A steel silo roll forming machine is equipment used to produce cylindrical or conical steel silos for storage of bulk materials. It creates steel coils by feeding a flat steel strip through a series of roller dies to continuously form the sheet into rounded profiles.
Key Details of Steel Silo Roll Forming Machine
Towering above fields and industrial landscapes, steel silos are testaments to human ingenuity and efficient storage solutions. But have you ever wondered how these metallic giants are born? The answer lies in a remarkable machine – the steel silo roll forming machine, a powerhouse of metalworking responsible for shaping the core component of these structures. Let’s delve into the key details that make this machine tick.
At its heart lies the uncoiler, a hydraulic marvel that unwinds massive coils of steel, feeding them like a continuous ribbon into the forming process. These coils, typically made of galvanized steel or high-strength alloys, come in varying thicknesses depending on the silo’s intended purpose.
The magic truly happens at the forming stations. Imagine a series of precisely machined rollers, each meticulously designed with unique grooves and profiles. As the steel sheet passes through these stations, it undergoes a gradual transformation. Each roller bends the metal in specific increments, creating the signature corrugated pattern that defines a silo wall. This pattern not only adds strength and rigidity but also enhances the overall surface area, maximizing storage capacity.
But the forming process doesn’t stop at just shaping the metal. Additional stations might be incorporated to punch holes for bolting the segments together, create interlocking edges for seamless assembly, or even add reinforcing ribs for extra support in demanding environments.
The entire operation is a concerto of coordinated motion. The feeding and leveling mechanisms work tirelessly to ensure the sheet enters the rollers perfectly aligned, preventing imperfections and ensuring a smooth forming process. Hydraulics provide the necessary force to bend the metal without compromising its structural integrity. And finally, a flying cutting unit chops the formed sheet into individual segments, ready to be assembled into the silo wall.
The beauty of the steel silo roll forming machine lies in its versatility. By adjusting the thickness of the sheet, the type of steel used, and the profiles of the rollers, the machine can cater to a wide range of silo applications. From storing delicate food grains to withstanding harsh outdoor conditions, this machine adapts to diverse needs, making it a valuable asset in various industries.
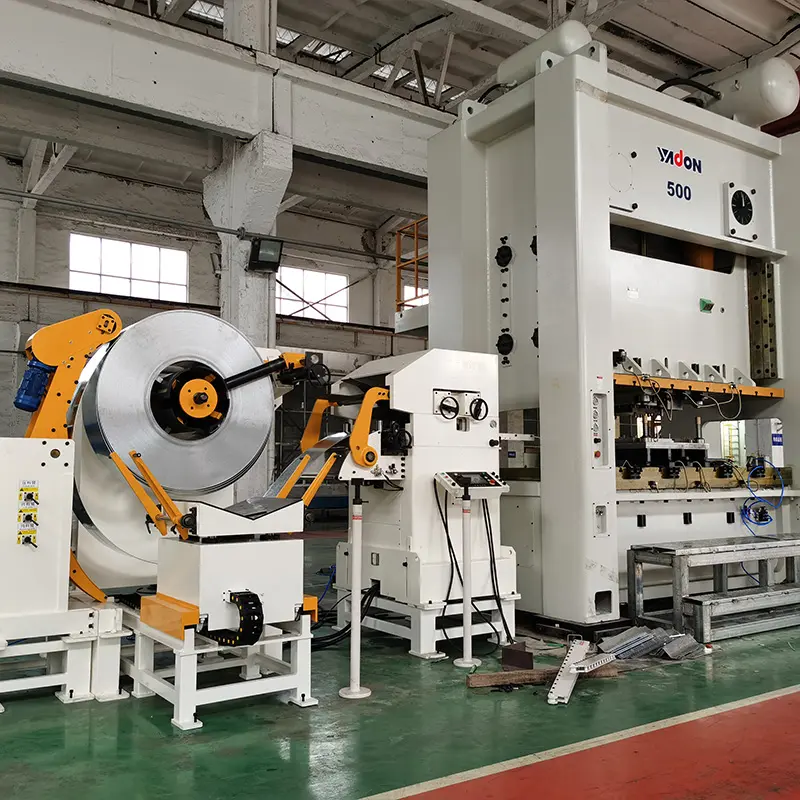
Working Process
Imagine a giant metal cylinder reaching for the sky, its corrugated surface gleaming in the sun. This, my friend, is a steel silo, a marvel of modern engineering used to store everything from grain and cement to plastic pellets and wood chips. But have you ever wondered how these towering titans are born? The answer lies in a remarkable machine – the steel silo roll forming machine.
This powerhouse of metalworking operates like a tireless sculptor, continuously shaping flat sheets of steel into the curved segments that make up a silo’s wall. The process begins with a massive coil of steel, unfurling like a giant ribbon onto a hydraulic uncoiler. This uncoiled sheet then enters a series of precisely positioned rollers, each meticulously designed to bend the metal in specific increments.
