Track roll forming is a metal forming process used to form metal sheets into customized profiles with repetitive cross-sections. Track roll forming machines are designed for efficient continuous production of metal parts with consistent quality.
This comprehensive guide provides key information on track roll forming equipment to help you understand their working, applications, specification details, supplier options and more.
Overview of Track Roll Forming Machines
Track roll forming machines shape metal coils into customized parts by progressively bending the strip through consecutive sets of rolls. Each roller set performs an incremental bend until the desired cross-section profile is obtained.
Key Features of Track Roll Forming Lines
- Continuous production of profiles with repetitive cross-sections
- High productivity and speeds up to 100 m/min
- Capability to form complex and asymmetric shapes
- Tight tolerances and excellent consistency in product quality
- Lower tooling costs compared to other processes
- Minimal material waste and smaller space requirement
- Automated operation for high efficiency and precision
- Flexibility to switch profiles quickly
Main Components of a Track Roll Forming System
The major components of a track roll forming line include:
Component | Function |
---|---|
Uncoiler | Holds the coil of sheet metal to be formed |
Feed assembly | Feeds metal strip into the forming section at a constant speed |
Roll forming stations | Progressive sets of rolls performing incremental bends |
PLC control | Precisely controls each station and overall line |
Cutoff device | Cuts finished profiles to desired lengths |
Runout table | Supports formed profiles leaving the last station |
Types of Track Roll Forming Machines
Track roll forming systems are available in different configurations designed for specific applications:
- Standard – Basic roll former for long parts like panels, rails, tracks
- C-shaped – For forming enclosed channel and frame sections
- O-shaped – For hollow tube-like profiles with open section
- Specialty – Custom machines for complex shapes like squares, ellipses
Working Principle of Track Roll Forming Lines
The working principle involves:
- Sheet metal coil loaded on an uncoiler is fed into the roll forming section
- Progressive roller stations apply incremental bends to gradually form the profile
- PLC-controlled rollers precisely shape the strip without defects
- Cutting device cuts finished parts to required length
- Formed profiles exit on runout table for collection
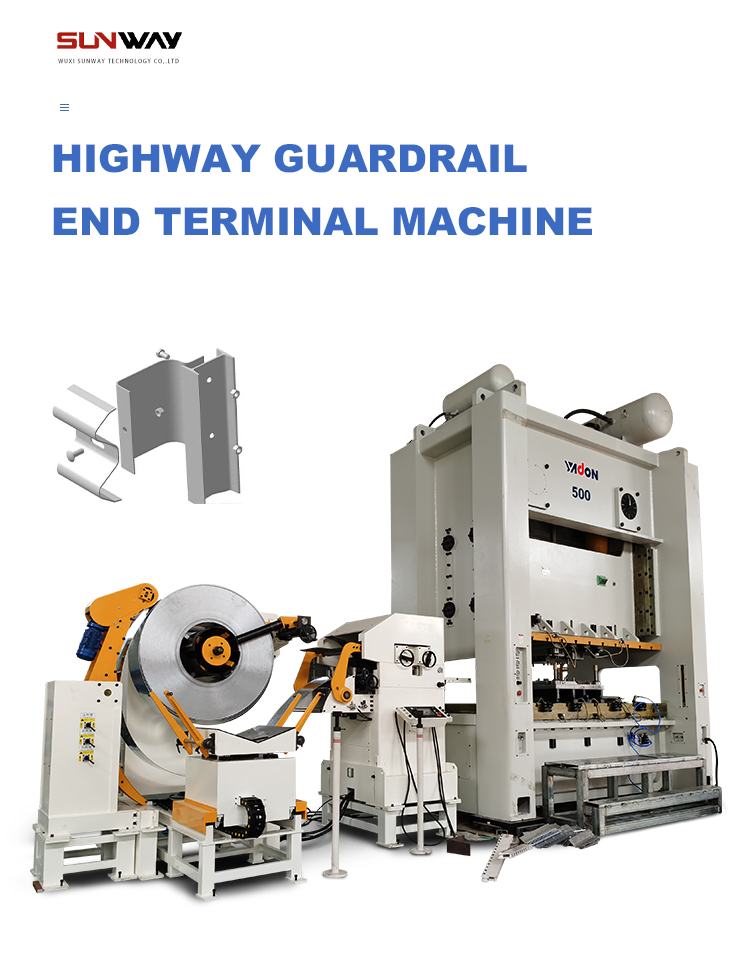
Applications of Track Roll Forming Machines
Track roll forming is used to produce long, straight metal parts with constant cross-sections across many industries:
Construction and Infrastructure
- Metal roofing
- Wall panels
- Highway guard rails
- Steel roof trusses
- Bridge decks
- Culverts
- Structural frames
Transportation
- Rail tracks
- Truck frames
- Bus body panels
- Railway coach side walls
- Ship hulls and platforms
Furniture
- Bed frames
- Shelving standards
- Storage rack uprights
- Refrigerator liners
- Office furniture frames
Automotive
- Chassis parts
- Bumpers, braces
- Door beams
- Seat frames
- Exhaust components
Appliances
- Washing machine drums
- Refrigerator panels
- Air conditioner grilles
- Electrical enclosures
- Kitchen equipment
Comparison of Roll Formed Parts vs Other Methods
Parameter | Roll Formed | Stamped | Extruded |
---|---|---|---|
Shape complexity | Medium | High | Low |
Strength | Medium | High | Medium |
Dimensional accuracy | High | Medium | High |
Surface finish | Good | Excellent | Good |
Setup time | Low | High | Medium |
Tooling cost | Low | Very high | High |
Production rate | High | Medium | Medium |
Part length | Continuous | Limited | Continuous |
Cost efficiency | High | Low | Medium |
How to Choose a Track Roll Forming Machine
Selecting the right track roll forming line requires matching the equipment capabilities to the product requirements:
Product Shape and Dimensions
- Capacity for part size, width, thickness, length
- Profile geometries possible – open, closed, round etc.
