Genel Bakış Engel Rulo Şekillendirme Makineleri
Engel rulo şekillendirme makineleri, metal çatı, panel, zemin kaplaması, güneş modülü çerçeveleri ve çeşitli yapısal profiller üretmek için kullanılan yüksek kaliteli rulo şekillendirme sistemleridir. Temel özellikler:
- Büyük bir rulo şekillendirme ekipmanı tedarikçisi olan Engel Machinery Inc. tarafından sunulmaktadır.
- Bobinlenmiş sacdan sürekli profil üretimi.
- Kaburgalar, eğriler, kabartma ve diğer özelliklerle karmaşık profiller oluşturabilir.
- Esnek üretim için merdane takımlarının hızlı değişimi.
- Malzeme taşıma, kesme ve parça istifleme için çeşitli otomasyon seçenekleri mevcuttur.
- Kolay değişimler için reçete depolamalı dokunmatik ekranlı HMI kontrolleri.
- Üreticiler tarafından inşaat endüstrisi için kaplama, panel, çatı kaplama üretmek için kullanılır.
- Kaliteli parçalar için servo merdane ayarı ve pasif merdane teknolojisi.
Engel Rulo Şekillendiricilerde Üretilen Tipik Ürünler
- Metal çatı kaplaması - kenet, yatay, kiremit, sallama
- Duvar panelleri, dış cephe kaplamaları, astarlar
- Yapısal saplamalar, kirişler, kirişler, raylar
- Zemin ve çatı kaplaması
- Güneş modülü çerçeveleri
- Özel mimari profiller
Engel makineleri çok çeşitli standart ve özel yapı bileşenleri üretmektedir.
Temel Özellikler
Parametre | Yetenekler |
---|---|
Şekillendirme genişliği | 18 - 80 inç aralığı |
Malzeme kalınlığı | 26 ga - 3/16 inç |
Şekillendirme hızı | 400 ft/dk'ya kadar |
Geçiş programı | 20 adede kadar şekillendirme standı |
Kontroller | Dokunmatik ekran HMI, servo rulo ayarı |
Takımlama | Hızlı değişim kartuşları, tahrikli standlar |
Güvenlik | Koruma paketleri, ışık perdeleri |
Engel, birçok standart modelin yanı sıra özel mühendislik çözümleri de sunmaktadır.
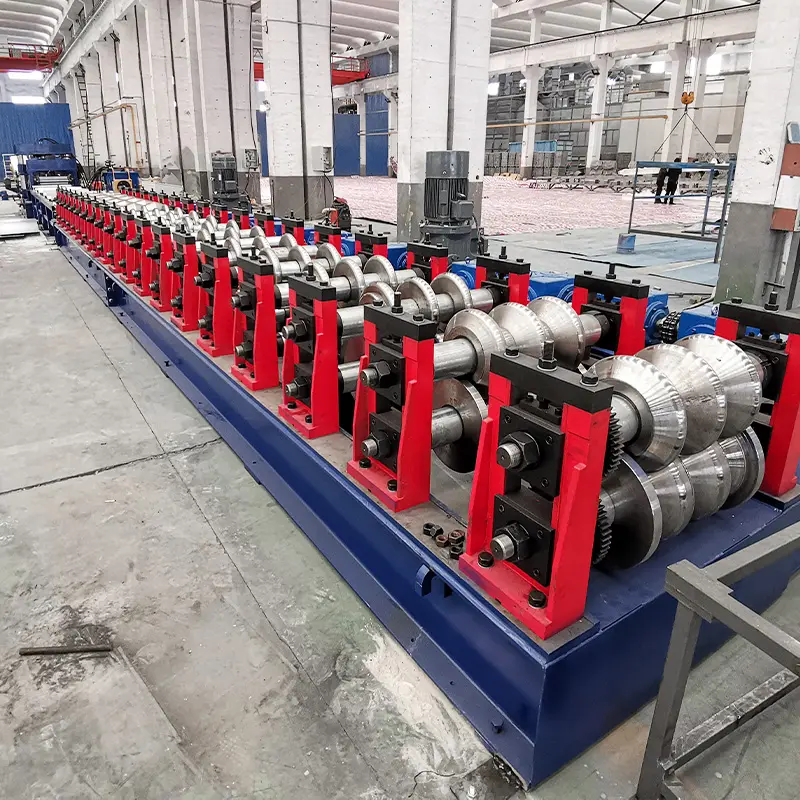
Engel Rulo Şekillendirici Nasıl Seçilir
Bir Engel rulo şekillendirme sistemi seçerken temel faktörler:
- Üretim gereksinimleri - İstenen saatlik çıktı oranı, bobin genişlikleri / ölçüleri, üretilecek profillerin karmaşıklığı.
