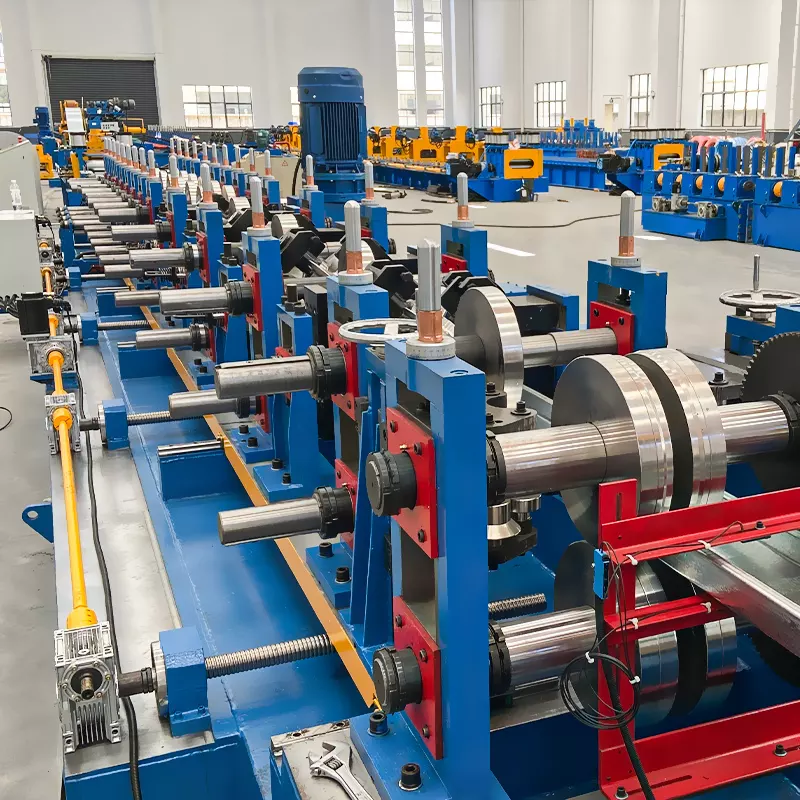
Purlin roll forming is a cost-effective and efficient manufacturing process used to create structural components that support the roofs of buildings and other structures. It involves continuously bending metal into the desired shape using a series of rollers, resulting in a product with consistent dimensions and tight tolerances. The versatility of purlin roll forming allows for the creation of custom-designed solutions for a wide range of applications.
Custom-designed solutions are essential for meeting the unique needs of various projects. Purlin roll forming offers the flexibility to create custom-designed solutions tailored to meet the specific requirements of a given application. This versatility is due to the wide range of materials that can be used, as well as the ability to produce purlins in different shapes, sizes, and configurations. Whether it is a large commercial building, an agricultural structure, or an infrastructure project, purlin roll forming can provide custom-designed solutions for a variety of applications.
In this post, we will explore the versatility of purlin roll forming for custom design solutions. We will discuss the types of purlins that can be created, the importance of material selection, the advantages of purlin roll forming. By understanding the versatility of purlin roll forming, we can appreciate its importance in meeting the unique needs of various projects.
Types of Purlins
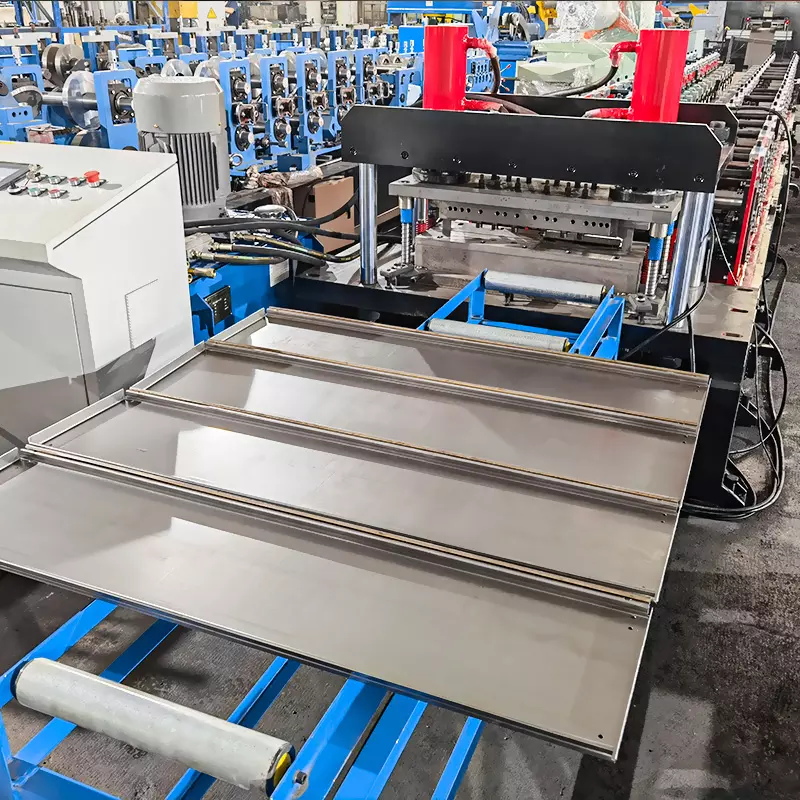
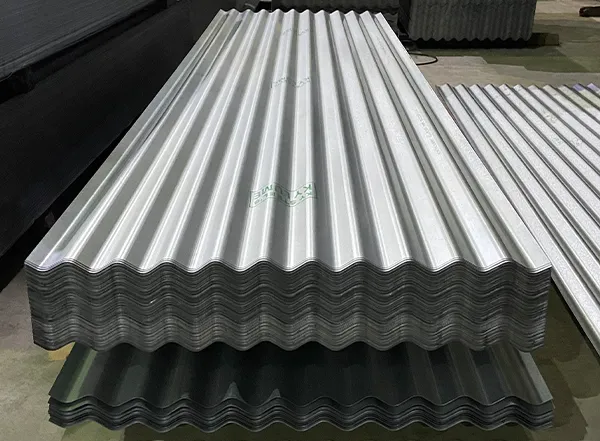
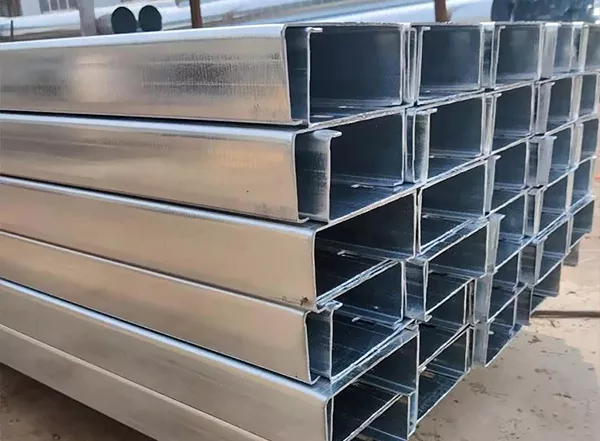
There are two primary types of purlins that can be created using roll forming: C and Z purlins. Both types of purlins are used to support the roofs of buildings and other structures, but they have some key differences.
C purlins have a unique shape that resembles the letter “C.” They are commonly used in structures with single-sloped roofs or as headers over doors and windows. C purlins are usually installed with the open side facing up, and they are often used in conjunction with girts to provide additional support for wall cladding.
Z purlins, on the other hand, have a shape that resembles the letter “Z.” They are commonly used in structures with pitched roofs and are installed with the open side facing down. Z purlins are often used in conjunction with sag rods to provide additional lateral stability to the roof structure.
The advantages of C purlins include their simplicity and versatility. They are easy to install and can be used in a variety of applications. However, they may not be suitable for larger structures that require more support.
The advantages of Z purlins include their strength and stability. They are well-suited for use in larger structures and can provide additional lateral stability to the roof structure. However, they may be more challenging to install and may require more complex connections.
Overall, the choice between C and Z purlins will depend on the specific requirements of the project. The design and construction team should consider factors such as the size and shape of the structure, the load capacity required, and the overall budget when selecting the appropriate purlin type.
