Keel roll forming machines are an essential piece of equipment for manufacturing industries working with sheet metal. This guide provides a comprehensive overview of keel roll forming machines, their applications, types, specifications, suppliers, installation, operation, maintenance, and more.
Overview of Keel Roll Forming Machines
Keel roll forming machines, also known as channel roll forming machines or C-roll forming machines, are used to form sheet metal into C-shaped channels and structural parts like U-channels.
The key features of keel roll forming machines are:
- High production efficiency and speed
- Capability to form complex and customized channel shapes
- Consistent and high-quality finished products
- Low operational costs compared to other forming methods
Keel roll forming utilizes a series of consecutive sets of rollers to gradually bend and shape flat sheet metal stock into the desired channel configuration. Adjustable forming rollers accurately control the material flow and deformation during the continuous forming process.
Keel roll forming machines are available in different configurations and specifications to suit the requirements of various industries such as:
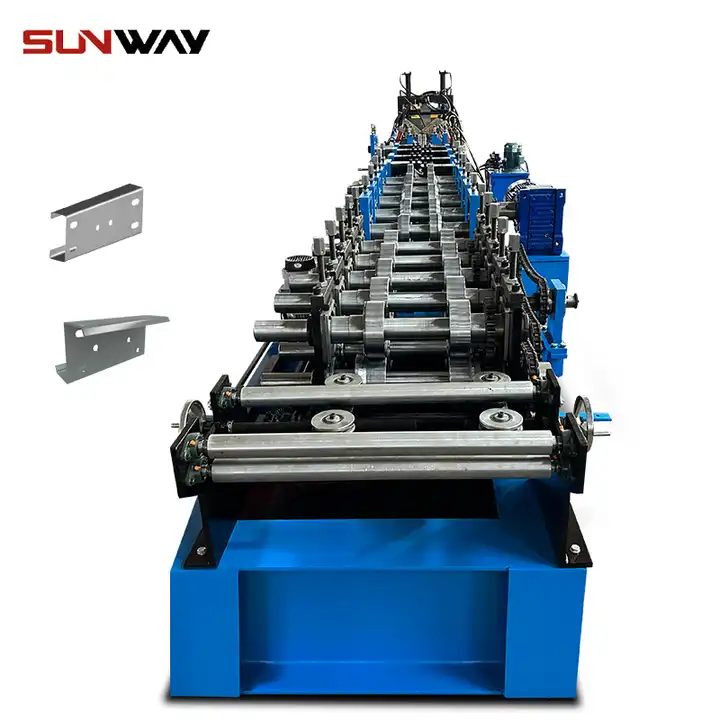
Applications and Uses of Keel Roll Forming Machines
Keel roll forming machines have broad applications across industries:
Industry | Applications |
---|---|
Construction | Roofing, cladding, structural frames, light gauge steel framing |
Automotive | Chassis, brackets, body panels |
Aviation | Aircraft structural parts like stringers and ribs |
Electrical | Cable trays, enclosures, racks |
Furniture | Shelves, storage units, desk frames |
Transportation | Containers, trailers, rail coaches |
In construction, keel roll forming machines produce C and U-channels for:
- Light gauge steel load bearing structures
- Wall studs, roof trusses, solar panel frames
- Roofing and cladding for industrial buildings
- Structural columns, beams, and joints
In automotive and aviation, channels formed by these machines provide:
- Chassis, brackets, and critical structural components
- Interior panels, running boards, trim parts
- Stringers, ribs, rails, and frames
For electrical and telecom applications, channels are used in:
- Cable trays and trunking
- Server and switch enclosures
- Equipment racks and cable ladders
Overall, keel roll forming technology enables lean and agile manufacturing across industries compared to press braking or other alternatives.
