In today’s fast-paced industrial world, sheet metal panels have become one of the most versatile and essential components across a variety of industries. From construction to automotive manufacturing, these metal sheets have a wide range of uses that makes them irreplaceable. But what exactly are sheet metal panels? Why are they so vital in different applications? And more importantly, how do you choose the right one for your specific needs? In this guide, we’ll dive deep into the fascinating world of sheet metal panels, discuss their types, key components, the processes involved in making them, and even explore some of the most popular sheet metal powders available on the market today. Let’s get started!
What are Sheet Metal Panels?
At the core, sheet metal panels are thin, flat pieces of metal that are used in manufacturing to form parts and structures. These panels are created through an industrial process of metal forming, and they come in a variety of sizes, thicknesses, and materials, including aluminum, steel, copper, and more. Due to their durability, flexibility, and strength, sheet metal panels are widely used in everything from roofing to car bodies to HVAC systems.
What makes sheet metal panels truly stand out is their versatility. They can be bent, cut, and shaped into almost any form, which makes them indispensable in both small-scale and large-scale projects. Whether you’re constructing a high-rise building, designing a car, or fabricating parts for electronics, sheet metal panels offer a level of customization and functionality that few other materials can match.
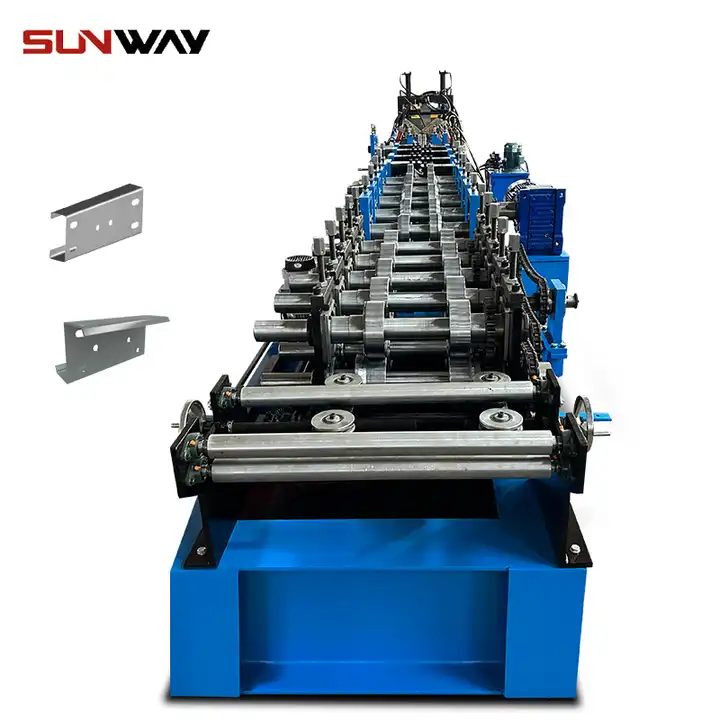
The Corrugated Iron Sheets Guide
Corrugated iron sheets, a specific type of sheet metal panel, have gained immense popularity due to their unique design and strength. The wave-like pattern of corrugated sheets enhances their durability and provides excellent resistance against harsh environmental conditions such as heavy rains, strong winds, and even snow. Because of this, they are widely used in roofing applications, especially in rural areas or industrial settings where long-lasting protection is essential.
These sheets are typically made from galvanized steel or aluminum, both of which are corrosion-resistant materials. When compared to flat sheet metal panels, corrugated iron sheets offer better structural integrity while maintaining a relatively light weight. They’re also cost-effective, easy to install, and ideal for projects where durability and weather resistance are non-negotiable.
Benefits of Corrugated Iron Sheets:
- Increased strength due to the corrugated design.
- Lightweight and easy to handle.
- Excellent weather resistance.
- Versatile for various applications such as roofing, cladding, and fencing.
- Cost-effective and readily available.
Types of Sheet Metal Panels
Sheet metal panels come in many different types, each suited for specific applications. Here’s a breakdown of the most common types of sheet metal panels you might encounter:
Type | Material | Features | Best Uses |
---|---|---|---|
Galvanized Steel | Steel | Corrosion-resistant, durable, low maintenance | Roofing, fencing, industrial applications |
Stainless Steel | Steel with chromium | High corrosion resistance, shiny finish, sturdy | Kitchen appliances, surgical instruments |
Aluminum Panels | Aluminum | Lightweight, corrosion-resistant, highly ductile | Aircraft, automotive parts, electronics |
Copper Panels | Copper | Excellent conductivity, aesthetic appeal, durable | Electrical wiring, roofing, decorative applications |
Brass Panels | Copper & Zinc | Aesthetic, corrosion-resistant, easily machinable | Musical instruments, plumbing fixtures |
Titanium Panels | Titanium | High strength-to-weight ratio, corrosion-resistant | Aerospace, medical implants |
Zinc Panels | Zinc | Eco-friendly, long-lasting, patina over time | Roofing, facades, cladding |
Tin Panels | Tin-coated steel | Rust protection, highly malleable, smooth surface | Food containers, decorative tins |
Cold Rolled Steel | Steel | High tensile strength, smooth finish | Automotive parts, construction framing |
Hot Rolled Steel | Steel | Economical, rougher finish, ideal for larger projects | Structural components, large machinery |
Working Process of Sheet Metal Panels
The manufacturing process for sheet metal panels is complex and varies depending on the type of metal being used and the desired end product. Below is a step-by-step explanation of how sheet metal panels are typically created:
Step 1: Material Selection
The first step in the production of sheet metal panels is choosing the right type of metal for the job. Common materials include steel, aluminum, copper, and others, each selected based on the specific properties needed—whether it’s corrosion resistance, strength, or malleability.
