Roofing sheets roll forming machines produce long sections of ribbed metal roofing profiles via continuous bending and gradual shaping from coiled strip stock feeds. This guide covers configurations, process overview, forming capabilities, components, suppliers, and comparative assessment.
roofing sheets roll forming machine Working Principle
Roofing sheet roll formers incrementally bend sheet metal into arched ribbed profiles:
Process | Continuous bending into progressive die forms by motorized flower rollers |
Metal Strip | Feeds through consecutive roll stations to shape profile along length |
Die types | Circle rounding, pre-cutting, punching, beading, rib shaping |
Bending methods | Rotary bending of strip through top and bottom rollers |
Sheet cutting | Pneumatic trimming knife slices formed sheets at the exit |
Typical metals | Galvanized steel, aluminum, zinc alloys, copper alloys |
Synchronized actuation between material feed, roller dies and cutting blade facilitated by precision controls.
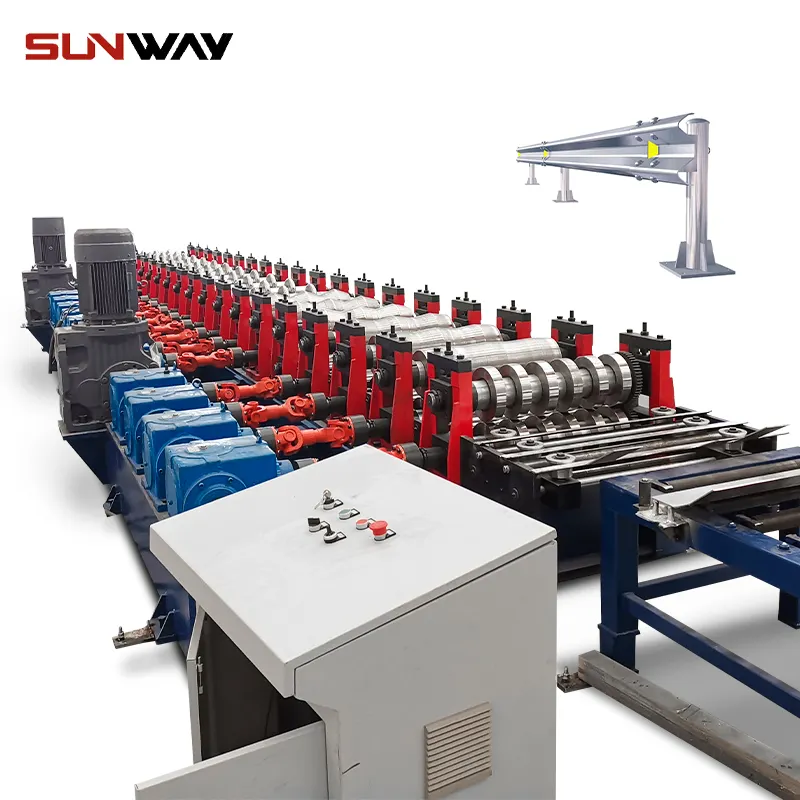
System Equipment
Component | Function |
---|---|
Decoiler | Feeds raw coil stock into line |
Feed table | Controls material speed and tension |
Forming stations | Impart profile shape via flower rollers |
PLC controls | Automate roller position, feed and cutting |
Hydraulics | Adjust roller pressure during bending |
Exit conveyor | Catches finished parts |
Additional Modules: Straighteners, hole punching, embossing, punching and part marking systems.
roofing sheets roll forming machine Production Capabilities
Part width | Up to 1000mm for largest machines |
Thickness range | 0.15mm to 1.2mm metals |
Material strengths | From soft aluminum to ultra high strength steels |
Profiles | Trapezoidal, corrugated, box rib and custom profiles |
Secondary operations | Embossing, hole punch, beading, hemming |
Metal coatings | Pre-painted, galvanized, weathering finishes |
-
Electrical Cabinet Frame Roll Forming Machine
-
Din Rail Roll Forming Machine
-
Cable Ladder Roll Forming Machine
-
PV Mounting Bracket C Shape Profile Roll Forming Machine
-
Cable Tray Roll Forming Machine
-
PV Mounting Bracket Roll Forming Machine (HAT / Omega Profile)
-
PV Mounting Bracket Z Shape Profile Roll Forming Machine
-
Solar mounting strut channel roll forming machine
-
Strut Channel Roll Forming Machine
roofing sheets roll forming machine Suppliers
Company | Model Series | Cost Range |
---|---|---|
Copra | CRC Roof Former | $200,000-$900,000 |
Dragos | DRF | $250,000-$950,000 |
Formtek | Orion RF | $300,000-$1,100,000 |
Ernst Beckert | SRFF | $350,000-$1,250,000 |
Quotes vary based on width capacity, production speed, level of automation and customization needs. Get references on local service support.