- Otomasyon ihtiyaçları - Manuel veya motorlu malzeme taşıma, parça kesme ve istifleyicilerin gerekli olup olmadığını belirleyin.
- Takımlama - Engel'den istenen profiller için standart takım paketlerinin kullanılabilirliğini değerlendirin.
- Kontroller - Reçete depolama, veri kaydı vb. gibi gerekli işlevleri belirleyin.
- Teknik Destek - Engel kurulum desteği, eğitim ve servis sağlar. Bölgesel kullanılabilirliği sağlayın.
- Özelleştirme - Engel, özelleştirilmiş özellikler, güvenlik eklentileri ve enstrümantasyon sağlayabilir.
- Genişletilebilirlik - Gelecekte kapasitesi artırılabilecek ve ilave geçişler eklenebilecek bir sistem seçin.
Üretim gereksinimlerinize göre uyarlanmış bir sistem elde etmek için ekipman belirlerken Engel uygulama mühendisleriyle birlikte çalışın.
Rulo Kalıp Tasarım İlkeleri
Doğru merdane takımı tasarımı, bir Engel makinesinde verimli bir şekilde kaliteli merdaneyle şekillendirilmiş parçalar üretmenin anahtarıdır. Tasarım yönergeleri:
- Malzeme akışı için parça profillerini optimize edin ve sertlik katmak için nervürleri, dikişleri ve kabartmaları sertleştirin.
- İncelme, yırtılma veya çatlama olmadan malzemeyi şekillendirme boyunca yönlendirmek için mühendis rulo konturları.
- Malzemede indüklenen gerilmeleri kontrol etmek için şekillendirme pasolarını ve merdane penetrasyonunu dikkatlice tasarlayın.
- Eşit büküm ve hassas toleranslar sağlamak için rulo çaplarını üstten alta eşleştirin.
- Sürtünmeyi azaltmak için merdaneleri yağlayın - sert alaşımlar için metal akışını destekleyen üretan gibi malzemeler kullanın.
- Daha büyük yarıçaplı bükümler kullanarak gerilimi yoğunlaştıran keskin büküm açılarını azaltın.
- Kurulum ve değişimlere yardımcı olmak için takım çizimlerini geçiş sıraları ve referanslarla iyice açıklayın.
Sağlam üretim için en uygun merdane tasarımlarına ve dizilimlerine ulaşmak için Engel takım mühendisleriyle birlikte çalışın.
Engel Roll Former Kurulumu için Hazırlık
Yeni bir Engel rulo şekillendirme sisteminin gelişi ve kurulumu için hazırlık yapmak:
- Gerekli elektrik beslemesini ayarlayın - voltajı ve kapasiteyi onaylayın. Bağlantıları kurun.
- Makinenin etrafında güvenli çalışma için yeterli açıklıkta alan sağlayın. Parça konveyörleri için izin verin.
- Gerekli tüm izinleri alın - bina, elektrik, yerel kanunlar.
- Yükleri taşımak için Engel spesifikasyonlarına göre rijit temeller hazırlayın.
- Bileşenleri kamyonlardan indirmek için vinçler, forkliftler, zincirler vb. kaldırma ekipmanları bulundurun.
- Kurulum, hizalama, kablolama ve hata ayıklama için kalifiye teknisyenleri planlayın.