- Tolerances required
Production Output Needs
- Output speed required in feet/minute
- Coil width, thickness, and material
- Annual volume to be produced
Line Configuration
- Number of roll stations needed
- Type of uncoiler, feeder, cutoff
- Level of automation
- Line layout – C-type, O-type, standard etc.
Quality Standards
- Surface finish level needed
- Tolerances to be achieved
- Capability for part features like holes, embossing
Budget Constraints
- Capital investment for equipment
- Operating costs – labor, utilities, maintenance
- Payback period expected
Matching the roll former model and features to the product specifications ensures optimum results.
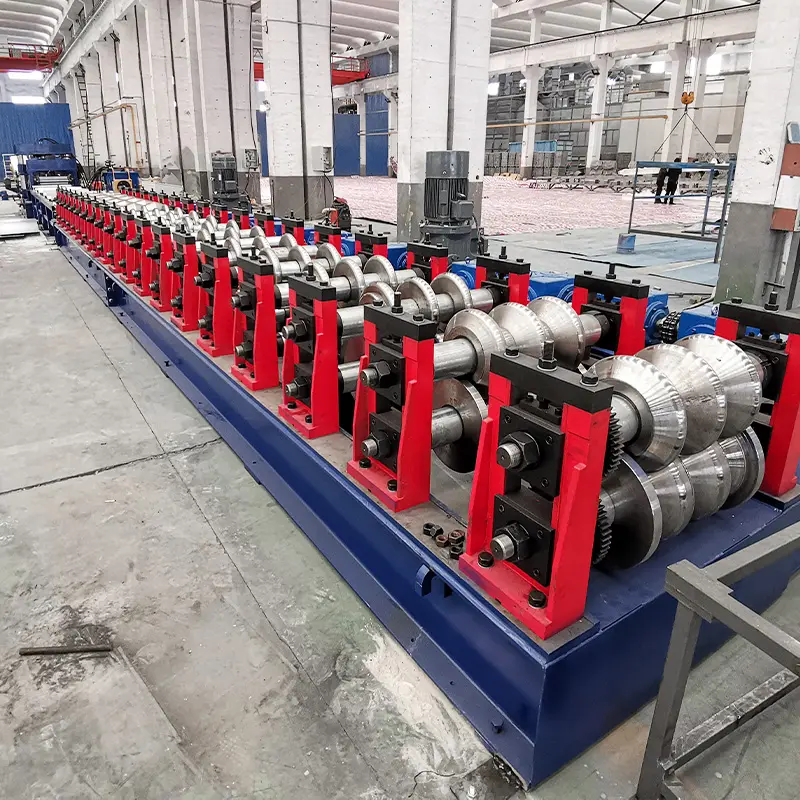
Specifications of Track Roll Forming Machines
The key specifications and parameters to consider for track roll formers are:
Equipment Dimensions
- Length, width, and height
- Line layout style – C, O or I type
- Number of roll forming stations
- Space required for operation and maintenance
Drive and Speed
- Forming speed in feet per minute
- Motor power and torque
- Type of speed control system
Rolls
- Roll barrel diameter and width
- Roll materials – steel, carbon steel, alloy steel
- Roll hardness level
- Quick change-over rolls to alter profiles
Material Capabilities
- Width range of coils accommodated
- Thickness range possible
- Types of materials – steel, stainless steel, aluminum etc.
