Overview of Roll Forming Machinery
Roll forming machinery is the cornerstone of modern metalworking, transforming flat metal sheets into complex profiles through a continuous bending process. These machines are integral to industries ranging from construction to automotive manufacturing. This guide will delve into the specifics of roll forming machinery, exploring its types, working process, key components, speed, efficiency, customization, applications, and more.
Roll Forming Machine Guide
Roll forming machinery comes in various types, each designed to cater to specific needs and applications. Here, we’ll explore different models and their unique features, providing a thorough understanding of what makes each type suitable for certain tasks.
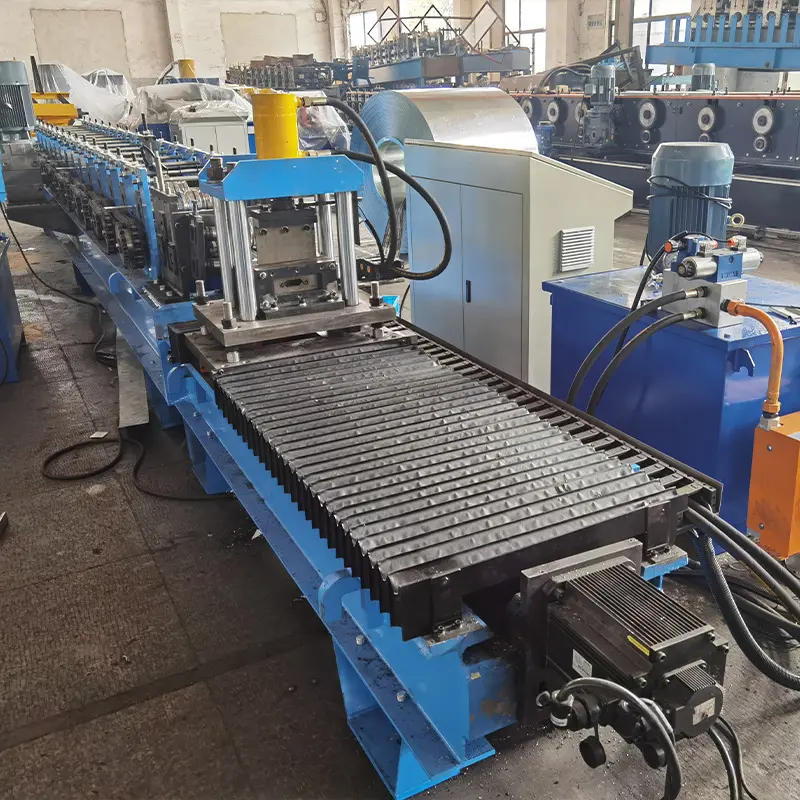
Types of Roll Forming Machinery
Type | Description |
---|---|
Single-Head Machines | Designed for simple profiles, ideal for low-volume production and small-scale operations. |
Double-Head Machines | Allow for the creation of more complex profiles by combining two sets of rolls, increasing production capabilities and efficiency. |
Multi-Head Machines | Feature multiple roll sets for high-volume production of intricate profiles, suitable for large industrial applications. |
Adjustable Machines | Equipped with adjustable roll positions to accommodate different profile shapes without needing separate machines for each profile type. |
Portable Machines | Lightweight and mobile, these machines are perfect for on-site construction work or small production facilities with limited space. |
CNC Roll Forming Machines | Computer Numerical Control (CNC) machines offer high precision and automation, ideal for complex and high-accuracy profiles. |
Hydraulic Roll Forming Machines | Utilize hydraulic power for enhanced force and capability, making them suitable for heavy-duty applications and thick materials. |
Servo-Electric Machines | Use servo motors for precise control over roll positioning and speed, offering high efficiency and reduced energy consumption. |
Inline Roll Forming Machines | Integrated with other production processes, these machines streamline the manufacturing process by reducing handling and transfer times. |
Custom Roll Forming Machines | Tailored to specific industry needs and unique profile requirements, these machines provide flexibility and adaptability for specialized applications. |
Working Process of Roll Forming Machinery
Roll forming machinery operates by gradually bending a metal sheet through successive sets of rolls. Here’s a step-by-step breakdown of the process:
- Feeding the Material: The metal sheet is fed into the roll forming machine.
- Initial Positioning: The first set of rolls positions the sheet and begins the bending process.
- Progressive Forming: As the sheet progresses, each successive set of rolls further shapes the metal, gradually achieving the desired profile.