Types of Keel Roll Forming Machines
Keel roll forming machines are available in different types based on:
1. Production Speed
- High speed: Up to 120 m/min
- Medium speed: 60-100 m/min
- Low speed: Up to 50 m/min
2. Automation Level
- Manual: Require operators to feed and offload material
- Semi-automatic: Automatically feeds material, manual offload
- Fully automatic: Automated material feed and offload
3. Driveline Configuration
- Direct drive: Each roller has independent motors
- Chain drive: Rollers linked by transmission chains
- Central drive: All rollers driven from one main motor
4. Number of Roller Stands
- 10 stands: For simple C and U channels
- 16 stands: For complex profiles and hems
- 18-24 stands: For high strength channels
Selecting the right keel roll forming machine type depends on the production volume, product shape, level of automation, and budget.
Specifications of Keel Roll Forming Machines
The key specifications and parameters to consider for keel roll forming machines are:
Specifications | Details |
---|---|
Forming Capacity | Thickness up to 3mm, width up to 1200mm |
Forming Speed | Up to 120 m/min |
Roller Size | Diameter 100-150mm, length 400-1000mm |
Roller Material | Alloy steel or carbon steel |
Driveline | Independent motors, chains, or central drive |
Power Consumption | 18-75 kW range |
Control System | PLC with HMI touchscreen |
Frame | Welded steel frame with base |
Machine Size | 8000-30000mm length, 2500-4000mm width |
Weight | 4000-15000 kg range |
The number of roller stands, max strip width, and forming speed determine the production capacity. Construction applications generally require slower speeds but wider widths, compared to automotive parts which require higher speeds but narrower widths.
The roller size, material, and driveline configuration define the forming power. The steel frame provides rigidity during forming. The control system enables setting forming parameters and recipes.
As production requirements go up, higher kW motors, larger rollers, and more roller stands are needed. The machine footprint also increases proportionally.
Keel Roll Forming Machine Suppliers
Some of the leading global suppliers of keel roll forming machines include:
Company | Location | Products |
---|---|---|
Beijing Jingjiang Huaxiang | China | High-end C/U channel and frame forming lines |
Botou Xianfa | China | Roll forming lines for construction industry |
Gasparini S.p.A. | Italy | C/U/L section and profile forming machines |
Formtek | USA | C, U, Z purlin roll forming machines |
Metform International | Canada | Customized roll forming solutions |
Samco Machinery | UK | Light gauge roll forming systems |
Shanghai Whitney | China | High-speed cable tray forming lines |
Ernst Machine | USA | Structural channel forming machines |
Pricing: Basic keel roll forming machines start around $30,000 and go up to $250,000 for high-end integrated production lines. Cost depends on speed, automation level, features, and customization.
Lead Time: Roll forming equipment is generally built to order with deliveries ranging from 2 to 4 months. Readymade machines may be available for faster delivery.
Customers should evaluate suppliers based on industry experience, local support, machine quality/reliability, and capability to deliver integrated solutions.