Advantages of Purlin Roll Forming
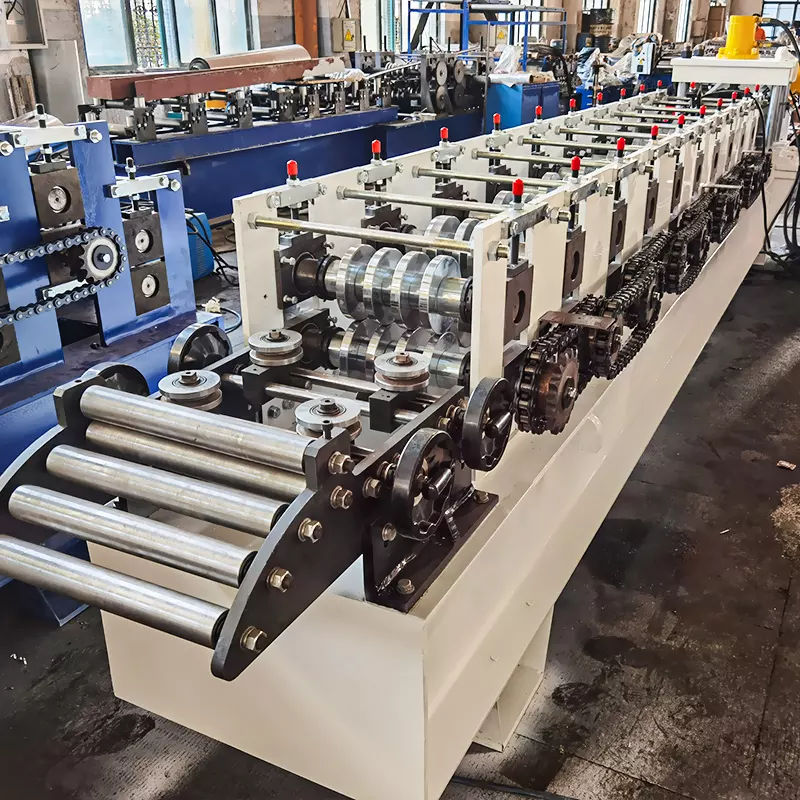
Purlin roll forming offers several advantages for custom design solutions, making it a popular choice for the creation of structural components for buildings and other structures. Here are some key advantages of purlin roll forming:
- Versatility: Purlin roll forming is a versatile process that can be used to create custom-designed solutions for a wide range of applications. By allowing for the creation of purlins in different shapes, sizes, and configurations, as well as the ability to use a variety of materials, roll forming provides greater flexibility for meeting the unique requirements of a given project.
- Cost-Effectiveness: Purlin roll forming is a cost-effective manufacturing process. It is capable of producing high volumes of components quickly and efficiently, which can help reduce labor costs and increase output. Additionally, the ability to use a variety of materials can help reduce material costs by allowing the project team to select the material that best suits the project’s requirements.
- Consistent Dimensions and Tight Tolerances: Roll forming produces high-quality components with consistent dimensions and tight tolerances. This is because the process involves the continuous bending of metal into the desired shape using a series of rollers, resulting in a product with consistent dimensions and tight tolerances.
- Strength and Durability: Purlin roll forming produces components that are strong and durable, making them ideal for use in structural applications. The ability to use a variety of materials, including high-strength steel, ensures that the finished product is capable of withstanding the stresses and strains of its intended use.
- Automation: Roll forming can be easily automated, which can further increase efficiency and reduce costs. Automated systems can be used for material handling, feeding, and quality control, minimizing manual labor and maximizing output.
In summary, purlin roll forming offers several advantages for custom design solutions, including versatility, cost-effectiveness, the ability to produce high-quality components with consistent dimensions and tight tolerances, strength and durability, and the potential for automation. These advantages make purlin roll forming an excellent choice for the creation of custom-designed structural components for a wide range of applications.
Custom Design Solutions of purlin roll forming
Purlin roll forming is a versatile process that can be used to create custom-designed solutions for a wide range of applications. Custom-designed solutions are essential for meeting the unique needs of various projects. Roll forming can provide these solutions by allowing for the creation of purlins in different shapes, sizes, and configurations, as well as the ability to use a variety of materials.
For example, if a project requires a specific shape or size of purlin that is not readily available, roll forming can be used to create custom purlins that meet these requirements. Roll forming can also be used to create custom-designed solutions for challenging or complex projects, such as curved or tapered roofs.
Custom-designed solutions are important because they ensure that the finished product meets the specific requirements of the project. By using roll forming to create custom-designed purlins, the project team can ensure that the components are precisely tailored to the structure and its intended use. This can lead to better performance, improved safety, and longer-lasting results.
Roll forming can also help meet the unique requirements of a given project by providing greater flexibility in material selection. Roll forming can be used with a wide range of materials, including steel, aluminum, and copper, among others. This means that the project team can select the material that best suits the project’s requirements in terms of strength, durability, and corrosion resistance.
In summary, roll forming can be used to create custom-designed solutions for a wide range of applications. Custom-designed solutions are important because they ensure that the finished product meets the specific requirements of the project, leading to better performance, improved safety, and longer-lasting results. Roll forming provides greater flexibility in material selection, allowing the project team to select the material that best suits the project’s requirements.
In conclusion, purlin roll forming is a versatile and cost-effective manufacturing process that can create custom-designed solutions for a variety of applications. By using this process, it is possible to produce high-quality purlins with consistent dimensions and tight tolerances, making them ideal for use in structural applications. Purlin roll forming also offers greater flexibility in material selection, allowing project teams to select the material that best suits the project’s requirements. With its advantages of cost-effectiveness, automation potential, and ability to create custom designs, purlin roll forming is an excellent choice for creating custom-designed structural components for a wide range of applications.