Think of these rollers as the sculptor’s tools – each with a unique groove or profile. As the sheet passes through them, it’s gradually transformed, acquiring the signature corrugated pattern that provides strength and rigidity to the silo wall. But the roll forming doesn’t stop there. Additional stations may punch holes for bolts, create interlocking edges, or even add reinforcing ribs, depending on the silo’s specific needs.
The entire process is a ballet of coordinated motion. The sheet glides smoothly through the rollers, guided by feeding and leveling mechanisms that ensure perfect alignment. Hydraulics power the operation, providing the necessary force to bend the metal without compromising its integrity. And at the end of the line, a flying cutting unit chops the formed sheet into individual segments, ready to be assembled into the silo wall.
But the steel silo roll forming machine is more than just a metal bender. It’s a testament to human ingenuity, a machine designed to meet the demands of diverse industries. By adjusting the thickness of the sheet, the type of steel, and the roll profiles, the machine can produce silo walls for a wide range of applications, from storing delicate food grains to withstanding the harsh elements in outdoor environments.
Equipment Comparison
Type | Suitable For | Max. Speed | Precision | Automation |
---|---|---|---|---|
Manual | Small volumes | Slow | Low | Minimal |
Semi-automatic | Medium volumes | Moderate | Medium | Limited |
Fully-automatic | High volumes | High | High | Full |
Components of Steel Silo Roll Forming
The main components include:
Uncoiler – Feeds raw steel coil into system
Guiders – Guide strip alignment
Roller dies – Gradually form coil into circular section
Welder – Join formed edges together
Cutter – Cut steel tube/pipe to length
Control panel – Adjust parameters and automate process
Additional parts: hydraulic unit, chiller, base frame, protective housing
-
Highway Guardrail End Terminal Forming Machine
-
Highway U/C Post Roll Forming Machine
-
2 Waves Highway Guardrail Roll Forming Machine
-
3 Waves Highway Guardrail Roll Forming Machine
-
Vineyard Post Roll Forming Machine
-
Auto Size Changeable Sigma Purlin Roll Forming Machine
-
Auto Size Changeable C Z Purlin Roll Forming Machine
-
Auto Size Changeable Z Purlin Roll Forming Machine
-
Auto Size Changeable C U Purlin Roll Forming Machine
Working Principle
The working principle involves:
- Material Feeding – Steel coil loaded onto powered uncoiler which feeds strip into machine
- Forming – Strip passes through progressive dies to bend sheet in stages into circular profile
- Welding – Longitudinal edges welded together to form tube/pipe
- Sizing – Final sizing rollers calibrate diameter precisely
- Cutting – Tube/pipe cut to required length by built-in cutter
- Exit – Formed steel silo components exit system for storage/transport
Design and Customization
- Diameter – Available from 300mm to 3000mm or more
- Length – Up to 15m long silo sections
- Material – Galvanized steel, stainless steel or carbon steel coils
- Shape – Round, oval, square or custom profiles
- Thickness – 0.3mm to 2.5mm thick coils
- Modular – Additional functions like corrugation, embossing possible
Customization offered for non-standard tube sizes, lengths, materials.
Key Suppliers and Price Range
Supplier | Location | Price Range |
---|---|---|
Furukawa | Japan | $$ |
Gasparini | Italy | $$$ |
Joubert | South Africa | $$ |
Technocraft | India | $ |
Approximate price range from $50,000 to $250,000 based on automation and output.
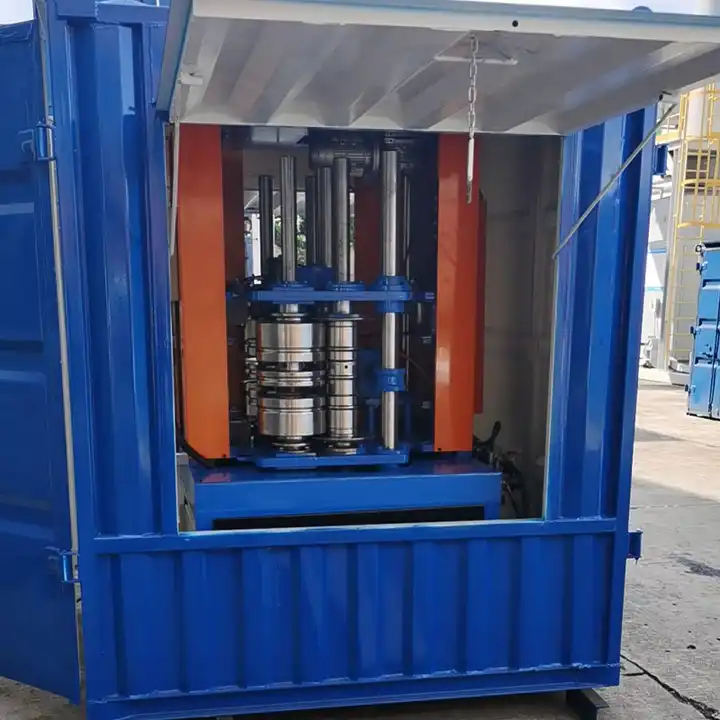
Installation, Operation and Maintenance
Process | Guidelines |
---|---|
Installation | Level ground; Anchor bolts; Electrical, hydraulic connections |
Operation | Control panel instructions; Safety procedures; Raw material loading/unloading |
Maintenance | Lubrication schedule; Inspect/replace wear items; Check alignments; Calibrate sensors |
Personnel training recommended by supplier.