- Maximum strip tensile strength
Tooling
- Quick change tooling for fast profile switching
- Tooling for special features like lancing, punching, embossing
Automation
- Servo motor drives for precision
- PLC and HMI for control
- Sensors for monitoring operation
- Automatic lubrication systems
Handling Equipment
- Coil holding capacity of uncoiler
- Type of feeds – pinch roll, spindle ball bearing
- Cutoff device – flying shear, rotary shear etc.
- Runout table length and conveyors
The specifications directly influence the roll formed part quality, production rates, and line costs.
Design and Engineering Standards
Track roll forming machines need to be designed, manufactured and tested according to relevant standards for optimal performance.
Structural Design Codes
- AISC specifications for steel construction
- ASME standards for guards and safety
- IBC for wind, seismic and building loads
- MBMA standards for metal building systems
Material Standards
- ASTM standards for metals like ASTM A1008, A653, A792
- EN, DIN standards for European materials
Process Guidelines
- AISI guidelines for cold-formed steel framing
- AWS standards for welding
- SAE recommendations for fasteners
Control System Standards
- UL, CSA, CE standards for electrical systems
- ISO 13849 for safety-related controls
- IEC 61131 for PLC programming
Testing and Inspection
- ASTM standards for materials testing
- AWS codes for weld inspection
- FEMA seismic certification
- UL panel certification
Following relevant codes ensures the roll former meets quality, safety and performance requirements.
Roll Forming Machine Manufacturers and Suppliers
Some of the leading global suppliers of track roll forming equipment are:
Metform International
- Offer complete roll forming lines for standard and custom profiles
- Capabilities for high strength steels and large parts
- Manufacturing facilities in the USA, Thailand, and China
Formtek Group
- Wide range of standard and specialty roll formers
- Max forming speed of 130 m/min
- Custom profile design and production
Hangzhou Roll Forming Machinery
- Focus on roll forming lines for construction industry
- Advanced PLC control systems
- Roll forming equipment exported worldwide
Anhui Yuming Machinery Technology
- Roll formers for roofing, racking, furniture, automotive industry
- CNC controlled production lines
- R&D center for new product development
Moderne Technologie d’Usinage S.A.
- 50 years experience in precision roll forming
- Custom and standard roll forming machines
- Turnkey projects delivered globally
In addition, many regional manufacturers and OEMs offer roll forming equipment options catering to local markets.
Roll Former Pricing
Roll former cost depends on factors like:
- Line size and production speed
- Number of roller stations
- Level of automation and controls
- Material capabilities
- Line configuration – C, O or I type
- Add-on equipment like decoilers, runout tables etc.
Indicative Pricing Range
- Small roll formers – $50,000 to $100,000
- Medium lines – $150,000 to $500,000
- High capacity systems – $600,000 to $2 million
- Custom roll formers – $500,000 to $5 million
Seeking competitive bids from shortlisted suppliers helps find optimum value.
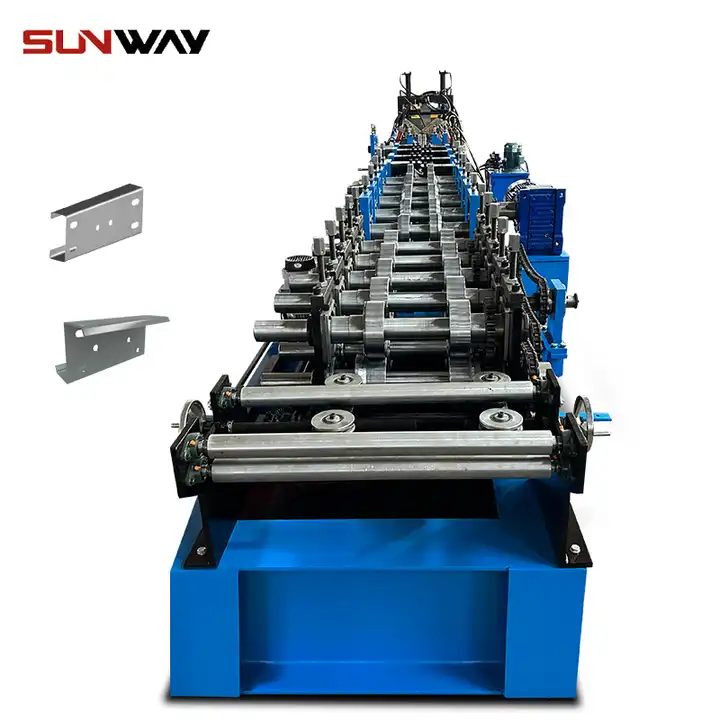
How to Choose A Track Roll Forming Machine Manufacturer
Selecting the right roll former OEM involves:
Product Quality
- Use of precision machining, reliable components
- Stringent quality control and testing
- Compliance to standards – ISO 9001, CE
- Consistent roll formed part quality
Technical Expertise
- Experience in roll former design and builds
- In-house engineering for profiles
- Knowledge of latest standards and processes
- Installation and field support capabilities
Customization Ability
- Offering custom machines for special profiles
- Flexibility in line layout and features
- Integration of secondary operations like punching, welding
- Custom controls and automation solutions
Responsiveness and Support
- Quick response to RFQs and inquiries
- Shorter lead times for delivery
- Readily available spare parts and service
- Troubleshooting assistance via remote connectivity
Pricing
- Cost competitiveness
- Fair pricing for capabilities
- Good value for money
- Flexible payment options
Selecting a manufacturer with relevant expertise results in a high-performing roll forming system.
