multi-Profile Machines | Versatile machines that can produce a range of profiles by adjusting the roller configuration, enabling the production of various shelving components. | Cold-rolled steel, aluminum |
Automated Machines | Fully automated systems with integrated material handling, cutting, and stacking capabilities for high-volume production environments. | Cold-rolled steel, hot-rolled steel |
Working Process
The roll forming process for producing warehouse shelf upright racks typically involves the following steps:
- Decoiling: The flat metal coil or sheet is fed into the machine through a decoiler, which unwinds the material at a controlled rate.
- Straightening: The material passes through a straightening unit to remove any curvature or irregularities before entering the roll forming process.
- Roll Forming: The straightened material is guided through a series of precisely arranged rollers, each applying a specific bend or shape to the metal strip. The rollers are designed to progressively form the desired profile, such as upright frames, beams, or other shelving components.
- Punching and Notching: Depending on the specific component requirements, the formed profile may undergo punching or notching operations to create holes, slots, or other features necessary for assembly and installation.
- Cutting: The continuous formed profile is cut to the desired lengths using a flying shear, press brake, or other cutting mechanisms.
- Finishing: The cut components may undergo additional finishing processes, such as deburring, painting, or galvanizing, depending on the application requirements.
Material Feeding and Forming
Material | Characteristics | Forming Considerations |
---|---|---|
Cold-Rolled Steel | High strength-to-weight ratio, corrosion resistance, versatility | Suitable for light to medium-duty applications, may require additional surface treatment for enhanced corrosion resistance |
Hot-Rolled Steel | Superior strength and durability, suitable for heavy-duty applications | Requires more robust roll forming equipment due to higher material thickness and strength |
Stainless Steel | Excellent corrosion resistance, high strength, aesthetic appeal | Typically more expensive, may require specialized tooling and lubricants during forming |
Aluminum | Lightweight, corrosion-resistant, easy to form | Suitable for light-duty applications, may require specific roller designs due to material softness |
Design and Customization
Warehouse shelf upright rack machines offer a high degree of customization to meet specific application requirements. Manufacturers can tailor the roller configurations, tooling, and machine settings to produce a wide range of profiles, dimensions, and design features. This flexibility allows for the production of upright frames, beams, posts, and other components tailored to the customer’s storage system specifications.
Slicing and Punching
Precise slicing and punching operations are crucial in the production of warehouse shelf upright racks. These processes ensure accurate hole patterns, notches, and cutouts for easy assembly, installation, and integration with other shelving components. Advanced machines often incorporate automated punching and slicing stations, ensuring consistent quality and reducing the risk of errors.
-
Rolling Shutter Slat Roll Forming Machine
-
Highway Guardrail End Terminal Forming Machine
-
Highway U/C Post Roll Forming Machine
-
2 Waves Highway Guardrail Roll Forming Machine
-
3 Waves Highway Guardrail Roll Forming Machine
-
Electrical Cabinet Frame Roll Forming Machine
-
Din Rail Roll Forming Machine
-
Two waves highway guardrail machine
-
Three waves highway guardrail machine
Suppliers and Price Range
The market for warehouse shelf upright rack machines is highly competitive, with numerous suppliers offering varying levels of quality, features, and pricing. Here are some reputable suppliers and their approximate price ranges:
Supplier | Price Range (USD) | Notable Features |
---|---|---|
ACME Roll Form | $50,000 – $250,000 | Customizable roller configurations, advanced control systems, high-precision forming |
RollMatic | $75,000 – $300,000 | Modular design, easy tooling changeover, integrated material handling |
FormTech | $60,000 – $200,000 | Wide range of profile capabilities, robust construction, extensive customization options |
MetalForm Solutions | $80,000 – $350,000 | Automated systems, high-volume production, advanced quality control |
Global Roll Form | $70,000 – $250,000 | Competitive pricing, reliable performance, comprehensive technical support |
Please note that these price ranges are approximate and can vary based on specific machine configurations, customizations, and additional features or accessories.