Choosing a Steel Silo Roll Forming Machine
Consider key factors:
- Production volume – Match speed/automation to required output
- Product dimensions – Confirm machine capacity meets size needs
- Raw material – Specify type and thickness of steel coil
- Power supply – Ensure adequate electricity availability
- Budget – Weigh capital cost versus production efficiency
- Expandability – Consider potential future increases in output
- Vendor reputation – Research quality and reliability record
- Warranties & support – Confirm after-sales service terms
Advantages of Steel Silo Roll Forming
- Flexibility – Adjustable to varying production needs
- Cost-effectiveness – Economies of scale in continuous production
- Consistency – Precise forming and dimensional tolerance control
- Speed – High output up to 40 meters per minute
- Simplicity – Compact footprint; easy to operate and maintain
- Automation – Reduced labor by integrating robotic elements
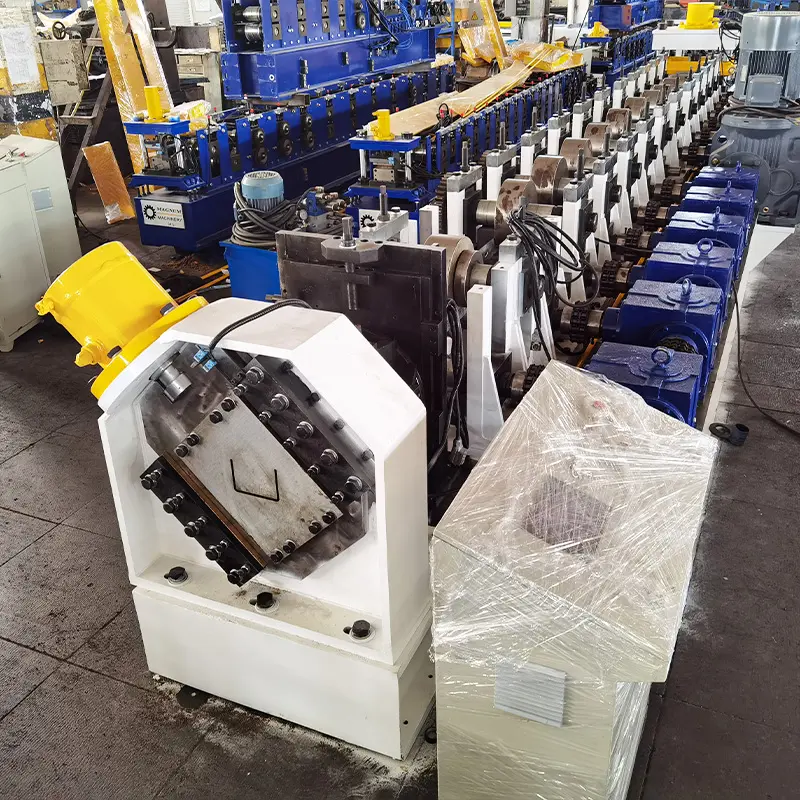
Limitations of Steel Silo Roll Forming
- High initial cost – Large investment required for automated versions
- Fixed tooling – Changes in profiles require mechanical adjustments
- Dimensional constraints – Limited to forming capability of roller dies
- Power demands – Significant electricity load for industrial operation
- Setup time – Machine changeover between different configurations
- Skilled labor – Technical personnel needed for programming and maintenance
FAQ
Q: What materials can be formed on a steel silo roll machine?
A: Most common is low carbon steel coil but stainless steel and aluminum coils can also be formed.
Q: How to determine correct machine capacity for required silo output?
A: Supplier should size based on annual steel tonnage needed, silo dimensions, feed material, hours of operation.
Q: What safety measures are necessary?
A: Safety guarding, operator training, maintenance schedule, shutoff protocols to avoid jamming or coil breaks.
Q: Can a machine be upgraded to higher automation levels later?
A: Yes, modular enhancements often possible for uncoiling, welding, cutting, packaging based on initial foundation capacity.
Q: What regular maintenance is vital on the machine?
A: Lubrication, visual inspections, replacing consumable parts like guides, bearings and belts according to schedule.
Q: How to troubleshoot irregular shaping defects?
A: Review die alignment/wear, feeding method, strip lubrication, adjust forming speeds or pressures to optimize uniformity.