Installation and Operation of Track Roll Forming Machines
Proper installation and operation procedures are vital for trouble-free functioning of track roll formers.
Installation
- Civil works completed for line mounting
- Equipment unloading using cranes, forklifts
- Positioning and alignment of line components
- Assembly of stations according to drawings
- Levelling and securing machines on foundations
- Power, utilities and compressed air connections
- Trial runs and testing before production
Operation
- Roller adjustments for profile settings
- Entry guides aligned to coil width
- Test runs to verify strip flow and formed profile
- Monitoring line speed, motors and power
- Feeder system to ensure constant material feed
- Sensors to detect jams or failures
- Lubrication of moving parts
- Hydraulic system maintenance
- Tooling changeover as per production schedule
Following standardized practices for installation and operation enhances productivity.
Maintenance of Track Roll Forming Equipment
Preventive maintenance is key for continuous functioning of roll formers.
Scheduled Maintenance
- Daily checks of roll alignment, strip guidance
- Inspection of motors, bearings, gearboxes
- Monitoring oil levels in hydraulics
- Cleaning of PLC cabinets, air filters
- Observation of roll and strip wear
- Electrical, hydraulic systems inspection
- Fastener tightening, gear lubrication
- Oil changes, greasing as specified
Overhaul Maintenance
- Roll regrinding or hard-facing
- Gearbox overhaul or replacement
- Replacement of worn or damaged components
- Hydraulic system flush and fluid change
- Refurbishment of PLC hardware
- Upgrade or reprogramming of controls
- Calibration of instruments and sensors
Breakdown Maintenance
- Troubleshooting faults and failures
- Repairing rolls, tooling or feeding systems
- Fixing conveyor issues, jamming
- Electrical repairs and rewiring
- Emergency replacement of damaged components
- Commissioning, test runs before resuming production
Proactive maintenance minimizes downtime and maximizes roll former uptime.
Advantages and Limitations of Track Roll Forming
Benefits
- High production rates up to 100 m/min
- Continuous forming of profiles up to 50 ft long
- Consistent and repeatable profile quality
- Tight tolerances down to +/- 0.5 mm
- Tooling flexibility allows profile changes
- Lower investment cost versus other processes
- Material savings from little waste
- Smaller footprint than other metal forming methods
Limitations
- Not suitable for short and small pieces
- Size constraints from coil width and thickness
- Limited profile complexity versus other processes
- Higher tooling trials needed for custom profiles
- Secondary operations often required for holes, notches etc.
- Significant strip strength and precision required
- Special measures for high strength materials
Understanding both pros and cons helps determine optimal applications.
How Track Roll Forming Compares to Other Metal Forming Methods
Versus Press Brake Bending
- Press brakes limited to shorter parts
- Lower tonnages for roll forming
- No length constraints with roll forming
- Higher initial tooling cost for press brakes
- Quicker changeover on roll formers
- Press brakes need skilled setup
Versus Steel Extrusion
- Better surface finish with roll forming
- Simpler tooling allows fast profile change
- More size constraints with extrusions
- Lower cost for custom roll form tooling
- Extrusion needs high volumes to justify cost
- Roll formed steel properties more consistent
Versus Metal Stamping
- Progressive stamping also continuous process
- Roll forming simpler method for long pieces
- No stripping issues with roll forming
- Lower roll former tooling costs
- Stamping needs greater hitting precision
- Secondary fabrication often still required
Weighing trade-offs helps select the optimal process.