Installation, Operation, and Maintenance
Aspect | Description |
---|---|
Installation | Proper installation is crucial for optimal machine performance and safety. Manufacturers typically provide detailed installation guides, and some offer on-site installation services. Factors to consider include floor leveling, power requirements, and adequate workspace. |
Operation | Operators should receive comprehensive training on machine controls, safety protocols, and quality assurance procedures. Regular maintenance and adherence to operating manuals are essential for consistent product quality and machine longevity. |
Maintenance | Regular maintenance is vital for ensuring efficient operation and minimizing downtime. This includes routine inspections, lubrication, tool replacements, and adhering to recommended maintenance schedules provided by the manufacturer. |
Choosing a Supplier
When selecting a supplier for a warehouse shelf upright rack machine, it is essential to consider the following factors:
Factor | Description |
---|---|
Reputation and Experience | Research the supplier’s industry reputation, years of experience, and customer feedback to ensure they have a proven track record of delivering high-quality machines and reliable support. |
Product Range and Customization | Evaluate the supplier’s product range and ability to customize machines to meet your specific requirements, such as material handling, automation, and profile versatility. |
Service and Support | Consider the supplier’s technical support, training, and after-sales services, as well as the availability of spare parts and timely maintenance support. |
Quality Assurance | Inquire about the supplier’s quality control processes, certifications, and adherence to industry standards to ensure consistent product quality. |
Pricing and Value | While price is an important factor, it should be weighed against the overall value proposition, including machine capabilities, durability, and long-term operating costs. |
Advantages and Limitations
Advantages | Limitations |
---|---|
High production rates and efficiency | Initial investment in equipment can be substantial |
Consistent product quality and dimensional accuracy | Limited material versatility; typically restricted to metal forming |
Versatility in producing various profiles and designs | Potential noise and environmental concerns during operation |
Automation and integration capabilities | Specialized operator training and maintenance requirements |
Durable and long-lasting equipment | Floor space requirements for larger machines |
Industrial Applications
Warehouse shelf upright racks produced by roll forming machines find widespread applications across various industries, including:
- Warehousing and Distribution: Upright frames, beams, and load-bearing components for pallet racking systems, shelving units, and storage solutions in warehouses and distribution centers.
- Retail and Merchandising: Shelving units, display racks, and point-of-sale fixtures for retail stores, supermarkets, and shopping malls.
- Manufacturing: Storage and organization of raw materials, work-in-progress components, and finished goods in manufacturing facilities.
- Automotive: Storage and handling of automotive parts, components, and accessories in assembly plants and service centers.
- Logistics and Transportation: Cargo handling and storage solutions in shipping terminals, airports, and transportation hubs.
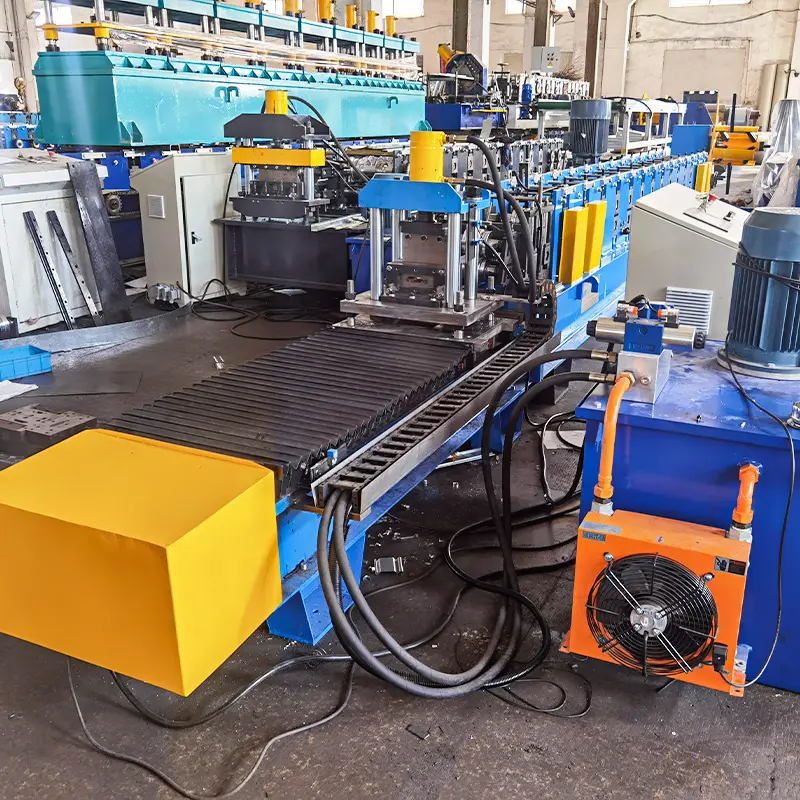
FAQ
Question | Answer |
---|---|
What is the typical production rate of a warehouse shelf upright rack machine? | Production rates can vary significantly based on the machine configuration, material type, and profile complexity. Generally, high-speed machines can produce upwards of 100 feet (30 meters) of formed profile per minute. |
How long does it take to change tooling for different profiles? | The time required for tooling changeovers can range from a few hours to a full day, depending on the machine design and the complexity of the new profile. Some machines feature quick-change tooling systems to minimize downtime. |
What is the typical lifespan of a warehouse shelf upright rack machine? | With proper maintenance and care, roll forming machines can have a lifespan of 10 to 20 years or more. Regular servicing, tool replacements, and adherence to manufacturer recommendations are crucial for maximizing machine longevity. |
Can roll forming machines produce components from materials other than steel and aluminum? | While steel and aluminum are the most common materials used, some advanced roll forming machines can also process other metals, such as stainless steel, copper, and certain non-ferrous alloys, depending on the machine’s capabilities and tooling configuration. |
How do I ensure consistent product quality from a roll forming machine? | Consistent product quality is achieved through a combination of factors, including proper machine setup and calibration, regular maintenance, quality control processes, and operator training. Following manufacturer guidelines and implementing robust quality assurance measures are essential. |