Step 2: Rolling the Metal
Once the material is chosen, it is typically rolled into thin sheets using a rolling mill. There are two types of rolling: hot rolling and cold rolling. Hot rolling is used for creating larger, rougher sheets, while cold rolling is used for producing smooth, high-tolerance panels.
Step 3: Cutting and Shaping
After the metal has been rolled, it is cut and shaped into the desired dimensions. This step involves the use of various cutting tools, including shears, lasers, and water jets, to achieve precise cuts.
Step 4: Forming
Forming involves bending or pressing the metal sheet into its final shape. This can be done using a press brake, roll forming, or other specialized tools, depending on the thickness and material of the sheet.
Step 5: Finishing
The final step in the process is finishing, which may involve galvanizing, painting, or applying a protective coating to enhance the durability and appearance of the panel.
Key Components | Function |
---|---|
Rolling Mill | Compresses metal into thin sheets, either through hot or cold rolling. |
Cutting Tools | Used for trimming and cutting the metal sheets into specific shapes. |
Press Brake | Bends and forms the metal sheets into their final shapes. |
Galvanizing Equipment | Adds a layer of zinc to steel to prevent corrosion. |
Coating Machines | Apply protective or decorative coatings to the finished metal sheets. |
-
Carriage Board Roll Forming Machine
-
Highway Guardrail End Terminal Forming Machine
-
Highway U/C Post Roll Forming Machine
-
2 Waves Highway Guardrail Roll Forming Machine
-
3 Waves Highway Guardrail Roll Forming Machine
-
C Section Bracing Omega Storage Rack Upright Post Roll Forming Machine
-
Steel Box Plate Making Roll Forming Machine
-
Box Beam Steel Roll Forming Machine For Shelf Column
-
Pallet Racking Step Beam P Beam Roll Forming Machine
Machine Speed and Efficiency in Sheet Metal Production
Efficiency is critical in the manufacturing of sheet metal panels, and various machines and equipment are used to optimize the process. The table below provides an overview of typical machine speeds and their efficiencies in sheet metal production.
Machine Type | Speed (sheets per minute) | Efficiency (%) |
---|---|---|
Rolling Mill | 10-30 sheets/min | 85% |
Laser Cutter | 15-50 sheets/min | 90% |
Water Jet Cutter | 5-15 sheets/min | 80% |
Press Brake | 8-25 sheets/min | 88% |
Customized Mechanical Parameters
In some applications, standard sheet metal panels won’t cut it. Customizing mechanical parameters can help achieve more precise results tailored to the unique needs of a project. Here’s a table detailing some of the key parameters that can be customized.
Parameter | Standard Range | Customizable Range |
---|---|---|
Sheet Thickness | 0.5mm to 5mm | 0.2mm to 10mm |
Sheet Width | 500mm to 1500mm | 300mm to 2000mm |
Tensile Strength | 250MPa to 600MPa | 200MPa to 800MPa |
Coating Thickness | 5µm to 20µm | 1µm to 50µm |
Surface Finish | Matte, Gloss, Textured | Custom Colors, Patterns |
Applications of Sheet Metal Panels
Sheet metal panels have a wide range of applications across various industries. Below is a table showcasing the primary uses for different types of sheet metal panels.
Industry | Application | Preferred Metal |
---|---|---|
Construction | Roofing, cladding, structural | Galvanized Steel, Aluminum |
Automotive | Car bodies, panels, exhausts | Aluminum, Cold Rolled Steel |
Aerospace | Aircraft parts, fuselage, wings | Titanium, Aluminum |
Electronics | Enclosures, casings, circuit boards | Copper, Aluminum |
Agriculture | Machinery, storage facilities | Stainless Steel, Galvanized Steel |
HVAC | Ductwork, air conditioners | Galvanized Steel, Copper |
Installation, Operation, and Maintenance of Sheet Metal Panels
Proper installation, operation, and maintenance are crucial to maximizing the lifespan and functionality of sheet metal panels. Below are the general guidelines for these aspects.