Operation and Maintenance
Activity | Description | Frequency |
---|---|---|
Decoiler checks | Inspect strip alignment and tension | Start of coil |
Bearing lubrication | Grease key roller bearing points | Monthly |
Hydraulic inspection | Check fluid, cylinders, and seals | 6 months |
Die inspections | Inspect forming dies for wear/damage | Yearly |
Control diagnostics | Validate sensors, actuators and sequences | As needed |
Proactive preventative maintenance reduces high cost emergency breakdowns and improves uptime productivity. Keep spare tooling inventories.
Selection Considerations
Factor | Guidelines |
---|---|
Volume throughput | Size appropriately for daily production volume targets |
Material specification | Accommodate desired metal type, thickness and strengths |
Number of tooling stages | Balance complexity with changeover needs |
**Profile consistency ** | Heavier machines sustain tighter tolerances |
Software capabilities | Flexibility for future profile programming |
Secondary operations | Availability of punching, notching, embossing, bending |
Reputation and support | Validate references and localized service capability |
Carefully evaluate specifications against requirements to minimize costly reworks down the road.
Key Takeaways
- Continuous roll forming efficiency excels for high volume roofing sheet production
- Additional dies enable profile variation but limit design flexibility
- Heavier machines facilitate tighter tolerances
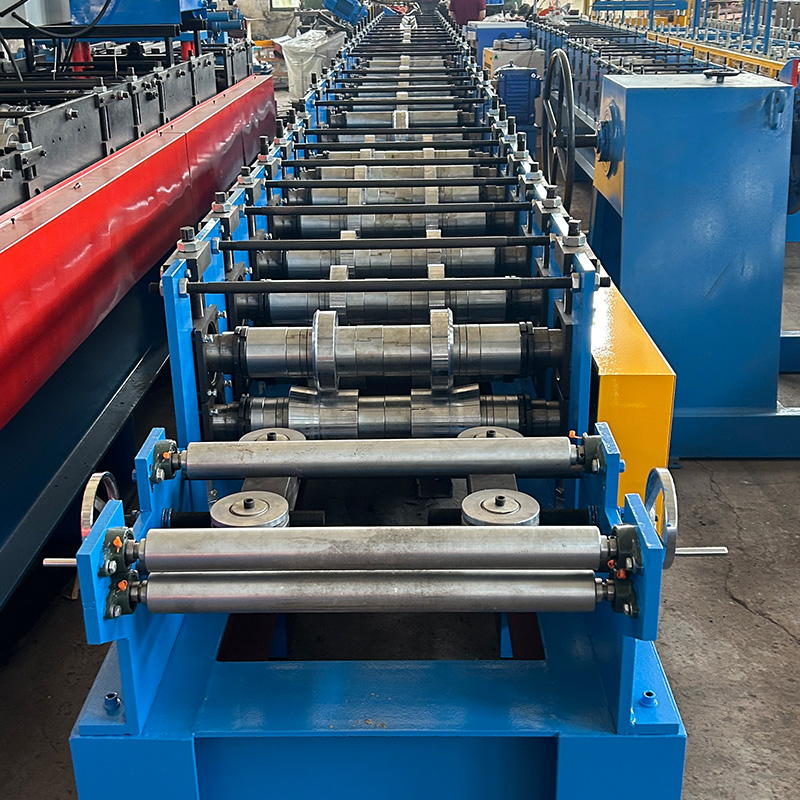
FAQs
Q: What metals can be roll formed into ribbed roofing profiles?
A: Galvanized steel, zinc alloys, aluminum and copper alloys are commonly formed. Stainless steel is also possible for high corrosion resistance needs.
Q: What thickness range can roofing sheet roll forming handle?
A: Incoming coil thickness capabilities typically range from 0.15mm to 1.2mm thickness, with 0.3-0.7mm optimal for balancing productivity, yield and tolerance.
Q: Can roll formed roof sheets be curved or angled?
A: Yes secondary flanging and hemming operations can be added inline to impart multiple planes and curve shapes to finished roll formed sheets.
Q: What tolerances are held on roll formed roofing sheets?
A: ±0.5-1mm accuracy is common for critical dimensions like width, rib height and straightness over length depending on machine rigidity, wear and controls capability.