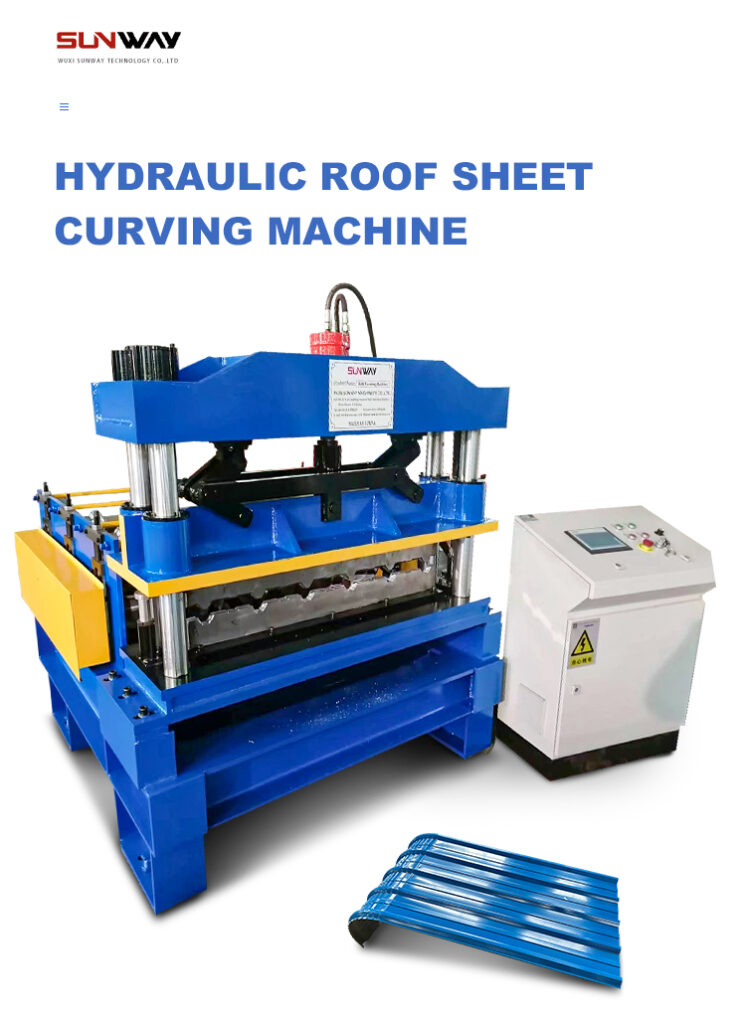
Installing Keel Roll Forming Machines
Proper installation of keel roll forming machines is critical to ensuring forming accuracy, efficiency, and safety. The key steps are:
- Prepare level concrete foundations as per floor plan drawings
- Unload machine parts safely using lift truck or crane
- Assemble frame, ensure squareness using laser alignment
- Mount roller stands per specified layout
- Install driveline, motors, and hydraulics
- Connect electrical, controls, sensors, and safeties
- Anchor machine securely to foundation
- Lubricate moving parts and load tooling
- Verify alignments and clearances
- Trial run without load, then with material
Sufficient space should be provisioned around the rear and sides of the machine for safe material loading, unloading, and transfer. Utilities like power, compressed air must be adequately sized.
Vibration damping pads can be used underneath the machine to minimize floor vibration. Proper grounding, safety guarding, lighting, ventilation and fire safety systems must also be in place.
Operating Keel Roll Forming Machines
Keel roll forming machine operation involves the following key activities:
1. Safety Checks: Verify all guards in place, no obstacles in machine area, functioning E-stops and safety mats.
2. Machine Warmup: Turn on hydraulics and run machines through warmup cycle without load. Verify smooth operation.
3. Parameter Setting: Input product recipe on HMI screen – part width, thickness, line speed, roller pressures.
4. Tooling Setup: Install correct top and bottom roll tooling as per part profile.
5. Material Loading: Prepare sheet metal coil of the required thickness and load on decoiler. Feed strip through leveler and guides into machine.
6. Trial Run: Jog machine and run sample part to validate tooling setup. Check edge quality and make tooling adjustments if needed.
7. Production Run: Initiate automatic run cycle. Monitor line speed, tooling, strip feed, and part quality continuously.
8. Part Unloading: Collect formed parts downstream using lift table or conveyor. Stack and inspect quality.
9. Tooling Changeover: For new part profiles, change top and bottom roll sets per manufacturing sequence plan.
Safety, preventive maintenance, and following SOPs are critical for roll forming operations.
Maintenance of Keel Roll Forming Machines
Regular maintenance improves productivity and extends service life of keel roll forming machines. Key maintenance activities include:
Daily/Weekly:
- Visual inspection of machine condition
- Verify proper lubrication on all moving parts
- Check tooling condition and wear
- Inspect electrical, controls, and hydraulics
- Monitor vibration, temperature, noise
- Cleanup accumulation of dirt, debris, metal fines
Monthly:
- Check anchor bolt torques
- Check chain/gearbox backlash
- Verify hydraulic hose/cylinder condition
- Lubricate machine per schedule
- Validate machine alignments
Yearly:
- Complete machine inspection and service
- Replace worn components like shafts, bearings, sprockets
- Hydraulic system service
- Reapply corrosion protective coatings
- Update control software and electronics
Roll forming machines generate fines and debris. Regular cleaning and preventing accumulation is important. Properly anchoring machines, maintaining alignments, and preventing vibrations also helps extend longevity.