- Final Shaping: The last set of rolls completes the profile, ensuring precision and consistency.
- Cutting: The formed profile is cut to the required length, either in-line or post-process.
This process ensures high precision and repeatability, making roll forming an efficient method for producing complex profiles with minimal material waste.
Key Components and Their Functions
Component | Function |
---|---|
Uncoiler | Holds and unwinds the metal coil, feeding it into the roll forming machine. |
Feeding Guides | Direct the metal sheet into the initial set of rolls, ensuring proper alignment. |
Roll Stands | Support the roll tools and maintain the required forming pressures and positions. |
Roll Tools | Series of rollers that progressively bend the metal sheet into the desired profile shape. |
Cutting System | Cuts the formed profile to the required length, can be integrated in-line or as a separate process. |
Control System | Manages the machine operations, including roll positioning, speed, and cutting, often using CNC technology. |
Hydraulic System | Provides the necessary force for forming thick or high-strength materials. |
Servo Motors | Offer precise control over roll positioning and speed, enhancing accuracy and efficiency. |
Safety Guards | Protect operators from moving parts and ensure safe operation of the machinery. |
-
Highway Guardrail End Terminal Forming Machine
-
Highway U/C Post Roll Forming Machine
-
2 Waves Highway Guardrail Roll Forming Machine
-
3 Waves Highway Guardrail Roll Forming Machine
-
Vineyard Post Roll Forming Machine
-
Auto Size Changeable Sigma Purlin Roll Forming Machine
-
Auto Size Changeable C Z Purlin Roll Forming Machine
-
Auto Size Changeable Z Purlin Roll Forming Machine
-
Auto Size Changeable C U Purlin Roll Forming Machine
Machine Speed and Efficiency
Type of Machine | Speed (m/min) | Efficiency |
---|---|---|
Single-Head Machines | 10-30 | Moderate, suitable for low to medium volume production. |
Double-Head Machines | 20-50 | High, allows for more complex profiles with higher output. |
Multi-Head Machines | 30-80 | Very high, ideal for large-scale industrial production. |
CNC Roll Forming Machines | 15-40 | Extremely high, with precise control and minimal waste. |
Hydraulic Roll Forming Machines | 10-35 | High, capable of handling thicker materials efficiently. |
Servo-Electric Machines | 20-60 | Very high, energy-efficient with excellent precision. |
Customized Mechanical Parameters
Parameter | Details |
---|---|
Material Thickness | Ranges from 0.2mm to 6mm, depending on the machine type and application requirements. |
Profile Width | Adjustable from 10mm to 1500mm, allowing flexibility in profile dimensions. |
Roller Diameter | Typically between 100mm to 500mm, impacting the forming accuracy and profile complexity. |
Machine Length | Varies from 5m to 30m, depending on the number of roll sets and machine design. |
Power Supply | Options include 220V, 380V, or 440V, matching the industrial power standards. |
Forming Speed | Adjustable speed controls to match production requirements and material characteristics. |
Control System | Options for manual, semi-automatic, or fully automatic (CNC) control systems. |
Applications and Uses
Industry | Application |
---|---|
Construction | Roofing, wall panels, steel framing, and gutter profiles. |
Automotive | Vehicle body parts, structural components, and chassis elements. |
Aerospace | Aircraft structural components and custom profiles for aeronautical applications. |
Electrical | Cable trays, enclosures, and custom metal profiles for electrical installations. |
Furniture | Metal frames, support structures, and decorative profiles for furniture manufacturing. |
Energy | Solar panel frames, wind turbine components, and structural profiles for energy projects. |
Appliance Manufacturing | Metal housings, structural parts, and decorative profiles for home appliances. |
Transportation | Trailer frames, shipping container profiles, and railway components. |
Agriculture | Equipment frames, structural components, and custom profiles for agricultural machinery. |
Installation, Operation, and Maintenance
Aspect | Details |
---|---|
Installation | Requires proper site preparation, foundation setup, and alignment checks before machine commissioning. |
Operation | Operate via manual, semi-automatic, or fully automatic control systems, ensuring operator training and safety. |
Maintenance | Regular inspections, lubrication of moving parts, and timely replacement of worn components to ensure optimal performance. |
Suppliers and Price Range
Supplier | Price Range (USD) | Details |
---|---|---|
ABC Roll Forming Solutions | $50,000 – $200,000 | Offers a wide range of machines with customization options. |
XYZ Metal Machinery | $40,000 – $150,000 | Known for robust and reliable machines suitable for various applications. |
Precision Roll Forming Inc. | $60,000 – $250,000 | Specializes in high-precision CNC and servo-electric roll forming machines. |
Global Roll Forming Tech | $45,000 – $180,000 | Provides comprehensive after-sales support and maintenance services. |
Universal Roll Forming | $55,000 – $220,000 | Offers both standard and custom roll forming solutions for diverse industrial needs. |
Choosing the Right Supplier
Selecting the right supplier is crucial for ensuring the best roll forming machinery for your needs. Consider these factors:
- Reputation and Experience: Look for suppliers with a strong track record and extensive experience in the industry.