- Elde bulundurmak için ilk takım paketlerini ve malzeme bobin stoğunu sipariş edin.
Kapsamlı planlama, ekipman sahaya ulaştığında gecikmeleri ve sorunları en aza indirir.
En İyi Kurulum Uygulamaları
Engel rulo şekillendiricileri monte ederken önerilen uygulamalar:
- Uygun kaldırma cihazlarını kullanarak bileşenleri kamyonlardan dikkatlice indirin. Zarar vermekten kaçının.
- Doğru montaj sırası ve hizalamalar için Engel belgelerini takip edin.
- Elektrik teknisyenlerinin güç bağlantılarını ve kontrol kablolarını elektrik baskılarına göre kurmasını sağlayın.
- Makineyi zemine sıkıca sabitleyin - şekillendirme dinamik yüklere neden olur.
- Makineye güç vermeden önce tüm güvenlik koruyucularını takın. Sıkışma noktalarını ortadan kaldırın.
- Çalıştırmadan önce sürücülerde doğru jog yönünü doğrulayın. Gerektiğinde tersine çevirin.
- Doğru çalışmayı onaylamak için makineyi kademeli olarak çalıştırın ve çevrim yapın.
- Takım geçişlerinde hata ayıklamak için girişten çıkış ucuna kadar merdane ayarlamaları yapın.
- Sadece başarılı devreye alma denemeleri hattı kanıtladıktan sonra üretim için serbest bırakılır.
Kalifiye personel tarafından yapılan dikkatli kurulum, sorunların önlenmesine yardımcı olur ve sorunsuz bir başlatma sağlar.
Rulo Şekillendirme Operasyonu ve Kalite Kontrol
Engel rulo şekillendiriciyi optimum kalitede güvenli bir şekilde çalıştırmak için:
- Hat hızını, ağ hizalamasını, rulo yüklerini ve diğer değişkenleri sürekli olarak izleyin. Gerektiğinde ayarlamalar yapın.
- Go/no-go göstergelerini kullanarak şekillendirilmiş parça boyutlarını sık sık kontrol edin. Tolerans dahilinde olduğundan emin olun.
- Giriş bobini parametrelerinin Engel tavsiyelerine uygun olduğundan emin olun - kalınlık, genişlik, gerdirme, yağlama vb.
- Parçalarda çizikler oluşmadan önce aşınmış rulo segmentlerini derhal değiştirin.
- Planlı üretim duruşları sırasında önleyici bakım için duruş süreleri planlayın.
- Bir hata oluştuğunda çalışmayı durduran programlanmış güvenlik durdurucuları ve ışık perdeleri uygulayın.
- Sürekli yüksek hızda çalışmayı desteklemek için yağlama seviyelerini kontrol edin ve gerektiğinde rezervuarları doldurun.
- Operatörlerin tüm prosedürler ve güvenlik önlemleri konusunda uygun şekilde eğitildiğinden emin olun.
Tutarlı kaliteli çıktı, sürekli izleme, eğitim ve kanıtlanmış parametreler dahilinde disiplinli çalışma gerektirir.
Yaygın Rulo Şekillendirme Hataları ve Düzeltmeleri
Kusur | Olası Nedenler | Düzeltmeler |
---|---|---|
Burrs | Yuvarlanma hasarı, ağın yanlış hizalanması | Ruloları giydirin veya değiştirin, kılavuzları yeniden hizalayın |
Dalgalı bölümler | Yanlış merdane ayarı | Rulo geçişlerini kademeli olarak yeniden açın |
Büküm | Paralel olmayan üst/alt rulolar | Alt silindiri diğerlerine paralel olarak yeniden hizalayın |
İnceltme | Aşırı rulo penetrasyonu | Rulo geçişlerini gevşetin, şim boşlukları |
Gevşek kıvrım | Tutarsız rulo ayarı | Problemli geçişlerin kademeli olarak yeniden ayarlanması |
Çizikler | Rulolarda kumlanma, ağ kirliliği | Silindirleri temizleyin, giriş malzemesi yüzeyini iyileştirin |
Parça özelliklerini yakından gözlemleyin ve kusurlar giderilene kadar sistematik ayarlamalar yapın.