Choosing a Keel Roll Forming Machine Supplier
Choosing the right keel roll forming machine supplier is critical for getting capable and reliable equipment. Key selection criteria include:
Technical Expertise
- Extensive knowledge of roll forming process and machines
- Engineering staff capable of designing optimal solutions
- Experience implementing similar projects
Manufacturing Quality
- Modern and capable machinery to fabricate roll forming lines
- Stringent quality control procedures
- Reliable components sourced from reputable vendors
Customization Capability
- Offer both standard and custom engineered solutions
- Flexibility to modify and optimize designs to requirements
- Integration of peripherals like decoilers, feeders, stackers
Commissioning and Support
- Complete on-site commissioning and operator training
- Responsive after-sales technical support and service
- Local technicians for quick troubleshooting and repairs
Financial Stability
- Financially sound company with sustainable business
- Able to provide warranties and performance guarantees
Evaluating sample products, site visits, and customer references are also valuable in picking the right partner. Consider long-term vendor relationship for ongoing support.
Keel Roll Forming Machine Comparison
Advancements in Keel Roll Forming Technology
Recent advancements that have enhanced keel roll forming machines include:
- Servo-electric drives for precision speed and tension control
- Programmable controls for fast recipe and tooling changeovers
- Automatic lubrication systems for consistent lubrication
- Quick-change tooling systems to reduce setup times
- In-line part cutting for finished cut-to-length parts
- Integrated forming and welding for hybrid C-U channel production
- Robotic part handling for automated load/unload
- Vision systems for quality inspection feedback
- IoT connectivity for remote monitoring and diagnostics
These technologies enable agile and high-quality manufacturing with keel roll forming lines. Companies invest in upgrading equipment with such features to maximize productivity and competitiveness.
Pros and Cons of Keel Roll Forming vs. Alternatives
Compared to press braking, key advantages of keel roll forming machines are:
- Higher production speeds and volumes
- Lower operational costs
- Consistent quality along the length
- Ability to form complex and customized shapes
- Lower tooling costs
Limitations are:
- Higher initial capital investment
- Require separate cutting process
- Size limitations of roll forming lines
Compared to laser cutting, roll forming advantages include:
- Lower equipment cost
- No heat affected zones or finishing needed
- Higher production rates for long length parts
- Lower operational costs
Disadvantages are:
- Limited in complexity of shapes vs laser cutting
- Typically require secondary cutting process
- More floor space needed
Overall, keel roll forming provides lean and agile production for high-volume sheet metal channels and profiles.
Cost Saving Benefits of Keel Roll Forming
Key cost savings with keel roll forming machines:
- Labor: Automated material handling reduces labor
- Tooling: Roll dies last longer than press brakes
- Quality: Consistent quality improves yields
- Speed: Higher production rates improve productivity
- Space: Compact lines maximize facility utilization
- Safety: Reduced handling minimizes accidents
- Energy: Higher efficiency lowers power costs
With its continuous production method, roll forming is often a lower cost manufacturing process compared to alternative approaches.