Process | Best Practices |
---|---|
Installation | Ensure accurate measurements, use the appropriate fasteners and brackets for each type. |
Operation | Regular inspections for wear and tear, ensure proper ventilation to avoid corrosion. |
Maintenance | Clean regularly to remove dirt and debris, apply protective coatings as needed. |
Sheet Metal Panel Suppliers and Price Range
Prices for sheet metal panels can vary greatly depending on material type, size, and customization. Below is an overview of some common suppliers and their price ranges.
Supplier | Material Type | Price Range (per square foot) |
---|---|---|
Metal Supermarkets | Stainless Steel, Aluminum | $5 to $12 |
Online Metals | Copper, Brass, Titanium | $8 to $20 |
Grainger | Galvanized Steel, Zinc | $4 to $10 |
McMaster-Carr | Cold Rolled Steel, Tin | $6 to $14 |
How to Choose the Right Supplier for Sheet Metal Panels
Choosing the right supplier for sheet metal panels can make a significant difference in the quality and cost of your project. Here’s how to evaluate suppliers effectively:
Evaluation Factor | What to Look For |
---|---|
Material Quality | Ensure the supplier offers high-quality, certified materials. |
Price | Compare prices from different suppliers to ensure you’re getting the best deal. |
Customization Options | Suppliers should offer customization based on your specific project needs. |
Delivery Time | Check lead times and whether they align with your project deadlines. |
Customer Reviews | Look for suppliers with positive reviews and testimonials from other clients. |
Advantages and Disadvantages of Sheet Metal Panels
Every material has its pros and cons, and sheet metal panels are no different. Here’s a comparison of their advantages and limitations.
Advantages | Limitations |
---|---|
Durable and long-lasting | Can be expensive for high-end metals |
Versatile and customizable | Requires specialized machinery for shaping |
Lightweight (in the case of aluminum) | Prone to corrosion without proper protection |
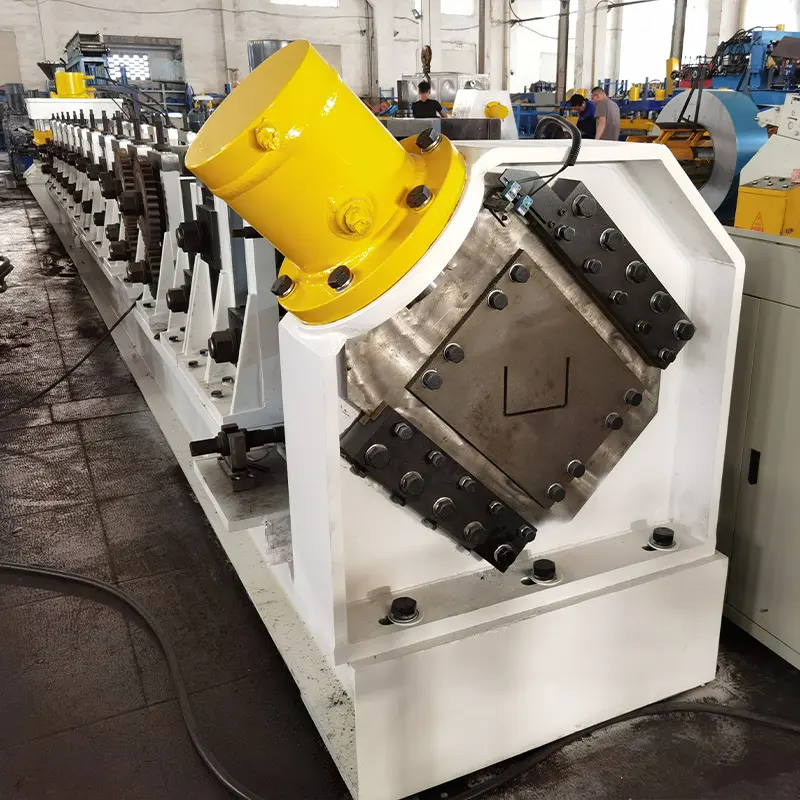
FAQ
Question | Answer |
---|---|
What is the most durable type of sheet metal panel? | Stainless steel is one of the most durable types of sheet metal panels due to its high resistance to corrosion and strength. |
Can sheet metal panels be used for DIY projects? | Yes, sheet metal panels can be used for DIY projects, especially aluminum or galvanized steel panels, which are relatively easy to handle. |
How do you prevent sheet metal panels from rusting? | Applying a protective coating like galvanization or paint can prevent rusting in sheet metal panels. |
Is it possible to customize the size and shape of sheet metal panels? | Absolutely! Many suppliers offer customization services to match your specific project requirements in terms of size, thickness, and finish. |
Which metal is best for roofing applications? | Galvanized steel or aluminum panels are excellent choices for roofing due to their weather resistance and durability. |
In conclusion, sheet metal panels are indispensable in modern manufacturing and construction. Their versatility, durability, and wide range of applications make them a go-to material for projects of all sizes. By understanding the different types of sheet metal, the processes involved in their production, and how to choose the right supplier, you can ensure the success of your next project involving sheet metal panels.