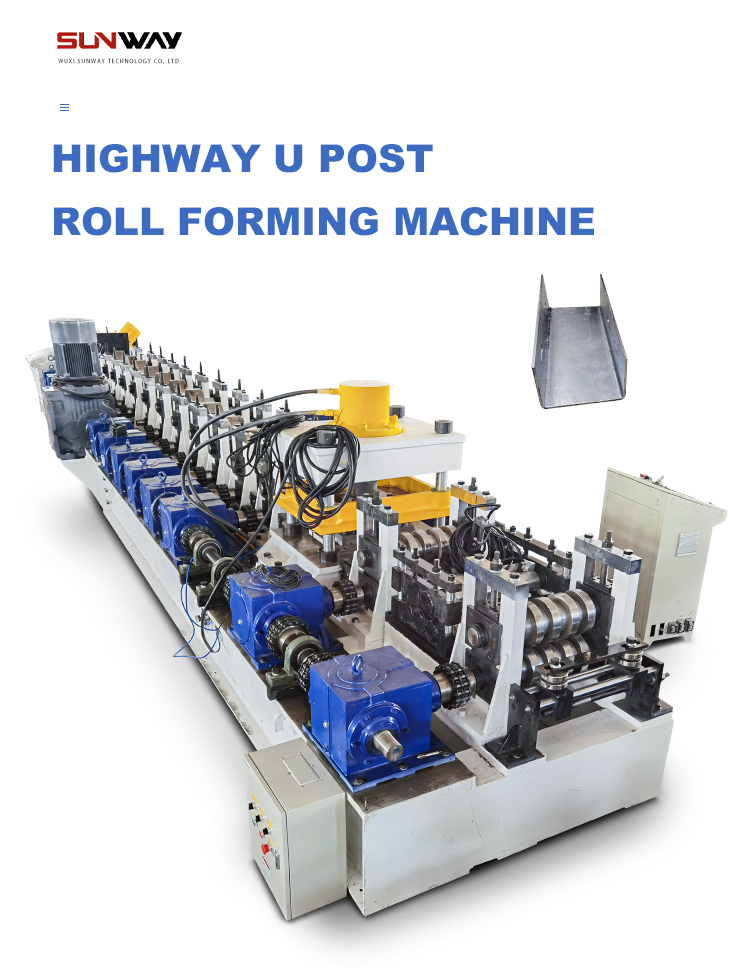
FAQ
What types of materials can you roll form?
Roll forming is suitable for most sheet metals including mild steel, stainless steel, aluminum, copper, brass up to 6 mm thickness. With special tooling, some machines can form high strength steels over 1250 MPa.
How do you design a roll formed profile?
Profile design for roll forming involves CAD modeling, defining bend sequences, material recommendations, FEA analysis, tooling design, and iterative roll forming trials to develop the optimal profile.
What determines the roll forming speed?
The maximum production speed depends on factors like material thickness, line length, profile complexity, number of forming stations, motor power, and designed speed capacity of the machine.
How accurate is roll forming?
With proper machine configuration, precision tooling, and strip feed control, roll formed parts can achieve dimensional tolerances of +/- 0.5 mm (+/- 0.02″)
What is the cost of a roll forming machine?
Roll former cost varies widely from $50,000 for basic machines to $5 million for large custom lines. Key factors determining price are production speed, size, automation level, and customization needs.
How long does a roll forming machine last?
With proper operation and preventive maintenance, a roll former will typically have a working life of 15-20 years. Periodic upgrades to controls, hydraulics, tooling etc. can further extend equipment lifespan.
Can you weld a roll formed section?
Yes, additional fabrication like welding is possible on roll formed parts either by incorporating secondary operations on the line or in separate processes.
How do you maintain roll forming tools?
Common maintenance tasks include scheduled lubrication, daily cleaning, visual inspection for wear or damage, regrinding or hard-facing of rolls as needed, replacement of damaged components.
Why is roll forming better than other processes?
Benefits of roll forming include high speeds, continuous production runs, close tolerances, flexible profile changeovers, lower cost for long parts, reduced material waste versus other metal forming methods.
What safety is required for roll forming?
Critical safety elements are proper machine guarding, emergency stops, maintenance lockouts, electrical safety systems, conveyor guards, hearing protection, protective equipment for handling coil stock and formed parts.
Conclusion
Roll forming is an efficient process for continuous production of precise metal profiles across many industries. Track roll forming lines with multiple forming stations offer high productivity for long parts like panels, rails and roofing components.
Selecting the right forming machine based on product needs, optimizing line design, and proper operation and maintenance enables roll forming to produce metal parts with accuracy, speed, and flexibility.
With their benefits of fast setup, lower cost, and lean requirements, track roll formers are set to see continued growth in coming years across diverse sectors.