Rulo Şekillendirici Güvenlik Hususları
Engel rulo şekillendiricileri kullanırken önemli güvenlik uygulamaları:
- Tehlikeler ve uygun prosedürler hakkında kapsamlı operatör eğitimi.
- Tüm sıkışma noktaları, dişliler, bobinler etrafında yeterli koruma. Açıkta kalan tehlikelerden kaçının.
- Bakım faaliyetleri ve sıkışmaları gidermek için kilitleme/etiketleme. Makinenin enerjisini kesin.
- Sıkı giysiler, eldivenler, gözlükler ve işitme koruması dahil olmak üzere KKD gerekliliklerini uygulayın.
- Makinenin etrafındaki güvenlik bölgelerini açıkça işaretleyin. Tüm erişim kurallarına uyun.
- Hat sıkışmaları gibi güvenli olmayan durumlar için otomatik güvenlik durdurmaları uygulayın.
- Şekillendirme alanındaki hava kalitesini iyileştirmek için gerekirse toz toplama.
- Riskleri proaktif olarak belirlemek için düzenli güvenlik denetimleri - düzeltici eylemlerin belgelenmesi.
Güvenliğe öncelik vermek çalışma koşullarını iyileştirir ve yaralanmaları önler. Tüm yasal gerekliliklere uyun.
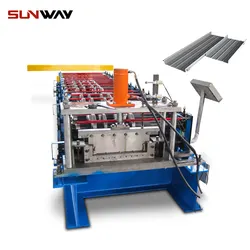
Hakkında SSS Engel Rulo Şekillendirme Makineleri
S: Engel makinesinde ne tür metaller rulo şeklinde şekillendirilebilir?
C: Çelik, paslanmaz çelik, alüminyum, bakır alaşımları dahil olmak üzere çoğu sünek metal. Daha yumuşak, daha ince malzeme en kolay şekilde oluşur.
S: Yeni bir profil için takım hazırlamak ne kadar sürer?
C: Hızlı değişim makinelerinde tipik kurulum süresi, geçiş hata ayıklama dahil 1-3 saattir. Daha zor profiller daha uzun sürebilir.
S: Hangi kalınlık aralığında rulo şekillendirilebilir?
C: Standart Engel modelleri 0,5 mm ila 4,75 mm (26 ga ila 3/16") kalınlıklara uygundur. Bu aralık dışında özel modeller mevcuttur.
S: Maksimum üretim hızını belirleyen faktörler nelerdir?
C: Malzeme kalınlığı/sertliği, parça karmaşıklığı, mevcut beygir gücü ve istenen kalite maksimum sabit hızı belirler.
S: Rulo şekillendirilmiş parçalar nasıl boyuna kesilir?
C: Servo kumandalı kesme presleri veya testereler parçaları önceden programlanmış aralıklarla otomatik olarak boyuna keser. 65 ft'ye kadar uzunluklar mümkündür.
S: Rulo şekillendirme ile hangi toleranslar mümkündür?
C: Bakımı düzgün yapıldığında, haddede şekillendirilmiş parçalar tipik olarak ±0,5 mm (±0,02 inç) civarında boyutsal toleranslara sahiptir. Daha dar toleranslar zorlaşır.
S: Merdane takımları ne sıklıkla değiştirilmelidir?
C: Yüksek üretimli 24 saatlik operasyonlar için ortalama 1-3 ayda bir. Hızlı değiştirilen takımlar, değiştirme için duruş süresini azaltır.
S: Hangi güvenlik önlemleri en önemlisidir?
C: Eğitim, koruma, kilitleme, işaretli güvenlik bölgeleri, toz toplama, kilitler, değişiklik kontrolü, KKD ve periyodik denetim.
S: Özel rulo şekillendirilmiş profiller yapılabilir mi?
C: Evet, Engel mühendisleri uygulama gereksinimlerine göre özel standart dışı parçalar üretmek için özel takım paketleri tasarlayabilir.