- Customization Capabilities: Ensure the supplier can provide tailored solutions to meet your specific requirements.
- After-Sales Support: Check for comprehensive support services, including maintenance, training, and spare parts availability.
- Price and Value: Compare prices relative to the features, quality, and support offered to ensure you get the best value for your investment.
Pros and Cons of Roll Forming Machinery
Aspect | Advantages | Limitations |
---|---|---|
Efficiency | High production speed and consistency. | Initial setup and tooling can be expensive and time-consuming. |
Precision | Produces highly accurate and complex profiles. | Limited to the profiles that can be designed and too led for. |
Material Utilization | Minimal material waste during the forming process. | Requires consistent material quality to avoid defects. |
Flexibility | Suitable for a wide range of materials and profile shapes. | Changing profiles requires tooling adjustments or changes. |
Automation | CNC and servo-electric machines offer enhanced automation and control. | Higher initial cost for advanced automated systems. |
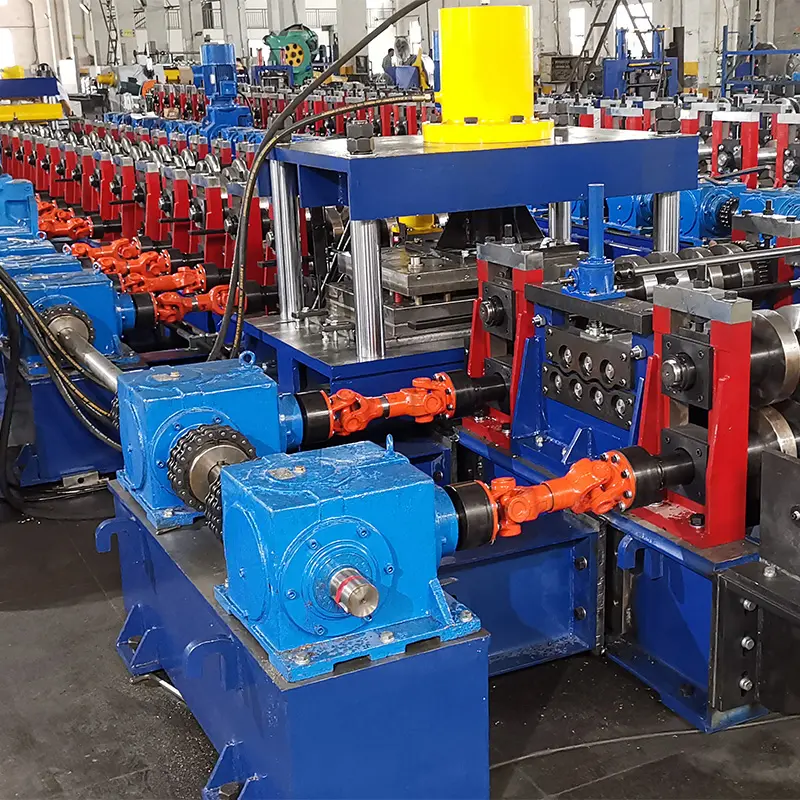
FAQs
Question | Answer |
---|---|
What materials can be used with roll forming machines? | Common materials include steel, aluminum, copper, and other metals with suitable ductility. |
How do I choose the right roll forming machine for my needs? | Consider factors such as material type, profile complexity, production volume, and budget. |
What maintenance is required for roll forming machines? | Regular inspections, lubrication, and timely replacement of worn components are essential for optimal performance. |
Can roll forming machines create custom profiles? | Yes, custom roll forming machines can be tailored to produce specific profiles according to your requirements. |
What is the typical lifespan of a roll forming machine? | With proper maintenance, roll forming machines can last for several decades. |
Are roll forming machines energy efficient? | Modern roll forming machines, especially servo-electric types, are designed for high energy efficiency. |