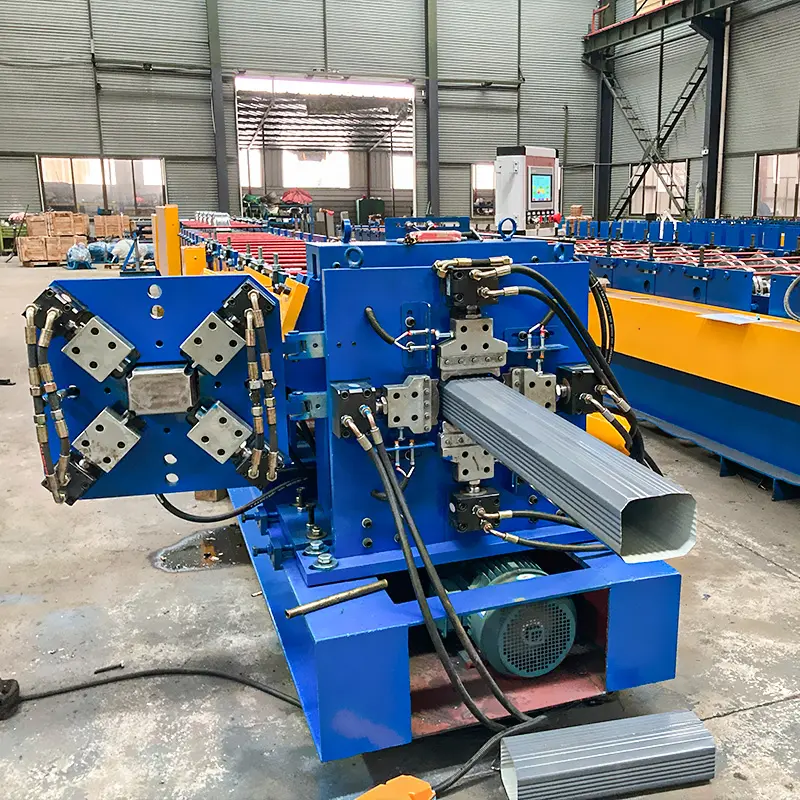
FAQ
What is keel roll forming used for?
Keel roll forming machines are used to form C-shaped and U-shaped structural steel channels from sheet metal coils. Common applications are building construction, automotive chassis, and manufacturing equipment frames.
What thickness of steel can be roll formed?
Keel roll forming machines can typically process steel sheet thickness ranging from 0.5 mm to 3 mm. The maximum thickness depends on the machine’s rolling power and material strength.
What shapes can be formed by keel roll forming?
In addition to C and U channels, these machines can produce complex profiles like furring channels, angles, tubes, rails, panels and open girts. Custom tooling allows flexibility in shapes.
How does keel roll forming work?
It works by passing sheet metal strip through a series of roller dies to gradually shape the material. The rollers bend the flat strip into the desired contour profile based on the roller geometry.
What are the components of a keel roll forming machine?
Main components are decoiler, feeder, pre-cut shear, roller stations, driving system, guide rails, PLC control, and exit tables. High-end systems also integrate punching, welding, and cutting processes.
What is the production rate of keel roll forming machines?
Production speed ranges from 10 to 120 meters per minute depending on part complexity. Typical speeds are 50-80 m/min for common C and U channel forming applications.
How to maintain keel roll forming equipment?
Key maintenance involves lubricating rollers, inspecting tooling wear, checking alignments, changing hydraulic fluids, servicing motors/drives, and cleaning dust/debris. Periodic preventive maintenance improves productivity.
What safety is required for roll forming operations?
Machine guarding, E-stops, safety mats, electrical interlocks, and PPE like gloves/eyewear should be used. Proper material handling and stackout practices are also important. Lockout procedures must be followed during maintenance.
How much does a keel roll forming machine cost?
Cost ranges from $30,000 for basic machines to over $250,000 for large high-end production lines. Price depends on speed, size, automation features, and customization. Used machines are also available.
What factors affect keel roll forming productivity?
Key factors are line speed, setup time, material handling, tooling changeover, maintenance, line downtime, and operating practices. Modernizing equipment and training also improves productivity.
This covers the key aspects of keel roll forming machines. To summarize, it is an efficient technology for high-volume production of structural steel channels and profiles across various industries. With proper machine selection, installation, operation, and maintenance, manufacturers can benefit from lean and agile roll forming production.